Ontario, Calif. — The Radiant Professionals Alliance (RPA) and professional/educational association Geothermal Rising (GR) have entered into a memorandum of understanding with the mutual goal of promoting and advancing technological innovations of geothermal systems. The partnership will engage RPA, GR and their respective members in technical activities coordination, education, advocacy, community engagement and policy, publications Read more
Industry News
Ontario, Calif. — The Radiant Professionals Alliance (RPA) and professional/educational association Geothermal Rising (GR) have entered into a memorandum of understanding with the mutual goal of promoting and advancing technological innovations of geothermal systems. The partnership will engage RPA, GR and their respective members in technical activities coordination, education, advocacy, community engagement and policy, publications, and consistent leadership communication for more sustainable building operations and advancing the green economy.
The RPA and GR will support the geothermal and thermal energy network (TENs) industry on providing opportunities to participate in codes and standards development, guidelines, policies, and position statements developed on technical subjects as they relate to geothermal energy. They will collaborate in the development of research related to the design and construction of geothermal energy systems and promote research in areas where results will add to the body of knowledge in the conservation of natural resources, increasing energy efficiencies and sustainability, and improving public health and safety.
“This collaboration brings the geothermal industry together for consistency in the approach, installation, and guidance of geothermal systems,” IAPMO CEO Dave Viola said. “This partnership will further advance the geothermal industry with superior leadership, awareness, and best practices for the safe installation of systems.”
“GR is thrilled to deepen our partnership with the RPA and the international plumbing and mechanical community,” said Dr. Bryant Jones, GR executive director. “This collaboration helps leverage the strengths of both organizations to provide the best resources of the geothermal industry to all of our members.”
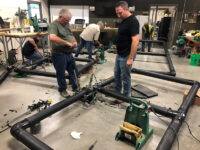
Concise ‘How To’ and Tutorial Subjects Available The Plastics Pipe Institute, Inc. (PPI) today announced that another free library of instructional videos is available on the association’s website and YouTube channel. Called ‘Training Shorts’, the teaching modules focus on piping materials such as CPVC, HDPE, PEX, PE-RT, PP. Topics include joining, installation, fusion, trenching, design Read more
Concise ‘How To’ and Tutorial Subjects Available
The Plastics Pipe Institute, Inc. (PPI) today announced that another free library of instructional videos is available on the association’s website and YouTube channel.
Called ‘Training Shorts’, the teaching modules focus on piping materials such as CPVC, HDPE, PEX, PE-RT, PP. Topics include joining, installation, fusion, trenching, design, testing, sustainability plus other subjects important to those involved in drainage, natural gas, heating, plumbing, water, and sewer systems plus conduit projects. Not only an educational tool, the information contained in the videos can also be used for bid documents, according the association. PPI is the major North American trade association representing the plastic pipe industry.
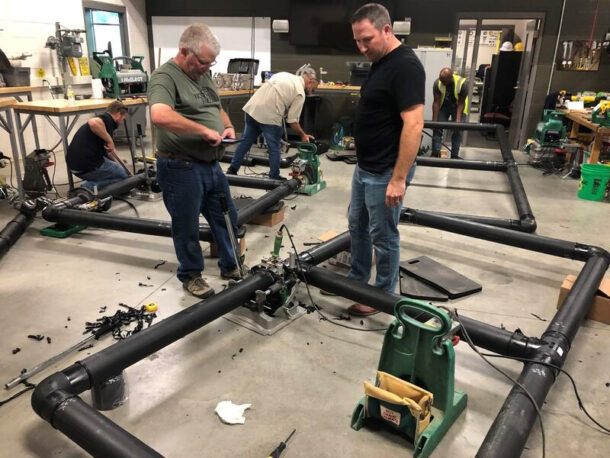
“The PPI Training Shorts series of videos deliver quick and clear instruction,“ stated David M. Fink, president of PPI. “Currently, we have nearly 30 video courses, with most running under three minutes. We’ve been able to create videos that get right to the heart of the matter because of our members who have contributed their time and knowledge. They hear first-hand what is important and what is not as well as where to find additional information on these subjects.”
Episodes include Life Cycle Analysis Results & Benefits, Fitting for PEX and PE-RT Tubing, Basics of Butt Fusion, How HDPE Conduit Materials are Specified, and Composite Pipe Introduction. Other subjects will be added periodically.
Training Shorts couples with the association’s eLearn™ educational channel that contains a catalog of plastic pipe programs, which are self-paced and built on a module platform. A certificate of completion is awarded at the end of each course. It can be found at https://elearn.plasticpipe.org/
The Plastics Pipe Institute’s website with links to its divisions is: www.plasticpipe.org.
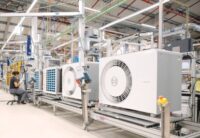
Home Comfort business will nearly double Bosch chairman Stefan Hartung: “Biggest transaction in Bosch history and important milestone in the implementation of our corporate strategy for 2030.” Bosch deputy chairman Christian Fischer: “Acquired entities will strengthen Home Comfort in an extremely attractive segment, and will become part of Bosch core business.” Expansion of presence in Read more
Home Comfort business will nearly double
- Bosch chairman Stefan Hartung: “Biggest transaction in Bosch history and important milestone in the implementation of our corporate strategy for 2030.”
- Bosch deputy chairman Christian Fischer: “Acquired entities will strengthen Home Comfort in an extremely attractive segment, and will become part of Bosch core business.”
- Expansion of presence in U.S. and Asia
- Innovative, energy-efficient solutions for the move to alternative energy and for helping to mitigate global warming.
- Bosch Home Comfort Group sales revenue to increase from roughly 5 billion euros to 9 billion euros.
- Integrated unit will then have workforce of more than 26,000 and complementary portfolio at the interface between heating and cooling.
Bosch, the supplier of technology and services, is continuing its growth course with a strategic acquisition. For its Energy and Building Technology business sector, the Bosch Group plans to take over the global HVAC solutions business for residential and light commercial buildings from Johnson Controls. As part of this transaction, Bosch also intends to acquire 100 percent of the Johnson Controls-Hitachi Air Conditioning (JCH) joint venture, including Hitachi’s 40 percent stake. The Bosch shareholders and supervisory board have approved the transaction. Binding agreements on the acquisitions were signed by the parties involved today. The acquisition is subject to approvals from the antitrust authorities. The purchase price for the acquired businesses is 8 billion dollars (7.4 billion euros). The acquisition is expected to be closed in approximately 12 months.
“As the biggest acquisition in Bosch history, this is an important milestone in the systematic implementation of our strategy for 2030. We are dynamically pushing ahead with the strong development of Bosch, and will achieve a globally leading position in the promising HVAC market with this acquisition,” says Stefan Hartung, chairman of the board of management of Robert Bosch GmbH. “In taking this step, moreover, we will strengthen our presence in the U.S. and Asia and achieve a better balance among our business sectors. This is also part of our strategy. In this way, we will open up further growth opportunities and put the company as a whole on a firmer footing.”
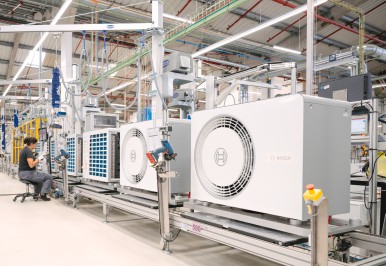
Together with JCH, the businesses Bosch intends to acquire generated sales revenue totaling roughly 4 billion euros in 2023, and employ some 12,000 people worldwide. The transaction includes 16 manufacturing sites and 12 engineering locations in more than 30 countries. The product portfolio covers the entire spectrum of HVAC solutions for residential and light commercial buildings, and includes well-known brands such as York and Coleman in the U.S. and Hitachi in Asia, for which Bosch will be granted a long-term license.
Christian Fischer, the deputy chairman of the board of management of Robert Bosch GmbH who is responsible for the Bosch Group’s strategic growth initiatives, and thus for this planned acquisition, adds: “With this acquisition, Bosch will accelerate its growth and nearly double its sales revenue in the HVAC market to roughly 9 billion euros. Together with our future colleagues, we want to seize the huge opportunities offered by the market for the further growth of this new unit.” The company expects the global HVAC market to grow 40 percent by 2030, driven by technological progress, the fight against climate change, and new regulations. “The acquired businesses will become part of the Bosch core business – and this will benefit customers, installation partners, and associates,” Fischer adds. “We have proved several times in the past that we can successfully integrate brands, take them forward through investments, and strengthen them.”
In the words of George Oliver, CEO of Johnson Controls: “Our leading residential and light commercial business and its world-class team perfectly complement the Bosch portfolio. We are confident that under Bosch’s leadership the business will continue to excel and deliver innovative products and service to its customers. We look forward to seeing their continued success.”
Jun Abe, executive officer and executive vice president at Hitachi, and executive officer and general manager of the Hitachi Connective Industries division, says: “The new partnership with Bosch to establish a global air-conditioning business is an important step. The market is dynamic, and is flourishing. I firmly believe that a global supplier such as Bosch, with its strong European presence and many years of experience in the heating business, is the optimum partner for further expanding the global air-conditioning business of the longstanding Hitachi brand.”
Innovative, energy-efficient solutions for mitigating global warming and the move to alternative energy
The current transformation in technologies and market conditions in the field of HVAC solutions opens up huge opportunities for supplying innovative and energy-efficient solutions for mitigating global warming and the move to alternative energy. Heating technology is moving away from fossil fuels such as oil and gas toward heat pumps and heat pump-hybrid solutions. At the same time, air-conditioning technology is growing in importance both in Europe and worldwide. Frank Meyer, the Bosch management board member responsible for the Energy and Building Technology business sector, and thus also for the Bosch Home Comfort Group and the integration of the new unit, says: “It is Bosch’s aim to play an active part in shaping the innovative and growing market for energy and building technology, and to occupy a globally leading position. With this acquisition, we are improving our position, especially in air conditioning. In addition, we will be able to globally expand our heat-pump business and achieve greater economies of scale. With our technology and our products, we can work together to make a bigger contribution to energy efficiency and to more comfort and a better quality of life for many people in light of global warming. That’s ‘Invented for life’ in its truest sense.”
Complementary portfolio, established brands, and a strong team
Bosch intends to integrate the acquired businesses into the Home Comfort Group. The 14,600 associates of the existing Bosch Home Comfort Group generated sales of roughly 5 billion euros in 2023. Home Comfort is excellently positioned in the major segments of the heating market, of the heat-pump market, and of the market for heat pump-hybrid solutions, which comprise a heat pump and a fossil fuel-fired boiler for peak loads. Following the transaction, the new unit will have a workforce of more than 26,000 and be able to benefit considerably from economies of scale and a complementary portfolio at the interface between heating and cooling. Jan Brockmann, president of the Bosch Home Comfort Group, says: “With our successful heating technology in Europe, we already have a strong team and a sound foundation. Now is the right time for a bold step toward a global presence. Demand for air-conditioning solutions is growing especially fast.” In the U.S., for example, Bosch expects to see more than 50 percent growth by the end of the decade, and in Europe as well, strong growth of approximately 30 percent is forecast up to 2030. Together, we will be able to build on strong, well-established brands. We are looking forward to shaping the future of the Bosch Home Comfort Group with our future colleagues and their innovations and ideas,” Brockmann adds.
The HVAC business Bosch plans to acquire from Johnson Controls has an especially strong presence in the United States and Asia. In the United States, its portfolio focuses on ducted solutions in which air passes from a central source through ducts in order to heat or cool all rooms at the same time. In Asia, it especially sells ductless solutions, where interior units in each room can heat or cool individually, as well as modern air-conditioning systems based on variable refrigerant flow (VRF) systems. This technology is used in commercial applications ranging from light commercial premises such as retail stores to large projects such as hotels and hospitals. The portfolio in these regions is supplemented by efficient air-water heat pumps, which Johnson Controls offers above all in Europe.
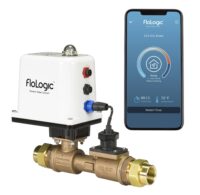
Trusted manufacturer of premium water heating solutions acquires North Carolina-based manufacturer of advanced leak detection and shutoff technology Bradford White Corporation, an industry-leading manufacturer of water heaters, boilers and storage tanks, announced today the acquisition of FloLogic, a North Carolina-based manufacturer of premium plumbing leak detection and automatic shut off solutions for homes and light commercial Read more
Trusted manufacturer of premium water heating solutions acquires North Carolina-based manufacturer of advanced leak detection and shutoff technology
Bradford White Corporation, an industry-leading manufacturer of water heaters, boilers and storage tanks, announced today the acquisition of FloLogic, a North Carolina-based manufacturer of premium plumbing leak detection and automatic shut off solutions for homes and light commercial buildings.
The acquisition aligns with Bradford White’s commitment to innovation and quality and enhances the company’s smart technology offerings. FloLogic’s premium IoT-based leak detection and automatic shutoff technology offers a comprehensive solution and state-of-the-art protection from plumbing leaks, the most preventable cause of property damage and a significant source of water waste. The system’s robust IoT platform can be monitored in real time via an app for constant connection and protection.
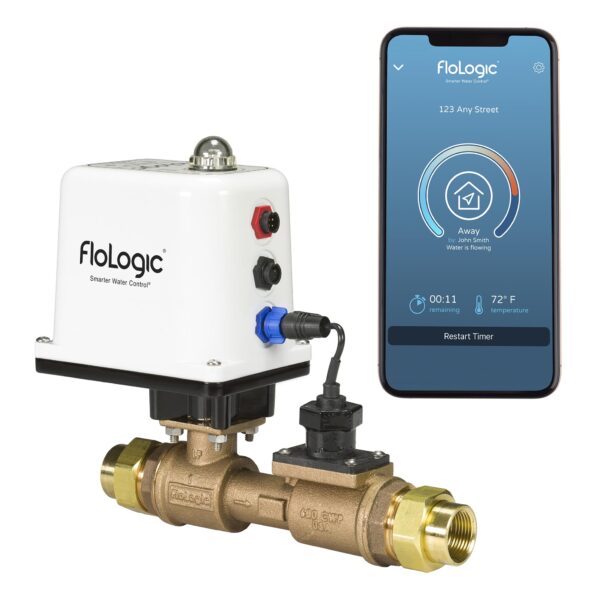
“We’re proud to welcome FloLogic into the Bradford White family,” said Bruce Carnevale, president and CEO of Bradford White Corporation. “Their expertise, market leadership and trusted technology will be integral to Bradford White as we continue to meet the needs of our customers in a rapidly evolving industry. This acquisition will allow us to expand the reach of FloLogic, leveraging our strong customer relationships.”
Founded in 1996 in Raleigh, North Carolina, FloLogic is a pioneer in plumbing leak detection and has become a trusted name in the marketplace, focusing on quality and innovation over the past two decades. FloLogic’s partnerships with major North American insurers have boosted leak detection technology adoption and increased consumer awareness.
“We are thrilled that FloLogic will become part of Bradford White Corporation,” said Chuck DeSmet, founder, president and CEO of FloLogic. “I am very proud of the company we’ve built, and this acquisition will allow FloLogic to continue to grow, innovate, and better serve our customers with the additional resources and support from Bradford White.”
The expertise in IoT from FloLogic will be a great asset to Bradford White and allow them to build upon their capabilities in this area as they look at future innovations and provide expanded solutions to meet the needs of their customers.
“We are very excited to add this new product line, technology, and team of dedicated employees to the Bradford White family,” said Glenn Griffin, senior vice president and CIO at Bradford White Corporation, who will lead the integration. “The FloLogic team has pioneered the leak detection industry and built one of the leading solutions in the marketplace.”
Current FloLogic customers should continue to use their existing contacts for sales and service support.
For more information about Bradford White and its trusted water heating, space heating, combination heating and storage products, visit www.bradfordwhitecorporation.com.
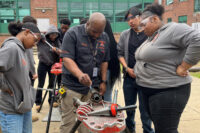
Bullard-Havens Technical High School to receive water heaters, service parts through Industry Forward® charitable giving program Bradford White Corporation, an industry-leading American manufacturer of water heaters, boilers and storage tanks, is continuing its support of hands-on training and education by donating water heaters, service parts and in-person training to the Bullard-Havens Technical High School, located Read more
Bullard-Havens Technical High School to receive water heaters, service parts through Industry Forward® charitable giving program
Bradford White Corporation, an industry-leading American manufacturer of water heaters, boilers and storage tanks, is continuing its support of hands-on training and education by donating water heaters, service parts and in-person training to the Bullard-Havens Technical High School, located in Bridgeport, Connecticut.
The in-kind contribution of water heating products is funded by Bradford White’s signature charitable giving initiative, Industry Forward®. The company’s technical field trainers are also donating their time to provide in-person training to Bullard-Havens students. In addition, students will get access to Bradford White’s exclusive educational resources to enhance their classroom learning experience.
“Bradford White is dedicated to supporting organizations that help develop the skilled trades workforce of the future by offering funding for a range of programs and hands-on learning opportunities,” said Rebecca Owens, senior manager of communications for Bradford White. “Bullard-Havens is an excellent technical school that is committed to the success of its students and the trades. The suite of water heaters, service parts and in-person training will equip Bullard-Havens students with essential tools to prepare for good-paying jobs in the industry.”
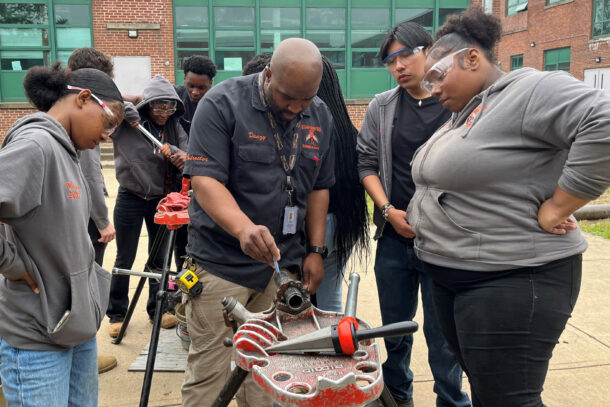
Bullard-Havens, part of the Connecticut Technical Education and Career System, serves a diverse population of students from various socio-economic backgrounds. The school offers high-quality technical education and training in 13 skilled trade areas to prepare students for successful careers. Bullard-Havens is dedicated to providing the 72 students enrolled in the plumbing and heating program with comprehensive training and education to ensure they have opportunities for a successful career in the plumbing industry.
“Our program’s impact extends beyond technical skills, as we also focus on instilling professionalism, work ethic, and a strong understanding of industry standards and practices,” said Keith Danzy, head of
the Plumbing & Heating Department at Bullard-Havens. “This incredible investment in our program for our students will enhance the skills needed for a career in the plumbing trade.”
The items donated by Bradford White to Bullard-Havens include:
- 50-gallon residential gas water heater
- 50-gallon residential electric water heater
- Aerotherm® heat pump water heater
- Infiniti® tankless water heater
- Service parts package to facilitate hands-on training for students in repair and maintenance
Bradford White partners with nonprofit organizations and technical schools to educate individuals and families on the importance of the skilled trades and the role that industry professionals provide in the health, safety, sanitation and infrastructure of their communities. The company provides strategic grant funding to support workforce development training, education programs, industry career opportunities, events and partnerships.
For more information about Bradford White Corporation’s Industry Forward® initiative, visit bradfordwhitecorporation.com/giving.