Prototyping is a crucial step in the design and development of a product. It ensures the product, as envisioned in the design phase, is brought to life through a functional prototype. Of late, injection molding has emerged as the first choice prototyping method for manufacturers.
There can be many reasons one chooses injection molding for prototype processing, but will it be the right choice for your project? Let’s find out.
Definition
Prototype injection molding refers to creating a prototype using molds in less time. It is a process that is chosen for the rapid production of prototypes. In this process, molten plastic gets injected into a mold, thus creating a prototype that can be tested to check whether a part or product works.
It is often used to produce quick and high-quality prototypes and samples. The molds are two pieces that are held together with force and extreme pressure to create an accurate prototype after the process of prototype material selection that can be used to study the efficiency and usability of a part or product.
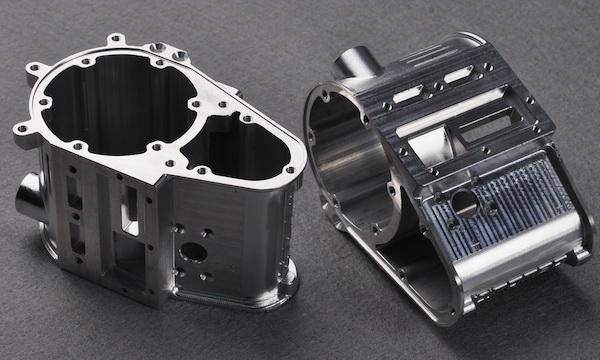
Advantages of Prototype Injection Molding
If you’re leaning towards prototype injection molding, you can enjoy many advantages which can positively affect your project. So here are the benefits of prototype injection molding.
Lower concept risk: As it is made of aluminum or soft metal alloy, the concept risk is quite lower with prototype injection molding. The material is easy to machine, making it easier to modify and alter. It provides much freedom to alter and put changes to previous output.
More time efficient: It is an accelerated process as it can produce your first part within 2-4 weeks with the right prototype material selection. Prototype injection molding is time efficient, especially when you have to produce multiple parts. It is more than 40% faster than a machine. It can help you create more.
Low Financial Risk: It may be known as the most expensive prototyping process, but when it comes to producing with right prototype material selection, it will be a smart investment. It can help you produce thousands of parts in no time. Those parts will be your property and can be used to produce small fragmented plastic parts.
Disadvantages of Prototype Injection Molding
Well, every process has its pros and cons, and so does prototype injection molding. When it comes to limitations, it has a fair share of it, from being the most expensive to the use of plastic injection and choosing prototype injection molding.
Time-taking process: Even though being quicker than standard injection molding, it is a longer process than some of the other prototype technologies. It takes time, as one must create a mold and inject materials to create the parts.
Use of plastic injection: Prototype injection molding requires plastic injection, which requires a special set of skills, does skilled labor with a specific qualification, which invites the hassle of finding a suitable candidate. Apart from that, finding especially skilled employees can put a strain on the entire budget and the process.
Most expensive prototyping process: As discussed earlier, manufacturing a prototype will be less expensive, but the investment is relatively high. The cost of the equipment and the injection materials is very much higher. The labor cost is also something that will prove to be challenging with prototype injection molding.
Click here to read about prototyping your ideas before manufacturing.
Conclusion
Prototype injection molding can be a great option that will be perfect due to many reasons. It has been designed to provide a large output with lesser effort and resources. Apart from this, several more amazing options are available for rapid prototyping.
Join the conversation: