By Heather Ripley Most humans are resistant to change. But in order to keep up with the times, change is nearly always necessary. That goes for your home service business’s appearance and messaging. If you’ve been in business for a decade or more, your logo and website may look dated. Or maybe you’ve become more Read more
Industry Blogs
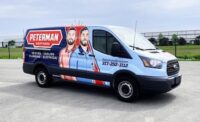
By Heather Ripley
Most humans are resistant to change. But in order to keep up with the times, change is nearly always necessary. That goes for your home service business’s appearance and messaging.
If you’ve been in business for a decade or more, your logo and website may look dated. Or maybe you’ve become more specialized in your services and want to convey this message to new customers.
Either way, it could be time to consider a rebrand.
But don’t make this decision lightly. A rebranding is more than just a change in your logos, the colors you use, your truck wraps and your website.
Rebranding should be about overhauling your business’s look, its attitude and the way it communicates its new vision to current customers and the new customers you want to attract.
One of the best ways to successfully rebrand is to tap a public relations team to help you with your market research and strategy, and to assist in developing the right message that encompasses your new look, attitude and vision.
The Reasons for Rebranding
Rebranding isn’t a task to take lightly. While it may be prudent to upgrade your logo to incorporate more modern icons and pull your website out of its 2000s doldrums, cosmetic changes won’t solve the problems you may be having attracting your target customers.
In order to make your rebranding a success, you need to take an impartial look at your current mission and value statements and see if they align with who you are as a company now. Your mission statement may be outdated or simply not reflect what your business has evolved into.
If you started as a plumbing company but now offer HVAC and electrical services, for example, your message needs to be more inclusive of your updated service offerings. Or maybe your company started more than 50 years ago and is now run by the grandchildren of the founder. Not only has the ownership changed in that time, but the vision has, as well.
But whatever the reason, you need to strategize with experts on how to successfully update your brand. A PR team that knows the home service industry will understand your issues and have experience in helping other companies with their rebranding efforts. If you already have a PR team, don’t forget to include them in your strategy sessions. Their knowledge of your company, the industry, and even your customers, is invaluable.
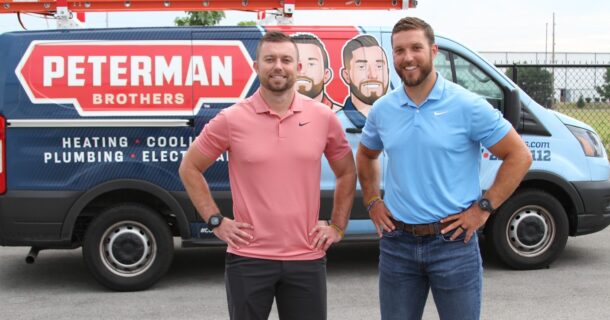
The Right Audience
For many plumbing and HVAC contractors, one of the best ways to scale their business growth is to attract customers who have never used their services before.
To bring in those new customers, you have to get your message out to where they live. While truck wraps and websites are still relevant, they are passive ways to reach customers. In today’s world, you need to be active on social media and you need to be putting your expertise on display.
If the weather is turning cold, writing a press release about how to protect your pipes is one way to reach out, but a PR team can carry that further. Not only do most of their content experts know how to write a release in Associated Press style, they also have media relations people who will pitch your press release to local and trade media journalists.
If you’ve ever turned on the news only to see your biggest competitor interviewed about weather-related problems in the home, chances are they weren’t just lucky – they probably had a PR team pitching their experts.
PR teams also know when the audience you want to reach is online and where they are spending their time.
As an owner, you should be writing your business plan and holding training sessions instead of spending your time pitching your expertise to journalists or engaging with customers online. Hire a PR team to do that for you. Especially one that knows your industry.
The Right Message
If your current brand no longer tells your story or doesn’t tell customers why you’re different, it’s time to rebrand.
But if you don’t have a handle on how best to tell your story or explain why customers should hire your crew, it’s time to call in the experts.
PR agencies hire content writers for a reason. These professionals know what resonates with audiences and can wordsmith your message so that it stands out from your competition. Just as you know the Global Warming Potential (GWP) of the latest refrigerant, a PR writer knows what words work with a particular audience.
Bringing in a public relations agency to help you nail the message is just good business, according to companies like Peterman Brothers, which rebranded from Peterman Heating, Cooling & Plumbing in the spring of 2021.
The company had been known as Peterman Heating, Cooling & Plumbing, but once brother owners Chad and Tyler Peterman began leading the company, they wanted a new name, look and vision to celebrate their family history and honor their father’s mission.
“Ripley was critical in our rebranding efforts made back in 2021,” said Peterman Brothers President Chad Peterman. “While our new brand had a similar feel to our old one, the main difference was in the story behind the brand. Ripley helped promote the new brand in the communities we serve, and that allowed people to make a connection. Building a brand story is critical to any business. Ripley helped us tell our unique story.”
Protecting Your Message
Once you’ve researched your avatar customer, updated your marketing assets and crafted the right message for the right audience, the rebrand isn’t done.
Now is the time you need to create a strategy to protect the rebrand.
If you’re like most home service business owners, you know that a crisis isn’t just possible, it’s most likely inevitable. You have team members that physically go inside customer homes and work on equipment that is essential to their daily lives. This could create many problems.
Let’s say you may have made a poor judgment call and hired a rude service technician or installed a system that broke down within a few days of service. No matter what the issue is, you shouldn’t be caught flatfooted.
That’s why it’s essential to have a crisis communications plan in place for when these events occur. You’ve spent a great deal of time and money updating your assets and developing a new message that better reflects your company’s new vision. You don’t want that ruined because of a human mistake.
A PR team can help you craft a crisis communications strategy to protect your new brand. This will include detailed steps about who can represent the company and speak about the issue, what message you need to convey and a protocol for keeping the right people in the know.
An experienced PR agency unlocks the doors you need to reach more people, improve your credibility, give you an edge over your competitors, and protect your company’s reputation during and after a rebranding effort.
So, if you’re thinking about rebranding, don’t forget to include the very experts who can help your rebranding stick the landing. PR helps you flesh out the values and legacy your organization needs to scale the growth a rebranding should provide.
Heather Ripley is founder and CEO of Ripley PR, an elite, global public relations agency specializing in the skilled trades, franchising and B2B tech industries. Ripley PR is recognized as the top PR agency for the home service industry, and it has also been listed by Entrepreneur Magazine as a Top Franchise PR Agency for six consecutive years. Heather Ripley is the author of “NEXT LEVEL NOW: PR Secrets to Drive Explosive Growth for your Home Service Business,” which is now available on all audiobook platforms. For additional information, visit www.ripleypr.com.
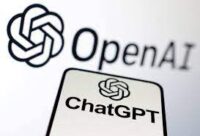
By Scott Bohannon Home service company owners will be some of the first small businesses to truly visualize the impact of Artificial Intelligence (AI) as its use becomes more widespread. But company owners should be wary not to expect a miracle and concentrate more on how AI, and applications like ChatGPT, can help reduce tasks Read more
By Scott Bohannon
Home service company owners will be some of the first small businesses to truly visualize the impact of Artificial Intelligence (AI) as its use becomes more widespread.
But company owners should be wary not to expect a miracle and concentrate more on how AI, and applications like ChatGPT, can help reduce tasks and enhance performance. Right now, you should be a fast follower rather than an early adopter.
While it’s true that ChatGPT can help our home service companies reduce the time it takes to perform some tasks like scheduling, composing documents and performing simple tasks, it’s a technology that will still require training to become the powerful tool it is destined to become.
At CEO Warrior, for example, we’ve identified several unique ways that ChatGPT can help reduce the time it takes to perform tasks and other ways that it can enhance your work. It can be used to help your team improve customer correspondence, interact with vendors and even provide insights on predictive maintenance.
The key is to understand that the capabilities of AI will vary depending on your individual business and that there is no one-size-fits-all solution.
The Heavy Lifting
The most effective way to view AI is to consider its capabilities as a task-specific tool. Larger businesses perform more tasks, so their early adoption allows them to reduce the time their people spend on tasks or enhances the quality of the tasks they perform.
But smaller companies may need to begin their experimentation by using AI to help them develop the very processes they may want help with in the future. It’s these processes that you will eventually use to grow and scale your organization.
Let the larger companies and the technology providers continue to do the heavy lifting for now. The technology has to be better trained, and, unless you want to spend precious time away from your customers and your business, don’t be afraid to wait.
That’s not to say that you shouldn’t experiment with AI. Home service companies are poised to benefit tremendously from this technology if they use it correctly.
Customer Service
By now, we have probably all experienced using a chatbot. But, if you’re like most users, you spend most of your time interacting with a chatbot in an attempt to have it get you to a live person.
It may be tempting to think that AI can solve your customer service issues, but even larger companies have discovered that AI’s customer-facing tech isn’t all that great for their customers. It cannot be used to replace a professional customer service team and is best used to enhance their role by providing them with answers to specific questions. It can also generate and deliver customer data that your team can use to improve a customer’s experience.
Applications like ChatGPT have to be trained. If your goal is to use it live to replace your customer service team, you need to know that it will only learn by experimenting with customer trends. That’s not an ideal use for this powerful tool.
Customer service representatives are there to ensure your clients have a positive customer service experience. So, for now, we need to keep our people talking to our customers and focus AI on other areas within our businesses where it can do its best work.
Business Processes
While AI and ChatGPT may have more learning to do before they can seamlessly interact with clients, using their applications for backend work is already proving indispensable. There is almost no business process that can’t be improved by using these tools.
In fact, one of the earliest uses of this technology for smaller home service providers might be in process development.
Many smaller organizations don’t have the resources to hire high-powered consultants to help them develop these processes. But, with ChatGPT, they can simply tell the application the process they use, and it can help them to develop written policies that can be used companywide. Its comprehension of human language and capacity allows it to produce responses that are both coherent and appropriate for the occasion.
ChatGPT can help the home service business owner in other ways, such as with reporting and data analysis. It can then turn this reporting and analysis into visually stimulating graphs and charts and summary information about your datasets that you can use to scale your business.
Marketing Assistance
Harvard Business Review suggests that small businesses stand to gain the most from using AI in their marketing efforts.
Many small businesses can’t afford to hire an external marketing team, and they probably don’t have an expert on staff to help write ad copy or run market research. This is where a product like ChatGPT or CopyAI can be the most beneficial.
Home service companies thrive on personal relationships and quality service. AI can help these companies create more personalized marketing campaigns while collecting and analyzing the data a small business owner needs to make the most effective advertising decisions.
One of AI’s most beneficial features is its ability to help create content. Business owners can use it to generate several drafts of an ad campaign or copy for social media or email marketing. Its ability to provide you with new ideas or alternative content is already very well developed.
These tools are especially helpful in checking your work. If you write an email campaign, ask it for feedback. If you write ad copy, ask it to make the copy more dynamic. If you need data analysis to know the best places to invest your ad dollars, let AI help you develop this research.
What AI in marketing won’t do is make you a marketing whiz overnight. Remember to focus on what you do well and stick to it. AI can help you get better, but it won’t do everything a full-service marketing agency can do.
In the hands of someone with practical experience in marketing, it’s an advantage. But if you don’t have this knowledge, it can be overwhelming. With this in mind, don’t be afraid to ask your marketing company if they’re using AI. Get them to explain how they’re using it to better market your company and save you money.
The Smart Home
But where home service companies will probably see the biggest changes is in how they interact with a client’s home comfort systems.
AI won’t replace HVAC technicians, for example, but it will revolutionize how these technicians serve your customers while servicing the home.
The home of the future will have home comfort systems equipped with AI features that can communicate with the technician or allow the homeowner to envision how a new HVAC system can be more efficient.
From predictive maintenance to educating the homeowner, AI’s potential will help home service providers and technicians do a better job of improving the customer experience.
Be Practical
As AI is used more frequently in the home service industry, business owners should keep in mind that AI is a tool and not an employee. Many companies that have eliminated positions in the hopes that AI can perform their tasks haven’t always been satisfied with this decision.
AI will eliminate the need for people to do some tasks, reduce the time it takes to do tasks and enhance the efficiency of the tasks that need to be done, but it should not eliminate whole jobs. If you look into purchasing an AI application with the hopes of reducing your workforce in mind, right now, you’ll be disappointed.
AI will certainly change the way jobs look five years from now, and it’s a skill we’ll all need to become familiar with in the future. Like using the internet for work functions, AI will become a seamless part of our working experience. As more big tech companies begin to integrate AI into the platforms we already use – like Microsoft Word or Excel – we’ll need to develop the skills to be able to use it effectively.
So, go ahead and start using it, but let the tech companies continue to do the heavy lifting of developing and training it. Once it becomes as commonplace as the internet, you’ll be ready to use it effectively in your business.
Scott Bohannon is the CEO of CEO Warrior, where he supports entrepreneurs and their teams in the trades by helping them improve their business performance. Bohannon previously served as the president and CEO of the Center for Creative Leadership, CEO of AchieveForum, and CEO of Info-Tech Research Group and McLean & Co. Before entering into the corporate world, Bohannan practiced law in Washington DC, advising telecommunications and energy clients throughout the United States, Asia and Australia. He received his bachelor’s degree in public policy from Centre College in Danville, Kentucky. He later received a master’s degree and Ph.D. in economics, as well as a J.D., from the University of Virginia. For more information about Bohannon and CEO Warrior, please visit https://ceowarrior.com/.
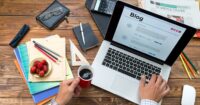
If you run a business, the chances are that you already know just how important an effective website can be. The business website is the modern-day equivalent of a storefront. It’s a point of contact and an opportunity to show off your work to potential customers. A bad business website, while potentially better than no Read more
If you run a business, the chances are that you already know just how important an effective website can be. The business website is the modern-day equivalent of a storefront. It’s a point of contact and an opportunity to show off your work to potential customers.
A bad business website, while potentially better than no website at all, is a problem. It can look unprofessional and put people off your company.
First things first, why have a blog at all?
There are a lot of reasons. Yes, it’s a lot of work, but a blog is an expected part of any business website.
Typically, the blog should include helpful and interesting posts that are related to your business in some way. For example, if you are a plumber, the blog could talk about common plumbing issues and what people can do about them.
This is kind of like a shopkeeper talking to customers. It adds a personal touch, but it also establishes you as an authority in the field.
It also gives you a much better opportunity to advertise your products and services in a less in-your-face way.
And, because it’s expected, not having a blog can make your business seem less professional. Blogs encourage customers to stick around, and the longer they spend on your website, the more likely they are to want to do business with you.
At least, they’re more likely to want to do business with you if you have a good blog.
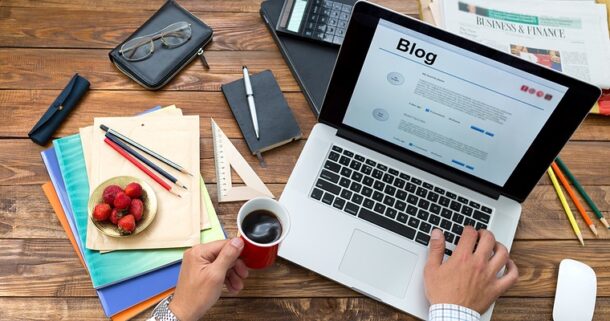
Regular Content
The first way to upgrade your blog is to pay attention to how often you update it. An abandoned blog is barely any better than a non-existent blog, as people will notice if new posts haven’t been added for months or even years.
You don’t need to post every day or even every week. The key to regular content is to post at set times. Weekly or every couple of weeks will do, as long as it’s regular.
This proves that you’re paying attention, while a neglected blog will look just that, neglected. Your blog reflects your company and your work.
Good Content
On the same note, a shoddy blog can have a similarly negative effect on how people perceive your business.
So, the content needs to be relevant, interesting, and competent. Your business blog is not the place to ramble on about your favorite fishing spots or what cars you love.
The spelling and grammar should be excellent. Yes, you aren’t an expert, but people do spot mistakes. Also, try to include images to break up the text and make the blog more visually engaging.
SEO Marketing
One great use for your blog is that it can market your business and draw people to your website. In order to get the most about this, use an SEO agency to level up your content marketing game using SEO strategies.
This way, your blog will work for you.
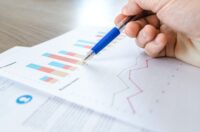
Michele Windsor, Vice President of Training and Implementation, Successware As 2023 draws to a close, many business owners are taking stock of their business from top to bottom, making plans for the coming year. There are multiple areas to consider, including personnel and equipment needs, budget forecasts, growth plans and more. One common theme that Read more
Michele Windsor, Vice President of Training and Implementation, Successware
As 2023 draws to a close, many business owners are taking stock of their business from top to bottom, making plans for the coming year. There are multiple areas to consider, including personnel and equipment needs, budget forecasts, growth plans and more.
One common theme that often surfaces during this time of reflection and planning ahead is how to best fix and streamline business processes. For home service contractors, it’s imperative to have a range of features and tools to manage your team in the field or in the home office, and it’s even better when it’s all combined in a comprehensive platform. When you have the right system working for you, it can significantly enhance your business’s efficiency, productivity and profitability.

A few software tools that will help your team’s daily functioning:
- Centralized Data Management – Technicians and employees across all departments need real-time access to the business data in order to make informed decisions and perform their tasks efficiently. Make it a priority to have a centralized hub for storing and managing all data. When everything is consolidated in one place, access to critical information is streamlined, reducing the risk of it being stolen.
- Workflow Automation – Automating routine and repetitive tasks will reduce human error and save valuable time. If you want to ensure that tasks are completed on time, invoices are sent out promptly and inventory is restocked when needed, look at setting up automated alerts, reminders and triggers.
- Customer Relationship Management (CRM) – Everyone wants to improve customer satisfaction and retention and also increase upselling opportunities. When a business is tracking customer data, communication history and preferences, those interactions can be personalized and more tailored services can be offered.
- Seamless Finances – Efficient invoicing, payment tracking and expense management are crucial for any business. A great tool for managing these financial processes will streamline every step, ensuring accurate and timely transactions. The right tool can also provide valuable insights through financial reporting and analytics, helping business owners make data-driven financial decisions.
A few important features to up your business operations game:
- Analytics and Reporting – More and more businesses are realizing the value of analytics and reporting tools that allow them to gather insights into their performance, identify areas for improvement and make strategic decisions based on data. This kind of data-driven decision-making is a core component of modern business success. Look for tools that give a clear overview of business operations by providing key performance indicators (KPIs), customizable reports and visual dashboards.
- Mobile Access – Remote access is crucial in today’s fast-paced business environment. Technicians are able to stay connected and productive even when they are on the road when they have mobile app and remote access capabilities. Because this feature enables real-time updates and communication, it is particularly valuable for businesses with field service teams.
- Scalability – As an organization expands, it’s important that the business management platform adapt and scale to accommodate additional users and increased workloads. This scalability ensures that a business can continue to benefit from the platform as it evolves.
As you seek to improve efficiency, reduce operational costs and drive overall success, it’s imperative to centralize data, automate workflows and integrate business functions. This year, resolve to fix and streamline your business processes by harnessing the power of these tools all in one comprehensive platform. Doing so will help your company stay competitive in today’s dynamic and demanding marketplace.
Michele Windsor is an experienced leader with over 23 years’ experience within the software vendor space. She has expertise in management and optimization and has conceptualized and executed enterprise solutions for high-profile corporations. Michele is focused on increasing business efficiencies, growing revenue and improving operational processes. As Vice President of Training and Implementation at Successware, she is committed to a seamless customer journey and creating customers for life by helping them understand how to use Successware products to increase their business productivity.
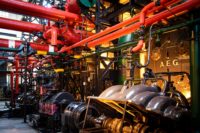
A staggering 85% of manufacturers believe that adopting industrial machinery is paramount to staying competitive. As the world swiftly moves towards the fourth industrial revolution, or Industry 4.0, the manufacturing sector finds itself amidst a transformative phase. The change isn’t just about replacing old machinery with newer models. It’s about a holistic integration of technology Read more
A staggering 85% of manufacturers believe that adopting industrial machinery is paramount to staying competitive. As the world swiftly moves towards the fourth industrial revolution, or Industry 4.0, the manufacturing sector finds itself amidst a transformative phase.
The change isn’t just about replacing old machinery with newer models. It’s about a holistic integration of technology, automation, and digital solutions into the heart of manufacturing. The role of advanced industrial equipment, from robotics to IoT, has proven to be a game-changer.
Especially for those in mechanical contracting, understanding this shift isn’t a choice anymore—it’s a necessity. Let’s dive deeper into how modern industrial machinery is revolutionizing how we think about manufacturing and contracting.
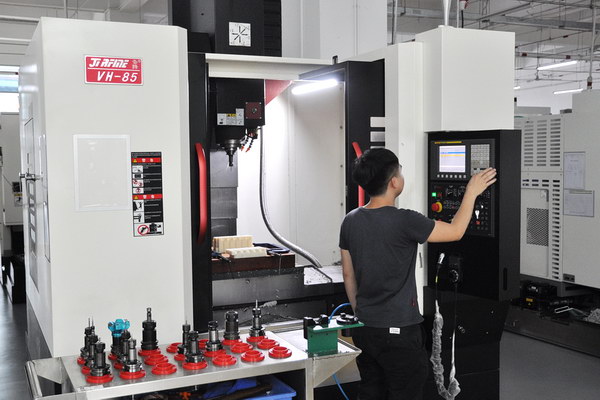
The Significance of Advanced Industrial Machinery
The adoption of advanced industrial machinery has indelibly transformed the landscape of the manufacturing industry. As the world gravitates towards the promises of Industry 4.0, manufacturers find themselves at the forefront of this change, ushering in new opportunities and addressing challenges head-on.
Advanced machinery, incorporating insights from AI and IoT, isn’t just a luxury; it’s the cornerstone of modern manufacturing.
Enhancing Efficiency in Modern Mechanical Contracting
Today’s mechanical contracting is no longer just about connecting pieces of equipment or overseeing manual labor. It’s about harnessing the power of modern industrial machinery to redefine what’s possible. At the heart of this transformation is efficiency. With every industry facing intense competition, streamlining operations and maximizing output have never been more crucial.
Enter advanced industrial equipment. These aren’t merely replacements for obsolete tools; they’re sophisticated solutions that help streamline workflows, ensuring tasks are completed efficiently and with unparalleled accuracy.
Consider the role of sensors in the machinery. They offer real-time monitoring, enabling predictive maintenance that dramatically minimizes unplanned downtime. Once a fanciful notion, robotics now plays a vital role in reducing operational costs, thereby increasing efficiency.
Moreover, as the supply chain faces disruptions from a pandemic or a shortage of raw materials, having advanced machinery equipped with real-time connectivity becomes pivotal. It allows manufacturers to adapt to changing scenarios swiftly, ensuring customer expectations are always met.
Advanced industrial machinery isn’t just a thread; it’s the fabric holding everything together, empowering contractors to offer more, faster, and with an efficiency previously thought unattainable.
Types of Advanced Industrial Machinery
As the manufacturing industry delves deeper into the digital age, an array of advanced industrial machinery is essential for improving efficiency and productivity. This modern equipment, integrated with technology and automation, promises a bright future for manufacturers.
Let’s delve into some of the prominent types that are revolutionizing the sector.
Hydraulic Systems
Hydraulic systems have long been a cornerstone in the industrial machinery manufacturing sector. Harnessing the power of fluid mechanics, they optimize operations by offering unparalleled accuracy and force. From cranes to loaders, these systems play a vital role in ensuring machinery operates smoothly, responding efficiently to the demands of heavy-duty tasks.
CNC Machines
Computer Numerical Control (CNC) machines are nothing short of a game-changer. These marvels, backed by digital solutions, have transformed the manufacturing process. By automating and streamlining manual labor, CNC machines offer unparalleled precision, allowing manufacturers to produce customized products with unparalleled accuracy.
Conveyor Systems
A well-organized supply chain is at the heart of every efficient manufacturing setup, and conveyor systems are pivotal in ensuring this. Beyond just moving raw materials, these systems are now equipped with sensors and IoT connectivity, ensuring real-time monitoring and thus minimizing disruptions in the workflow.
Industrial Robots
Robotics, once a vision of the distant future, are now a reality in every industry. Industrial robots, equipped with AI and machine learning capabilities, reduce labor costs and ensure tasks, from welding to assembly, are executed with improved productivity. Their adoption in the manufacturing industry signifies a transformative shift towards automation, ensuring operations are streamlined and output maximized.
Hydraulic systems, a foundational aspect of modern industrial machinery, have carved a niche in almost every sector, from energy production to manufacturing.
Overview
At its core, a hydraulic system harnesses the power of fluid dynamics to generate force or motion. Predominantly found in heavy machinery, these systems are essential in tractors, drills, mixers, and even some prototypes of 3D printers. Their adoption by industrial machinery manufacturers is testimony to their efficiency and reliability.
As we move towards greener solutions, research and development in this domain are geared towards integrating hydraulic systems with renewable energy sources, making them an enticing choice for new markets.
The rise of hydraulic systems can be attributed to the evolving needs of the middle class, whose demand for faster, more efficient, and affordable production processes is ever-growing. OEMs (Original Equipment Manufacturers) understand the significance of this, ensuring that modern industrial equipment, especially in the manufacturing realm, includes hydraulic components.
Maintenance Tips
Maintaining hydraulic systems is paramount for their profitability and longevity. The first steps include regular checks for leaks, ensuring fluid levels are optimal, and replacing worn-out parts. Contacting professionals for hydraulic repairs is wise for those unfamiliar with these systems.
Additionally, sharing data with manufacturers can help them enhance newer models, offering improved customization options. Always refer to the privacy policy before sharing sensitive data, and for hands-on experience, consider workshops that cater to the wholesale builder community, focusing on hands-on simulation exercises.
CNC Machines
In the panorama of advanced industrial machinery, CNC (Computer Numerical Control) machines stand out as a testament to how technology can redefine precision and efficiency in the manufacturing sector.
Overview
At their essence, CNC machines are industrial machines governed by computerized controls, leading to the automation of traditionally manual tasks. This adoption of industrial machinery, particularly CNCs, has revolutionized how manufacturers make intricate components. From automotive parts to intricate jewelry designs, CNCs offer unparalleled accuracy.
Their digital nature ensures that the same design can be replicated flawlessly, continuously enhancing productivity and customer satisfaction. Furthermore, their flexibility means they can be reprogrammed easily to cater to different tasks, making them an invaluable asset in diverse industries.
Maintenance Tips
While CNC machines offer exceptional precision and reliability, they require a dedicated maintenance routine to ensure longevity. Here are some general tips:
- Regularly clean the machine, ensuring no debris interferes with its operation.
- Lubricate moving parts as specified by the manufacturer to reduce wear and tear.
- Back up your CNC programs, ensuring you can quickly restore operations if there’s a system error.
- Frequently check for software updates. Manufacturers often release patches that enhance the machine’s performance or rectify known issues.
- Always have a line of communication open with your supplier. If you face any challenges, feel free to contact us for more information or the respective support channels to address your concerns promptly.
While CNC machines herald a new era of manufacturing prowess, their efficiency remains intertwined with diligent maintenance and care.
Conveyor Systems
At the heart of many industrial operations, conveyor systems play a pivotal role, streamlining the movement of materials and ensuring seamless production flows.
Overview
As the name suggests, Conveyor systems are designed to convey materials from one point to another within a facility. Whether in a sprawling manufacturing plant, a distribution center, or a packaging facility, these systems ensure timely and efficient material handling. They come in various forms, such as belt, roller, and chain conveyors, each tailored for specific operational needs.
Beyond just transportation, modern conveyor systems often integrate sensors and advanced technologies, offering real-time monitoring and even sorting capabilities. Their ubiquity in industries underscores their importance in achieving optimal workflow and production targets.
Maintenance Tips
A consistent maintenance routine is crucial to maintain the efficiency and longevity of conveyor systems. Here are some general maintenance tips:
- Regular Inspections: Inspect belts or chains for signs of wear, tear, or misalignment. This proactive approach can prevent potential breakdowns.
- Cleanliness: Ensure the conveyor’s surface and surroundings are free from debris or materials that might hinder its operation.
- Lubrication: Parts like bearings, chains, and other moving components need regular lubrication to function smoothly and prevent premature wear.
- Update Software: If your conveyor system has integrated technology, constantly update its software for optimal performance.
- Safety First: Always prioritize safety. Ensure all safety guards are in place and the system’s emergency stop functions are working correctly.
While conveyor systems offer tremendous operational advantages, their peak performance is tied to regular and diligent maintenance efforts.
Industrial Robots
Industrial robots represent the pinnacle of digital transformation in manufacturing and production, epitomizing the blend of technology and mechanical prowess.
Overview
Industrial robots are automated, programmable machines capable of carrying out complex tasks with high precision and speed. These robots have been a transformative force born out of the need to enhance efficiency and reduce supply chain disruptions. Their integration into the manufacturing scene signifies an upgrade in machinery and a paradigm shift towards embracing a sustainable and technologically advanced future.
With the incorporation of IIoT (Industrial Internet of Things), these robots offer an operator enhanced visibility throughout the production process, ensuring discrepancies are addressed promptly. Moreover, as the workforce adapts to this digital transformation, robots and systems like ERP (Enterprise Resource Planning) promise streamlined operations, reducing errors and wastage.
Maintenance Tips
To ensure the extended lifespan and optimal functioning of industrial robots.
- Routine Inspections: Have an operator regularly check for signs of wear or mechanical stress. Addressing issues early can prevent more significant malfunctions later.
- Software Updates: Robots benefit from periodic software updates like any tech-driven machinery. These not only fix bugs but can enhance performance.
- Lubrication and Cleaning: Ensuring moving parts are well-lubricated and debris-free can prolong their lifespan.
- Training the Workforce: Continuously train the workforce to understand the nuances of the robot’s operations, ensuring smooth collaboration.
- Safety Protocols: Always prioritize safety. Enhance visibility around the robot’s operational area and ensure safety mechanisms are active to prevent mishaps.
- Plan for Upgrades: With technology evolving rapidly, be ready to upgrade components to ensure sustainability and prevent obsolescence.
While industrial robots are a marvel of modern engineering and technology, their optimal performance relies on regular maintenance and a well-trained operator, ensuring they remain valuable in the production chain.
Proactive Maintenance Strategies
In the vast world of industrial operations, downtime is a costly enemy. Every minute a machine stands idle, expenses accrue, production targets falter, and the bottom line suffers. As the adage goes, prevention is better than cure, and nowhere is this more evident than equipment maintenance.
Preventing Costly Downtime
Understanding the importance of proactive maintenance isn’t just about recognizing the costs associated with breakdowns; it’s about appreciating the broader implications for the entire operation. Unscheduled halts can disrupt supply chains, tarnish a company’s reputation, and compromise safety standards. Therefore, being proactive rather than reactive is crucial.
By adopting a preventive approach, operators can anticipate potential issues before they escalate into significant problems. Regular inspections, timely upgrades, and a keen understanding of equipment life cycles are all essential aspects of this strategy.
Furthermore, technology integration has cast light on the importance of proactive maintenance, with tools offering insights that were once impossible to glean.
The Role of IoT and Predictive Maintenance
The Internet of Things (IoT) has been a maintenance game-changer. With sensors and devices connected in real-time, the data generated provides a granular view of machinery health. This technological adoption has paved the way for predictive maintenance.
Predictive maintenance, as the name suggests, allows companies to predict when a piece of equipment is likely to fail or requires servicing. Instead of relying on generic schedules or waiting for a machine to show obvious signs of wear, data analytics can now foretell potential issues. This minimizes downtime and optimizes machinery’s lifespan, ensuring operations remain smooth and efficient.
Conclusion
In today’s rapidly evolving industrial landscape, integrating advanced machinery, from CNC machines to hydraulic systems, underscores a paradigm shift towards efficiency and precision. While these innovations offer unparalleled advantages, their optimal performance is intrinsically tied to regular maintenance and proactive strategies. Embracing the power of IoT and predictive maintenance, industries can preemptively address potential issues, minimizing costly downtimes and maximizing machinery lifespan.
Furthermore, continuous training and collaboration between man and machine will become paramount as the workforce adapts to this digital transformation.
The future of industrial operations isn’t just about adopting advanced machinery but nurturing them through informed maintenance strategies, ensuring sustained productivity and growth.