As showcased in the Uponor booth at the 2020 NAHB International Builder’s Show (IBS), Phyn, the leader in intelligent water solutions backed by Uponor and Belkin International, showcases its commitment to innovation in sustainable and water efficient construction products and technology with the introduction of Phyn Plus Pro Edition. Created for and sold exclusively to Read more
Featured Articles
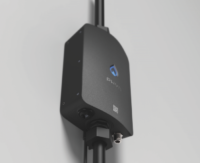
As showcased in the Uponor booth at the 2020 NAHB International Builder’s Show (IBS), Phyn, the leader in intelligent water solutions backed by Uponor and Belkin International, showcases its commitment to innovation in sustainable and water efficient construction products and technology with the introduction of Phyn Plus Pro Edition.
Created for and sold exclusively to professional channels including home builders and the residential construction community, Phyn Plus Pro Edition shares all of the best-in-class capabilities of the award-winning consumer Phyn Plus Smart Water Assistant + Shutoff product, the most accurate and comprehensive whole-home smart water monitoring solution on the market.
The Phyn Plus Pro Edition is enhanced with features that are optimized for installation at scale, including an ethernet port, a direct scan QR code for quick setup, and a unique rough-in “blank” to hold the place of the device until the finish plumbing stages of construction.
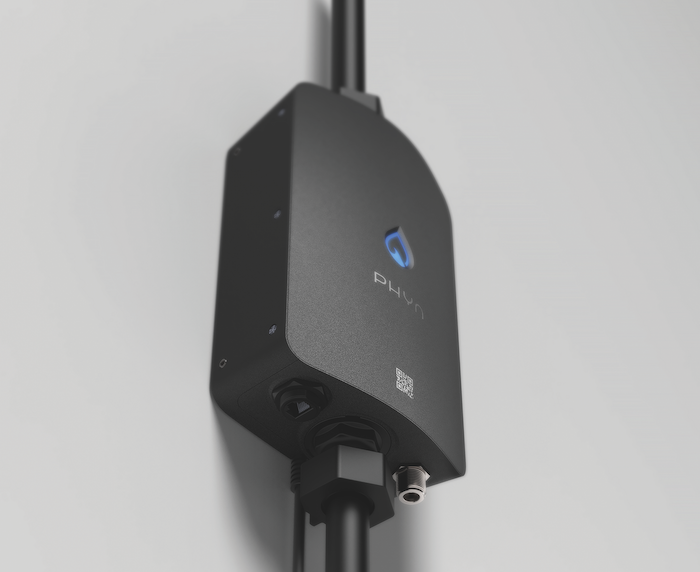
The adoption of smart home technology in standard new-home construction is growing at a rapid pace as more consumers want to stay connected to their homes for added security, convenience and comfort. 81% of home buyers are more likely to purchase a home with smart technology already installed. Not only does Phyn’s smart technology add to the overall value of a home, but also creates a more eco-friendly residence that supports the overwhelming majority of people looking to live more sustainably.
“In working with home builders we discovered that they have unique needs that the existing solutions on the market have not yet met,” said Ryan Kim, CEO of Phyn. “With the Pro Edition, we listened and took the opportunity to incorporate both their business as well as operational needs to develop an extension of our best-in-class Phyn Plus product that makes it easy for them to integrate into the existing life cycle of a new home build.”
Installed on a single location on the main water line, Phyn Plus Pro Edition is an innovative smart home device that protects and monitors a home’s entire plumbing system. The device analyzes microscopic changes in water pressure — 240 times every second — to fingerprint each water fixture and give homeowners unprecedented insight into their water consumption. From the smallest drip leak to frozen pipes, Phyn ensures homes are water tight and can automatically shut off the main water in the event of a catastrophic leak to mitigate damage.
With a sleek, durable, and compact design that is built for quick installation, the Phyn Plus Pro Edition features an integrated power supply that is built into the device. Additionally, the Pro Edition includes an ethernet port for the device to be hardwired to the home’s network instead of having to only rely on the homeowner’s WiFi. This is key in situations where the device may be installed in a part of the property where the WiFi signal may not adequately reach.
Professional channels will be able to purchase the Phyn Plus Pro Edition for $499 starting in Q3 of 2020. The device joins Phyn’s growing lineup of award-winning products, which includes the recently announced Phyn XL 1.5” and the Phyn XL 2” created for larger homes, new construction and light commercial properties with supply lines up to 2”. Phyn’s robust product suite now offers a full range of leak detection and water monitoring solutions for every type of residence, ranging from the DIY installed Phyn Smart Water Assistant to the professionally- installed Phyn Plus, Phyn XL1.5” and Phyn XL 2”.
Builders and professional installers may contact Phyn at Phyn.com for more information about the Phyn Plus Pro Edition.
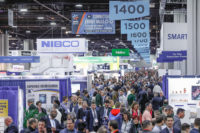
We have made it to the new year, a new decade. And with the turn of every calendar comes the rush of industry trade shows. Next week we will be traveling to Las Vegas for the IBS/KBIS Show or the Builder’s/Kitchen & bath Show. Following that, we will be in Orlando for the AHR Show Read more
We have made it to the new year, a new decade. And with the turn of every calendar comes the rush of industry trade shows. Next week we will be traveling to Las Vegas for the IBS/KBIS Show or the Builder’s/Kitchen & bath Show. Following that, we will be in Orlando for the AHR Show, North America’s largest HVAC show. Oh yeah, let’s not forget about World of Concrete, back in Vegas. The goal is to see, feel and test new products, learn and network with fellow attendees.
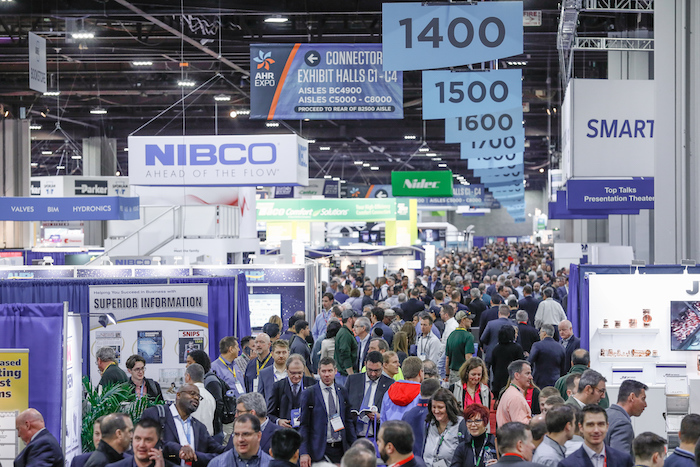
The AHR Expo is one of the largest annual North American trade shows.
When attending these trade shows, it is best to have a plan. Having attended dozens of these show in the past, I have come up with some tips and strategies for a better trade show experience.
- Map Out Your Plan — All of these shows have corresponding websites with maps, and a list of exhibitors and events. I can’t stress enough to map out your day so you are the most efficient with your time, energy and steps on the trade show floor. (ahrexpo.com & www.buildersshow.com & www.worldofconcrete.com) Downloading the appropriate trade show apps is a must.
- Wear Comfortable Shoes & Clothing — We all want to look good, and professional, but gone are the days of stuffy apparel. I’d rather feel comfortable and fresh at the end of the day than out of sorts, sweaty and dogs a barking.
- Give Yourself Enough Time — The stress of a trade show can be daunting in and of itself. Take as much time as you need to take a deep breath and move freely on the show floor. It’s always a good idea to come in the day or night before a show to make sure all is in order and registration for the show is set. If you are planning a night out, make sure you make any necessary reservations ahead of time.
- Afterparty Over-Indulging — We all love to go out and enjoy ourselves, especially after a long day at a show. There are numerous manufacturer parties, dinners, soirees, etc. where one can relax and wind down. But staying out all night—and drinking—can be fun, and up to your discretion, but it isn’t advisable, especially if you intend to be at the show the following day. Nobody is impressed with the over-perspired, alcohol lingering on breath, bags under the eyes, headache pounding visit from on overserved attendee. Pro Tip: Keep hydrated and carry a protein bar just in case you get the munchies. The IAQ in these large buildings is usually very poor and the air can get dry.
- Plan Accordingly for Transportation — Most of the time at busy trade shows, transportation can, well, be a bitch, especially after a show. Keep this in mind as long taxi lines will form to and from the shows. Download your favorite rideshare app so you are locked and loaded.
- Travel in Packs — If traveling in groups, try to stay in one place or area. It alleviates costs on transportation and makes meetings much more amenable.
- Be Prepared to Exchange Contact Info — Make sure you have business cards on hand and be prepared to exchange info digitally, so make sure your phone is charged or bring extra chargers! Also, make sure you have proper badges for the show. For example, attendee, exhibitor and press badges all provide different access and different access times. Make sure you understand the limitations of your particular given badge.
- Follow-up with Contacts — Once the show is over, what it your end game? What better way to measure the results of a show personally than to document leads, follow up with new contacts, and were you satisfied with your expectations of information, contacts and overall impressions?
- Cellular/WiFi Service — Most shows do not offer WiFi on the show floor, or if they do, it usually sucks. There are certain spots at different venues you may be able to sneak a signal, maybe. Make sure your service is covered in the areas where you are, or be prepared to go without in the dark recesses of a concrete building.
- If Unable to Attend … — Be sure to follow your favorite social media outlets that are attending (Search Mechanical Hub on Facebook, Twitter & Instagram) and keep up to date on what’s going on from the show floor. First of the year trade show events are when companies have big product announcements, launches and press briefings.
Good luck, and have a great trade show experience!
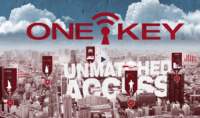
Nearly five years ago, at an undisclosed location nearby its corporate headquarters, invitees to the annual Milwaukee Tool NPS event were introduced to what would be the future of how contractors in the field view and use tools. Piggybacking off of what Milwaukee stands behind, One-Key—Milwaukee’s initial dive into tool connectivity—is another statement in the Read more
Nearly five years ago, at an undisclosed location nearby its corporate headquarters, invitees to the annual Milwaukee Tool NPS event were introduced to what would be the future of how contractors in the field view and use tools. Piggybacking off of what Milwaukee stands behind, One-Key—Milwaukee’s initial dive into tool connectivity—is another statement in the company’s ongoing mission to be a solutions provider. “More data in the hands of contractors helps them make better decisions,” says Steve Matson, director of Program Management, One-Key.
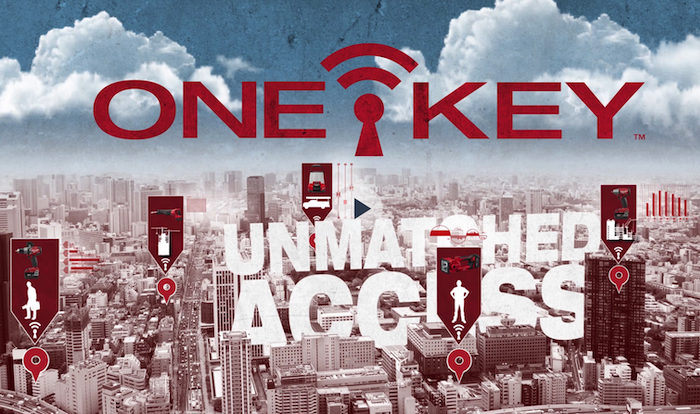
According to Matson, the smart technology that is One-Key falls within Milwaukee’s general approach to development—being a solutions company first. “When we started rolling up the problems that we were hearing during our product research years ago, connectivity became a great enabler to solve these issues in ways that we couldn’t in the past,” says Matson.
“If you accept that technology is continuously evolving, it starts to become more of a conversation around how you can maintain a platform that’s adaptable and capable of change over the years, and that’s how we plan. We recognize that even though most smartphones turn over once a year or once every two years, our products are expected to last closer to a decade. The conversation becomes focused on how we set a contractor up for success, and how we ensure that purchase remains as capable five years down the road as it is today,” says Matson.
When first launched, One-Key was touted as the first digital platform for tools and equipment, One-Key integrates industry-leading tool electronics with a custom-built cloud-based program to provide a new level of control and access to information. “By leveraging this cloud-based innovation, we’re opening the doors to a virtual, interactive, and instantaneous experience for power tool users; ultimately creating a jobsite of endless possibilities through smarter tools,” said Andrew Lentz, product manager, Milwaukee Tool, back in 2016.
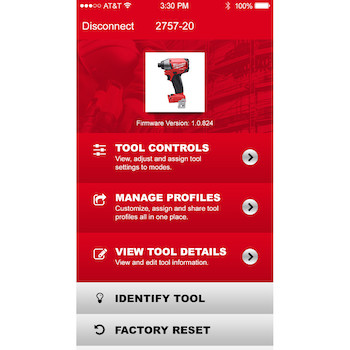
One-Key interface
This was done in three ways:
- Inventory Management— the mobile App and web interface will allow users to input any product (via serial #, receipts, etc.) and keep detailed records of each tool. Managers were also able to assign locations or specific owners to each asset, providing accountability, and enabling easy information sharing between the field and back-office. This feature helps contractors be better inventory managers.
- Tool Reporting— will give the user the ability download critical information and use this information to generate reports that can confirm the success/accuracy of an installation, and will be able to upload data and history to create custom reports that track the success and timing of electrical terminations. By syncing tool data, users can conduct preventive maintenance through data analysis and collection.
- Tool Control— Users can use pre-determined set-ups for specific fasteners and materials, or completely customize their own profile with torque and speed settings for the application at hand. With a touch of the button on the tool, they can easily go back and forth between these saved profiles so that each application is done with the most accurate and productive settings.
When asked about the possibility of an auto shut-off feature for the tool for guys who take the tool home from the jobsite, or the possibility of embedding some type of GPS component, Milwaukee representatives didn’t rule it out for the future. “This is really just the beginning,” I was told. Not too long after, Milwaukee offered Integrated Tool Tracking where users could identify where and when their One-Key compatible tools were last seen.
Today, the One-Key platform is considered the industry’s largest tracking network, and the platform is said to provide, on average, up to five million location updates every single day, which have helped facilitate the recovery of thousands of tools. With Community Bluetooth tracking, barcode scanning and geofencing, users get complete control and visibility of their inventory across any job, crew and location. Real-time alerts help prevent loss and expensive setbacks.
“We’re always looking at ways to make this technology more available in our tools and equipment,” says Matson, as evidenced with the launch of the MX Fuel line late last year.
“2020 will be our biggest launch year yet for One-Key enabled product. I see a lot of similarities to how the FUEL line has grown over the years, from just a drill and an impact driver to a healthy majority of our line. Where connectivity makes sense, adds value, and solves a problem: you’ll see One-Key,” says Matson. “If you haven’t experienced One-Key in a while, it’s time to take a look again.”
Benefits of One-Key
- Free
- Digital Record of Ownership
- Beacons out Identity
- Service Reminders
- Provides Warranty Info
- Track Tools and Lock Tools
- Geofence Your Job
- Get Alerts
- Who Is Using Tool; What Are They Doing with It
- Spec in a Tool; Give Report
- Complete Inventory Management Via App or Desktop
For more info on the One-Key platform, visit https://onekey.milwaukeetool.com
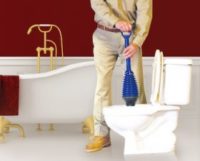
“I grab two things when I leave my truck: my flashlight and my VersaPlunge”. That’s Michael Williams, Field Manager for Just Drains LLC – the “the Number 1 drain cleaning company in Philadelphia” – on the revolutionary new plunger from General Pipe Cleaners. “It’s what pros use,” he quickly adds. “And it’s what we recommend!” Read more
“I grab two things when I leave my truck: my flashlight and my VersaPlunge”.
That’s Michael Williams, Field Manager for Just Drains LLC – the “the Number 1 drain cleaning company in Philadelphia” – on the revolutionary new plunger from General Pipe Cleaners.
“It’s what pros use,” he quickly adds. “And it’s what we recommend!”
Williams knows what he’s talking about. With six expert crews, Just Drains LLC serves Southeastern Pennsylvania from the Delaware River to Harrisburg. And their seasoned professionals demand maximum performance from all the tools they have.
Innovative New Plunger Design
With its patented, extremely pliable VersaFlange™ cone, the VersaPlunge® plunger easily conforms to nearly any shaped toilet bowl opening, creating a tight seal in virtually any toilet design.
Williams pulls no punches: “It works better than any other plunger on the market. Period.”
Traditional plungers, by contrast, have hard rubber round cones – incompletely and loosely sealing the bowl drain, risking messy, germ-laden splash-back.
“VersaPlunge gives both the suction and tight seal you need,” Williams notes. “Where you put it, VersaPlunge stays.”
Extra Performance When It Counts
“Its remarkable,” he continues. “You don’t get any back-pressure – and no blow-back. If you push down on a conventional plunger, it can actually collapse on you – and you gotta fight to bring it back up.”
Not with VersaPlunge, he declares.
General’s innovative tool sports a convenient relief valve in the handle to minimize overflow. And its super-compressible, accordion-style bellows lets users apply extra force on stubborn stoppages.
“VersaPlunge comes back up – and actually ‘breathes’,” Williams contends. “As you push down, it stays in place – gives what you need to get the full plunge each time.”
For More Than Just Toilets
VersaPlunge is extremely versatile, too.
Roll up the VersaFlange end – and make a flat bottom to clear sinks, tubs, and other drain openings.
“You can use in floor drain traps to make sure the trap doesn’t have debris in it,” said Williams. “If it still holding water you can plunge it to get it open without using the big machine.”
That’s why many professionals carry extra VersaPlunge plungers to handle a range of problems.
“The flexibility of the handle and bellows lets you precisely position VersaPlunge for maximum performance,” he explains. “It’s good in sinks with a fixed faucet. If you can’t move the spout, the accordion style bellows let you flex the handle to the side and plunge effectively from an angle. You can’t do that with conventional plungers.”
The Bottom Line
Michael Williams thinks “every drain cleaning and plumbing professional” should carry a few VersaPlunge plungers for a range of stoppages.
He says that VersaPlunge helps clear clogs faster than old-fashioned plungers do – and keeps surroundings cleaner.
“With VersaPlunge, you’re not just getting a plunger – you’re getting the plunger!” he smiles. “VersaPlunge is like a plunger on steroids!”

Xcel Energy is headquartered in Minneapolis, Minn., and is the largest electrical energy provider in Colorado. The company also provides electricity and natural gas to eight states in the Upper Midwest and Southeast. Its thermal energy business began in 1998, but its history as an electrical power supplier began more than 100 years ago in Read more
Xcel Energy is headquartered in Minneapolis, Minn., and is the largest electrical energy provider in Colorado. The company also provides electricity and natural gas to eight states in the Upper Midwest and Southeast. Its thermal energy business began in 1998, but its history as an electrical power supplier began more than 100 years ago in many of the states it serves. Xcel Energy serves more than 3.6 million electricity customers and two million natural gas customers. It is a forward-thinking energy company when it comes to providing clean power. It has set a carbon reduction goal of 80% from 2005 levels by 2030 and has an aspirational goal of offering 100 percent carbon-free electricity to customers by 2050. Xcel Energy currently employs about 12,000 people.
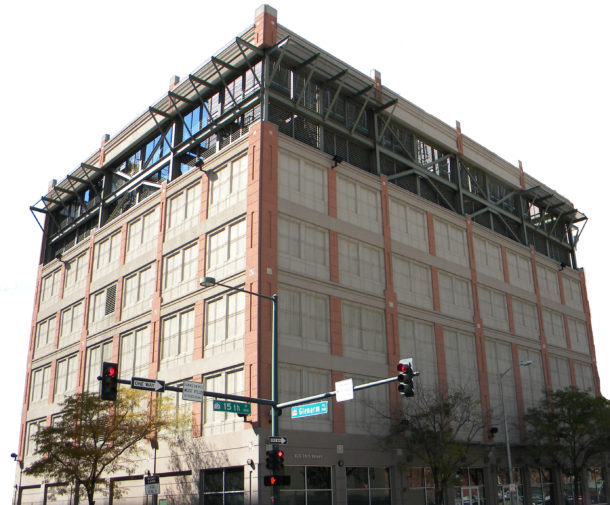
Denver District Cooling Building – Denver, CO
Refrigerant monitoring updates were needed at Xcel Energy’s Chilled Water building in downtown Denver. The different types of refrigerant monitoring systems that were in use offered no communications ability among plant locations in the city. The Thermal Energy team was spending time conducting constant walkthroughs of five separate buildings to check the health and functionality of 16 chillers and related mechanical equipment, including the refrigerant.
There was also inconsistent monitoring and the absence of data that could identify leaking refrigerants. This, plus the lack of consistency and reliability in the refrigerant equipment used throughout the plants, made troubleshooting difficult and finding correct spare parts from manufacturers arduous.
The result was sub-optimal refrigerant use, monitoring and communications plus inefficiencies in maintenance and repairs and potential safety issues. Today, Xcel Energy uses refrigerant monitors in its five locations to monitor the chillers. Each plant has its own Multi-Zone (MZ), Halogen Gas Monitor and they all communicate with the building automation system, which records levels of refrigerant readings while each plant is continually monitoring for potential refrigerant leaks. The MZs use an NDIR (Non-Dispersive Infrared) sensor that enables early refrigerant leak detection to 1 ppm and a pump that allows for fast sequential sampling up to 16 points.
Michael O’Malley, Operations Manager at Xcel Energy’s Thermal Energy Department in Denver, Colorado, has been with the company for 10 years and has double that experience in operations management. He and his team are responsible for a system that includes five different locations, 16 chillers and four miles of underground pipes that distribute chilled water to some of the city’s most important downtown buildings, including the art museum, main branch of the city’s public library, convention center, hotels, data centers, courthouses and Denver city and county buildings. In each building heat exchangers have been installed, eliminating the need for owners to provide their own equipment.
Clear Requirements
After evaluating refrigerant monitoring products and understanding the operation of the legacy system, Mr. O’Malley thought it important to find active sampling refrigerant monitoring equipment. A system that used a pump for sequentially monitoring different locations would get air through to the sensor and the possibility of increasing sampling frequency could help to prevent any serious consequences. To be proactive and quickly counteract any refrigerant leaks, Mr. O’Malley wanted to set up alarm sensitivities at levels lower than what a passive refrigerant monitor is able to detect. “The cost of a large refrigerant leak to our organization could range from $10,000 to $100,000 or more, depending on the size of the leak,” said Mr. O’Malley.
Using different refrigerant gases such as R22, R123, and R134a at multiple locations, it was also important that the same monitoring system within the different buildings look for all these refrigerant types and that all monitors could communicate with the main plant.
Rocky Mountain High Implementation
The implementation and installation of the first new refrigerant monitor involved a collaborative effort between Xcel Energy, Bacharach and the local representative. A number of refrigerant monitors were installed at different Xcel Energy facilities, so there were some concerns about product reliability. Michael O’Malley wanted to make sure the products would last a long time, be reliable and not require a lot of maintenance. Once Xcel Energy selected the unit it wanted, the initial installation went great, recalled the local representative. Shortly after, however, they were experiencing issues with filters and false alarms. Due to Denver’s mile high altitude, the diaphragms in the pump were working much harder. The issue was quickly remedied by replacing the sealed unit with a more robust rubber diaphragm that would not crack or break. The MZ was installed at a remote plant and as budgets allowed a total of 5 MZs were installed.
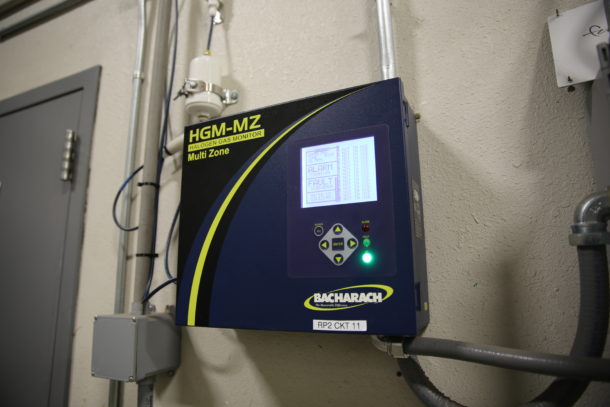
Reliable refrigerant monitor Bacharach’s HGM-MZ ensures Xcel Energy chillers remain in good operating condition.
Latest Technology
The role of technology is inseparably linked to the Xcel Energy Chilled Water Plant. It remains an important safety factor to the team to have highly sensitive leak detection technology incorporated into the refrigerant monitors. Using a technologically advanced sensor that recognizes a variety of refrigerants and a system that provides faster cycle times for all monitoring zones would provide continual sampling to detect any refrigerants that might leak into the mechanical room. Mr. O’Malley said, “It’s important that the operations team have confidence that it’s safe to go into the room–that no refrigerant leak happened in the mechanical space and that nothing is leaking into the environment. We need to keep refrigerant inside the chiller. That’s important, so I’m not constantly buying refrigerant.”
The local representative noted that Xcel Energy was not using the same gases in all the chillers and not all those gases were supported in the product they were using. This situation could be addressed by the HGM-MZ’s extensive library of gases built into the monitor plus the accuracy of the refrigerant readings provided.
The HGM-MZ has a library of over 60 refrigerant gases, solving the refrigerant variety issues within the plant for detecting R22, R123 and R134a. Product standardization keeps maintenance easy by using the same product for spare parts and for quick replacement. The Xcel Energy Operations Team has had a significant reduction in the frequency of the walkthroughs they need to conduct. The MultiZone system also keeps refrigerant emissions at bay by having 1ppm performance. It also solved the issue of needing to monitor for different refrigerants at different locations.
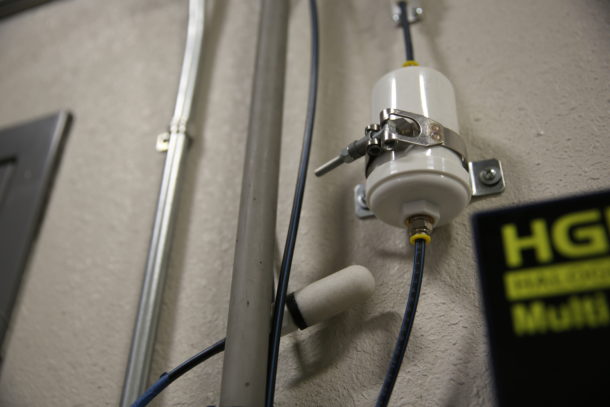
Charcoal filter and detection point shown beside the HGM MZ refrigerant monitor.
Clear Financial Advantage
Reducing lost refrigerant, cutting technician travel time for repair work and having the right system to do the job were important from a cost and environmental perspective. According to Mr. O’Malley, “It’s critical we find refrigerant leaks early. Most importantly, we are concerned with the negative effects on the environment. I don’t want refrigerants getting into the atmosphere. The second concern is the financial impact. The machines’ performance will suffer if they don’t have the refrigerant. It’s like gas leaking out of your car.”
Because of the time it took to check the legacy product, it was critical to have a product that would constantly be drawing sequential samples at the chillers and recording refrigerant levels to ensure the product was in operation, no matter the location. “Having reliable, continuous monitoring that we could see from a central location would allow us to dispatch a technician only when having to make an assessment or deal with a minor issue,” Mr. O’Malley said. The technician’s time alone would save costs. Additional benefits include system performance, lower energy costs and reduced refrigerant cost.
Reliability
Being able to rely on the equipment in continual operation was another important consideration. The manufacturer’s representative remembers visiting the Xcel Energy chiller plant in downtown Denver and noted that it was the largest underground chiller plant he had ever visited. He recalls that Xcel Energy wanted a “set-it and forget-it”’ type unit and that they had some concerns surrounding code compliance. Wanting to focus on refrigerant sensitivity, the representative demonstrated that the refrigerant monitor could detect leaks down to 1pm.
“The monitors have been reliable. I don’t recall having to change out the pumps in quite some time,” said Mr. O’Malley, “You basically hang them on the wall and will get years and years and years of service out of them.”
Building Automation System and Communications
The facilities supplied with water by Xcel Energy are either directly owned by the building’s owners or are leased. At any time customers can request records from Xcel Energy on the management of the system. “If a customer wanted to see records on how we’re managing the system, all we would have to do is pull the data to show them the preventive maintenance we are doing and the historical data,” said Mr. O’Malley. “The monitor can talk back to the building management system if the pump goes bad or if the unit sees refrigerant. It will tell you and you don’t have to walk by it to find out.
Functionally, it “talks” the building system language,” he said. Based on the equipment performance, impression and usability, Mr. O’Malley and his Operations team are making good use of the MZs reliability, ensuring the 16 chillers remain in good operating condition and helping keep Xcel Energy’s environmental commitment and reliable service to customers.