For years, the question posed in the title wasn’t heavily considered. Vented roofs were the standard, and unvented roofs were practically unheard of. Unvented roofs have become more popular in recent years for a wide variety of reasons, many of which we’ll examine in the body of the article. Before getting into the meat of Read more
Guest Blog
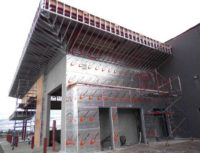
For years, the question posed in the title wasn’t heavily considered. Vented roofs were the standard, and unvented roofs were practically unheard of. Unvented roofs have become more popular in recent years for a wide variety of reasons, many of which we’ll examine in the body of the article.
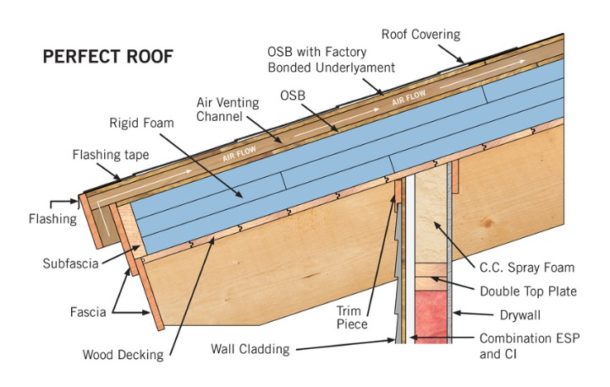
Before getting into the meat of things, it’s worth noting that “what is the best design?” never has a clean answer; if it did, things would be a lot less interesting. Instead, what we’re considering is the advantages of both roofing types given certain circumstances. In other words, vented roofs may well be the best design for one home, while an unvented roof will be a better solution for another home.
Vented Roofs
Vented roofs serve a number of different purposes and their roles vary from climate to climate. In colder climates, the main purpose of a vented roof is to keep the roof cold and reduce the formation of ice dams. A secondary goal is to vent moisture that infiltrates the attic from the conditioned home. In warm climates, ventilation serves to reduce the cooling load of the rest of the building by reducing the impact of solar heating, though studies have shown this method isn’t as effective as we previously thought.
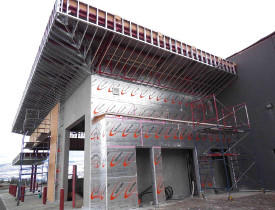
There are a couple of disadvantages to vented roofs; they tend to be more susceptible to certain hazards. For example, windstorms can cause vented soffits to collapse, creating excessive pressure, which may lead to window blowout and roof loss. And, according to experts from Solargenerator guide, setting up a solar system to power up the whole house might as well be a little complicated when using a vented roof.
Unvented Roofs
Unvented roofs have a number of advantages. Ventilation becomes more difficult the more complicated a roof’s construction is. As a result, unvented roofs have become popular in homes with feature-dense roofs – think multiple skylights, dormers, and other aesthetic flourishes.
The disadvantages of unvented roofs have, to a certain degree, been overstated – in hot climates, the extra heat gain from unvented roofs rarely exceeds a couple of degrees Celsius.
Moisture from the conditioned section of the building must be addressed when using an unvented model. Generally, this can be handled by employing moisture barriers during the construction process, effectively creating something of a self drying roof. The folks at Quik-Therm Insulation say you can employ permeable insulation because “a self-drying non-vented roof design is unattainable if the roof assembly can’t dry both inward and outward”.
Roofing and HVAC
There are a number of reasons why you might want to install ductwork and mechanical systems in the attic of a home, including aesthetic considerations and saving space. In light of this, it’s important to think about the difference between vented and unvented roofs and different HVAC configurations.
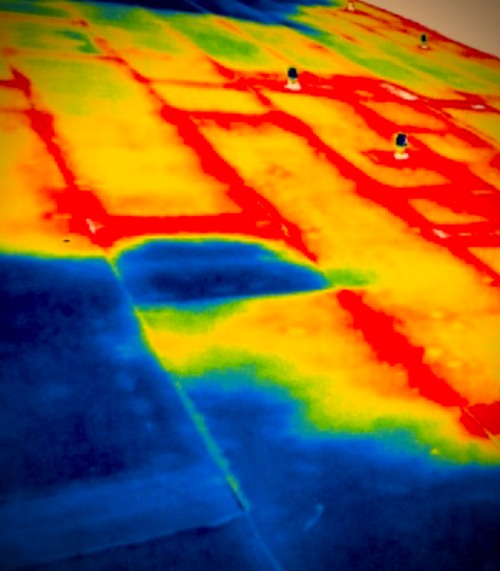
When ductwork and mechanical systems are located in the roof, an unvented roof is generally preferred. When the roof is vented, exfiltration from leaky ducts and air handling units is intensified, and infiltration from the external climate is accelerated by the change in pressure from air loss. This creates thermal penalties in both hot and cold climates. What’s more, heat leaking from ducts can melt snow and create ice dams, the prevention of which is one of the key reasons to employ vented roofs in the first place.
There is much debate about whether or not HVAC systems should ever be placed in the attic. Many modern green building principles rely on a completely sealed building envelope to avoid hot and cold spots caused by increased thermal transfer. The attic and roof can play an essential role in building envelope construction; sealing the roof off from the rest of the house can allow the creation of a highly insulated barrier to the conditioned areas of the home.
Should you opt to run ductwork or place mechanical systems in the attic, an unvented roof is best for avoiding thermal penalties as the ductwork will be located in a conditioned space, allowing the system to recover thermal losses through the ducts. As Provincial Heating points out, any weakness in your thermal envelope can cause problems: “Wood studs between sheets of insulating fiberglass, for example, have a lower R-value and thus reduce the R-value of the total system”.
What’s Best?
As you can see, the best type of roof is highly variable. Are you in a cold climate with an uncomplicated roof? Is your HVAC system entirely located within the conditioned area of your house, and you want to use your attic as a thermal barrier? Your best bet is likely to be a vented roof.
Are you in a warmer climate? Is your roof difficult to construct? Do you want to keep ducts and the like in your attic? You’re probably better off with an unvented roof.
It’s always worth mentioning with any change like this, that the quality of the finished product will always depend on the quality of the workmanship. So whichever you go for, you are going to get the best result by making a point of hiring only the very best, such as Contractors Inc, for the whole procedure. As long as you bear that in mind, you are more likely to get the results that you are really hoping for with your roofing.
Keep in mind that vented and unvented roofs are quite different; everything from the building materials you use to the type of insulation you’ll install will vary depending on what type of roof you opt to construct. When advising clients on their HVAC systems, it’s important to consider the type of roof they have as well as their overall building envelope. Optimally, this should all be done during the planning and construction stages, but for replacements and renovations, roof type needs to be kept in mind.
Blogger Bio: Kiara Fullam is a blogger and some of her favorite pieces can be found on Powertec Electric’s website.
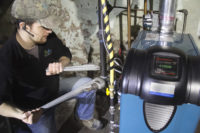
I will always preach that a successful cast iron water boiler installation begins with proper planning. I worked for an oil company for 20 long years, and nine years of that I was a service manager. During this time, I came across many problematic jobsites. I would evaluate the installation issues and try to figure Read more
I will always preach that a successful cast iron water boiler installation begins with proper planning. I worked for an oil company for 20 long years, and nine years of that I was a service manager. During this time, I came across many problematic jobsites. I would evaluate the installation issues and try to figure out where the problems had started. This knowledge has greatly helped me as a Training Manager for U.S. Boiler Company. Now, after 40 years in the heating business, I know how important proper boiler installation planning really is for reducing the number of problem jobs and expensive callbacks. In fact, planning is much easier than you may think …
- Proper boiler sizing. Complete a thorough heat loss calculation. Do not fall into the trap of oversizing the boiler because you sized it based on the old boiler size or you measured the connected radiation load, and never allow the customer to talk you into a larger boiler than needed. Today, with physically smaller boilers and less water volume, oversized boilers will short cycle more than ever. Increased short cycling means higher maintenance, higher fuel costs, and higher installation costs.
- Follow the boiler Installation & Operation (I&O) Manual. Be sure to follow one of the suggested near boiler piping options listed in the manual. The boiler tapping may not have to be the same size as the manifold piping. Use the flow charts for pipe size. You can pipe the boiler the same size as the tapping, or in some cases, use smaller piping dependent on the heat loss requirement. When the heat loss is known and the proper boiler size is chosen, you may be able to use smaller air separators, expansion tanks, and piping. You can use the following as a guide to size the boiler and system piping:
- 3/4” pipe = 40,000 BTU’s @ 4 – 5 GPM (gallons per minute)
- 1” pipe = 70,000 BTU’s @ 7 – 8 GPM
- 1-1/4” pipe = 160,000 BTU’s @ 16 – 18 GPM
- Bypass piping. Bypass piping is discussed briefly in the I&O manual. We cannot continue to install modern cast iron boilers the same way we used to install boilers with larger water volumes. When needed, a bypass system should be installed to protect the boiler. There are primary/secondary piping and circulated bypass options, both of which we will discuss later in this article.
The bypass system discussed in the manual is called a “boiler bypass” and is always installed the same size as the supply and return headers. When adjusted, the water flow through the boiler is slowed so the water spends more time in the boiler. This allows the boiler temperature to increase faster and decreases the possibility of boiler condensation. This means that some of the system return water is bypassed around the boiler and enters the supply beyond the boiler. I know what you are about to say. “Well, that will cool off the supply water going to the homes heating system!” That is correct, but it is not a problem. This is what I call a “poor man’s outdoor reset.”
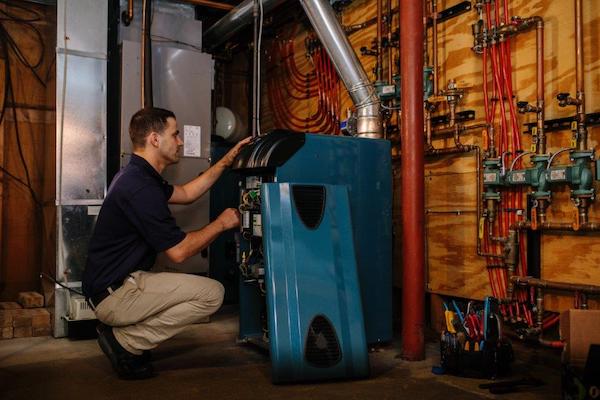
The system will run quieter and the system water temperature will increase slowly until the radiation outputs enough heat to satisfy the thermostat. The colder it gets outside, the hotter the system supply water temperature will be. When the valve placement is installed as shown in the manual, we can easily adjust the ΔT through the boiler. Simply put, leave the bypass valve open and adjust the flow through the boiler with either valve located on supply or return pipes below the bypass pipe to slow the flow and force more water through the bypass. Partially close one of these valves and check the ΔT through the boiler. You will need a minimum of a 20°F rise. If this is a large water volume system, like cast iron radiation, increase the ΔT through the boiler to 35 – 40°F ΔT.
Quick Tip: If the bypass is hotter than the return pipe, the flow is backwards and you have piped a system bypass as opposed to a boiler bypass. Follow the piping in the manual to verify correct installation.
- Primary/secondary piping option. Primary/secondary piping utilizes hydraulic separation so that the water flow from system pumps do not affect boiler pump flow. This allows us to reduce the flow through the boiler to heat the water faster and heat the water to a higher temperature without affecting the flow in the system. In other words, we can have a higher flow in the system and a lower flow in the boiler. We still want a minimum of 20°F rise through the boiler, and for higher water volume systems we want a higher ΔT near 35°F – 40°F.
- Variable speed bypass pump option. To have the best boiler protection, install a variable speed bypass pump with a temperature sensor. This will change the speed of the pump to obtain the proper return water temperature. We offer a variable speed bypass kit with instructions for gas water boilers. This will protect the boiler in a high-water volume system or radiant in-floor radiation application.
Quick Note: My concern, and the reason for the above discussion of boiler protection from condensation, is excessive water flow through the boiler and slower temperature increase. I have experienced multiple boiler installations where the ΔT through the boiler is less than 20°F. In fact, I have witnessed some as low as 8°F. Lower ΔT’s are a result of excessive flow, possibly caused by the number or circulator sizes installed on the system. So, what is the minimum flow rate on cast iron water boilers? Look in the I&O manual under specifications and find the DOE heating capacity (MBH) of the boiler. For instance, the Series 3 model 304B has an input of 105k MBH and a DOE heating capacity of 88k MBH. Divide the DOE output by 10,000 to discover the maximum flow required by the boiler. If your flow exceeds that number, the ΔT will be less than 20°F. You can use this hydraulic formula to determine flow rate through the boiler.
- Avoid short cycling. Short cycling is caused by lower water flow, or higher ΔT. Higher ΔT may mean that the circulator is to small, the boiler is oversized, or the valves not adjusted properly. Generally, the minimum boiler flow should be half (but not limited to) of the maximum boiler flow.
Boiler Flow Formula:
Q/(500*ΔT) = Flow
Q = DOE Heating Capacity
Let’s put some numbers to that formula. Let’s assume that a boiler has a ΔT of 15°F. The Series 3 model 304 (referenced above) has a DOE heating capacity of 88,000.
88,000/10,000 = 8 GPM. This is the maximum flow required by the boiler. Divide this in half to get the minimum boiler flow. In this case, it would be 4 GPM.
Now, back to the formula.
Q=88,000
ΔT = 15°F
88,000/(500 * 15) = Flow
88,000/7500 = 11.7 GPM
The flow is almost 4 GPM higher than the maximum flow the boiler should have. This tells us we need to achieve a 20°F ΔT, which means less flow through the boiler. Why do we have to much flow? There are oversized pumps or to many pumps. Using a bypass or primary/secondary strategy above, we can easily correct the flow through the boiler.
- Vent the boiler properly. If the boiler is chimney vented, the local and federal codes apply. A chimney liner may be required. If the unit is direct or power vented, the manufacturer dictates the venting according to the certifications obtained during testing. Since this article applies to cast iron water boilers, a sidewall vented boiler requires AL29-4C vent pipe. No plastic!
- Outdoor air. I like to use outdoor air as much as possible to verify enough combustion air. Plus, there is less chance of contaminated air.
- Gas pressure. Check the incoming gas pressure and the manifold (outlet) pressure with other gas appliances running. Check all safeties. Finally, always complete a combustion check.
Ron Beck is Outside Technical Advisor and Manager of Training for U.S. Boiler Company, where he’s been since 1998. Ron’s 34 years of experience in the heating industry include climbing the ranks of a HVAC company, from apprentice to service manager. Currently, he’s the go-to solution guy for contractors in the field.
Ron can be reached at RBeck@usboiler.net
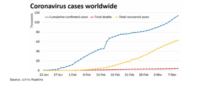
Peter DeMarco, Executive Vice President of Advocacy and Research – The IAPMO Group In 2019, the World Health Organization (WHO) started monitoring the outbreak of a new coronavirus which ultimately was named COVID-19. The virus was first identified in Wuhan, China. This paper is intended to provide practical guidance for plumbing professionals who work on Read more
Peter DeMarco, Executive Vice President of Advocacy and Research – The IAPMO Group
In 2019, the World Health Organization (WHO) started monitoring the outbreak of a new coronavirus which ultimately was named COVID-19. The virus was first identified in Wuhan, China. This paper is intended to provide practical guidance for plumbing professionals who work on sanitary waste and sewer systems on how to protect themselves, their loved ones and their coworkers during the current pandemic.
Coronaviruses are so named because, when viewed under a microscope, they have protrusions that resemble a crown. They belong to a family of viruses common in both humans and many animal species. In rare occurrences, animal coronaviruses can mutate to the point where they are able to also infect humans, which is likely what occurred in China late last year. The potential for viruses that cross over from animals to humans to develop into an epidemic, happens when the virus can then be transmitted between humans. The COVID-19 virus is highly transmissible between humans and can cause respiratory illness and even death.
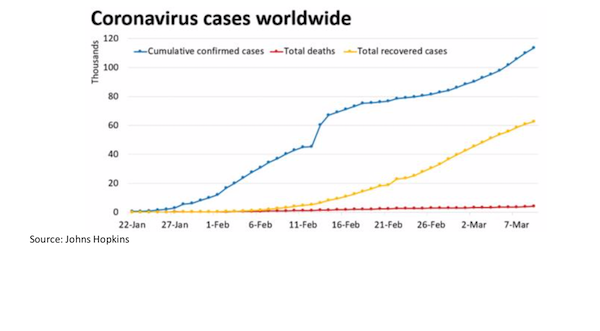
As of this writing on March 11, World Plumbing Day, the WHO has announced the outbreak qualifies as a pandemic, having spread on all inhabited continents. The worldwide number of humans diagnosed with COVID-19 has surpassed 120,000, with more than 4,300 deaths (see chart below). These numbers are predicted to grow. Unfortunately, there’s much we still don’t know about the virus, including important details about its transmissibility, how long it can survive on various surfaces or in water, and the range of illness severity amongst various population groups. It is known that the elderly and those who are immuno- compromised with pre-existing medical conditions are the most vulnerable for poor medical outcomes, which is consistent with other pathogen-based diseases, including influenza. However, contrary to some misinformation that’s currently available, the coronavirus is in fact considerably more dangerous than the current annual influenza virus.
So, what are the implications for those who work in the plumbing industry and what steps can plumbers take to stay safe? It is likely that the COVID-19 coronavirus can indeed be spread through building sanitary drainage systems. This became apparent when the Chinese government identified an outbreak in a Hong Kong high-rise building a few weeks ago (see the IAPMO white paper).
Therefore, for as long as the pandemic is still active, it should be assumed by anyone working on a sanitary drainage system that the virus is present. Considering the potential to come into contact with water and aerosols that contain the coronavirus when working on sanitary systems or sewers, it is highly recommended that plumbers wear proper personal protective equipment (PPE), including a full face shield that is worn over safety glasses, and gloves.
Of course, plumbers work on sanitary drainage systems that contain fecal matter and a host of dangerous pathogens every day. Taking careful precautions to prevent contact with wastewater and proper hand and arm hygiene is a matter of good practice for plumbers. In the United States, the Occupational Safety and Health Administration (OSHA) provides standards for worker protection. OSHA Standard 29 CFR 1926, Safety and Health Regulations for Construction provides the requirements for construction worker safety, including plumbers who work on sanitary drains, vent systems and sewers. The standards are available free at https://www.osha.gov/laws-regs/regulations/standardnumber/1926.
The most important subsections for plumbers to review are: 1926.20 – General safety and health provisions; 1926.21 – Safety training and education; 1926.22 – Recording and reporting of injuries; 1926.23 – First aid and medical attention; 1926.28 – Personal protective equipment; 1926.50 – Medical services and first aid; 1926.95 – Criteria for personal protective equipment; 1926.102 – Eye and face protection and 1926.103 – Respiratory protection.
Additionally, ASSE International’s Series 12000 Standard, Professional Qualifications Standard for Infection Control Risk Assessment for All Building Systems, is a standard that sets minimum criteria for the training and certification of pipe trades craftspeople, and other construction and maintenance personnel, on how to safely work in an environment with the potentially deadly diseases that may be present within
worksites. While the pandemic remains ongoing, ASSE International is making the ASSE Series 12000 Standard available for free at https://asse-plumbing.org/12000-2018 . The ASSE 12000 certification training addresses viruses, including the Sever Acute Respiratory Syndrome (SARS) virus, but does not specifically reference COVID-19. We welcome plumbers from across the globe to consider professional qualification for infection control risk assessment especially when working on sanitary systems that have a high probability of being contaminated with COVID-19, such as healthcare facilities and hospitals.
Finally, common sense still reigns supreme. Plumbers are advised to increase the frequency of hand washing and wash for at least 20 seconds with soap and water (even longer hand washing time is good practice after contact with wastewater); avoid touching of the face; cover any open cuts or wounds and wear proper PPE. If you personally come into close proximity, or into direct contact with an infected person, immediately report the incident to your supervisor and to your doctor or healthcare provider.
Good workplace and tool cleaning practices are also extremely important. Avoid sharing of tools with coworkers to the greatest extent possible. When choosing cleaning chemicals, look for cleaning agents with claims against viral pathogens. If such cleaning agents are not available, use soap and water and dry tools thoroughly after use. Keep your PPE clean as well by following manufacturer instructions carefully.
With no vaccine or treatment regimen currently available, it is important for all workers to be able to recognize the symptoms associated with contracting the coronavirus, which include fever, shortness of breath, and persistent cough. Symptoms can take between 2 to 14 days to become apparent after exposure to the virus. If you start to feel ill, stop work immediately so as to protect your coworkers and others around you, go home, contact your doctor and follow your doctor’s orders! This is critically important when working in a facility that houses immuno-compromised people.
The IAPMO Group sends its best wishes to plumbing professionals around the world. We hope that the information above is helpful. As usual, plumbers are on the front lines fighting the battles that keep people safe. By working carefully and thoughtfully, we can also keep ourselves and our loved ones safe as we deal with and defeat COVID-19!
Additional sources of useful information can be found at the links below:
https://www.who.int/emergencies/diseases/novel-coronavirus-2019
https://www.cdc.gov/coronavirus/2019-ncov/index.html
https://www.wef.org/resources/online- education/webcasts/ArchivedWebcasts/CoronavirusWebcastArchive/
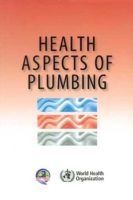
By Pete DeMarco, Executive Vice President of Advocacy and Research, IAPMO Health officials in Hong Kong have determined that plumbing systems in certain high-rise buildings are implicated in recent cases of the COVID-19 coronavirus. Based on the limited information available, it’s clear that transmission paths that would allow for the virus to spread between individual apartment Read more
By Pete DeMarco, Executive Vice President of Advocacy and Research, IAPMO
Health officials in Hong Kong have determined that plumbing systems in certain high-rise buildings are implicated in recent cases of the COVID-19 coronavirus. Based on the limited information available, it’s clear that transmission paths that would allow for the virus to spread between individual apartment units in at least one high-rise building have been identified. In order to understand how this has happened, it’s important to have some very basic knowledge of how wastewater systems work in high-rise buildings and to also look back at the SARS outbreak of 2003; the parallels are striking. In fact, the SARS virus is also a strain of coronavirus, so it’s not surprising that COVID-19 has been identified as having the potential to spread through plumbing systems.
High-rise buildings present unique challenges in plumbing design. The following simplified explanation is intended to help illustrate the problem: When toilets in high-rise buildings are flushed, fecal matter and wastewater are discharged into a vertical wastewater pipe, called a “drainage stack.” As the wastewater descends in the stack, it creates pressure changes within the pipe. The wastewater flowing down a stack will push air down ahead of it and drag air behind it, creating both positive and negative pressures within the drainage system. These pressures can affect trap seals by either siphoning the water or pushing the water out of the trap. A second vertical pipe, called a “vent stack,” typically runs parallel to the drainage stack and introduces air into the drainage stack every fifth floor to avert excessive changes that could deplete trap seals and allow contaminated air and aerosols to enter apartments on other floors.
When the SARS outbreak occurred in 2003, problems with dry traps were indicated, allowing contaminated air and wastewater aerosols to enter into apartments on lower floors through floor drains that are required by Chinese and many other Asian national construction codes. A full explanation of how the SARS outbreak occurred and technical solutions providing health and safety associated with proper plumbing practices can be found in The Health Aspects of Plumbing, a publication produced by the World Health Organization and the World Plumbing Council.
Sadly, with the current coronavirus outbreak in Hong Kong, history seems to have repeated itself. According to the Associated Press, a 2016 Hong Kong Housing Department policy change has allowed tenants in certain high-rise apartments to alter the pipe design in their bathrooms without requiring an inspection by a plumbing official, causing the problem that might have helped spread COVID-19. In one of the apartment units, the vent pipe was completely disconnected inside the bathroom, apparently by the occupant, which provided a pathway for contaminated air to enter the apartment, especially when the bathroom ceiling fans were activated. When health officials became aware of this problem, the building was evacuated, hopefully limiting the number of additional illnesses among building residents.
Can the COVID-19 coronavirus be spread in high-rise buildings in the United States in a similar manner? In short, the answer is yes, but unlikely. Due to U.S. plumbing codes, any modification to a building’s water, waste or vent system must be performed by a qualified professional and necessitates an inspection by a code official. In addition, wastewater stacks and vent pipes are typically hidden behind walls in high-rise buildings, reducing the opportunity for residents to easily cut into pipes and create unsafe conditions.
Both the SARS and the current COVID-19 coronavirus outbreaks in Hong Kong illustrate the importance of proper plumbing design and practice in keeping building residents safe from disease and the profound problems that can develop when unqualified individuals decide to work on building water systems. The axiom “the Plumber Protects the Health of the Nation” is more than a slogan. Improper deviations to building plumbing systems can, and indeed often do, result in very significant loss of life and property.

Distributor sales incentives and rebate programs can be deployed to accomplish strategic goals within the distribution channel. These goals might include structuring promotions to drive sales of high margin products, move old inventory to free up space or speed up the adoption rates of new products. There are important considerations to take into account to Read more
Distributor sales incentives and rebate programs can be deployed to accomplish strategic goals within the distribution channel. These goals might include structuring promotions to drive sales of high margin products, move old inventory to free up space or speed up the adoption rates of new products.
There are important considerations to take into account to ensure the success of a distributor incentive program. Utilize these best practices for maximum ROI.
Analyze Your Audience
The success of your distributor sales incentives and rebate program depends on being able to personalize your marketing to your distributor sales reps (DSRs). During the registration process, make sure you are collecting accurate contact, firmographic and demographic data to personalize your promotional marketing.
Align Promotions with Organizational Goals
Having specific, measurable outcomes in mind will allow you to structure your distributor incentive program to achieve those outcomes. The ability to run multiple promotions by product, region or organization can allow manufacturers to be really granular in tackling specific objectives.
Strategically Select Rewards
Your rewards should be scalable to different levels of performance. After all, you wouldn’t want to award your VIP accounts and part-time customers the same amount of value. The types of reward you offer also depends on the length of your promotions. Debit-card based SPIFFs and rebates are more suitable for short-term promotions, whereas merchandise rewards or incentive travel would make more sense for long-term, loyalty-based promotions.
Regularly Communicate with Your Distributor Sales Reps
To maximize the effectiveness of your incentive program, you should strive to regularly provide participants with relevant, engaging communication. This communication includes content on your program website, monthly statements, seasonal emails and promotional marketing via email, SMS and push notifications.
Track Distributor Incentive KPIs
KPIs – key performance indicators – are metrics you can track to ensure your incentive program is on pace to achieve its goals. These include site visits, the percentage of participants submitting claims, email open and click rates and sales-related metrics. It’s important to have software in place to monitor these KPIs and capitalize on opportunities for cross-selling, up-selling and re-engagement with your DSRs.
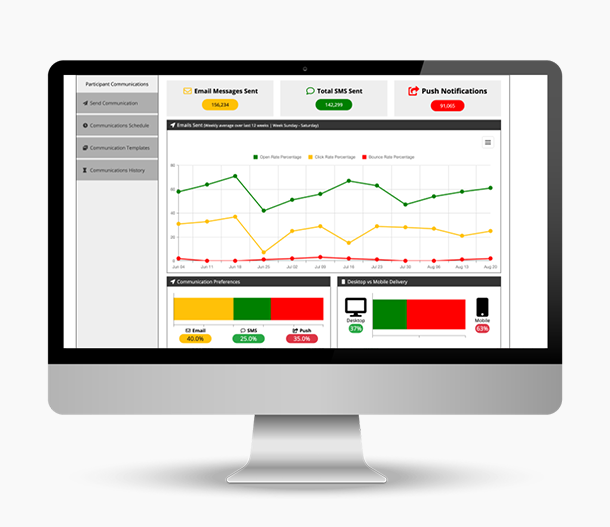
Monitoring KPIs gives you insight into account engagement and the success of each promotion.
Offer Sales Enablement for Eligible Products
Building brand preference depends on enabling your DSRs to effectively sell your products to dealers, contractors and wholesalers. There are a variety of ways to offer this enablement, such as:
- Creating interactive quizzes based on content or training videos;
- Requiring mandatory virtual or on-site training to qualify for promotions;
- Utilizing your reward program communications to educate participants on your product lines; and
- Rewarding participants for attending important trade shows.
Provide Convenient Platforms for Claims Submissions
In order to boost participation and maximize the quality of the data you receive, focus on making it easy for DSRs to submit and validate claims. Document upload tools allow DSRs to snap a picture of an invoice on their phones and attach it alongside their sales claims. Furthermore, this will make it easier for you to validate claims and quickly assign rewards. Doing so provides a better UX and will maximize the effectiveness of rewards as a behavioral modification tool.
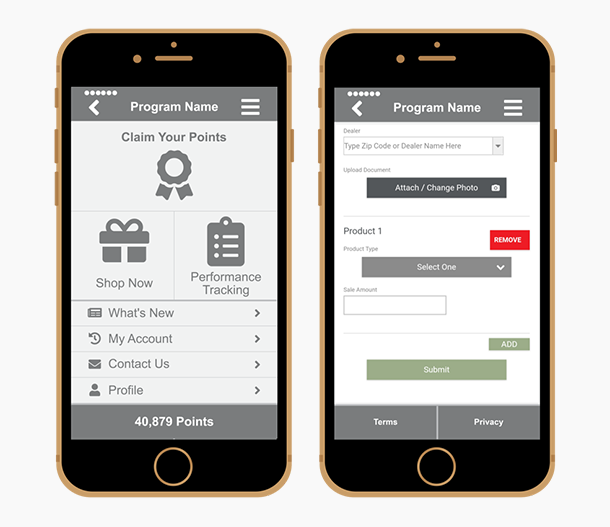
Providing mobile-ready platforms for participants to access your rewards program and upload sales claim verifications will ensure the success of your distributor sales incentive program.
Switch Things Up to Keep Your Program Fresh
Even an effective incentive program can reach a point of diminishing return. It’s important to switch up your promotions to keep your program exciting and interesting. Point multipliers and limited-time promotions can quickly boost sales growth or re-engage inactive accounts. And adding elements of gamification, such as leaderboards, spin-to-wins, achievement badges and on-the-spot point bonuses will make your program engaging and rewarding from end-to-end.
Seek Feedback and Analyze Results
Finally, you will want to arm yourself with data points to continuously improve your program. Seeking participants on surveys will help you add enhancements to your program and personalize your relationship with distributors. Analyzing KPIs and calculating ROI helps you prove program success and equip you with insights to make your next distributor sales incentive or rebate program even more successful!
For more incentive program strategies and best practices, check out Incentive Solutions’ complementary eBook, The Incentive Program Playbook.
Mark Herbert is President and CEO of Incentive Solutions. He has more than 30 years of experience overseeing business operations within the incentives industry. Incentive Solutions currently manages more than 220 programs, many of which are in industrial manufacturing and distribution. Mark Herbert may be reached at mherbert@incentivesolutions.com.