I was talking the other day with my buddy who lives northern Wisconsin on the topic heat pump water heaters (HPWHs). You see, he is in the market for a water heater and was asking my advice on those particular units. Wanting to know more myself, I pulled up some info and the more in-depth Read more
Featured Articles
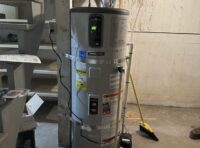
I was talking the other day with my buddy who lives northern Wisconsin on the topic heat pump water heaters (HPWHs). You see, he is in the market for a water heater and was asking my advice on those particular units. Wanting to know more myself, I pulled up some info and the more in-depth I got, the more I wanted to know. Cold weather performance, special ducting, size of mechanical space, accessibility to air, cooling and conditioning of adjacent space are all very important topics of discussion.
But, wait a minute, I thought to myself, I can use some of my “superpowers” as an editor in the trades these past 20+ years to ask people who are more in the know about HPWH than me.
I recently reached out to few people I trust to give me honest assessments of these units.
Advantage Heat Pump Water Heaters
According to Eric Aune, Aune Plumbing, Heating & Drains, there has been a ton of marketing to the public, and even more incentives for installation. “Local utilities are offering rebates upwards of $2-3K in some places, and here in Minnesota, we aren’t seeing rebates that high but it’s clear why the rebates are offered—because its lowering and spreading the load on the grid over longer periods at lower consumption rates. The utilities are trying to stay in front of or (most likely) catch up to the growing demand and stress on the grids all across the country. HPWH’s are one piece to the puzzle.”
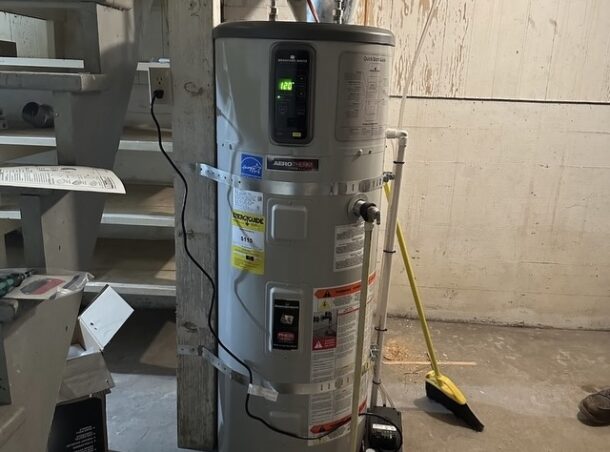
John Siegenthaler, P.E., Appropriate Designs, gives three bona fide advantages for HPWHs: One, they are excellent for capturing “surplus heat” (e.g., heat that’s present but not generated by another heat source for the purpose of warming the space). For example, solar heat gain to a garage, or heat generated by computer servers. Two, when properly applied, they can generate a given amount of DHW on about 1/3 the electrical input required by a standard “resistance type” electric water heater (tank or tankless). And three, some models are available that can operate on 120 VAC power, whereas all electric resistance water heaters require 240 VAC power.
But in Cold Climates?
But are these units considered more inefficient the more you climb the northern latitudes to colder climates? “Although heat pump water heaters are often placed in unconditioned spaces such as garages in southern locations, it would be a big mistake to do so in a cold northern climate where outside temperatures are below the minimum operating air temperature for the HPWH for weeks or months during winter,” says Siegenthaler. “The heating performance of any air source heat pump—ductless, central, air-to-water, HPWH, always decreases with decreasing air temperature—Putting any water heater in a cold space is not recommended. Standby heat loss would definitely increase.”
HPWHs have minimum air flow requirements, especially if placed in confined spaces, adds Siegenthaler. The I/O manual supplied with the unit should give all these requirements. “Some units allow ducting of outside air to the heat pump assembly on top of the tank, but I would only use this option in a relatively warm climate. Using ducted outside air also foregoes the cooling and dehumidifying benefit of the HPWH,” says Siegenthaler.
Living in Minnesota, Aune says, “HPWH’s capture/transfer the heat in the space surrounding them to the tank of water. When you talk about this here in Minnesota, it’s common for people to consider this inefficient since the we have to heat with a boiler or furnace, so aren’t we running our space heating system to provide heat for the water heater?
“The reality is the HPWH is able to capture and transfer a lot of energy without major negative effects on the conditioning and comfort of the space with a few considerations like ducting the less humid, colder air to the exterior of the house or even moving it with the furnace or exhaust fans,” says Aune.
According to Gary Klein, principal, Gary Klein and Associates, the majority of HPWHs sold today are hybrid HPWHs, and their efficiency is rated at 67.5 F and 50% relative humidity. “Very close to the temperature we keep the inside of conditioned buildings,” says Klein.
Klein suggests an interesting concept by managing the cold discharge air. “Install the HPWH in the basement near the space conditioning system. Use the return of that system to suck in the cold discharge air from the HPWH and distribute it throughout the house. Use a relay to link the fan to the HPWH. Let the thermostat decide if the air needs to be conditioned. Install a very large filter grille to bring air to the room where the HPWH is installed. (2-inch pleated filters).
“Need the ability to move at least 60 cfm per 100 watts of compressor, fan and control power. Warmer intake air increases the coefficient of performance (COP),” says Klein.
Siegenthaler points out that he did a column earlier this year that discussed a situation where a modern house used an air source heat pump for space heating, and combined it with a HPWH inside the house for DHW. Technically this puts the two heat pumps into a “cascade” relationship, says Siegenthaler.
“Think of the space heating heat pump as ‘feeding’ heat to the HPWH. It’s possible to show that the overall efficiency of this arrangement is lower than using a single air-to-water heat pump for both space heating and domestic hot water (DHW). I think that this is important because many builders, architects, energy planners, energy auditors, etc. don’t necessarily understand this concept. They assume that two heat pumps—one for space heating, and the other for DHW—are better than one.”
Siegenthaler stresses that the “ideal” scenario for a HPWH is to put it in a space where there’s “surplus heat.” “Don’t rob Peter to pay Paul,” says Siegenthaler.
There are plenty of such spaces, suggests Siegenthaler, especially in commercial buildings—manufacturing, heat from vending equipment or refrigeration equipment, cooking, laundry, computers, solar gain, attics that remain above 35ºF year-round, even mechanical rooms with lots of uninsulated piping, boilers, electrical transformers, greenhouses, cannabis grow houses, etc.
“Paraphrasing Patrick Henry, ‘Give me air, or give me death,'” says Klein.
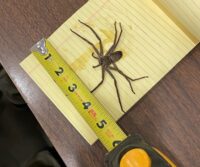
Okay, let’s not get out of control here. The pic below (and on the homepage) was taken at my nephew’s work. He opened a crate, which was delivered from Taiwan, and out jumped this huntsman spider, alive! YIKES! We thought it would be fun to ask some of our industry friends what would they rather Read more
Okay, let’s not get out of control here. The pic below (and on the homepage) was taken at my nephew’s work. He opened a crate, which was delivered from Taiwan, and out jumped this huntsman spider, alive! YIKES!
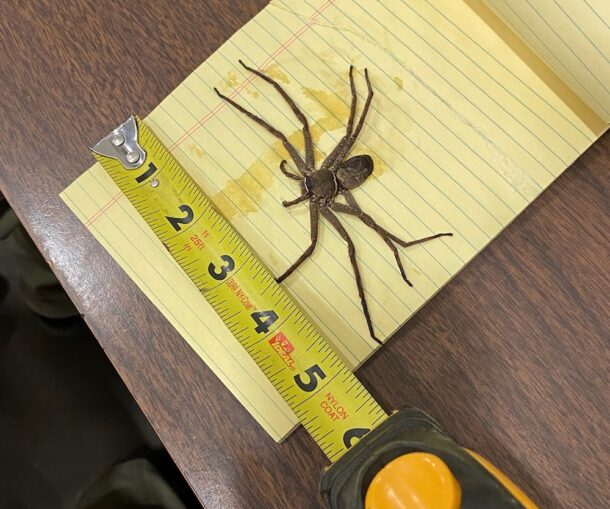
We thought it would be fun to ask some of our industry friends what would they rather encounter on the jobsite or in a tight crawlspace—spiders, rats or snakes?
Before we get to the responses, here’s a little background info …
… With more than 30,000 species of spiders in the U.S., only two are of any real concern: the black widow and the brown recluse. Although this info is a bit outdated—Feb 2001—according to U.S. Bureau of Labor Statistics, insects and arachnids inflicted 36,100 nonfatal occupational injuries and illnesses involving time away from work in the 1992-97 period. This was almost half of the total number of animal-related workplace injuries and illnesses.
It is estimated that less than three deaths per year occur from spider bites. However, most victims are children, this according to info provided by the Boston Children’s Hospital. Most of the 30,000 or so species of spiders found in the United States are poisonous, but their fangs are too short or too fragile to break through human skin. The bites of most spiders cause only minor, local reactions.
According to American Family Physician website. spiders inflict serious bites to humans because of their delicate mouthparts and impotent or prey-specific venoms. However, some spiders produce toxic venoms that can cause skin lesions, systemic illnesses, and neurotoxicity.
The Center for Disease Control’s (CDC) National Institute for Occupational Safety and Health says that venomous snakes found in the United States include rattlesnakes, copperheads, cottonmouths/water moccasins, and coral snakes. A venomous bite is called an “envenomation.” Although death from venomous snake bites is rare, a worker with a severe envenomation or allergy to snake venom can die from a venomous bite. Each year, an estimated 7,000–8,000 people are bitten by venomous snakes in the United States, and about 5 of those people die. The number of deaths would be much higher if people did not seek medical care.
Workers are far more likely to suffer long-term injuries from snake bites than to die from them. For those bitten by rattlesnakes, 10–44 percent will have lasting injuries. An example of a disability or permanent injury is the ability to use a finger or losing part or all of it.
And rats and mice? We all know by now that these varmints carry a number of diseases that can infect both people and pets. According the Environmental Protection Agency (EPA), rodent-borne diseases can be transferred directly to humans through:
- Bite wounds
- Consumption of food and/or water or breathing dust contaminated by rodent droppings and other waste products
- Indirectly by way of ticks, mites, and fleas that transmit the infection to humans after feeding on infected rodents.
Ok, now to the responses … Would you rather?
• Danielle “Twig” Browne, facilities management plumber for the Canadian government, stationed at the Memorial University of Newfoundland (@thelittelestplumber)—”I’d prefer bugs! We don’t have roaches here but if we did my answer might change. I can’t stand the smell of rat waste. And, we don’t have snakes on my island so that’s never been an issue for me. A deal breaker would absolutely be a snake though!”
• Mary-Anne Bowcott, owner, Westcom Plumbing and Gas Ltd, as well as Westcom Roofing and Sheetmetal, on Vancouver Island, British Columbia, Canada (@the_ladyplumber)—“Rats or mice. Because I’m used to them and they don’t bother me. They will run and hide if you’re down there as bugs and snakes won’t. Technically where I live, snakes would be the best option because here they are tiny, non-poisonous and don’t live in crawlspaces. But I’ve seen some of the videos on IG and those are def not the snakes we have here. Honestly, bugs and spiders don’t bother me, but there’s always a chance of a black widow, so I’ll choose rats over them.
• Adam Rotherham, owner, Down Under Drainage, Los Angeles (@downunderdrainage)—”In Sydney, Australia, where I’m from, I would probably rather deal with spiders. Generally, I would throw a couple of spider bombs (foggers) under the house a couple of days before I was going under. We have a lot of redback and funnel web spiders in Sydney. Funnel webs are deadly, redbacks not so much; they just give a nasty bite. Sometimes we would get brown snakes around the house, but I’ve never seen one in the crawlspace. I can’t stand the smell of rat and mice urine. In Los Angeles, I’m not really concerned about anything because there aren’t really any snakes, and the spiders are only black widows from what I’ve seen.”
• Linda Hudek, owner, LH Plumbing Services, Fairfield, Ohio (@thebrunetteplumber)—”I’ll take the snakes. I don’t mind the mice and rats, except for the diseases they carry lol. The snakes eat all of the bad stuff, so I’m good with them. I cannot stand it when I have spideys in my hair.”
• Tim Kuhlman, plumbing and hydronic technician, Grasser’s Plumbing & Heating, McNabb, Ill. (@tlkuhlman)—“In reality, I’m big on scene safety. Spiders, mice and snakes bite, and that could affect my health. I go in and sweep out spiders and cobwebs, maybe spray. Mice and snakes you can usually run off, and then I would tarp my work area and light it up.”
• Brent Ridley, owner, Miracle Mechanical, Cumming, Ga. (@miraclemechanical)—”I’ll take spiders/bugs. I don’t do snakes. “I carry a long piece of PEX with me to bat down the spider webs in the crawlspace.”
• Mike Prencavage, owner, The Family Plumber, Los Alamitos, Calif. (@socalplumbguy)—“Rats or mice because they avoid people. Roaches spiders and bugs will crawl all up on you. Honestly, possums are a deal breaker. They are viscous animals, and they will hiss and attack!”
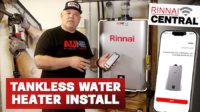
https://youtu.be/xJheBFA3-pU The new Rinnai Sensei RX series high efficiency condensing tankless water heaters have a ton of new features and industry leading technology. This is the NEXT GENERATION of tankless. In this video we are featuring the key features we think are most notable: 1. The RX series tankless is 10lbs lighter than previous models Read more
The new Rinnai Sensei RX series high efficiency condensing tankless water heaters have a ton of new features and industry leading technology. This is the NEXT GENERATION of tankless.
In this video we are featuring the key features we think are most notable:
1. The RX series tankless is 10lbs lighter than previous models
2. Because of new tech there are now just 6 skus instead of the 24 previous
3. Setup can be done using a mobile device without logging on to wifi
4. One tankless model for both indoor/outdoor installation (outdoor requires additional vent attachment)
5. Gas conversion is done without changing parts, using the control or mobile app.
6. Step-by-step mobile app setup.
If you would like more information or technical specifications of the Rinnai Sensei RX series tankless please visit this link: https://www.rinnai.us/professional/sensei-rxp
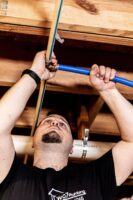
Known as quick-connect, push-on or push-fit, these breakthrough plumbing products are often at the center of plucky online debates. Since entering the U.S. plumbing market in 2004, the design and technology of push-to-connect fittings have revolutionized the industry as a quick, reliable, tool-free solution for connecting small potable water pipes. Driven by feedback from plumbers Read more
Known as quick-connect, push-on or push-fit, these breakthrough plumbing products are often at the center of plucky online debates. Since entering the U.S. plumbing market in 2004, the design and technology of push-to-connect fittings have revolutionized the industry as a quick, reliable, tool-free solution for connecting small potable water pipes. Driven by feedback from plumbers, this product class has evolved robust designs made of materials like rubber, silicon, brass and stainless steel, incorporating key components such as o-ring seals and gripping mechanisms.
But are they best used only as a temporary fix as some users claim, or can you count on them for a variety of long-term uses? We let the facts flow freely so you can make an informed decision on whether to give these fittings a try.
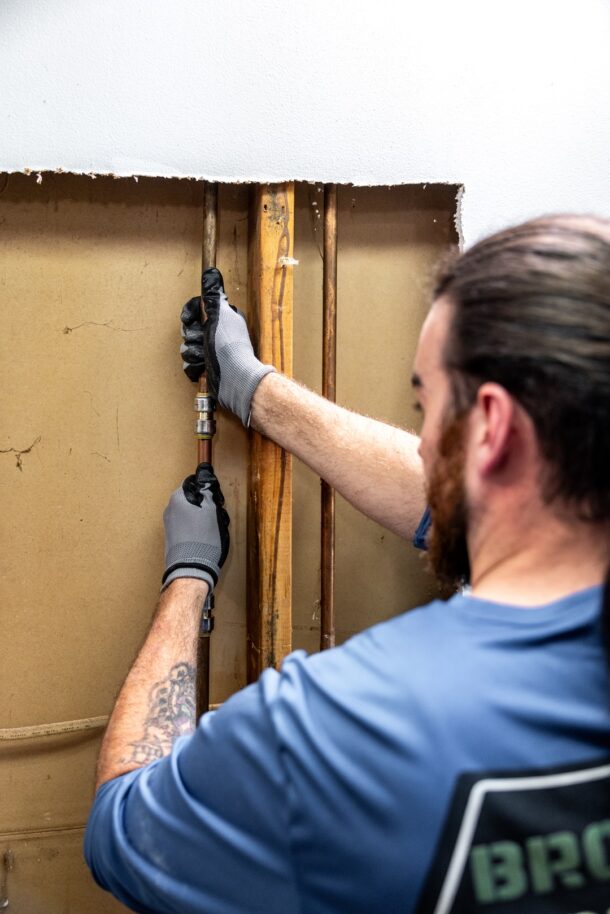
Rapid Adoption and Evolution
Two decades of innovation have made push-to-connect fittings indispensable for applications ranging from residential plumbing to advanced manufacturing. The most common uses are in residential service and repair, including some new builds. They went through a lead-free transition to newer models that are stronger and more durable, accelerating adoption further.
The American-made SharkBite Max model sets the industry standard with a stainless-steel retainer around the outside and a pressure rating of 250 psi. This doubled the burst pressure limit of the original model, the most popular push-to-connect fitting. A deeper insertion depth allows the new model’s steel teeth to engage the pipe more effectively, creating a stronger connection that eliminates the need for an interior tube liner.
Primary Benefits and Advantages of Push-to-Connect Fittings
Using push-on fittings means shorter installation times, fewer errors to correct, and easy, versatile disconnections and reconfigurations. No soldering, crimping, glue or special tools are needed for installation. Unlike conventional approaches, the pipe doesn’t need to be dry before making a connection. Water can be pouring out of a pipe and these fittings can still be quickly connected without a tool, even in a tight space, making them an excellent option for pipe repairs.
Knowing leaks and pipe aging are inevitable, it’s a good practice to keep some push-fit fittings handy. If it’s a failed joint pinhole leak, a push-to-connect fitting can be a fast, reliable and inexpensive solution, especially in areas where pipes are prone to freezing and bursting.
Other strengths of today’s push-fit models include:
- Perfect for transitioning between pipe materials, including copper, PVC, PEX, CPVC, PE-RT and HDPE (SDR-9)
- Fitting rotates around the pipe even after it’s connected
- Strong manufacturer warranties (SharkBite Max warranty is 25 years)
- Code approved to be buried underground (when wrapped in silicone tape) or installed behind walls
- Compliant with all regulatory changes
The simplicity and efficiency of push fittings have streamlined a handful of core plumbing tasks and even helped address labor shortages by making it easier to get new plumbers out in the field performing repairs quickly. They’ve also made basic and emergency plumbing repairs accessible to DIYers. However, despite their versatility, they’re not ideal for every situation.

Drawbacks, Limitations and Criticisms
Push fittings must be used in the right way to capitalize on their advantages. In the rare case when there’s a problem, installing them improperly or in a spot they’re not designed for is almost always the cause. By keeping a few points in mind, you can make the right decision every time on when and where to use them.
Here are the main things to consider for a smooth experience:
Initial Cost: The best push-to-connect fittings can be a bit pricier than soldering or crimping. You’ll save big on labor installing them faster, but the upfront cost per fitting can be higher.
Compatibility Limits: While leading push-fit fittings are compatible with almost all pipe types, they don’t work with everything, like galvanized steel or flexible hoses. And they still require specific fittings for certain transitions, like polybutylene to CTS tubing. This adds a step to some jobs and possibly to inventory management.
Not for All Applications: Standard push fittings are certified for potable water and radiant heating installations, limiting their use in industrial plumbing. Exceeding the certified limits (250 psi and 200°F for Max fittings) can lead to failures, so they’re not suitable for all high-pressure or high-temperature applications.
Designed for Single Use: While push-to-connect fittings can be removed if you need to adjust or test, they’re not designed to be reused multiple times in permanent installations. The integrity of the seal may be compromised with repeated removal and reinsertion.
Spotting Leaks: All push-to-connect fittings rely on o-rings for sealing. If the fitting isn’t installed correctly — such as failing to deburr the pipe — or gets jarred out of place inadvertently, the o-ring can get damaged, potentially leading to leaks. Although rare, leaks inside the fitting can be tougher to spot, so they might not be noticed immediately.
You’re best off choosing manufacturers that are transparent about the materials they use in their fittings, especially the o-rings since they keep the seal. For example, SharkBite Max o-rings are made of a specific type of rubber called EPDM (Ethylene Propylene Diene Monomer), chosen for its durability, flexibility and chemical resistance:
- EPDM is known for its resistance to aging and degradation, making it suitable for long-term plumbing applications
- It maintains its flexibility even at lower temperatures, ensuring a good seal
- EPDM is specifically selected for its resistance to chloramine, a disinfectant chemical often added to municipal water
Of these concerns, leaks are the most hotly debated. Some professionals still hesitate to use push-to-connect fittings behind walls because of concerns about long-term reliability and potential hidden leaks. But after two decades of continuous improvement and in-wall use by plumbers in homes and other buildings across America, these isolated instances can always be traced back to user error. Common causes of fitting failure include:
- Pipe that is unevenly cut, not deburred or not free of debris, potentially preventing a secure seal
- Using the wrong fitting for the wrong application
- Not marking the insertion depth to ensure that you pushed the pipe all the way into the fitting
- Not wrapping fittings in silicone tape that protects it from soil contaminants
- Rough or repeated disconnection
When it comes to quality, the widespread adoption of push-to-connect fittings speaks for itself. But don’t take anyone’s word for it. Test them out for yourself and you’ll see why they’ve become so popular with pros everywhere.
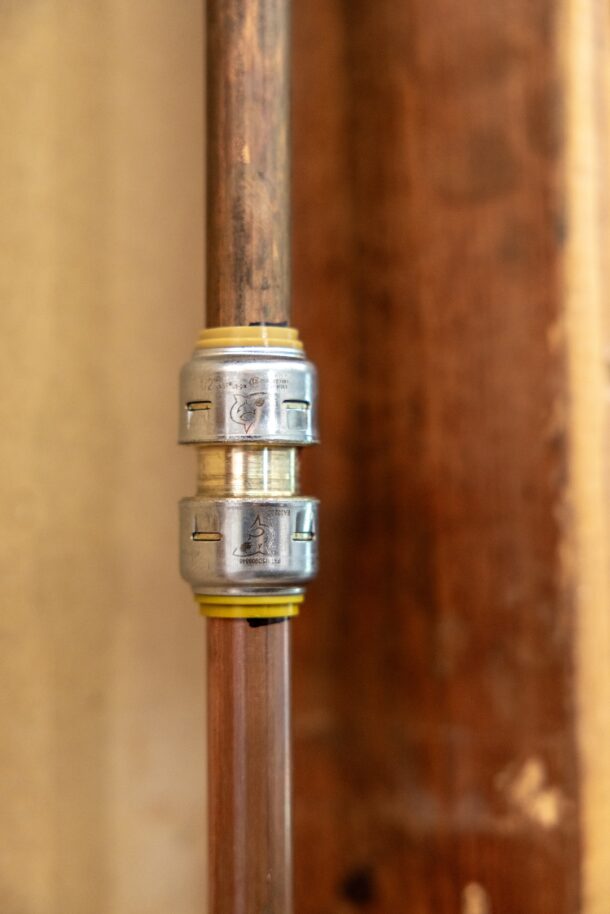
Plumbers Shape the Evolution of Push-to-Connect Technology
You can play a role in shaping this product’s evolution by sharing your thoughts and experiences directly with manufacturers. The best way to help drive the evolution of plumbing technology is for plumbers of all skill levels to share and connect online—post product reviews and reach out with comments and questions on social media or through company websites. Equipment manufacturers can serve you best when they hear from you often, and the most innovative tend to be more responsive to feedback.
Some manufacturers have employees who will share free resources like training materials and demonstrations to help plumbers integrate their game-changing products. If you ask nicely, they might even send someone to walk the job site with you when they can. Dropping the company a line on your favorite social channel is a great way to make another connection that’s built to last.
Written by Matt Glenn, senior product manager at RWC, a market leader and manufacturer of water control systems and plumbing solutions for residential, commercial and industrial applications.
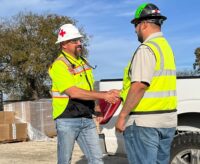
There’s a number out there that is pretty remarkable: 65% of construction workers that took their own life sought some sort of medical help within one month prior to the event. As we near the end of Men’s Mental Health Month—recognized every year in the month of June—suicide rates among construction workers are at an Read more
There’s a number out there that is pretty remarkable: 65% of construction workers that took their own life sought some sort of medical help within one month prior to the event.
As we near the end of Men’s Mental Health Month—recognized every year in the month of June—suicide rates among construction workers are at an alarming level. According to the Center for Disease Control (CDC), an estimated 6,000 construction workers died by suicide in 2022. In fact, the CDC found that men working in construction have one of the highest suicide rates by population: their rate of suicide is about four times higher than the general population and is the second-highest rate of all workplace industries at 45 per 100,000.

But why is the suicide rate so much higher in construction than other professions? Fact is, construction is an at-risk population for suicide. “Construction is a perfect storm for a predisposition for depression and suicide,” says Dr. Dan Carlin, MD, Founder and CEO of World Clinic / JobSiteCare, a resource to create safe workplaces and deliver great healthcare on the job.
Mental health is no different than, say, heart disease or diabetes. It is a dissolution of brain tissue. “If you are thinking of killing yourself, your brain is not working in a healthy manner,” says Carlin.
Crescendos and Dislocations
So, throw it back to that stat thrown out at the beginning of this article: Is there any relevance to that, you ask? Well, yes. A connection can be made between injury and suicide. Construction jobs in general can be tough on the body, and for those injuries that happened as a direct result of the work, individuals tend to self-medicate for the chronic pain. And, that can come in the form of prescribed drugs, illicit drugs (opiates, for example) and alcohol. But as the medication wears off, withdrawal sets in and the brain becomes vulnerable, with bad feelings magnified.
“Self-reliance and stoicism form a unique crescendo,” says Carlin. And men, more than women, fall into these characteristics. Especially in a male-dominated industry such as construction, the psychosocial aspect sees men focusing on things, whereas women tend to concentrate on people. Men are programmed to just shake things off in the face of adversity; address challenges in a more stoic nature. “Women are much more aware with other people than men.” says Carlin. “Men normally don’t look to others to talk. Men are more mission-focused—get the job done, on time.”
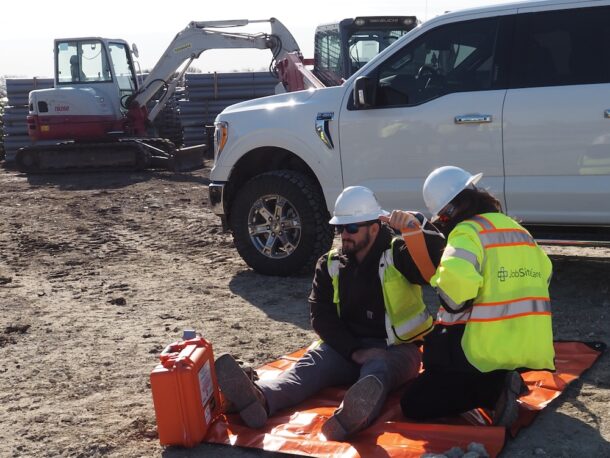
Often is the case in construction, one works long, rigorous hours, and often times away from family for long stretches of time. New projects arise and those old jobs come to an end—or one leaves one job for another that pays 20% more but loses that support network, which creates physical dislocations, says Carlin, and that usual social network goes away, resulting in less contact with family. Because the work dynamic has changed, this can lead to a dislocation to the family network, which can lead to friction and a sense of heightened vulnerability.
And let’s not forget COVID. “COVID was a tremendous paradox that has driven a lot of this due to social isolation, leading to depression and anxiety,” says Carlin.
Social Acceptance
Are we at a place in time where men in particular are more comfortable talking about mental health? It’s getting to a level of acceptance. “We’ve made a lot of progress but we aren’t all the way there yet. It’s not a sign of weakness. We need to be strong to share enough and aware enough to ask,” says Carlin.
Thomas Young, TY Custom Builders and Motherflushers Plumbing, agrees, saying, “I definitely think it’s more acceptable to talk about it. I think the people that are open about their issues or some of the people that are probably the ones that are dealing with it more than anybody. It shouldn’t be ‘hey, I’m an adult or I’m a man and I’m gonna deal with this on my own.’”
Easier said than done, some of the ways to reduce stress and damaging brain tissue is to cut back, be it work hours or substance abuse. Steps to increase brain health include exercise—which helps relieve stress, burning off anxiety—eating well and having a rhythmic day.
“When I’m overworked/stressed, I will just unplug, perhaps binge watch a show, and reach out to someone that helps bring peace,” says Young.
And that reaching out could include social media. “Social media has helped me create great friends,” says Young. “I have friends that live in different countries and will reach out, which can mean a lot.”
But, as we all know, social media, while supportive in so many ways, can have its negative rabbit holes. “With hateful comments and bullying, it was something that bothered me a lot in the beginning and I’d delete right away, but most the time,” says Young, “I can laugh it off or even engage back and it can help engagement.”
There is no one-size-fits-all solution to this. According to Carlin, “The nature of the cure starts at a community level where we need the confidence to ask, ‘how are you doing?’” Carlin says it’s important to establish relationships, and find an opportunity to talk about mental health when the time is right. “We can all learn to be a better listener and share stories about problems we all have as a community. We need to come to an awareness that the solution is us,” says Carlin.