It’s tempting to assume that all you really need to succeed in business is a good concept and a strong desire to succeed, but the fact is that there is a lot more to it, especially if you’re hoping to build something lasting rather than simply a one-time thing. After all, the point of having Read more
Whats New
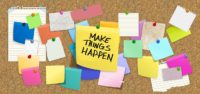
It’s tempting to assume that all you really need to succeed in business is a good concept and a strong desire to succeed, but the fact is that there is a lot more to it, especially if you’re hoping to build something lasting rather than simply a one-time thing. After all, the point of having a business is to make it work over the long-term, building up bit by bit into something to be proud of.
In order to be successful as a company owner, you must meet a wide range of criteria. You don’t have to do everything yourself, but if you want to have a chance of generating money and succeeding, you must be knowledgeable about all aspects of the business. In light of this, continue reading to learn what makes a business work.
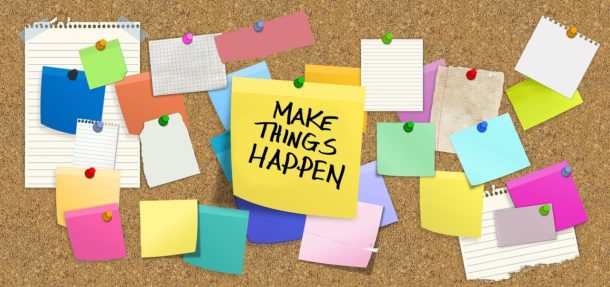
Strong Leadership
Strong leadership is one of the most important parts of making a business work. When a smart, knowledgeable, and determined leader is in charge, the business is much more likely to be successful and last for a long time.
There are many ways to be a strong leader in business. Some of these skills you will already have, some you can learn over time working within the business, and others you can learn through courses and even degrees. Examples of strong leadership include:
- Working with the team rather than just giving orders
- Understanding perfection doesn’t exist
- Continuing to learn as much as possible about your industry and business in general
- Be inspiring
- Have goals that you work towards
A USP
USP stands for “unique selling point,” and your business will need one if you want it to be successful now and in the long run. This USP is the one thing (or usually at least one thing) that your business does that no one else does. When you start your business, it will be easier to find your USP if you can find a gap in the market. This is because your USP will already be there for you. But if you are starting a business in an area where there is already competition, it may be harder to find the USP, but you must find it.
The USP could be related to anything, from how you treat customers to how you ship your goods. It doesn’t have to be completely new, but it does need to be good and make customers happy. Once you’ve found your USP, it’s important to use it in all of your advertising to remind people what makes you the best choice.
A Strategy
Having a good idea (or any idea at all) is a good start, but if you don’t know what to do with it, it won’t get you very far. This is why it’s important to do research and understand business in general.
But if you really want your business to be successful, you’ll also need a good plan or strategy. When you have a strategy for success, your idea becomes much more concrete, and it will be much easier for you to make decisions for your business because you’ll know which way to go.
The last thing you want is to start your business and then not know what to do next, causing it to fail. Before you launch, it’s best to have a plan and stick to it unless you find that the plan isn’t working, in which case you need to make a new one. Your plan needs to cover everything, including all the ideas you have for the future. It should set out exactly how much you’ll need to invest in fleet leasing, for example, and when you envision that needing to take place, as well as when you intend to hire staff and how your marketing is going to attract customers.
Try to write a plan that covers at least the next five years or, better yet, the next seven or even ten years. Make sure it has all your financial data so that if you need to borrow money for your business, you have everything you need.
Competitor Analysis
You have a great idea for a business and want to do something with it. You put a lot of time and effort into making your business work and getting it off the ground. Then you find out that another business, or maybe more than one, is already doing what you’re doing, and it’s popular and well-known. You might be able to beat the competition if you use your leadership skills, your USP, and other ideas. But it will be hard. This is why the best thing you can do right away is to check out your competitors. First of all, this will let you know if your business idea is good or not. You can also figure out how much of a threat the competition is.
If you do want to keep going with your business, you need to know more about your competitors if you want that business to work. It will give you ideas to build on, show you what works and what doesn’t, and help you find the perfect USP that makes you stand out from the competition.
In reality, if you want your business to work and be successful, you need to know as much about your competitors’ businesses as you do about your own. You need to know what they are doing so that you can offer something better to your customers.
Marketing
What good is a good business if it doesn’t have good marketing? The answer is that it’s not a business at all; it’s just someone hoping that something will take place and people will start wanting to buy. There is a lot of competition out there, some of which is directly related to your business and some of which is similar enough to make potential customers think twice. Also, a huge number of small businesses start up every day, and most of them are moving online. This makes it harder and harder for your business to be seen at all. This is why marketing is so important if you want to be successful and for your business to work.
When it comes to marketing, there are many different ways to do things. You could write a newsletter or send out emails. You might do better with social media. You might want to start a blog or make videos. Another choice is content marketing. You could do any or all of these things, as long as they help you get the most out of your important marketing budget.
When it comes to marketing, it’s usually best to use at least some of that budget to hire experts. A business owner doesn’t always know what to do, which can lead to mistakes or to not doing anything at all. If this happens, your business might go under, and it will be hard to get it back up.
Customer Service
If you want your business to be successful, you need the public to be on your side. If you don’t have a lot of loyal customers who keep coming back and telling others how happy they are to have found your business, it will be hard to move forward. Considering all of this, it’s clear that customer service is an important part of any business.
Most businesses should make it a priority to treat customers well because word of mouth is a cheap and easy way to get new customers and referrals, even if they also use other marketing methods. All you have to do is provide good customer service, and your customers will do the rest. When we say “good customer service,” we mean things like going above and beyond, being polite and friendly all the time, making sure the customer is always happy, and so on. It doesn’t matter how big or small the thing is, as long as it makes the customer happy and makes them feel appreciated, it’s worth doing and could help your business succeed.
A Great Team
When you start your business, you may be the only one there. Even though this isn’t always the case, and you could start it with a whole team, most people do it on their own or with maybe just one other person. At some point, you’ll have to decide whether to stay a sole trader and keep your business small but all yours or to start growing and hiring employees or subcontractors to help you get the work done.
Some people find it hard to decide, so you should do as much research as you can and, of course, do the math to help you figure out what to do. If you do decide to hire a team, that team needs to be as good as it can be if you want your business to work. Every member has to be loyal, skilled, and knowledgeable, and they all have to contribute to the culture of the company. Even if their job requires them to work alone, they still need to get along with others and care about the company’s goals and ideals.
Spend some time making job ads and talking to people to find the ones that will work best for you. Don’t rush. If you can put together a good team, you can run a good business that works.
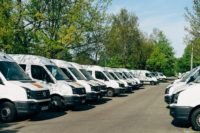
If your business operates a fleet of vehicles, you’ll probably know how costly the task can be. It’s not cheap and there’s lots of money that has to be spent just to keep them operating and functional. That’s precisely why it’s so important to look for ways to save money on your fleet of vehicles Read more
If your business operates a fleet of vehicles, you’ll probably know how costly the task can be. It’s not cheap and there’s lots of money that has to be spent just to keep them operating and functional. That’s precisely why it’s so important to look for ways to save money on your fleet of vehicles. We’re going to talk today about some of the tips and ideas that should make that a little easier to achieve.
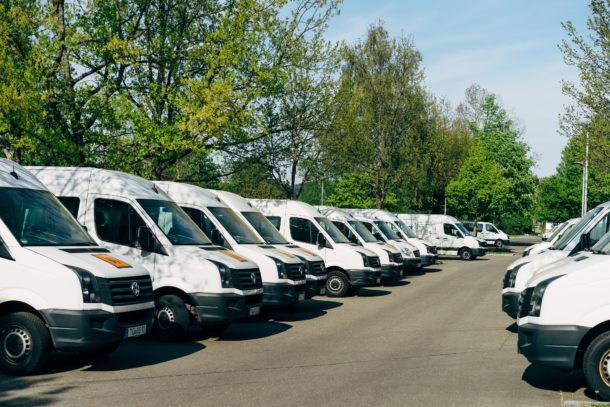
Travel Less
One of the easiest ways to save money on operating a fleet of vehicles is to use them less, even if this isn’t a realistic option for most business owners. If you can find ways to have fewer meetings or to consolidate your vehicles, you might be able to save some money that way. If it’s a realistic possibility for you, you should at least explore it.
Ensure Drivers Drive Efficiently
It’s important to ensure that the drivers that work for your business are able to drive in a way that’s efficient and careful. You don’t want to be in a position where your drivers are driving erratically or too fast or too slow. All of those things can be not only dangerous but also costly from a fuel efficiency point of view. You could provide them with training along those lines.
Take Out Fleet Insurance
If you don’t have fleet insurance already, that’s something that has to change. There are all kinds of things that can go wrong when operating a whole fleet of vehicles. Unfortunately, things go wrong and mistakes can be made. When that happens, it’s important to be able to fall back on the insurance policy that you had in place. If that doesn’t happen, you’ll be faced with paying the costs yourself.
Use GPS and Plot the Shortest Routes
Having some sort of GPS system in place is a good idea. That way, you can see where your vehicles are going and which routes they’re taking in order to reach their destinations. With the use of commercial GPS, you can make sure that your drivers are only taking the shortest and most efficient routes unless there’s a particular reason why they shouldn’t.
Be Careful About Where You Park
Finally, you should think about security and the potential for break-ins and burglaries. You should try to make sure that your vehicles are always stored in secure locations where there’s no opportunity for anyone to steal or even break into your vehicles. When that happens, it leads to potentially quite heavy losses for the business and that’s not what you want to happen.
Rent vehicles
When you run a business that requires a range of vehicles, it might not be the most cost-effective solution to always be purchasing new vehicles. If you decide you need additional fleet vehicles, something bigger, or something different, you may decide that a work truck rental is the best way to go. This will give you access to different vehicles, as and when you need them, without spending a fortune on keeping them running and maintenance all year round. If you can find a reputable company to work with, you may be able to pay as you go and save your business a lot of money. This will help you manage your fleet, as you have your main vehicles that are always in action, and then access to the additional vehicles, or bigger vehicles when you need them. For example, if you only get one bigger job per year, it would be more cost-efficient to hire the additional vehicles you need to complete that project, rather than them sitting there doing nothing for the rest of the year burning away your money. Many businesses are choosing the option to rent, just because of the difference it can make on their yearly profits, as well as the sheer convenience of them.
As you can see, there are plenty of different things you can do if you want to save money on your fleet of vehicles. It’s important not to let those costs spiral out of your control because that can eventually take a pretty big toll on your business and that’s obviously not something you want to be dealing with.
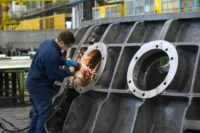
When it comes to running a manufacturing business, you have to think about more than just the products you’re making. You also need to find quality suppliers who can provide the materials and components you need to keep your production line running. Here are five suppliers worth considering when starting or expanding your manufacturing business Read more
When it comes to running a manufacturing business, you have to think about more than just the products you’re making. You also need to find quality suppliers who can provide the materials and components you need to keep your production line running. Here are five suppliers worth considering when starting or expanding your manufacturing business.
1) Raw materials supplier
This is the most important type of supplier for any manufacturing business. You need to find a supplier who can provide high-quality raw materials at a competitive price. This could include things like lathes, mills, presses, glue machinery, etc. If you’re not sure where to start, try reaching out to local businesses or searching online for suppliers in your area.
Once you’ve found a few potential suppliers, be sure to ask for quotes and compare prices before making your final decision.
You should also consider the quality of the raw materials when choosing a supplier. Make sure to read reviews and do your research to ensure you’re getting the best possible product for your needs.
2) Component supplier
In addition to raw materials, you’ll also need to find a supplier for any components or parts that are required for your manufacturing process. This could include things like screws, bolts, washers, etc.
Again, comparing prices and quality is essential when choosing a component supplier. You don’t want to cut corners on quality just to save a few bucks. It’s also worth considering whether you want to buy components in bulk or order them as needed.
Ultrasonic Components are just one example of a reputable component supplier. There are many others out there, so be sure to do your research before making a final decision.
3) Machinery supplier
If you’re starting a manufacturing business from scratch, you’ll need to find a supplier for all of the necessary machinery. This could include things like lathes, mills, presses, etc.
As with any other type of supplier, it’s important to compare prices and quality when choosing a machinery supplier. You don’t want to end up with inferior equipment that will break down often and be expensive to repair.
Research and ask for other manufacturers’ recommendations before making your final decision.
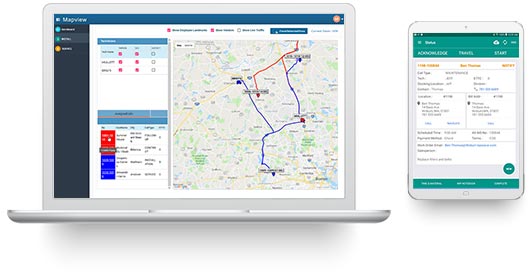
4) Software supplier
In today’s high-tech world, most manufacturing businesses rely on software to help run their operations. Therefore, you’ll need to find a software supplier that can provide the right tools for your specific needs.
ERP systems are a common type of software used in manufacturing. They can help with things like inventory management, production planning, and quality control.
5) Transportation supplier
You’ll need to find a reliable transportation supplier if you’re shipping products to customers. This could be a local trucking company or an international shipping carrier. FedEx is one example of a well-known transportation company that offers shipping services for businesses.
These are just a few of the different types of suppliers you need to consider when starting or expanding your manufacturing business. Take the time to do your research and choose the best possible option for each category. Your business will run more smoothly and efficiently if you have quality suppliers you can rely on.
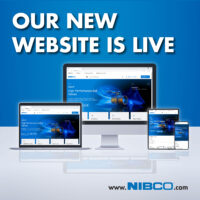
Whether you have a website already or you need to improve an existing one to make it more effective, you’ve come to the right place. The advice and resources in the article below will help to keep your website development on the right track, with help from professional services. DO keep the interface consistent Websites Read more
Whether you have a website already or you need to improve an existing one to make it more effective, you’ve come to the right place. The advice and resources in the article below will help to keep your website development on the right track, with help from professional services.
DO keep the interface consistent
Websites that have multiple colors, designs, and fonts on different pages aren’t as effective as ones that are consistent throughout. When a website is not consistent, it creates disharmony in the minds of the user and affects interactions and conversion rates. A better approach is to create a consistent look and feel for your website on every page, making it more predictable.
DO create excellent navigation
On average, a website visitor will spend less than 15 seconds on a webpage before moving on, and you want them to move on to another part of your website. Unless you have excellent navigation, chances are your potential customers will move on, so make sure that your links lead to the places and your categories are set up to support the right content.
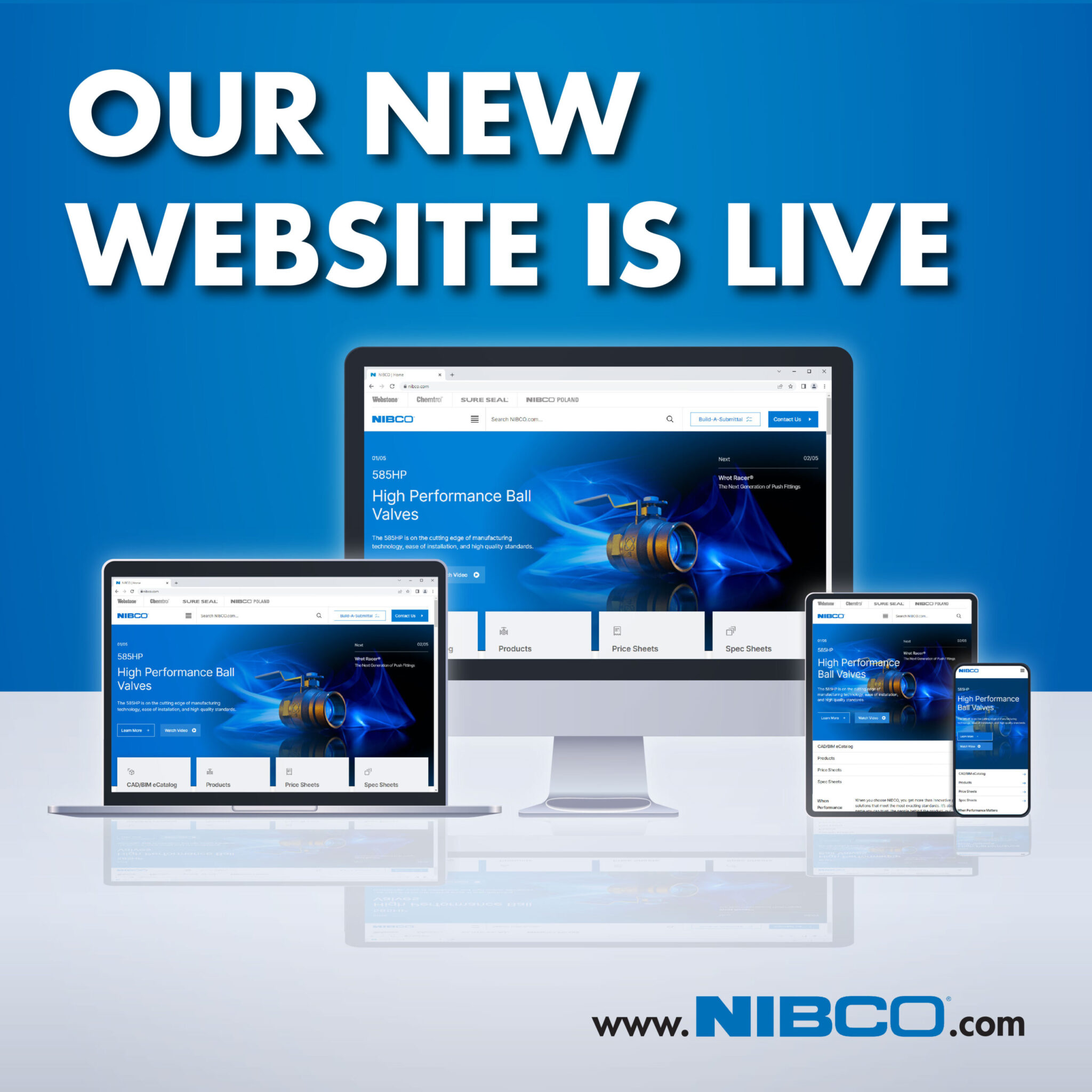
DO take your content seriously
When it comes to designing your website, there are two primary factors to consider one of them is website design, and the other is content. 95% of the content on your website is written language; it needs to engage visitors and rank well on search engines. It also needs to be well designed and optimized. Contact Red Spot Design for a professional website building service.
DON’T open links externally
Avoid opening internal links in a new window that takes your visitor away from your website. Website users have a short attention span, and navigation is paramount to maintaining their interest; once they leave your website, there’s a chance they won’t return. Internal links work better. If you must have an external link, make sure to warn users before they navigate away.
DON’T overuse colors or features
Some amateur website designs use a variety of colors, fonts, and page layouts for different pages of their website, but this leads to distraction and makes it difficult for your website visitors to interact with your business. Keep your colors, and design features minimal and on-brand; this creates consistency and a stronger brand identity. Use a professional website design company.
DON’T overpromote on the website
If you have a professional website with high-quality content, you can run online ads and create a new revenue stream. It can be tempting to run multiple ads on your website and boost your earning potential, but this can also be detrimental to your business. Too many ads on a webpage compete for your visitor’s attention and distract them from the content they need.
Final Thoughts
Nowadays, a website is an indispensable marketing tool. Not only is it your digital storefront, but it plays an important role in finding new customers and promoting your business. However, there are many ways the website can fail, so use the tips to build a more professional website.
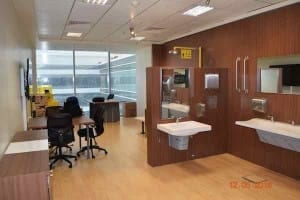
Building the perfect business office from the ground up might sound like a lot of work…and you would be right. It is a lot of work, and it’s going to take time to get it how you want it. However, this doesn’t mean that it isn’t worth doing. In this article, we are going to Read more
Building the perfect business office from the ground up might sound like a lot of work…and you would be right. It is a lot of work, and it’s going to take time to get it how you want it. However, this doesn’t mean that it isn’t worth doing. In this article, we are going to be taking a look at how you can build the perfect business office starting from the ground, and working your way up. Keep reading down below if you would like to find out more.
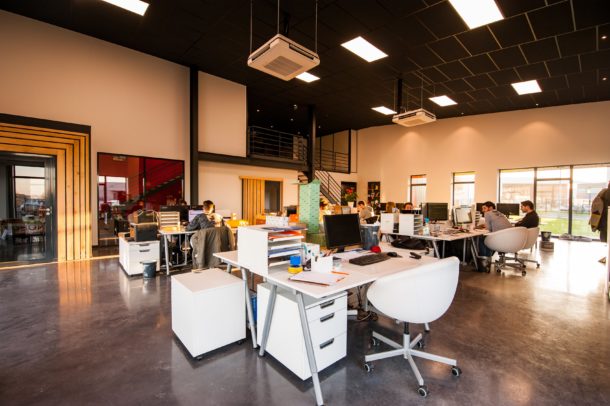
Hire The Right People
First, you want to make sure that you are hiring the right people. This is going to count for every single piece of the project from backhoe services if you need them, all the way to builders. We recommend that you take your time with this, looking through all of the possible options and reading reviews of each business. This will give you the most accurate idea of which company or tradesmen are going to be the best fit for you. Of course, you’re going to have to speak to all of them before you hire them, but then you can get started.
You have to be able to trust every single person that you hire, so if you can’t, you need to reevaluate your plan.
Think About Heating And Cooling
Heating and cooling is an important part of any business office, and you need an expert to work on this for you. It’s essential that you take the time to plan out, and speak to the contractors to work out the best way to do this. A lot of business owners think that saving money here by going for the cheaper options is a good idea, but it’s not in the slightest. It might cost you a little more, but it’s going to be worth it when you have a business office that is a suitable, comfortable temperature for everyone to work in., ensuring that your employees are working as well as they can be.
Work On The Design
The final thing that you can then do is work on the design of the business office. Again, hiring a professional to do this for you is likely the best option that you have got. They will be able to design an office space that fosters productivity, looks fantastic and appeals to both employees as well as customers. The design of your business office is important, so it’s not something that you want to take the risk with.
We hope that you have found this article helpful, and now see some of the things that you need to do in order to build the perfect business office from the ground up. It’s true that this is going to take some time, but it’s going to be worth it when you have an absolutely fantastic business office to call your own! We wish you the very best of luck, and hope that this works out in your favor.