What Is Plastic Injection Molding? Plastic is one of the essential materials used in many industries – food packaging, medical devices, the automotive industry, construction and building, transportation, electrical parts, home appliances, and more. Plastic components are versatile and allow greater flexibility to be used in several ways. These plastic parts can be produced by Read more
Whats New
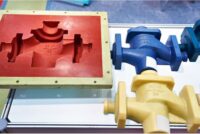
What Is Plastic Injection Molding?
Plastic is one of the essential materials used in many industries – food packaging, medical devices, the automotive industry, construction and building, transportation, electrical parts, home appliances, and more. Plastic components are versatile and allow greater flexibility to be used in several ways. These plastic parts can be produced by plastic injection molding. One significant advantage of plastic injection molding is the short production cycle. The entire process ranges somewhere from 2 seconds to 2 minutes.
- Injecting: In this process, machines inject molten plastic into a mold cavity.
- Cooling: The mold is exposed to the cooling process, solidifying the injected plastic.
- Ejection: Once the mold is cooled, the plastic part is removed and ready to use.
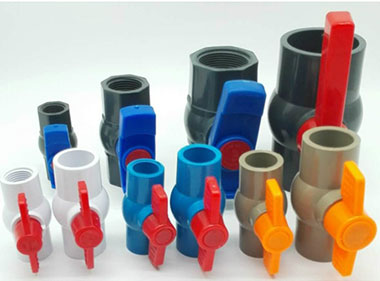
Applications Of Plastic Injection Molding
Injection molding can be used to create plastic components of different styles and shapes. Here are some of the most common applications of plastic injection molding.
- Medical Components: Includes devices such as dishes, syringes, and valves.
- Furniture: Includes parts such as cushions, chairs, side tables, etc.
- Automotive: Bumpers, cupholders, housings, and dashboards.
- Consumer Plastics: Caps, toys, and phone cases.
- Aerospace: Panels, housings, and bezels.
- Electronics: Switches, assemblies, circuit boards, etc.
Benefits Of Using Plastic Injection Molding
Injection molding is a reliable and quick manufacturing method, which sets it apart from other manufacturing processes. Here are some of the notable benefits of the process.
- Precision: When plastic components are fabricated by the method of injecting plastic into molds, it ensures high accuracy and consistency.
- Efficiency: Injection molding is incredibly efficient; it can create large quantities of parts quickly and easily, making it an ideal choice for mass production.
- Versatility: Plastic injection molding can produce any shape or design you want. This process is feasible for all types and sizes of businesses.
- Cost-effective: This manufacturing method is cost-efficient, setting up the machine and producing items at a low cost while yielding high-quality results.
What Factors Should You Consider When Choosing The Plastic Injection Molding Process?
Is plastic injection molding the right option for your business? Here are a few factors to consider.
- Part geometry
- Desired production quantity
- The desired quality of the finished product
- Number of gates and runners
- Type and amount of material
- Required cycle time
- Desired part finish
Once you have considered these factors, you can select the process that will best meet your needs.
What are the Important Factors to Consider When Choosing a Plastic Injection Molding Supplier?
The following are the top factors to consider when choosing a plastic injection molding supplier:
- Experience: One of the most important factors is the supplier’s experience and track record. You’ll want to find a supplier with much experience producing your desired product. You’ll also want to ensure the supplier has a good track record for quality and reliability.
- Design requirements: Plastic injection molding process starts with design. Choose a company with a great design team who can understand your objectives. A good design team knows to simplify geometry and minimize the number of moving parts in the process.
- Production requirements: Another critical factor is the supplier’s ability to meet your production needs. You’ll need to find a supplier to meet your volume requirements and turnaround times.
- Price: Make sure you compare the prices of several injection molding companies to find the best deal.
Final Words
Discuss your requirements with a plastic injection molding company. Communicate your expectations and specific design needs with them. Based on your needs, they will be able to give you an accurate estimate.
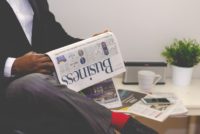
One of the biggest challenges faced by business owners is facing failure. When you’re on the right path to business ownership the last thing that you want to do is lose that. You have to choose to fail to learn in some cases, but you can easily get yourself caught in the belief that a Read more
One of the biggest challenges faced by business owners is facing failure. When you’re on the right path to business ownership the last thing that you want to do is lose that. You have to choose to fail to learn in some cases, but you can easily get yourself caught in the belief that a new business requires a LOT of funding, a youthful expression and a carefree attitude.
It’s a myth, and yet it’s something that most people consider to be a must when owning and running a business. The number of startups that fail in their first year is high, so that doesn’t really help! You need to know the statistics to be sure that your startup isn’t going to instantly flop out. So, we’ve got a Lendio list for you in an infographic below:
Infographic Design By Lendio
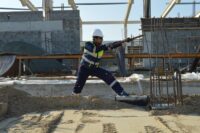
Today, many people aspire to start a career in the IT field. Such specialists are in great demand, and also receive high wages. Thus, even children from an early age understand where they need to strive to build a profitable career. However, not every person is born to work in the office at the computer Read more
Today, many people aspire to start a career in the IT field. Such specialists are in great demand, and also receive high wages. Thus, even children from an early age understand where they need to strive to build a profitable career.
However, not every person is born to work in the office at the computer. Many people are passionate about hands-on work. Specialists who can repair plumbing or complex equipment, build a house, and conduct wiring will always be needed. These jobs also pay well.
Everyone strives for luxury and dreams of buying a fancy car or being able to go on holiday to be pampered and rent a luxury car in Dubai. By the way, renting a premium car is not an impossible dream, because in Dubai everyone can rent a sports car at a reasonable price. In addition, car rental specialists offer the best customer experience.
Therefore, you do not have to dream of a career in IT. If you are born for hands-on activities, then we will tell you about professions that will become profitable for you.
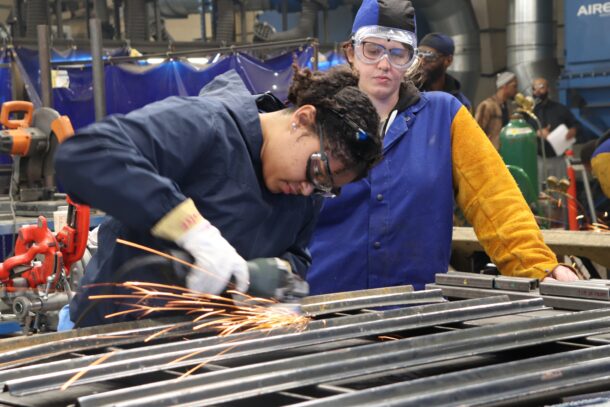
Construction Manager
If you want to connect your life with the construction of various houses and objects, you should strive to get the position of a Construction Manager. Such a person is the one who controls the construction projects from their very beginning to the end. This is a responsible job, so the ability to organize the work of subordinates and the skills of a leader are indispensable.
You can start with small projects. As you gain experience and improve your skills, you can start working on larger projects. However, if you want to further advance your career and increase your salary, you will need to complete a bachelor’s degree.
Elevator and Escalator Mechanic
In every city, more and more high-rise buildings appear every year, where the presence of elevators, as well as escalators, is mandatory. Since such objects are the most used, their breakdowns occur frequently.
A mechanic who can read blueprints, replace faulty parts, and ensure the safety of equipment will always be in high demand. The most important criterion for professionals is to improve their mechanical skills.
Experience and the ability to work at height will also be an advantage. Since improvements and changes are taking place in this area, such a specialist should be aware of all the latest improvements and be able to work with innovations.
Electrical and Electronics Engineering Technologist
To work in this professional area, specialists need to be trained at a trade school. During the training, specialists learn to work with electronic and electrical equipment, make drawings and diagrams, produce parts, and perform equipment maintenance.
You should have both mechanical and logical skills. In addition, your powers of observation will be to your advantage. To work with the equipment, specialists need to obtain a certificate. After that, you can work in various production facilities, in engineering services, as well as in various organizations.
Boilermaker
Since the assembly, repair, and maintenance of boilers often have to be done on the street, specialists need to have physical endurance. Sometimes specialists have to work even in the most unpredictable situations.
In addition, you can perform your work, both in residential and commercial buildings, in various factories, as well as on ships. Technical training includes training in reading blueprints, using tools, and safety precautions.
Conclusion
Not only IT professionals can make good money today. Specialists employed in construction, the ones who work with complex equipment and hardware, in engineering will always remain in high demand. Such work requires mechanical and technical skills. Moreover, your physical endurance will be a must-have. Having many years of experience and improving their skills, specialists can always count on a good salary and professional career advancement.
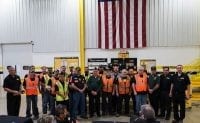
As someone who knows the ins and outs of running a trade business, you know that your employees are the backbone of your company. So, providing them with employee benefits can go a long way in showing that you value their hard work and dedication. In this article, we’ll dive into some of the most Read more
As someone who knows the ins and outs of running a trade business, you know that your employees are the backbone of your company. So, providing them with employee benefits can go a long way in showing that you value their hard work and dedication. In this article, we’ll dive into some of the most sought-after employee benefits and why they’re important for those in the trades.
Health Insurance
As a tradesperson, your physical health is crucial to your ability to work. That’s why health insurance is a must-have benefit for employees in the trades. It can help cover medical expenses, such as doctor visits, prescription medications, and emergency care. Plus, it can attract and retain top talent, as employees increasingly look for benefits that support their physical and mental well-being.
Retirement Plans
Planning for retirement may not be top of mind for many tradespeople, but it’s never too early to start saving. That’s why offering retirement plans, such as 401(k)s, IRAs, or other types of retirement accounts, is an important benefit to consider. Retirement plans can help employees save for their futures and feel more secure in their retirement plans. Some plans even come with employer matching contributions, which can help incentivize employees to save even more.
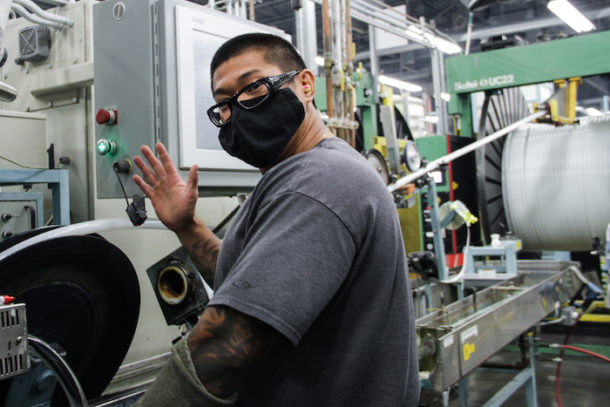
Paid Time Off
Paid time off (PTO) is a highly valued benefit that includes vacation days, sick leave, and personal days. Providing your employees with adequate PTO can help them maintain a healthy work-life balance and avoid burnout. Additionally, PTO can help employees feel more loyal to their employers, as they know their employer cares about their well-being.
Flexible Schedules
Working in the trades can mean long days and physically demanding work. Offering flexible schedules can help employees balance work and life responsibilities. This can include telecommuting options, flexible work hours, or even compressed work weeks. By providing employees with more control over their schedules, you can help them feel more in control of their lives and more satisfied with their jobs.
Employee Assistance Programs
Mental health is just as important as physical health, but it’s often overlooked in the trades. Employee assistance programs (EAPs) offer access to counselling, mental health resources, and other support services. EAPs can help employees address personal or work-related issues that may be impacting their well-being. By offering these services, you can demonstrate your commitment to your employees’ mental health and well-being.
Wellness Programs
The trades can be physically demanding, so prioritizing employee wellness is crucial. Wellness programs are a growing trend and can include initiatives such as gym memberships, healthy eating programs, and stress-management courses. By promoting wellness, you can help employees stay healthy and prevent injuries on the job.
EV Charging Stations
Another up-and-coming benefit to consider is providing EV charging stations for employees who drive electric vehicles. As more tradespeople adopt EVs, having a convenient and accessible charging station at work can be a significant perk. This benefit not only supports employee sustainability efforts but can also attract environmentally conscious talent to your team
Providing employee benefits is an essential part of running a successful trade business. Be sure to demonstrate your commitment to your employees’ well-being by helping them to feel valued and supported.
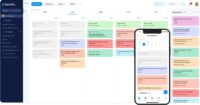
As technology continues to evolve, the construction industry has not been left behind. With numerous digital tools available to constructors, work is now faster, easier, and more efficient. In this article, we will take a look at some of the best digital tools for constructors. These tools are designed to help constructors to streamline their Read more
As technology continues to evolve, the construction industry has not been left behind. With numerous digital tools available to constructors, work is now faster, easier, and more efficient. In this article, we will take a look at some of the best digital tools for constructors.
These tools are designed to help constructors to streamline their work processes and ultimately deliver high-quality projects.
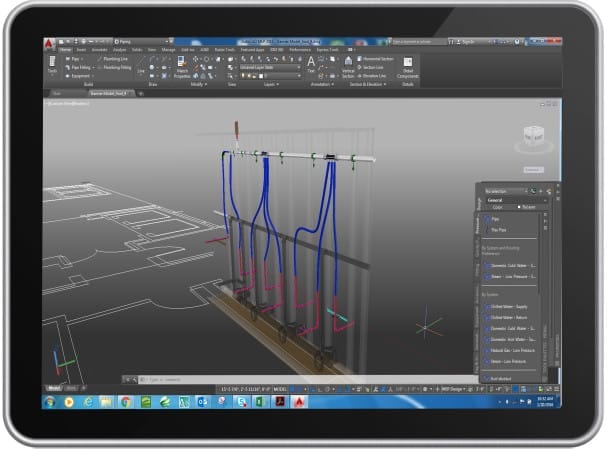
Building Information Modeling (BIM) Software
BIM software is one of the most useful digital tools for constructors. This software allows constructors to create 3D models of their projects, giving them a more detailed understanding of how everything will fit together. BIM software also helps constructors to visualize and identify potential issues before construction begins. Examples of popular BIM software include Autodesk Revit, ArchiCAD, and Autodesk BIM 360.
- Autodesk Revit allows users to design and model buildings in 3D, with tools for creating plans, sections, elevations, and construction details.
- ArchiCAD handles complex geometries and curved shapes with ease. ArchiCAD also offers a range of tools for design and documentation, as well as features for collaboration and data management.
- Autodesk BIM 360 – A construction management software that is designed for construction project teams. It provides tools for project management, design coordination, and construction document management.
Project Management Software
Project management software is another digital tool that has become essential for constructors. This software helps constructors to manage all aspects of their projects, including scheduling, budgeting, and tracking progress. Here are some of the most popular project management software tools available:
- Bordio – With Bordio, you can create and assign tasks to team members, set deadlines, and track progress in real-time. The platform also allows you to track the time spent on each task and generate detailed reports on project performance and productivity.
- Asana – A popular project management software that allows users to create and manage projects, track progress, and assign tasks to team members. It also provides tools for collaboration and communication.
- Trello – A visual project management tool that uses boards, lists, and cards to organize and track tasks and projects. It provides an intuitive interface and simple task management features.
- Basecamp – A web-based project management tool that allows teams to manage projects, share files and messages, and track progress in real-time.
- Microsoft Project – A project management software that allows users to plan, track, and manage their projects. It provides a wide range of features, including Gantt charts, project timelines, and resource management.
- com – A flexible project management software that allows users to manage projects, tasks, and workflows. It provides customizable project boards and collaboration tools.
- Wrike – A cloud-based project management software that provides tools for project planning, task management, and collaboration. It allows teams to manage projects and track progress in real-time.
- Smartsheet – A collaborative work management platform that provides tools for project and task management, resource management, and team collaboration. It allows teams to manage projects and track progress in real-time.
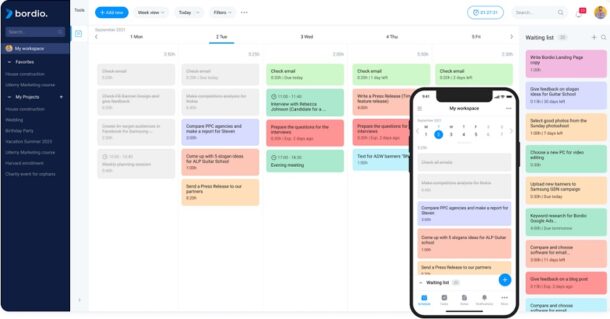
Field Service Management Software
Field service management software is designed to help constructors manage their field service teams. It includes features such as scheduling, dispatching, work order management, and invoicing. Examples of field service management software include ServiceTitan and Workiz.
- Workiz helps businesses manage their scheduling, dispatching, and billing needs. It offers features such as job tracking, invoicing, GPS tracking, and customer communication. Workiz also offers a mobile app, allowing technicians to view their schedules, manage jobs, and communicate with customers while on the go.
- ServiceTitan is a comprehensive platform that helps service businesses manage their operations, including scheduling, dispatching, invoicing, payments, and more. It provides real-time updates, customizable reporting, and automation features to help service companies streamline their workflows and improve their customer experience.
Construction accounting software is designed to help constructors manage their finances. It includes features such as invoicing, accounts payable, accounts receivable, and payroll. Examples of construction accounting software include QuickBooks and FreshBooks.
- FreshBooks is a cloud-based accounting software solution that offers invoicing, expense tracking, time tracking, and project management features. It is designed specifically for service-based small businesses, such as freelancers, consultants, and creative professionals.
- QuickBooks is a comprehensive accounting software solution that offers a range of features, including invoicing, expense tracking, payroll, inventory management, and more. It offers both desktop and cloud-based solutions and is popular among small to medium-sized businesses.
Collaboration Software
Collaboration software enables constructors to work together on documents and projects in real-time, regardless of location. It allows for easy communication and file sharing, making it easier for teams to work together on complex projects. Examples of collaboration software include Microsoft Teams and Google Drive.
- Google Drive is a cloud-based file storage and sharing platform designed to help individuals and teams easily store, access, and share files from anywhere with an internet connection. It includes Google Docs, Sheets, and Slides, which are similar to Microsoft Word, Excel, and PowerPoint.
- Microsoft Teams is a collaboration and communication tool that is designed for teamwork and group projects. Teams allows team members to collaborate in real-time on projects, share files, hold video and audio meetings, and chat with one another.
How to use a construction software tool
The specific steps for using a construction software tool will depend on the tool in question. However, here are some general steps that you can follow to use a construction software tool:
Research the software:
First, you should research the software you want to use. Look for reviews and ratings from other users, and consider factors such as the features, pricing, and user-friendliness of the software.
Install or sign up for the software:
Once you have selected a software tool, you may need to download and install it on your computer or device. Alternatively, you may need to sign up for an account on a web-based software tool.
Familiarize yourself with the software:
Once you have installed or signed up for the software, take some time to familiarize yourself with the features and functionality of the tool. This may involve reading the user manual or watching tutorial videos.
Set up your project:
Most construction software tools will require you to set up your project before you can begin using the software. This may involve creating a project timeline, setting budgets and goals, and assigning team members to different tasks.
Use the software to manage your project:
With your project set up, you can begin using the software to manage your project. This may involve using features such as scheduling tools, cost estimating tools, or collaboration tools to keep your project on track.
Update the software regularly:
Finally, be sure to update the software regularly to ensure that you have access to the latest features and bug fixes. Many software tools will automatically update, but you may need to check for updates manually from time to time.
By following these steps, you can begin using a construction software tool to manage your project more efficiently and effectively. Remember, it’s important to choose the right software for your needs and take the time to learn how to use it effectively.