A staggering 85% of manufacturers believe that adopting industrial machinery is paramount to staying competitive. As the world swiftly moves towards the fourth industrial revolution, or Industry 4.0, the manufacturing sector finds itself amidst a transformative phase.
The change isn’t just about replacing old machinery with newer models. It’s about a holistic integration of technology, automation, and digital solutions into the heart of manufacturing. The role of advanced industrial equipment, from robotics to IoT, has proven to be a game-changer.
Especially for those in mechanical contracting, understanding this shift isn’t a choice anymore—it’s a necessity. Let’s dive deeper into how modern industrial machinery is revolutionizing how we think about manufacturing and contracting.
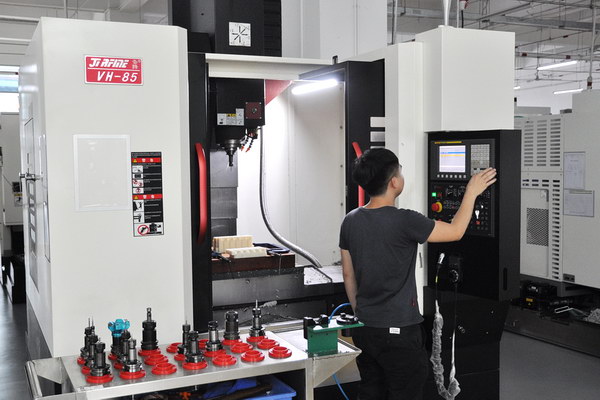
The Significance of Advanced Industrial Machinery
The adoption of advanced industrial machinery has indelibly transformed the landscape of the manufacturing industry. As the world gravitates towards the promises of Industry 4.0, manufacturers find themselves at the forefront of this change, ushering in new opportunities and addressing challenges head-on.
Advanced machinery, incorporating insights from AI and IoT, isn’t just a luxury; it’s the cornerstone of modern manufacturing.
Enhancing Efficiency in Modern Mechanical Contracting
Today’s mechanical contracting is no longer just about connecting pieces of equipment or overseeing manual labor. It’s about harnessing the power of modern industrial machinery to redefine what’s possible. At the heart of this transformation is efficiency. With every industry facing intense competition, streamlining operations and maximizing output have never been more crucial.
Enter advanced industrial equipment. These aren’t merely replacements for obsolete tools; they’re sophisticated solutions that help streamline workflows, ensuring tasks are completed efficiently and with unparalleled accuracy.
Consider the role of sensors in the machinery. They offer real-time monitoring, enabling predictive maintenance that dramatically minimizes unplanned downtime. Once a fanciful notion, robotics now plays a vital role in reducing operational costs, thereby increasing efficiency.
Moreover, as the supply chain faces disruptions from a pandemic or a shortage of raw materials, having advanced machinery equipped with real-time connectivity becomes pivotal. It allows manufacturers to adapt to changing scenarios swiftly, ensuring customer expectations are always met.
Advanced industrial machinery isn’t just a thread; it’s the fabric holding everything together, empowering contractors to offer more, faster, and with an efficiency previously thought unattainable.
Types of Advanced Industrial Machinery
As the manufacturing industry delves deeper into the digital age, an array of advanced industrial machinery is essential for improving efficiency and productivity. This modern equipment, integrated with technology and automation, promises a bright future for manufacturers.
Let’s delve into some of the prominent types that are revolutionizing the sector.
Hydraulic Systems
Hydraulic systems have long been a cornerstone in the industrial machinery manufacturing sector. Harnessing the power of fluid mechanics, they optimize operations by offering unparalleled accuracy and force. From cranes to loaders, these systems play a vital role in ensuring machinery operates smoothly, responding efficiently to the demands of heavy-duty tasks.
CNC Machines
Computer Numerical Control (CNC) machines are nothing short of a game-changer. These marvels, backed by digital solutions, have transformed the manufacturing process. By automating and streamlining manual labor, CNC machines offer unparalleled precision, allowing manufacturers to produce customized products with unparalleled accuracy.
Conveyor Systems
A well-organized supply chain is at the heart of every efficient manufacturing setup, and conveyor systems are pivotal in ensuring this. Beyond just moving raw materials, these systems are now equipped with sensors and IoT connectivity, ensuring real-time monitoring and thus minimizing disruptions in the workflow.
Industrial Robots
Robotics, once a vision of the distant future, are now a reality in every industry. Industrial robots, equipped with AI and machine learning capabilities, reduce labor costs and ensure tasks, from welding to assembly, are executed with improved productivity. Their adoption in the manufacturing industry signifies a transformative shift towards automation, ensuring operations are streamlined and output maximized.
Hydraulic systems, a foundational aspect of modern industrial machinery, have carved a niche in almost every sector, from energy production to manufacturing.
Overview
At its core, a hydraulic system harnesses the power of fluid dynamics to generate force or motion. Predominantly found in heavy machinery, these systems are essential in tractors, drills, mixers, and even some prototypes of 3D printers. Their adoption by industrial machinery manufacturers is testimony to their efficiency and reliability.
As we move towards greener solutions, research and development in this domain are geared towards integrating hydraulic systems with renewable energy sources, making them an enticing choice for new markets.
The rise of hydraulic systems can be attributed to the evolving needs of the middle class, whose demand for faster, more efficient, and affordable production processes is ever-growing. OEMs (Original Equipment Manufacturers) understand the significance of this, ensuring that modern industrial equipment, especially in the manufacturing realm, includes hydraulic components.
Maintenance Tips
Maintaining hydraulic systems is paramount for their profitability and longevity. The first steps include regular checks for leaks, ensuring fluid levels are optimal, and replacing worn-out parts. Contacting professionals for hydraulic repairs is wise for those unfamiliar with these systems.
Additionally, sharing data with manufacturers can help them enhance newer models, offering improved customization options. Always refer to the privacy policy before sharing sensitive data, and for hands-on experience, consider workshops that cater to the wholesale builder community, focusing on hands-on simulation exercises.
CNC Machines
In the panorama of advanced industrial machinery, CNC (Computer Numerical Control) machines stand out as a testament to how technology can redefine precision and efficiency in the manufacturing sector.
Overview
At their essence, CNC machines are industrial machines governed by computerized controls, leading to the automation of traditionally manual tasks. This adoption of industrial machinery, particularly CNCs, has revolutionized how manufacturers make intricate components. From automotive parts to intricate jewelry designs, CNCs offer unparalleled accuracy.
Their digital nature ensures that the same design can be replicated flawlessly, continuously enhancing productivity and customer satisfaction. Furthermore, their flexibility means they can be reprogrammed easily to cater to different tasks, making them an invaluable asset in diverse industries.
Maintenance Tips
While CNC machines offer exceptional precision and reliability, they require a dedicated maintenance routine to ensure longevity. Here are some general tips:
- Regularly clean the machine, ensuring no debris interferes with its operation.
- Lubricate moving parts as specified by the manufacturer to reduce wear and tear.
- Back up your CNC programs, ensuring you can quickly restore operations if there’s a system error.
- Frequently check for software updates. Manufacturers often release patches that enhance the machine’s performance or rectify known issues.
- Always have a line of communication open with your supplier. If you face any challenges, feel free to contact us for more information or the respective support channels to address your concerns promptly.
While CNC machines herald a new era of manufacturing prowess, their efficiency remains intertwined with diligent maintenance and care.
Conveyor Systems
At the heart of many industrial operations, conveyor systems play a pivotal role, streamlining the movement of materials and ensuring seamless production flows.
Overview
As the name suggests, Conveyor systems are designed to convey materials from one point to another within a facility. Whether in a sprawling manufacturing plant, a distribution center, or a packaging facility, these systems ensure timely and efficient material handling. They come in various forms, such as belt, roller, and chain conveyors, each tailored for specific operational needs.
Beyond just transportation, modern conveyor systems often integrate sensors and advanced technologies, offering real-time monitoring and even sorting capabilities. Their ubiquity in industries underscores their importance in achieving optimal workflow and production targets.
Maintenance Tips
A consistent maintenance routine is crucial to maintain the efficiency and longevity of conveyor systems. Here are some general maintenance tips:
- Regular Inspections: Inspect belts or chains for signs of wear, tear, or misalignment. This proactive approach can prevent potential breakdowns.
- Cleanliness: Ensure the conveyor’s surface and surroundings are free from debris or materials that might hinder its operation.
- Lubrication: Parts like bearings, chains, and other moving components need regular lubrication to function smoothly and prevent premature wear.
- Update Software: If your conveyor system has integrated technology, constantly update its software for optimal performance.
- Safety First: Always prioritize safety. Ensure all safety guards are in place and the system’s emergency stop functions are working correctly.
While conveyor systems offer tremendous operational advantages, their peak performance is tied to regular and diligent maintenance efforts.
Industrial Robots
Industrial robots represent the pinnacle of digital transformation in manufacturing and production, epitomizing the blend of technology and mechanical prowess.
Overview
Industrial robots are automated, programmable machines capable of carrying out complex tasks with high precision and speed. These robots have been a transformative force born out of the need to enhance efficiency and reduce supply chain disruptions. Their integration into the manufacturing scene signifies an upgrade in machinery and a paradigm shift towards embracing a sustainable and technologically advanced future.
With the incorporation of IIoT (Industrial Internet of Things), these robots offer an operator enhanced visibility throughout the production process, ensuring discrepancies are addressed promptly. Moreover, as the workforce adapts to this digital transformation, robots and systems like ERP (Enterprise Resource Planning) promise streamlined operations, reducing errors and wastage.
Maintenance Tips
To ensure the extended lifespan and optimal functioning of industrial robots.
- Routine Inspections: Have an operator regularly check for signs of wear or mechanical stress. Addressing issues early can prevent more significant malfunctions later.
- Software Updates: Robots benefit from periodic software updates like any tech-driven machinery. These not only fix bugs but can enhance performance.
- Lubrication and Cleaning: Ensuring moving parts are well-lubricated and debris-free can prolong their lifespan.
- Training the Workforce: Continuously train the workforce to understand the nuances of the robot’s operations, ensuring smooth collaboration.
- Safety Protocols: Always prioritize safety. Enhance visibility around the robot’s operational area and ensure safety mechanisms are active to prevent mishaps.
- Plan for Upgrades: With technology evolving rapidly, be ready to upgrade components to ensure sustainability and prevent obsolescence.
While industrial robots are a marvel of modern engineering and technology, their optimal performance relies on regular maintenance and a well-trained operator, ensuring they remain valuable in the production chain.
Proactive Maintenance Strategies
In the vast world of industrial operations, downtime is a costly enemy. Every minute a machine stands idle, expenses accrue, production targets falter, and the bottom line suffers. As the adage goes, prevention is better than cure, and nowhere is this more evident than equipment maintenance.
Preventing Costly Downtime
Understanding the importance of proactive maintenance isn’t just about recognizing the costs associated with breakdowns; it’s about appreciating the broader implications for the entire operation. Unscheduled halts can disrupt supply chains, tarnish a company’s reputation, and compromise safety standards. Therefore, being proactive rather than reactive is crucial.
By adopting a preventive approach, operators can anticipate potential issues before they escalate into significant problems. Regular inspections, timely upgrades, and a keen understanding of equipment life cycles are all essential aspects of this strategy.
Furthermore, technology integration has cast light on the importance of proactive maintenance, with tools offering insights that were once impossible to glean.
The Role of IoT and Predictive Maintenance
The Internet of Things (IoT) has been a maintenance game-changer. With sensors and devices connected in real-time, the data generated provides a granular view of machinery health. This technological adoption has paved the way for predictive maintenance.
Predictive maintenance, as the name suggests, allows companies to predict when a piece of equipment is likely to fail or requires servicing. Instead of relying on generic schedules or waiting for a machine to show obvious signs of wear, data analytics can now foretell potential issues. This minimizes downtime and optimizes machinery’s lifespan, ensuring operations remain smooth and efficient.
Conclusion
In today’s rapidly evolving industrial landscape, integrating advanced machinery, from CNC machines to hydraulic systems, underscores a paradigm shift towards efficiency and precision. While these innovations offer unparalleled advantages, their optimal performance is intrinsically tied to regular maintenance and proactive strategies. Embracing the power of IoT and predictive maintenance, industries can preemptively address potential issues, minimizing costly downtimes and maximizing machinery lifespan.
Furthermore, continuous training and collaboration between man and machine will become paramount as the workforce adapts to this digital transformation.
The future of industrial operations isn’t just about adopting advanced machinery but nurturing them through informed maintenance strategies, ensuring sustained productivity and growth.
Join the conversation: