UMC and IMC Committees Vote to Disallow Flammable Refrigerants in Direct Systems and Maintain Current Safety Restrictions. One of the hottest topics in the mechanical code world is that of flammable refrigerants and their applications. The issue is currently playing out in the model code arena. In the United States, jurisdictions have a choice of Read more
Guest Blog
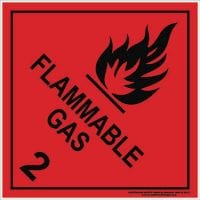
UMC and IMC Committees Vote to Disallow Flammable Refrigerants in Direct Systems and Maintain Current Safety Restrictions.
One of the hottest topics in the mechanical code world is that of flammable refrigerants and their applications. The issue is currently playing out in the model code arena. In the United States, jurisdictions have a choice of two model mechanical codes. The Uniform Mechanical Code (UMC) is developed by the International Association of Plumbing and Mechanical Officials (IAPMO); the International Mechanical Code (UMC) is developed by the International Code Council.
Uniform Mechanical Code
The IAPMO recently held their Uniform Mechanical Code (UMC) technical committee hearings to update the 2021 edition of the UMC in Denver Colorado on May 1 and 2. Several proposals would have allowed A2L (flammable) refrigerants to be used in direct, high probability systems in residential and commercial buildings.
It was a divided house as producers and manufacturers presented their respective cases on both sides of the issue. The committee allowed discussion to proceed for approximately 2 hours and experts from all facets of the industry debated and informed the committee’s decision makers. In the end, the committee sided with those who presented safety concerns about the introduction of flammable refrigerants before the risks were appropriately addressed. Assuming the committee’s decision is final, the 2021 edition of the Uniform Mechanical Code will not allow flammable refrigerants, including A2L refrigerants in direct air conditioning systems.
International Mechanical Code
The International Code Council (ICC) completed their 2021 International Mechanical Code (IMC) development process last year and also rejected code change proposals that would have loosened the restrictions on flammable refrigerants.
Summary
At both ICC and IAPMO mechanical code development hearings, a handful of manufacturers and industry associations advocated for enabling language to permit A2L refrigerants to be used in high probability direct air-conditioning systems for human comfort. They offered a great deal of testimony in support of their proposals. In the end, both technical committees came to the same conclusion: it is premature to allow flammable refrigerants to be widely used in direct, high probability systems.
Although they are forbidden in direct systems, both codes allow their use in indirect systems located in refrigeration machinery rooms due to the known attributes of such spaces, such as, size and volume of the room, current availability of reliable detection and ventilation and dilution rates.
Research is currently underway to inform those who are developing equipment and installation standards; this research includes an assessment of refrigerant detector characteristics; post-ignition risk assessment; effectiveness of mitigation strategies being proposed; ignition potential from electrical devices and more. This research should be used to develop equipment and installation standards. When the research is finished, the installation standards and equipment safety standards are completed, and the refrigerant technicians are trained, it’s likely the code development committees will look more favorably on the use of flammable refrigerants in these applications.
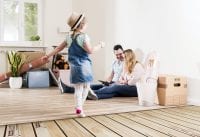
Forced air is still the traditional method of heating homes, but radiant heat is gaining significant momentum as an alternative. According to HGTV, the growth rate of in-floor radiant heating systems was estimated at 30 to 50 percent per year. At the heart of this shift is not just one single benefit. It’s a variety of advantages Read more
Forced air is still the traditional method of heating homes, but radiant heat is gaining significant momentum as an alternative. According to HGTV, the growth rate of in-floor radiant heating systems was estimated at 30 to 50 percent per year.
At the heart of this shift is not just one single benefit. It’s a variety of advantages that radiant floor heating systems bring to the table, the combination of which enhance the daily lives of a home’s occupants:
Even Heat Distribution
When a house is heated by a forced-air system, it will always be warmest near the vents that distribute the air. This can lead to “hotspots” on one end of a room while the other side of the room remains cool. And because hot air rises, upstairs rooms will be warmer than those downstairs.
With radiant floor heating systems, homeowners control how heat circulates in their home. Rather than heating the surrounding air, the heat that radiates from the floor warms other objects in the room and is evenly distributed without the potential for heat loss.
Improved Air Quality
While air pollution is more often associated with the outdoors, indoor air can be dirty as well. Whether it’s dust, pet dander or chemicals from fragrances (among other sources) that pollute the air, forced-air systems exacerbate the problem for allergy sufferers. That’s because the forced, heated air will stir up and mix with these airborne particles.
Since radiant floor heating systems don’t move air to deliver heat, the circulation of indoor particles is minimized. With less pollutants blown around, indoor air quality improves, which benefits allergy sufferers.
No Ductwork
The ductwork in forced-air systems further contributes to air pollution. When it’s riddled with cracks and holes, more dust and odors can enter and circulate. Without proper insulation, these same cracks and holes can cause air to leak out of the system and hinder its overall efficiency.
With no ducts, radiant floor heating systems reduce the churn of dust and allergens while curtailing heat loss. The absence of ducts means less work for homeowners as it eliminates the need for repairs like cleaning out ducts clogged with particles or adding insulation when heat loss mounts.
Energy Savings
With their uneven distribution of heat and potential for heat loss, traditional heating systems can be energy hogs.
Depending on how well a house is insulated, radiant floor systems can save up to 30 percent compared to forced-air systems. In terms of bills, the impact is quite significant as space heating is the largest energy expense for the average U.S. home, accounting for around 45 percent of energy bills.
Noiseless Operation
Homes should be quiet, but forced-air systems can be noisy as furnaces cycle on and off, gaps in the ductwork whistle and loose parts rattle.
By comparison, radiant floor heating systems are exceptionally quiet.
As consumers learn more about the advantages of radiant heating, its popularity will continue to grow.
Josh Quint is product manager, heating and cooling, for Viega LLC.
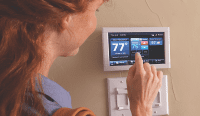
It’s easy to become overwhelmed when thinking about the Internet of Things (IoT) and the complexities of smart home appliances and products. However, it’s never too late to educate yourself on the smart HVAC features and products that are sought by today’s customers. Before the dawn of the smart age, HVAC controls were synonymous with Read more
It’s easy to become overwhelmed when thinking about the Internet of Things (IoT) and the complexities of smart home appliances and products. However, it’s never too late to educate yourself on the smart HVAC features and products that are sought by today’s customers.
Before the dawn of the smart age, HVAC controls were synonymous with a simple thermostat that provided comfort from a system designed to focus only on heating or cooling a space. Functionality and practicality were the most vital roles of an HVAC system. With the increased role that technology plays in our daily lives, a lot has changed.
It’s no secret that smart home technology has reshaped the way consumers interact with their homes on a day-to-day basis. Now more than ever, consumers demand the ability to change their home’s climate with the push of a button or a simple voice command – without ever touching the thermostat and from anywhere, whether sitting on a couch or away on vacation. The focus has gone from practicality to the accessibility and convenience that come with an integrated smart HVAC system. Simply put, consumers demand more from their HVAC systems.
Considering this smart home revolution, technology advancements have allowed for HVAC systems to evolve faster than can be absorbed by those in the field who must explain the functionality of the systems they are selling. How can one fully learn and understand the value of today’s smart HVAC? Dedicated time to learn about this rising tide of technology is important, but equally as helpful is to install and use similar HVAC-connected smart products within your own home. First-hand experience and determining how it can benefit your life will simplify explaining the value proposition to customers.
While the smart home revolution has markedly changed the products, services, and accessibility HVAC dealers can offer, making the sale comes back to the homeowner’s perceived financial outlay and return on investment. Knowing how to explain the value in energy savings and diagnostic capabilities throughout the life of the product can help make the case for the more costly, higher efficiency system. Similarly helping consumers understand the value of convenience from a connected systems, such as voice interactions through Alexa, or even Geofence-based set points through the app, are paramount to moving customers up to a connected system.
It also provides an avenue to become a trusted advisor for your customers while building lifelong relationships for not only yourself, but also for the brands you’re selling. While a robust consumer value proposition is key to making the initial sale, the long term value to a contractor of a connected customer is even more impactful. Using remote diagnostic capabilities, servicing dealers can better maintain the customer relationship over time, deliver more efficient service when required, and be in the best position for a proactive replacement at the end of the product lifecycle.
By being transparent and showcasing factors such as energy savings, user experience, cross-device capabilities, etc. dealers can leverage the smart home revolution to position themselves as knowledgeable and trustworthy.
Because smart home technology has reshaped the way HVAC systems are viewed within the greater home ecosystem, it should be noted that not everyone (or every home) is right for a smart HVAC installation. Consumers often do their own research before consulting dealers about whether a technologically advanced HVAC system is right for their home. In the end, an educated consumer can be the best barometer for whether upgrading to a smart HVAC system makes the most sense.
George Land, Connected Home Solutions General Manager for Ingersoll Rand Residential HVAC
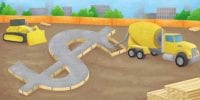
Historically, the construction industry has been one of the slowest to adopt new technology, lagging only behind agriculture in digitalization. But that’s changing as software entrepreneurs turn their attention to the needs of the deskless workforce. The ubiquity of mobile devices, cheap and powerful cloud computing, 5G, and the Internet of Things (IoT) are all Read more
Historically, the construction industry has been one of the slowest to adopt new technology, lagging only behind agriculture in digitalization. But that’s changing as software entrepreneurs turn their attention to the needs of the deskless workforce.
The ubiquity of mobile devices, cheap and powerful cloud computing, 5G, and the Internet of Things (IoT) are all making it possible to put robust technology into the hands of deskless staff, including construction workers. The venture capital industry has taken notice—funding for construction technology has seen a steady uptick since 2013.
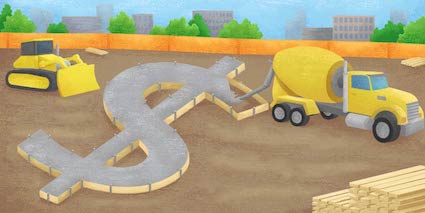
CFOs should partner with their IT teams to modernize their back-office systems, and prepare to handle a flood of data from the field as paper processes become digital. They should also figure out exactly what field data they want, what tools work best to get it, and how to integrate that data into their financial software. Deployed strategically, new tools can help construction finance teams resolve many challenges, including:
Business continuity planning
Family-owned businesses are common in the construction industry, and many thriving mid-market and even large companies are still majority-owned by founding families. Finance leaders need to create business continuity plans, whether that’s figuring out how to transfer company ownership to the next generation, establishing an ESOP (Employee Stock Option Plan), or selling or merging the company. There’s a lot of work involved in valuating the business, figuring out the best planning scenario, and helping negotiate relevant deals. Industry-specific ERPs (such as Viewpoint’s Vista) and cloud procurement platforms (such as Concur) can give finance professionals a better view into their numbers, help with planning scenarios, and standardize the purchasing process across acquired or merged companies. (Full disclosure: both companies are Nvoicepay partners).
Changing accounting standards
Revenue recognition is always top of mind in the industry. For the past several years, the Construction Financial Management Association (CFMA) has sought to ensure that the new Financial Accounting Standards Board (FASB) rules around revenue recognition are favorable—or at least not punitive—towards the construction industry. As these new rules are implemented, CFOs seek to refine their strategies for how to bill against contracts, and tie revenue to either a percentage of completion or work-in-progress schedules. Mobile technologies that expedite communication between the office and the field can also help speed the flow of information.
Risk management
Construction carries more risk, especially out on the job site, than many other industries—and insurance costs are rising. Some companies are investigating captive insurance programs, in which multiple companies pool their assets and fund their own risk by placing money under management so they don’t have to pay such exorbitant premiums.
Insurance companies have responded with more flexible products to try to help companies control their costs. CFOs need to evaluate their options—and if they want to participate in a captive insurance program, every participant needs to undergo a thorough assessment of their financial stability.
While a modern ERP system can facilitate most of that process, the assessment would also look at safety and security practices. There’s a lot of technology that can help reduce jobsite risk. Drones can monitor job sites for safety and security. Sensor-equipped wearables can alert workers to smoke or toxic chemical exposure, and geo-fencing can provide alerts when they’re entering a hazard zone. Firms can also use autonomous equipment to do work in environments that are too hazardous for human workers.
In the office, payment automation software such as Nvoicepay can mitigate payment fraud as part of an overall risk-management program.
Attracting and retaining talent
Lots of companies face growth opportunities while lacking enough employees to do the work. With unemployment at new lows, it’s been difficult to hire and keep good employees.
CFOs are working with HR—and, occasionally, external strategists—to refine their hiring, retention, and benefit strategies. Mobile training technology can help onboard unskilled workers faster, allowing companies to draw from a larger talent pool. Virtual reality technologies also offer promise for quicker training.
Improving job-cost accounting
Tablets and handheld phones let field staff capture data and send it back to their offices electronically. GPS-enabled time cards can record employee work hours and location on a mobile phone. IoT devices can measure equipment run time.
Cash management strategies
Cash management is probably the biggest challenge at any construction company, and effective work-in-progress (WIP) schedule management is critical. Key to the challenge is coordinating between the subcontractor confirming that a job is complete, project managers verifying that completion, and the accounting department billing the owner and syncing everything with the WIP schedule. This is also an area where drones and mobile apps can increase the speed and accuracy of data delivery to finance.
Finance also needs visibility, flexibility, and precision control over making and timing payments. With cloud-based payment-automation software, a project manager sitting in a truck can review a payment file, prioritize subcontractor payment schedules, and approve payments immediately, without having to return to the office to sign a stack of checks and backup documentation. Subs get paid faster and the job keeps moving.
With all the new purpose-built technology coming down the pipe, we’ll finally start to see some real movement towards digitizing the construction industry. Finance teams should prepare by enabling themselves with modern cloud systems for accounting, spend management, and payments. They need to enable the field with tools that communicate data back to the office in near real-time. Most importantly, they need to work out how to coordinate it all towards productivity gains and growth, and join the ranks of data-driven CFOs who have done the same in other industries.
Jason Krankota is VP of Construction Sales, West Region at Nvoicepay. His expertise in construction business technology spans 20 years, with 10+ years focused on corporate payments, accounts payable, and expense management solutions.
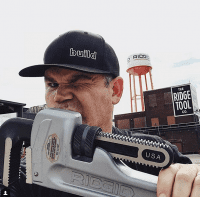
Just a couple days ago I returned from an event that has me so excited about working in the trades and what it means to be “Made in the USA”. The RIDGID Experience is only in it’s second year of existence but its clear to me that this will be an amazing annual event for Read more
Just a couple days ago I returned from an event that has me so excited about working in the trades and what it means to be “Made in the USA”. The RIDGID Experience is only in it’s second year of existence but its clear to me that this will be an amazing annual event for years to come. Here’s how it works: All across their social media channels RIDGID invites anyone who uses their tools, any and all of the RIDGID tools to show off their pride in the work they do with those tools. There’s an official entry process and some hashtagging involved but its super simple and fun. Once entered RIDGID picks the winners of the contest and those winners are treated to a total first-class experience with factory & hands-on training center tours, an inside look at new upcoming products and tools, meals, lodging, airfare, limo, professional photo shoots, a box suite at the Indians ball game and even a fishing trip on Lake Erie! Oh man, I gotta tell you it was a blast!
Of course factory tours are exciting, getting to see how our favorite tool is made and even meeting the people who make them daily leaves me with a higher level of respect for the brand and excitement for my work. That was definitely the case for me after the #RIDGIDExperience.
Unfortunately we don’t always get to take the camera’s along for every step of the tour but I’ve posted a few cool shots on our Facebook and Instagram along with some comments along the way. I’ve included a video of the final steps in the assembly of the iconic 300 below; its hard to believe that machine was ever so clean and shiny!
I’d like to thank the entire team at RIDGID and those involved who organized and pulled off a truly memorable experience for all of us “winners”. It’s clear the entire company knows and cares about who their customer is. Thank you, Eric Aune.
https://www.instagram.com/p/BlLwrqWhEO3/?taken-by=mechanicalhub