By Jonathan Simon The 2024 plumbing and mechanical codes contain a subtle but significant change all plumbers should know. For the first time, green-colored solvent cement has been approved into the model codes for use with copper-tube size CPVC. Here’s how that change came about and what it means to plumbing contractors. The Need for Read more
Industry Blogs
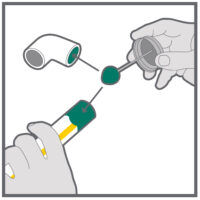
By Jonathan Simon
The 2024 plumbing and mechanical codes contain a subtle but significant change all plumbers should know. For the first time, green-colored solvent cement has been approved into the model codes for use with copper-tube size CPVC. Here’s how that change came about and what it means to plumbing contractors.
The Need for Change
Plumbers who work with CPVC appreciate its ease of installation, reliability, and the straight, professional appearance that showcases the plumber’s craftsmanship. But in recent years, plumbers have become increasingly concerned with the risk of dry-fit failures that occur when a joint is not properly solvent welded. The team behind FlowGuard Gold CPVC received feedback from plumbers that the lack of contrast between the yellow cement and the tan pipe could make it difficult to see the solvent cement when visually inspecting installations.
That’s important because CPVC pipes and fittings have an interference fit in which the fitting socket is tapered, so the outer diameter of the pipe is slightly larger than the inside diameter at the bottom of the fitting. When solvent cement is applied and the pipe is bottomed out in the fitting, the two components are fused into a single piece of CPVC and create a joint that is extremely strong and reliable.
But with a tight interference fit, a dry joint can still be strong enough to withstand a pressure test without being solvent welded. Because of this extreme joint strength, even an unwelded CPVC joint can hold for a long time under everyday operating conditions, but eventually natural movement and stress on the system will cause an unwelded joint to fail. These dry-fit installation errors are extremely rare but can be very frustrating.
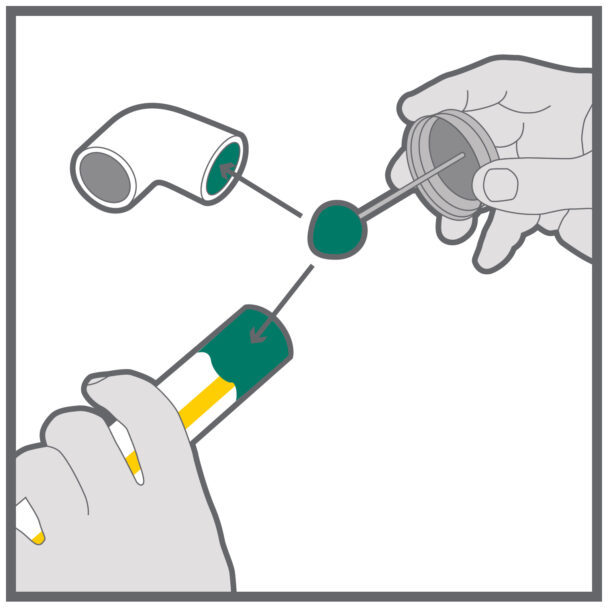
Eliminating Dry Fit Errors
There are two steps plumbers can take to eliminate dry-fit errors. One is to weld each joint as it is assembled. This helps ensure every joint is solvent welded and has the added benefit of enabling faster, more efficient installation than pre-assembling the entire system and then coming back through with solvent cement.
The other is to visually inspect the system after installation to ensure solvent cement is visible around each joint. Visual inspection is a critical step in any piping installation process, so when contractors told us that visual inspection was more challenging than it could be due to the color of the cement, we began exploring solutions.
Because the plumbing and mechanical codes required that one-step solvent cement be yellow in color, FlowGuard Gold first worked with our solvent cement partners to develop a cement that includes a UV indicator. This allows the contractor or installer to verify solvent welded joints using a UV flashlight. This solution proved effective, but we recognized there was an opportunity to make the process even easier for plumbers.
Changing the Plumbing Code
In 2020, we asked our solvent cement partners to support the manufacture of a new color solvent cement that would provide high contrast when used with FlowGuard Gold pipe and fittings and they agreed. By listening to the voice of plumbing and mechanical contractors across the country, we identified the color green as the ideal solution for a high contrast CPVC solvent cement.
The next step was to get code approval for the green-colored cement. We developed and presented a proposal to the leading code organizations requesting that the green-colored cement be approved as an alternative to yellow for copper-tube size CPVC. Because the color change did not impact the installation process or the performance of the cement, the proposal met no resistance in technical committees or in the public comment stage of the process.
The proposals were approved in 2023 and high-contrast green solvent cement is now included in the 2024 International Plumbing Code, section 605.14.2; the International Mechanical Code, section 1203.3.4; the Uniform Plumbing Code, section 605.2.2; and the Uniform Mechanical Code, section 1211.3.2.
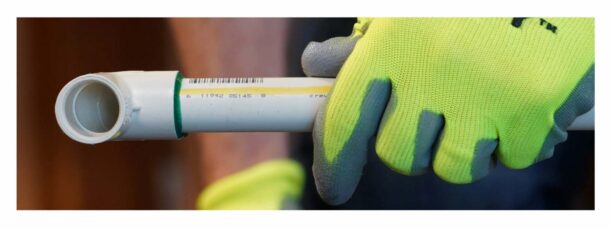
A Welcome Addition
Because our solvent cement partners were involved in the process from the beginning, they were prepared to bring green-colored, one-step solvent cement to market as soon as the proposed changes were underway. Simultaneously, the team communicated with state, county and local code officials across the U.S. informing them of the pending change and the reason behind it so they could feel confident approving installations using the high-contrast cement in the period between when the changes were approved and published.
These steps allowed contractors, with approval from the appropriate official, to begin using the green-colored cement as early as 2021. Feedback from early adopters was uniformly positive. A number of contractors transitioned to high-contrast green solvent cement for all their projects before the new codes were even published and use of the green-colored solvent cement continues to build momentum in the market.
Even though green-colored cement is now included in the published 2024 codes, it is recommended that contractors verify local codes and approvals prior to installation and always follow the manufacturer approved instructions.
A Small Addition with Big Benefits
Plumbing contractors working with CPVC now have three choices in manufacturer-authorized and code-approved FlowGuard solvent cement: traditional yellow, yellow with UV indicators, and high-contrast green. While the addition of green-colored cement represents a small addition to the FlowGuard Gold CPVC product family, it is a significant advancement giving contractors working with CPVC greater peace of mind and improved jobsite quality control. For more information on FlowGuard Gold CPVC, visit FlowGuardGold.com.
Jonathan Simon is the North American residential plumbing manager for Lubrizol Advanced Materials Inc., the parent company for FlowGuard Gold Pipe and Fittings.
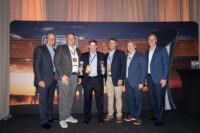
By Heather Ripley Do you remember the first time you received an award? Whether it was in school, after an athletic competition or through an after-school or volunteer program, you were probably elated. Getting recognized for a job well done spurs a sense of pride in most people. But as we grow into adulthood, awards Read more
By Heather Ripley
Do you remember the first time you received an award?
Whether it was in school, after an athletic competition or through an after-school or volunteer program, you were probably elated. Getting recognized for a job well done spurs a sense of pride in most people.
But as we grow into adulthood, awards are more likely to come as a result of our work performance. And, as the owner of your own plumbing or HVAC company, getting your community’s “Best of” award or winning recognition for your company’s growth rate from a national magazine is something you should celebrate with your employees and customers.
Receiving an award is not just an excuse to hold a party, though. You should also consider the public relations value that receiving that award can garner. That’s why you shouldn’t neglect sharing your award with your local media and with the trade publications that cover your industry.
Vying for Awards
The first thing you need to do to win an award is compete for it. Many home service contractors don’t realize that they’re not simply nominated for these awards organically but rather they need to actively pursue these opportunities.
While it can be true that a pleased customer might nominate you for the local “Best of” awards, it takes some planning to net some of the bigger awards, like the Inc. 5000 or Entrepreneur of the Year.
Vying for awards should be an integral part of your marketing budget. While it may take you some time to gather financial information or work with your public relations partner to wordsmith essay questions, the PR value in winning these awards can be used in a variety of ways.
According to Best Business Awards, smaller companies that win awards can see a 63% increase in their income and a 39% growth in their sales. The truth is that consumers like doing business with award-winning companies because they view them as more reputable.
Write a Press Release
Earning a top spot as your community’s best HVAC company or winning the best customer service award as a local plumbing company is something your entire area should know about.
If your local newspaper or radio station is the entity sponsoring the award, chances are they will prepare a news article or report on your awards, but that shouldn’t stop you from issuing a press release. Winning a local award can translate into regional coverage.
By sending out a well-crafted press release to newspapers and news stations in your regional area, you can drum up attention locally, which helps you draw new customers.
But don’t forget to include the media that covers your trade.
If you net a spot on Inc. magazine’s fastest-growing companies or your young general manager becomes a Top 40 Under 40 winner, make sure the trade magazines in your industry also get a press release about your accomplishments.
Trade publications aren’t usually read by your customers, but they are still considered valuable to others in your industry. By building your critical managers up as thought leaders and by showcasing your company as a growing force, you will gain the respect and admiration of your peers.
Having your company featured and your critical managers quoted in trade publications is also a boon for your recruiting efforts. The best skilled tradesmen and women want to work for organizations that show themselves to be thought leaders.
This may not net you more customers, but if selling your business to a larger organization becomes part of your growth strategy or you are planning your exit strategy, having a good name in the industry matters.
Building Relationships
Finally, sharing your award-winning news with journalists in your local media or with trade publications helps you build relationships with these reporters and their publications.
If you have a solid reputation with your local news, you’ll be the first expert they call when there is a news story relating to your industry. If a cold snap hits your area, your plumbing company will be the one tapped to provide tips to avoid frozen pipes. If a heat wave is on the agenda, local reporters will think of your HVAC professionals if they need pointers on how to stay cool.
Being your local expert helps you build credibility with potential customers and keeps your company top-of-mind when a homeowner needs professional work done.
Having good relationships with the trades that cover your industry may also mean you’ll be asked to author opinion pieces on news within your market. These reporters will also know they can call on you if they need a quote about industry trends, or they may even want to do a feature on your milestones.
So, if your team wins an award as the best plumber in town or your HVAC company lands a great spot on the Inc. 500, don’t forget to celebrate the news by sharing it with the media. Doing so helps you build relationships with reporters and within your industry.
Heather Ripley is founder and CEO of Ripley PR, an elite, global public relations agency specializing in the skilled trades, franchising and B2B tech industries. Ripley PR is recognized as the top PR agency for the home service industry. It also has been listed by Entrepreneur Magazine as a Top Franchise PR Agency for six consecutive years and was recently named as one of Newsweek’s Top PR Agencies 2024. Heather Ripley was recently named as a 2024 PRNews Top Women honoree in the business entrepreneur category. She is also the author of “NEXT LEVEL NOW: PR Secrets to Drive Explosive Growth for your Home Service Business,” which is now available on all audiobook platforms. For additional information, visit www.ripleypr.com.
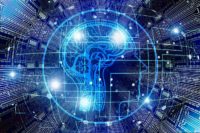
Artificial Intelligence (AI) is quickly becoming an essential partner for tradespeople, providing innovative solutions that make traditional methods faster, smarter and more reliable. As this advanced technology continues to evolve, its integration into various professions provides a competitive advantage, enhancing the quality of services delivered as well as boosting customer satisfaction. Below, we’ll explore seven Read more
Artificial Intelligence (AI) is quickly becoming an essential partner for tradespeople, providing innovative solutions that make traditional methods faster, smarter and more reliable. As this advanced technology continues to evolve, its integration into various professions provides a competitive advantage, enhancing the quality of services delivered as well as boosting customer satisfaction.
Below, we’ll explore seven different ways tradespeople across industries are harnessing the power of AI to improve precision, efficiency and beyond.
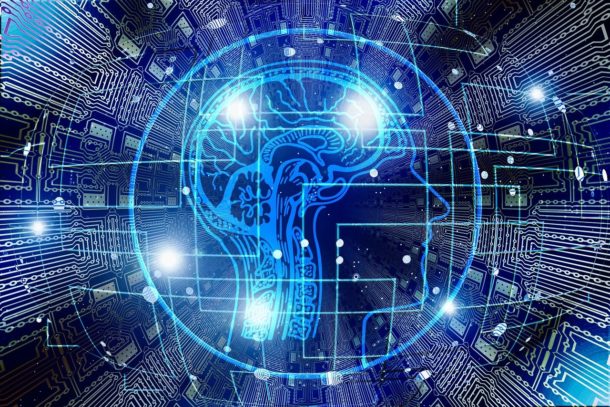
Enhanced Diagnostic Tools
For starters, AI can significantly boost the effectiveness of diagnostic tools in the trades. These tools analyze data from past projects to identify patterns and anomalies that might predict future problems. This foresight allows tradespeople to tackle issues before they worsen, reducing both downtime and expensive repairs. Plus, AI can integrate with mobile devices, providing tradespeople with immediate diagnostic feedback and recommendations right at the worksite.
Precision in Project Planning
AI algorithms can also play a critical role in refining project planning. These systems handle vast amounts of data to streamline project schedules and allocate resources like manpower and materials efficiently. This results in well-organized project timelines that reduce idle times and bottlenecks, helping projects stay on track to finish on time and within budget. What’s more, AI tools are capable of adjusting to unforeseen changes or delays, dynamically updating plans to keep projects moving forward.
Automated Administrative Tasks
One of the most common ways to utilize AI is to simplify administrative duties by automating tasks such as scheduling, inventory management and compliance documentation. Such automation frees up tradespeople to concentrate on the technical aspects of their jobs, enhancing overall operational efficiency and reducing the likelihood of human errors in administrative processes. This shift also allows businesses to better optimize their staffing and resources, focusing more on strategic decision-making and customer service improvements, which are essential for staying competitive in today’s market.
Real-Time On-Site Assistance
Another use is combining Augmented Reality (AR) with AI to transform the approach to complex installations and repairs. An AR headset provides detailed, step-by-step visual instructions overlaid directly onto the work area, indicating exactly where to place components or how to configure systems. This technology is especially beneficial for intricate tasks as it enables even novice technicians to accurately complete complex installations by following real-time guidance.
Safety Monitoring
In the realm of construction, AI can enhance job site safety by using sensors and cameras to continuously monitor for potential hazards, such as structural weaknesses or dangerous gas leaks. These systems instantly alert workers and supervisors to emerging dangers. By providing real-time data and alerts, AI-driven safety measures help prevent accidents and maintain strict adherence to health and safety regulations, thus safeguarding the workplace.
Optimized Supply Chain Management
AI can be very effective on a broader scale as well. For instance, AI excels at predicting project requirements and monitoring inventory levels. This can be a real game changer in supply chain management by minimizing project delays and controlling costs. AI can proactively order supplies before shortages arise, making sure materials are always available when needed and helping to reduce excessive storage costs and waste.
Advanced Training and Support
Last, but not least, AI-powered training platforms are helping revolutionize the training process for tradespeople. Through realistic, virtual simulations, tradespeople can practice their skills in a risk-free environment. This is particularly advantageous for complex procedures, such as an AC installation, where understanding every detail is crucial. Trainees can experiment with different installation techniques, delve into system intricacies and receive instant feedback from AI systems, all of which helps accelerate their learning and enrich their expertise.
The Future of Trades in the AI Era
The integration of AI into the trades marks a significant shift toward more knowledgeable, efficient and safer practices. Going forward, tradespeople who adopt AI tools are going to be better equipped to meet the changing demands of their industry and deliver superior service to their clients. This journey into an AI-enhanced future promises not only greater productivity and safety but also sets a new standard of excellence in the professional trades.
Tom Mascari is President of Mendel Plumbing and Heating. Providing Geneva, Illinois plumbing and HVAC services since 1985, Mendel Plumbing and Heating has a reputation for expert customer service and technical performance. The company also specializes in residential air duct sealing, remodeling and maintenance services to the Fox Valley area.
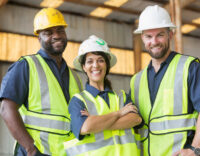
By: Jason Florek, Talent Acquisition Coach and Executive Recruiter at Nexstar Network I’ve been in talent acquisition for 25 years, and I can say with confidence that we’re in the middle of one of the most challenging labor markets I’ve ever seen. Right now, because there are seemingly infinite opportunities available, candidates have most of Read more
By: Jason Florek, Talent Acquisition Coach and Executive Recruiter at Nexstar Network
I’ve been in talent acquisition for 25 years, and I can say with confidence that we’re in the middle of one of the most challenging labor markets I’ve ever seen. Right now, because there are seemingly infinite opportunities available, candidates have most of the power. If you’re involved with the talent acquisition process, you can do everything right in interviews, present a strong culture, and make an aggressive offer, but your ideal candidate still might not bite. Losing a great candidate is discouraging; plus, the hard work and money involved in finding the right fit is lost! Because of this, it’s more important than ever before to create a positive experience for the candidate from the first time we make contact to the moment they come on board.
The candidate experience starts well before potential recruits walk in for an interview. Everything actually starts with your company’s branding tools. Creating enticing job descriptions that outline the information candidates value most can have a bigger impact on the candidate experience than most people realize. Sharing company history, along with your mission, vision, and values is important, but consider also putting information about compensation, benefits, and flexibility at the top of your job descriptions and advertisements, rather than burying this information at the bottom. Clearly defining the total rewards of a role helps potential recruits understand what’s in it for them.
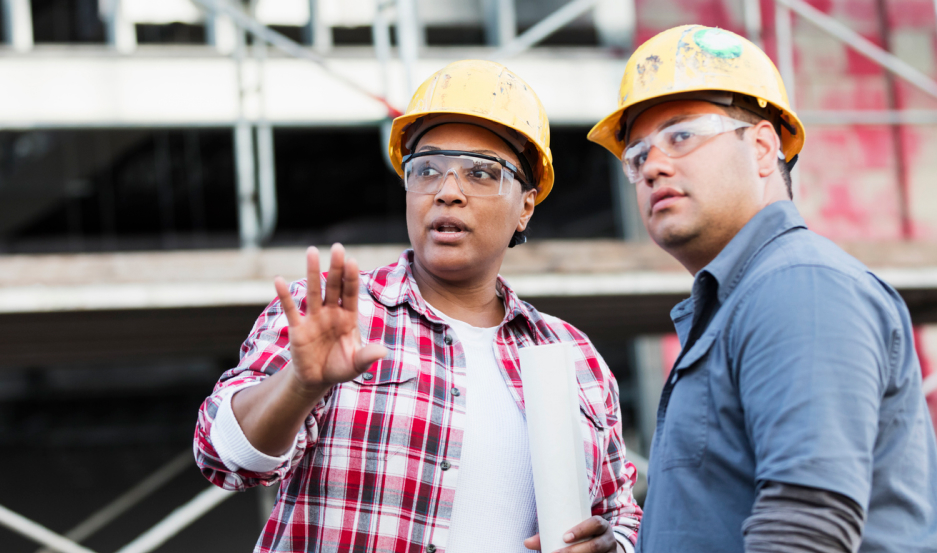
Your career site and social media are among the best places to define your employer brand. Embedding important information that affects a candidate’s understanding of the culture, role, and rewards in these areas can heighten their understanding of what to expect. Make applying as easy as possible on your career site; consider adding information about the entire interview process. This can help avoid confusion as to what’s next in the process. But be careful – candidates might turn away if the process is too complicated or requires too much effort to throw their hat in the ring.
Adding Equal Opportunity Employment (EEO) statements, using inclusive language, and thoroughly broadcasting your values will help candidates match their experience viewing your job advertisements with what they experience throughout the process. These things not only broaden the scope of potential targets, but they show a progressive culture – something that most people value.
When first contacting a potential candidate, it’s human nature to immediately dive into why the position they have applied to or been recruited for is a great opportunity. But if we do that, what can be lost is an understanding of the factors that caused the candidate to consider a job change in the first place. A strong early focus on a candidate’s personal situation can help create awareness of wants and needs that can be addressed throughout the recruiting process.
Many positions, specifically in the trades, are getting harder to fill. The candidate pool is shrinking for skilled roles, and strong candidates are harder to find. So, when we gain interest from a great candidate, it’s important to invest time into making sure they enjoy the process, regardless of the outcome. Doing the little things – creating a welcome sign when candidates show up for interviews, asking if they would like a beverage, and connecting on a personal level – can lead to a more positive experience.
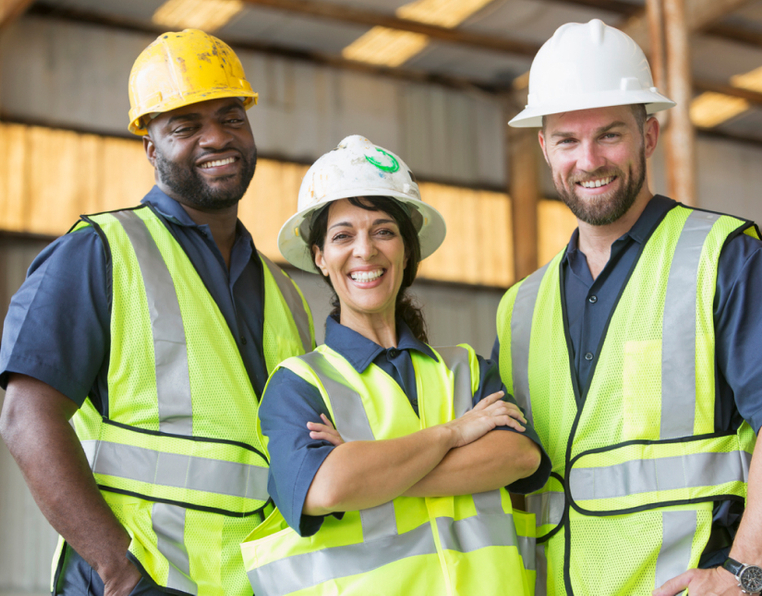
Common courtesy also goes a long way. The way we displace candidates who don’t fit our organizational needs speaks volumes about our company’s values. We’ve all experienced candidate “ghosting”, as well as that frustrating feeling when a candidate doesn’t show up for an interview. But put yourself in the candidate’s shoes! The same is true for them – they’ve experienced ghosting, too. It’s true that having a conversation or sending an email letting a candidate know they aren’t a good fit can be uncomfortable. I know it’s easy to walk away and focus on other things. However, the trades are a small world. How likely is it that someone who’s been “ghosted” by an employer will tell others about their experience? Very likely! It only takes a minute for us to provide valuable information for someone’s professional growth, even if we decide they aren’t the right fit for us.
Even if the news is good, everyone can benefit from more communication. If a good candidate we really want to hire has to wait too long for feedback and follow-up, they’re more likely to walk away, especially if they’re interviewing for multiple positions. This makes an efficient communication process even more important. Try integrating automated text messaging to improve communication, when it comes to scheduling and communicating next steps. Look for ways to provide insight and feedback for improvement to candidates throughout the process.
By providing excellent information in job postings, showing an understanding of a candidate’s personal situation, doing the little things, and being diligent in our follow-up, we can do our best to ensure a positive candidate experience. We’re more likely to gain a candidate’s interest, address their wants and needs, and leave them with a positive impression of the company culture.
The labor market shifts all the time. Conditions will shift again. Currently, the responsibility lies with us, as employers, to ensure we do everything possible to attract, hire, and retain the top talent available. In an environment where it feels like everyone is hiring, shifting the focus toward creating a positive candidate experience is an effective way to improve our hiring success.
Jason Florek has close to 25 years of experience developing and managing integrated recruiting programs for iconic brands. He loves to help businesses attain their growth goals, and specializes in sourcing strategy, multi-hire project management, and executive search. As a Talent Acquisition Coach and Executive Recruiter at Nexstar Network, Jason enjoys helping members work through the complexities of building strong teams in a competitive talent marketplace.
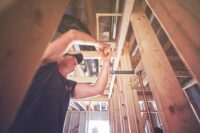
By Heather Ripley Everyone loves getting great reviews. Whether it’s a job performance review or a review from a customer on Google Business Reviews, having someone recognize your work is a feather in your cap. But it’s how you deal with your negative reviews that really speaks volumes about your integrity. Most home and property Read more
By Heather Ripley
Everyone loves getting great reviews.
Whether it’s a job performance review or a review from a customer on Google Business Reviews, having someone recognize your work is a feather in your cap.
But it’s how you deal with your negative reviews that really speaks volumes about your integrity.
Most home and property service companies know that positive reviews are their bread and butter.
Several studies have shown that about 90% of consumers read reviews before deciding to buy a product or hire a professional. This is particularly true for customers who need to hire a plumber, HVAC tech or electrician.
And, if you aren’t monitoring your reviews, you may be leaving your reputation up to your last review. If it’s a negative review and you aren’t addressing it, it could result in a lot of headaches for your business.
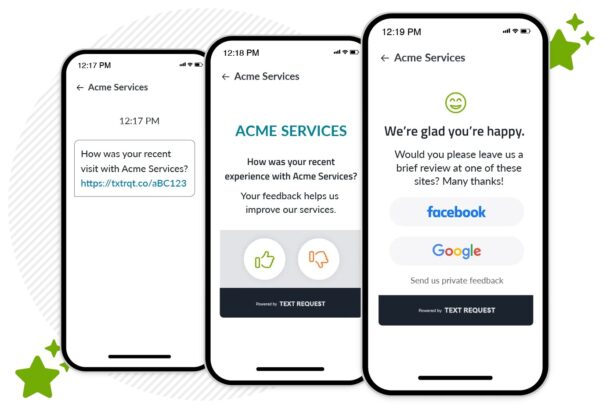
Dangers in Unanswered Reviews
Human nature, being what it is, means that when a customer is satisfied with the work their plumber did in repiping their old home, they aren’t as likely to go online to give a positive review.
Research shows that customers are more inclined to write negative reviews because of the way our brains react to negativity. When we’ve had a bad experience, our emotions are processed more thoroughly, driving us to let the world know we were wronged.
Human nature also means that not every job we have is going to go smoothly. Your team may try hard to please the customer at every job site, but sometimes things just go wrong. And when they do, you may be the recipient of a bad review.
When that happens, you need to acknowledge it publicly, even if you address it privately.
That’s why you need to dedicate an employee or a public relations team to monitor your reviews. And that person or team should also know when and how to respond.
If someone has taken the time to post a review online, even a bad one, their words should be acknowledged. It’s important that customers don’t feel their heartfelt expression of displeasure goes unnoticed. Not only does it make a more permanent adversary of your business, but it can make others who read the complaint have negative feelings about your company, too.
If someone writes a negative review and it sits there for weeks or months without a response, then others who are reading the review will get the impression that you and your leadership don’t care about their customers. Ignoring it doesn’t make it go away.
Managing Poor Reviews
So how should you handle a bad review?
The first thing you should remember is that your answer will be seen by anyone who views that page; therefore, you should always be considerate, apologetic and polite to any bad reviewer.
That can sometimes be hard to do. You’ve spent your blood, sweat and tears building your company, and it’s like your baby. But you can’t take offense and lash out. No one wins when the conversation devolves into a childish fight.
But you can manage your bad reviews professionally by:
- Reading the review thoroughly and responding promptly. Don’t wait months to make amends or others reading the reviews may think that you don’t care.
- Once you see a bad review, apologize immediately for the poor experience and acknowledge that something is wrong.
- Take it offline. After your public apology, let the reviewer know that you are looking into the problem and either give them a number to call you or let them know you will be getting in touch with them.
- Don’t try to sell your services. Turning any review – good or bad – into an opportunity to sell something shows poor taste. You have a whole website and an advertising budget for that.
Keep your responses short and professional, but always respond. And if you don’t have the time or the temperament to respond professionally, hire an employee in-house or a PR or reputation management team to help you.
After all, your business is only as good as your last review.
Heather Ripley is founder and CEO of Ripley PR, an elite, global public relations agency specializing in the skilled trades, franchising and B2B tech industries. Ripley PR is recognized as the top PR agency for the home service industry. It also has been listed by Entrepreneur Magazine as a Top Franchise PR Agency for six consecutive years and was named to Forbes’ America’s Best PR Agencies for 2021. Heather Ripley was recently named as a 2024 PRNews Top Women honoree in the business entrepreneur category. She is also the author of “NEXT LEVEL NOW: PR Secrets to Drive Explosive Growth for your Home Service Business,” which is now available on all audiobook platforms. For additional information, visit www.ripleypr.com.