https://youtu.be/MhqypPXJtxM?si=h-FhMaoiuUVe3c4w Frozen Tundra no longer. Mechanical Hub’s Hub on the Road series takes us to Lambeau Field. Lambeau’s mechanical contracting partner, Tweet/Garot, gives us a behind-the-scenes look at Lambeau’s mechanical room, which serves as the epicenter for snowmelt, field heat, and HVAC, as well as its prefabrication facility in Wrightstown, Wis Read more
Featured Articles
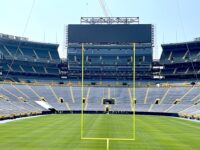
Frozen Tundra no longer. Mechanical Hub’s Hub on the Road series takes us to Lambeau Field. Lambeau’s mechanical contracting partner, Tweet/Garot, gives us a behind-the-scenes look at Lambeau’s mechanical room, which serves as the epicenter for snowmelt, field heat, and HVAC, as well as its prefabrication facility in Wrightstown, Wis.
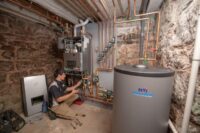
For the past several years, the Youndts, a family of five, kept their eyes open for a rural property—a new place to call home. Turns out the 10-acre property the Youndt family bought (not far from the company they own) had the ideal fixer-upper of a home on it, with a big barn and bungalow Read more
For the past several years, the Youndts, a family of five, kept their eyes open for a rural property—a new place to call home.
Turns out the 10-acre property the Youndt family bought (not far from the company they own) had the ideal fixer-upper of a home on it, with a big barn and bungalow, too.
While the pond and swimming pool caught the attention of Vince Youndt’s wife Amy and their kids Brynn, Drew, Riley and Brady, Vince was smitten by the old stone home and its 70-year-old, oil-fired boiler. He just knew he’d have a fine time dialing-in the hydronic heat.
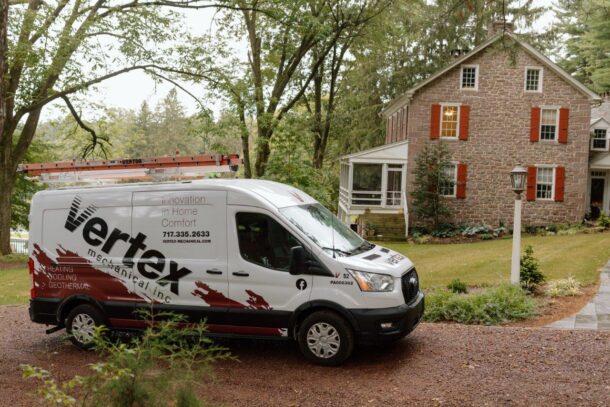
Vince Youndt (pronounced “Yunt”) is president of Vertex Mechanical, one of the best-rated HVAC contracting firms in Central Pa. Twenty-some years ago, Vince followed his father Ray into the business; Vince has been president of the company since 2002.
“When the stone home and property hit the market, we knew we had to see it,” said Youndt. It wasn’t long before the Youndts were signing settlement papers.
There were a few surprises along the way. They soon discovered the home’s 1847 date stone, its three working fireplaces, a hefty 36-inch rock foundation and the property’s 15-gallon-a-minute freshwater spring.
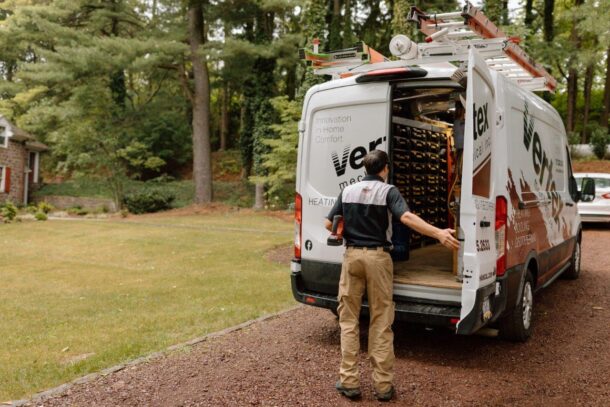
Youndt also learned that the home had only fireplace heating from 1847 to 1951. “Imagine carting hardwood to all those fireplaces several times a day and night,” he said. In ’51, the home’s first heating system was installed: the boiler that still occupied most of the lower-level mechanical room.
$2,000/month for fuel oil
The old 500 MBH behemoth steel block boiler served just one zone: the house. All 4,300 square feet of it, with three floors and no insulation, five bedrooms and 3½ baths, were all on a single zone. On, or off. In the shoulder seasons, the previous owner just opened windows to adjust the heat.
Youndt was also surprised to learn that the previous owner spent $2,000 a month to heat the place. “And that was long before fuel oil cost four dollars a gallon!” he exclaimed. “They also shelled out $600 a month through each summer season just to heat domestic water.”
A few months after buying the place and just after the 70-year-old heating system took its last gulp of fuel oil—Youndt decided to tackle the hydronic system retrofit.
Wedding venue
Just as Vince was muscling through the demolition of the 1,500-lb. boiler, another need appeared on the horizon. The Youndt’s eldest son, Andrew (“Drew”) expressed interest in having his wedding at the new homestead.
While Amy, Drew and his fiancé were scouring bridal websites and landscaping with flowers, Vince ran the business. His lunch hours were spent specifying the boiler of choice, circulators and other components, or with calls to wedding vendors.
Dreamy hydronics
Amidst the onset of preparations for the wedding, Youndt sketched and re-sketched his circulation and piping strategy for the hydronic retrofit, then finalized his wish list for the boiler replacement. Taco ECM circs and several Zone Sentry zone valves were planned, followed by an NTI boiler and indirect, and a heat pump water heater for use in the summer.
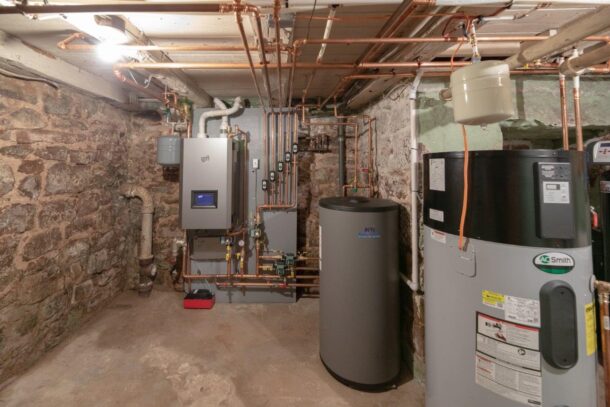
“At the time, I was having vivid dreams,” recalled Youndt. “I’d wake up at night with thoughts about the wedding—intermixed with dreams about a heavenly hydronic system! What a combination. It was all doable, and I knew that we’d have a really comfortable home. We now wake up to birds chirping, feeling that the home and property were left behind by one of those dreams.”
Good nights of rest led to moments of tough labor—including the rigors of demo work in the home’s daylight basement level. “The space downstairs seemed to triple in size when we finally got that monster boiler out’a there,” said Youndt. Vertex technicians Jared Fox, Steve Zook and John Harris will never forget the day they muscled it—all in one piece—to an awaiting truck.
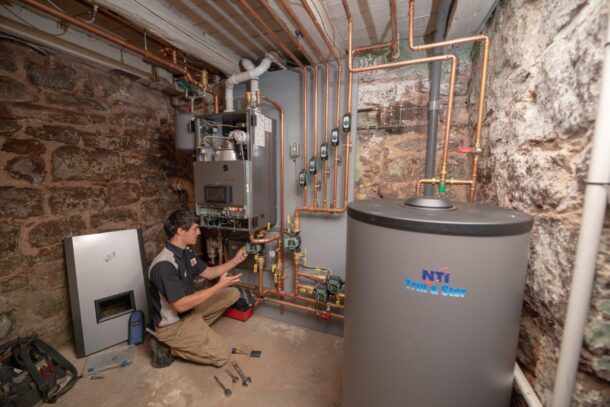
It then took Youndt most of a weekend to drill an eight-inch hole through the foundation. He quickly learned—to make way for a planned passageway for insulated supply and return lines to a wood-fired boiler (yet to be installed)—that the home’s masons, long ago, sandwiched giant granite boulders between Berks County sandstone.
“That granite was a bear!” he exclaimed.
In the fall of ’22, Eric Grant, regional business manager for Fernox USA, visited the Youndt’s home. Grant arrived with the company’s PowerFlush flushing machine, a mobile system with pump and filtration, mounted on a dolly. He also brought several gallons of Fernox hydronic fluids.
After Youndt cut into the old boiler’s iron pipes, the two soon found what sort of mess the pipes contained.
“The crud went from semi-solid gobs of oily sludge, to thick metallic pudding, then a dirt slurry, and finally semi-transparent soup,” explained Grant. That’s when Grant connected the cut pipes to the new PowerFlush. Together, he and Youndt then poured F3 cleaner into a reservoir that quickly mixed with water they ran through the flushing unit.
An hour later, the result of the chemical cleaning was made evident with crystal clear fluids returning to the PowerFlush unit. It pushes up to 30 gallons a minute to scour-out and capture all the scale and rust that can collect in a piped, hydronic system including—and especially—the heat emitters attached to it. The result: a fully-cleansed, restored system.
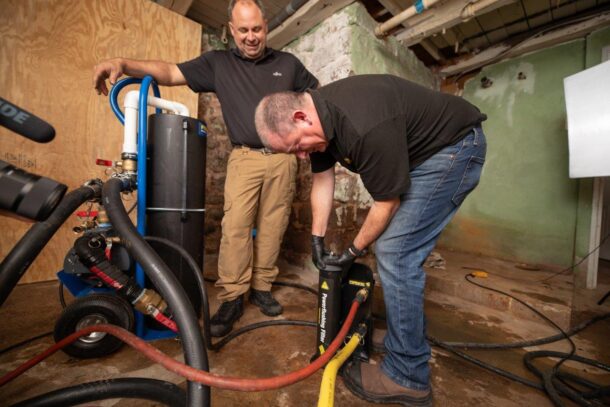
Before leaving the Youndt’s home, Grant left behind a couple of gallons of Fernox F1 Protector, a solution for later maintenance of the system—all prearranged with Youndt.
Grant then presented Youndt with the last of his purchases, a nickel-plated brass TF1 Omega+ filter to be installed when Youndt finalized installation of the new equipment.
Hydronic minimalism
Youndt recalls the days, years ago, when he wanted to fill a wall with hydronic components. “It was the ‘Mad scientist’ laboratory’ look that appealed to me back then,” he said. Lately, though, he favors what he refers to as “hydronic minimalism.”
His plan called for five heating zones in the home, and one for domestic water. Then, ultimately, the wood-fired boiler within a year or two.
One evening, he put two coats of gray paint on a single sheet of ¾-inch, pressure-treated plywood. “I wanted to hang everything on one sheet, to get the NTI boiler and Taco components as tightly together as possible, yet with plenty of room for later service work,” he said.

The plan materialized nicely. Youndt, Zook and Harris, armed with a stack of copper pipe and Viega press-fit couplings, began the process of reengineering the near-boiler piping. Now, the primary-secondary arrangement provides full-flow in the boiler loop, high- and low-temp distribution, and variable flow for secondary piping to all sources of heat distribution.
Throughout the house, there’s a mix of standing radiators, and baseboard for high-temp heat, with gentler provision of warmth for floor and ceiling radiant heat.
The NTI boiler was first in place. The 150 MBH, TFTN150 wall-hung boiler, representing a huge reduction in boiler output and physical size, and with outdoor reset, offers remarkable capability. “The boiler has the ability to control up to four zones of heat, each with its own temperature assignment,” stated Youndt. “Because of the five zones and a desire to use a sixth for domestic heating, we included NTI’s expansion board to add them; each zone now is independently managed.”
Youndt installed four Taco 0015e3 circulators. One serves as the boiler pump. Another manages the secondary heating zones. The remaining 0015e3’s serve the 50-gallon NTI indirect water heater, and future wood boiler. A Taco Zone Sentry zone valve manages circulation for each of the home’s five space-heating zones.
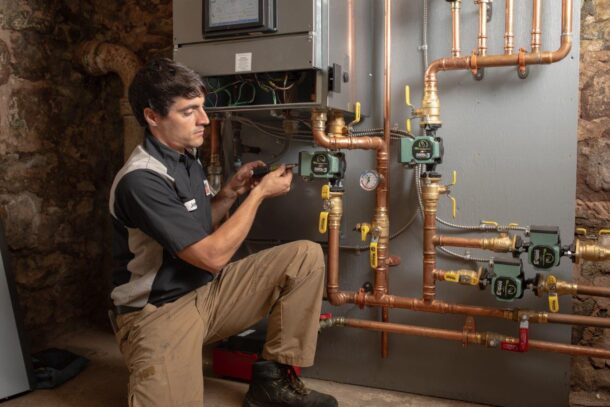
“We’re using only six circulators for the entire system, two of which are for the wood side of the system,” explained Youndt. “The NTI fires on a call from a thermostat, then looks first to see if there’s heat in the heat exchanger coming from the wood burner. If there is, it’ll be used as the first stage of heat.
“Because of the multiple low temp radiant zones in the system, the circulator for the heat exchanger offers variable speed with an outdoor reset control that governs the mixed temp coming from the heat exchanger—never to exceed the requirement,” added Youndt. “If the fire on the wood burner is out—maybe because I didn’t want to feed it, or we’re in the shoulder season—the NTI will kick in the burner utilizing the outdoor reset to determine the heat needed.”
In the summer, and with the old stone wall basement, the Youndts have a significant humidity problem. “But we don’t use a dehumidifier,” concluded Youndt. “We shut down all the other equipment while operating the heat pump water heater. It’s pretty remarkable—the water heater then uses the energy from the humidity to heat all of our hot water—all summer long. This allows us to keep the humidity in the basement at about 50 percent, and we never lack hot water, all at a cost of about $30 a month.”
A historic, and energy-efficient dream home. What could be better?
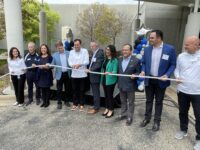
“It’s like Disney World for engineers and contractors,” said one visitor on the tour. The Mechanical Hub team made a quick visit to Apple Valley, Minn., to visit Uponor North America as the company celebrated the grand opening of its newly constructed Uponor Experience Center with a “pipe-cutting” ceremony. The team was treated to a Read more
“It’s like Disney World for engineers and contractors,” said one visitor on the tour. The Mechanical Hub team made a quick visit to Apple Valley, Minn., to visit Uponor North America as the company celebrated the grand opening of its newly constructed Uponor Experience Center with a “pipe-cutting” ceremony.
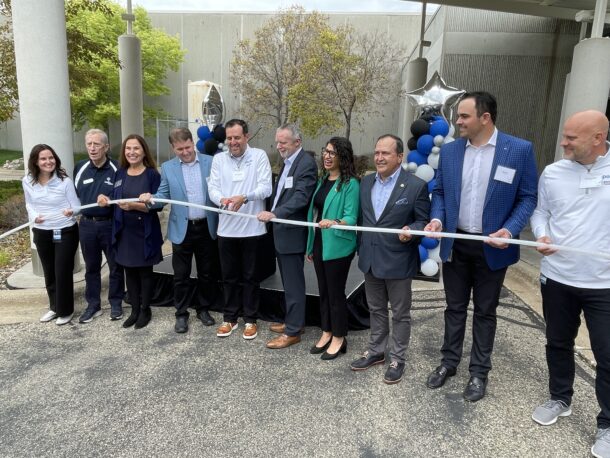
Andres Caballero (fifth from left) performs the pipe cutting for the new Uponor Experience Center.
The team was treated to a behind-the-scenes tour of the new 4,500-sq.-ft. customer experience center, which features hands-on displays, full-scale residential and commercial training areas, and cutting-edge innovation showcases, and a place to bring MEP students from the area to get a taste of the trades. The new Uponor Experience Center is a flexible education and discovery space designed to advance the technical skills of current and potential customers. In addition, it will help foster innovation within the plumbing and HVAC industry and provide an immersive experience for employees and visitors alike.
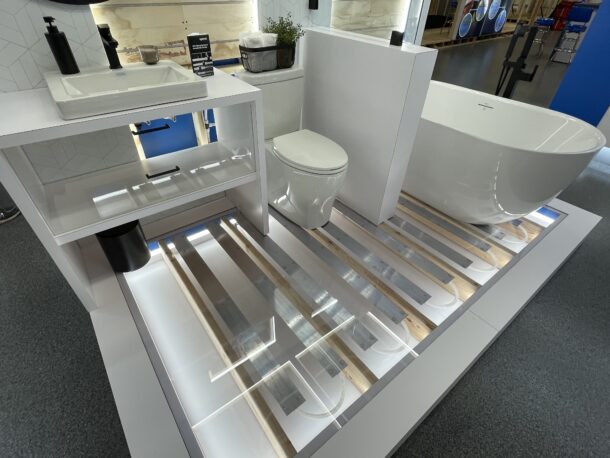
Some displays mimicked true applications.
The new Uponor Experience Center occupies the company’s previous customer training area, which was originally built in 2000 and renovated in 2010. It is at the center of the North American headquarters campus, surrounded by corporate offices, an R&D facility, and manufacturing space.
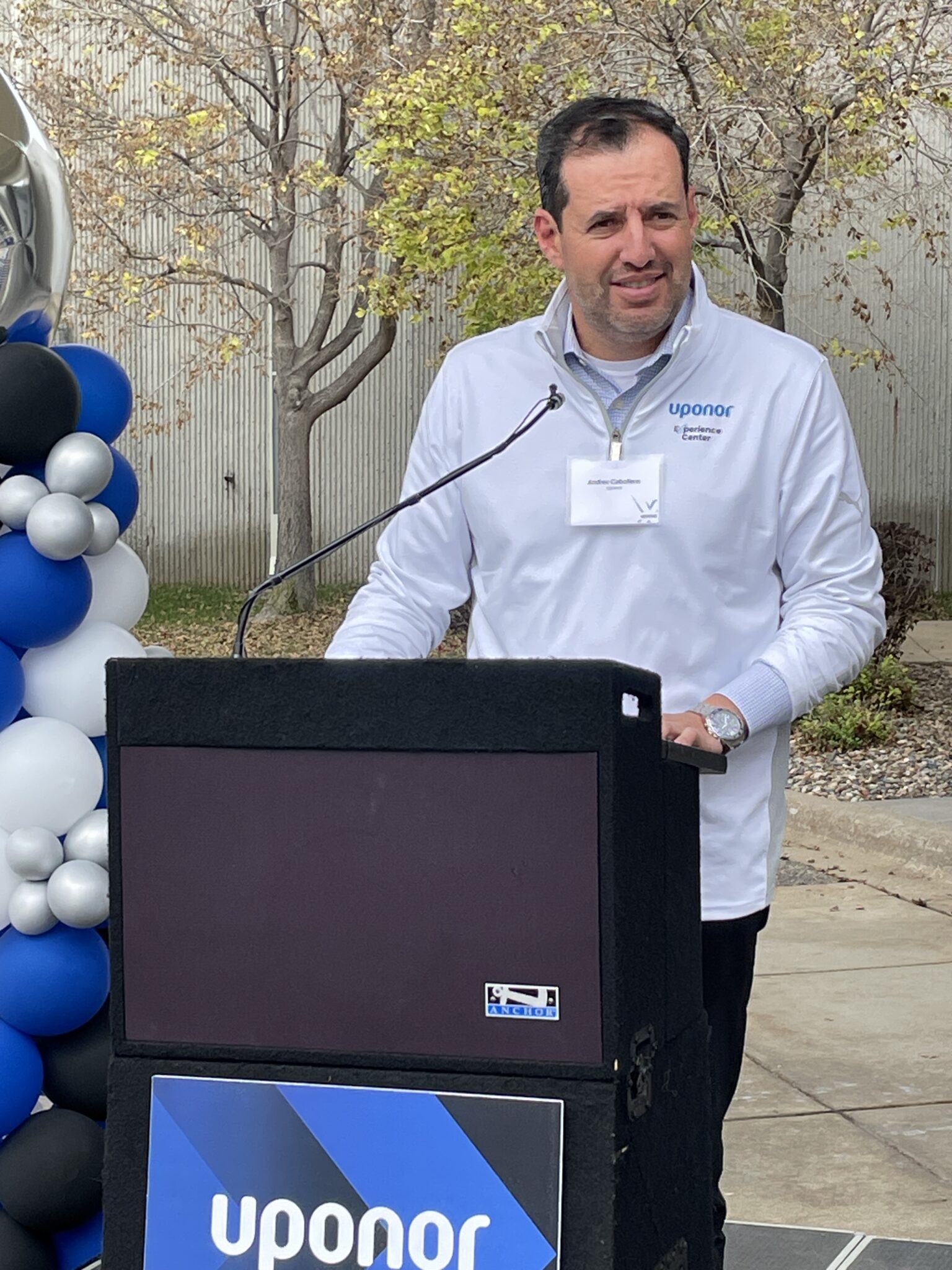
Andres Caballero thanks his staff for all of the hard work and dedication that went into planning and constructing the experience center.
“The opening of our new Uponor Experience Center signifies the importance we place on keeping the needs of our customers, employees, and key stakeholders top of mind as we continue our mission of becoming the global leader in sustainable water and energy solutions,” says Uponor North America President Andres Caballero. “The ‘X’, as our employees have begun to call it, is a culmination of our rich history and decades of innovation coming together to generate awareness and create enthusiasm for moving water more efficiently, effectively, and sustainably.”
With original concepts beginning back in 2020, the Uponor Experience Center was several years in the making. The thoughtful design, which takes into consideration the company’s rich Finnish roots, resulted from many months of internal team collaboration, as well as feedback from customers, partners, and industry influencers.
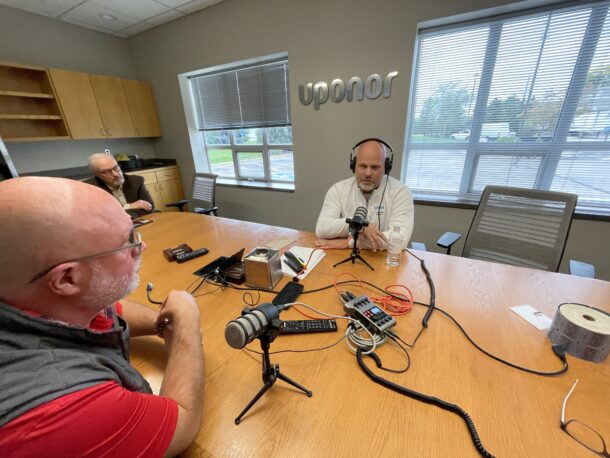
Mechanical Hub took the opportunity to record parts of the Appetite for Construction podcast with Des Clancy, director of training, Uponor, and the “architect” for the new center.
As guests move through the front doors toward the back of the space, they first experience displays depicting who Uponor is as a company along with the customers served and the unique value provided to key audiences and the industry.
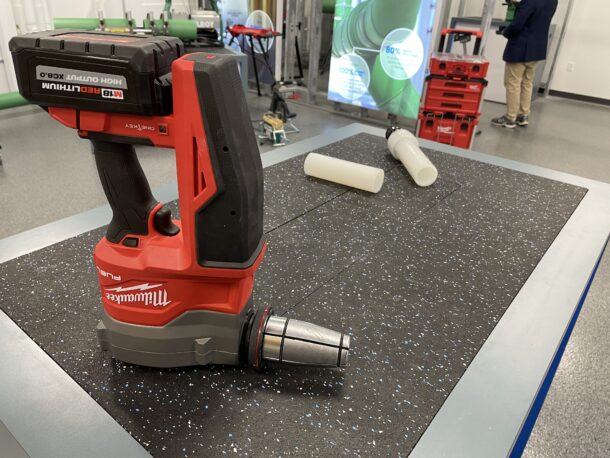
Experience center visitors will get the full hands-on treatment as seen here with one of its gracious partners Milwaukee Tool and its PEX Expander.
Then, there are product showcases and interactive displays for plumbing, fire safety, radiant heating/cooling, hydronic piping, and pre-insulated piping system solutions for residential and commercial markets. Finally, there is an oversized training area, featuring both wood and steel structures, where professionals will learn proper hands-on installation techniques as well as how Uponor’s emphasis on problem-solving and productivity delivers results for their businesses.
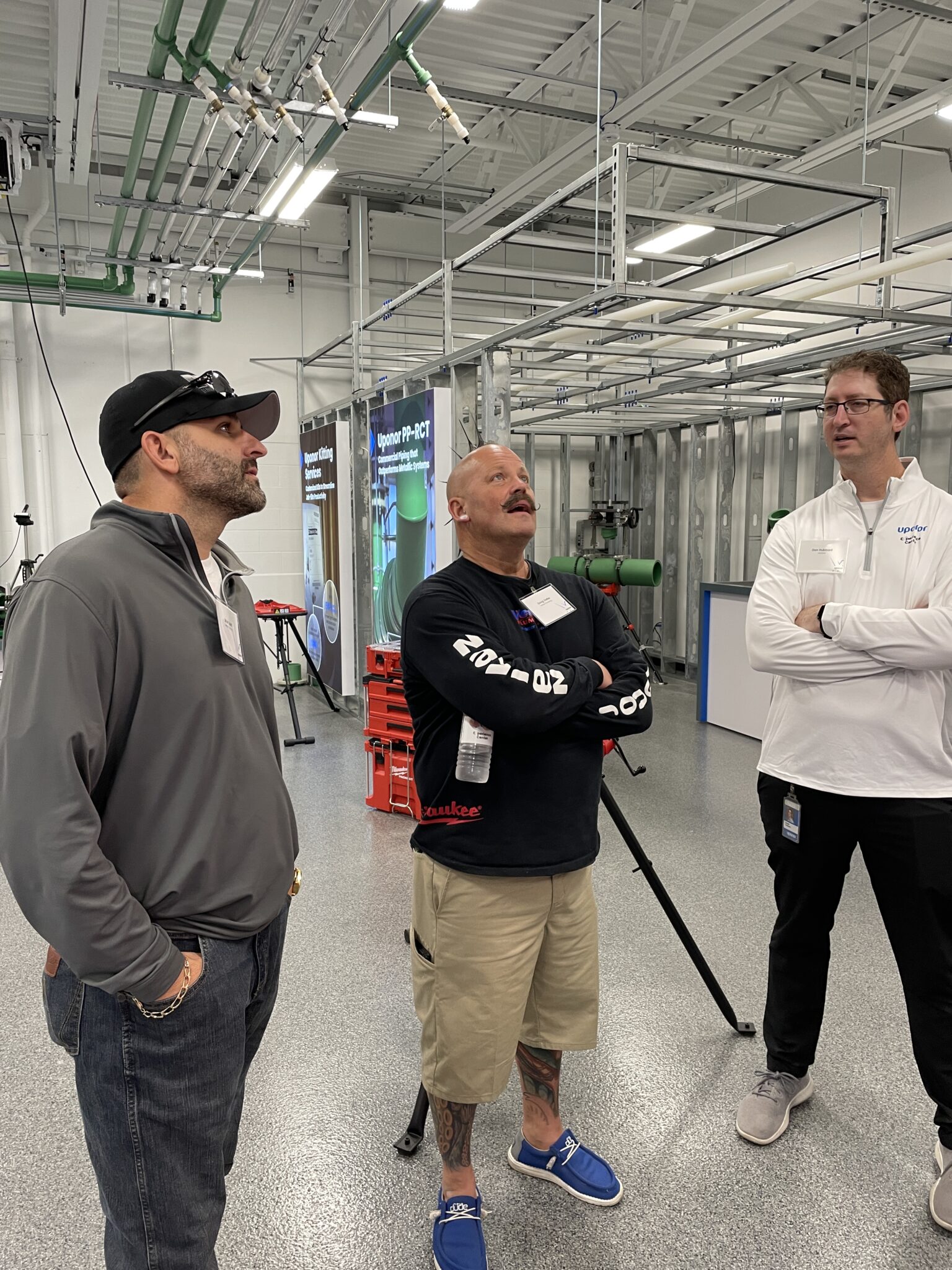
Doug Vetter, center, and Brian Spjut, left, from Vetter Plumbing, came all the way from Seattle to get a first glimpse of the space. (Pictured right is Uponor’s Dan Hubbard.)
“We wanted the Uponor Experience Center to extend beyond simply training customers on our products and systems,” says Vice President of Sales Matt Bahr. “As a result, we’ve created a holistic experience that spans a broad spectrum of who we are as a company, showcasing the depth and breadth of our product portfolio and sustainable solutions as well as providing access to the best trainers in the industry.”
With the focus not only on customers but also employees and those in the community, Director of Training Des Clancy says the planning team was very thoughtful about creating an elevated experience for everyone.
“At any given time, we will have contractors, builders, engineers, owners, students, employees, civic leaders, and other guests coming through the doors,” he says. “From tours and training, to onboarding and education sessions, the Uponor Experience Center offers something for everyone, and we are proud to showcase all we are offering to the industry and our community.”

Mechanical Hub’s John Mesenbrink (l) and Tim Ward (r) complete the “Uponor sandwich” as they also toured Uponor’s Distribution Center in Lakeville, Minn., with tour guide and director of logistics and warehousing, Nate McIntosh.
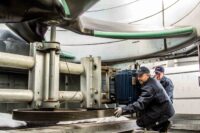
I’ve heard more than a few stories about catastrophic system failures—most of which were easily avoidable, given their forensic trail to negligent lack of maintenance. One that comes to mind is a catastrophic fan failure at a Midwestern manufacturing plant, several years ago. Naturally, this occurred on a Friday afternoon grinding the weekend process to Read more
I’ve heard more than a few stories about catastrophic system failures—most of which were easily avoidable, given their forensic trail to negligent lack of maintenance.
One that comes to mind is a catastrophic fan failure at a Midwestern manufacturing plant, several years ago. Naturally, this occurred on a Friday afternoon grinding the weekend process to a halt and incurring labor to be billed out at weekend rates.
A facility engineer noticed that water temperatures in the 1,200-ton tower were not decreasing sufficiently—yet there were no alarms. A maintenance tech was sent to investigate the tower and found that the fan assembly had blown apart. The fan screens, cylinder, mechanical supports, and other smaller components were damaged as well.
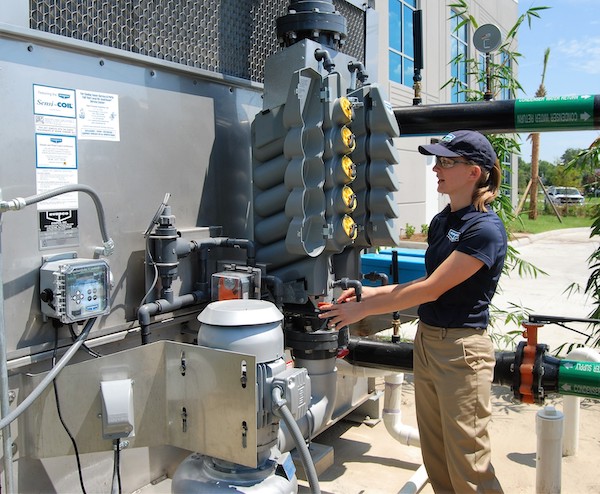
Water treatment of cooling towers and condenser water system is a critical component to ensure a long life and proper system operation.
Closer inspection revealed that the fan shaft had significant play due to worn out bearings, causing the fan blades to repeatedly hit the cylinder. Lacking vibration controls, the entire assembly eventually blew apart, destroying most of the fan section in the process.
Had the tower been subject to routine inspection and maintenance, this very expensive problem—with significant down time consequences—could have been avoided. Not counting lost production, the owner spent more than $20,000 in parts and service alone due to inadequate maintenance and monitoring of fan bearings.
Evaporative cooling equipment, like any mechanical unit of machinery, requires preventive maintenance to maximize its utility.
Simple maintenance procedures provide enormous benefit to a wide range of connected systems and equipment, manufacturing processes, and occupants too. Benefits include the reduction of operating costs, downtime and capital expenses, and improved system efficiency; even equipment lifespan.
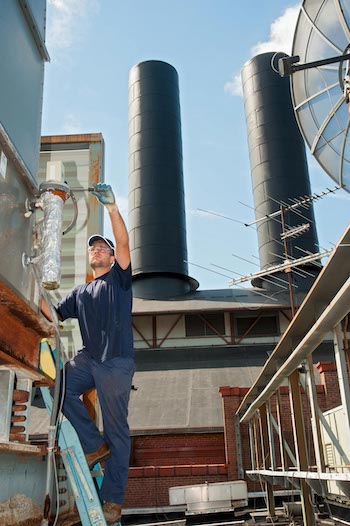
Externally mounted water level controls are a great way to provide accurate operating levels within the cold water basin. Don’t forget to heat-trace and insulate them to guard against freezing ambient temperatures.
Central to each of these benefits is the prevention of critical or catastrophic failures. Often, repair costs pale in comparison to costs that stem from the down-time loss of production.
Most failures of evaporative cooling equipment involve moving components and can typically be separated into three specific parts or systems:
- the fan motor,
- the fan, and
- drives, or power transmission – bearings, sheaves, and belts.
Evaporative cooling manufacturers provide resources to assist facility personnel with maintaining these components, such as the equipment operations and maintenance (O&M) instructions, and maintenance schedules. These tools often focus on the basic level of maintenance required for proper operation.
There are, however, a range of innovative processes and products designed to provide a greater level of security for the owner or facility manager.
Heart of the system
The fan motor is the heart of the evaporative cooling equipment. Like the human heart, it requires extra care for the well-being of the equipment.
Control sequencing is an appropriate starting point.
“When applied to across-the-line starts as opposed to the application of variable frequency drive (VFD), it’s critical to limit start-stop sequences to no more than six per hour,” advises Scott P. Buckley, Senior Manager, North America Parts, EVAPCO, Inc.
Buckley reminds us that each motor start is associated with a spike in voltage, referred to as in-rush current, which increases the motor operating temperature and can lead to motor winding insulation failure. Limiting the occurrence of these protects the motor.
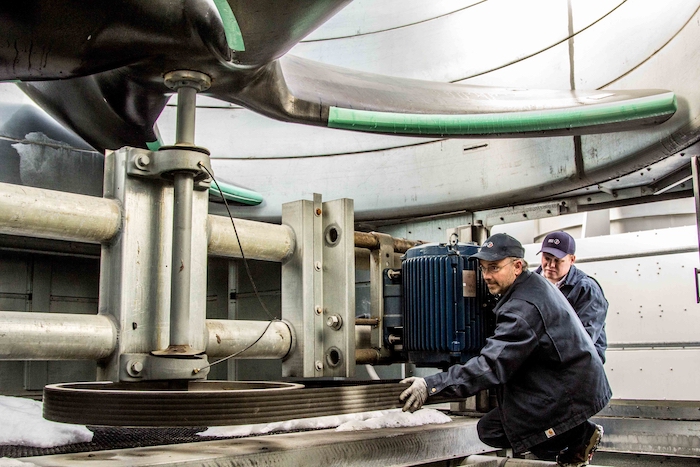
Increasing the temperature control deadband and/or lowering the setpoint are two ways to reduce fan cycling frequency.
VFDs are the preferred method for control of fan motors. However, there are still some concerns, chief among which is the issue of stray currents.
“VFDs simulate a sine wave via on-off switching of current,” said Buckley. “By-products of this are stray currents that often ground themselves at the motor bearings. Failure to address this will result in premature motor failure. “
A simple and cost-effective solution is available in the form of shaft grounding rings. They operate much like a lightning rod and provide a ground for the stray currents outside of the motor housing.
Moisture + motors
Moisture intrusion is a common mode of failure and can be a very serious challenge.
Yet, evaporative cooling equipment must operate, by necessity, in a humid environment. That’s why fan motors are designed to function properly with some influence by moisture. Consequently, they’re susceptible to moisture contamination, often from condensation.
A key remedy is to ensure that condensate drains are positioned at the lowest point of the motor mounting or enclosure.
The term “totally enclosed” for motors often leads to a false sense of security. The type of motor used for these systems is designed to prevent required cooling air from flowing over the motor windings, but is not airtight.
Another approach, advises Buckley, is proactive, greatly limiting the possibility of moisture contamination: installation of space heaters within the motor housing. Space heaters are wired to the motor control panel so that they are energized when the motor shuts off, and de-energized when the motor turns on. This helps to maintain a consistent internal temperature, preventing condensation.
Fans—more than meets the eye
While fans are much less complex than a motor, their maintenance is no less critical. Fan failures are chiefly associated with vibration, balance, or structural impairments. As a result, routine inspection and monitoring are required.
Vibration cut-out switches—designed to protect the fan in the event of excessive vibration—have been a fairly reliable “insurance policy” against fan failures. However, more aggressive approaches will improve equipment dependability.
After all, by the time a fan is vibrating excessively, damage is already occurring, or has occurred, to components such as fan bearings.
A better, smarter approach to assuring fan health comes with the installation of vibration sensors which generate control signals proportional to vibration levels. These devices allow constant monitoring of the drive system and can pinpoint degradation of components long before a failure occurs.
Another key facet of fan maintenance is balancing of the fan. Proper balance is critical to unit operation and performance. Fan balancing can be either static or dynamic. Static balancing is performed when the fan is at rest. Fan suppliers routinely balance fans, statically, following manufacture.
Dynamic balancing, however, is performed while the fan is in motion. Dynamic balance values often differ from static balance values because the fan is subjected to the influence of moving components such as the sheaves and belts.
Any time the drive system is disrupted, the fan system should be dynamically balanced. Disruptions take the form of component replacements—such as a fan, sheave, shaft, or a set of bearings. This will ensure proper operation and increased reliability and longevity.
“Fan blades and fan surfaces should be routinely inspected,” commented Buckley. “Corrosion, cracks, gouges and sometimes ice formation, may contribute to fan imbalance, leading to premature or catastrophic fan failure.”
Any corroded surfaces should be sanded and treated with an industrial grade rust inhibitor. Cracks and gouges often result from blade contact with foreign objects. The objects do not require a great deal of size or density given that fans often rotate upwards of 400 rpm or more. Problems like these should be reported to a service company and followed up with a complete unit inspection.
Drive components
In between the fan motor and the fan are the drive components. Whether gear driven or belt driven, proper alignment is critical. Gear drives require a coupling between the motor and gear. These can be close couplings or a floating shaft.
Not only can misalignment contribute to a premature failure, but the couplings themselves are under heavy and frequent torque conditions. Because of this, the hardware and flex elements are designed to absorb torque and will usually be the first to show signs of wear.
Regular inspection and timely replacement of these components involve considerably less cost and downtime than a full gear drive or fan failure.
Alignment of belt driven systems is just as important, although part replacement of belt driven systems are often less costly and require less down-time than gear driven systems.
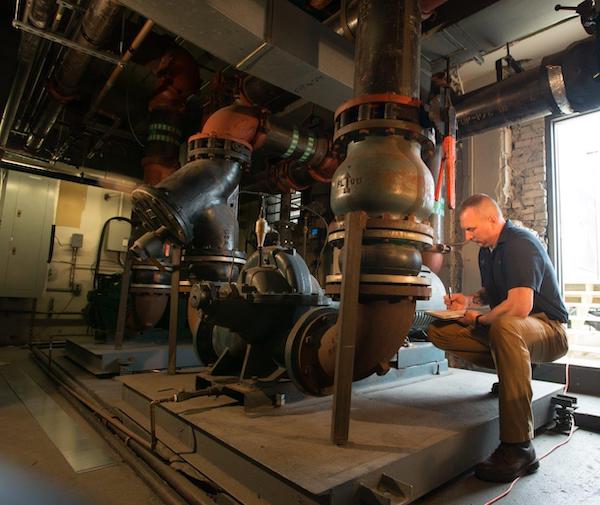
Balancing condenser water pump flow rates will ensure optimal cooling tower heat transfer.
Sheave alignment should result in a four-point contact of a straight edge or laser tool, with a maximum deviation of 1/16-inch. The maximum mid-point deflection of the belt should be one-half inch.
Buckley and I know that fan shaft bearings are often the most frequently replaced part of evaporative cooling equipment. Replacements can be reduced with increased care and attention to lubrication.
For starters, use only greases approved by equipment manufacturers. All grease formulations contain some form of detergent, and it’s these chemicals that don’t play well together when mixed. Consistency plays an important role. If new grease is introduced, it’s critical that the entire system—including bearings and lube lines—be fully purged of the old lubricant.
Lubrication schedules are typically provided by equipment manufacturers; these are based on long-term service data—not to be ignored.
Just as important to the schedule is the manner by which bearings are re-greased. Grease is often applied too vigorously—causing bearing seals to blow out—sure to cause premature failure.
Automatic bearing greasers can be a real advantage. Many are designed to provide a timed release of lubrication. The discharge is performed under low pressure to prevent damage to bearing seals. Despite these advantages, automatic bearing greasers should not be considered a substitute for visual inspections.
Systematic and thorough attention to the fan and motor assemblies is essential to avoid the unexpected interruption of service.
Tyler Lee is Senior VP Sales & Marketing, Chesapeake Systems, LLC, a manufacturer’s rep, and service firm with offices in Hanover, Md. and King of Prussia, Pa.
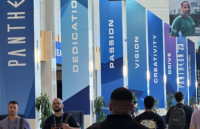
Solutions will Equip Trade Contractors with Powerful Tools to Run and Grow Their Businesses Mechanical Hub was onsite last week at ServiceTitan Pantheon 2023, its annual user conference, and if there was ever any doubt or fear that artificial intelligence (AI) was coming to the trades, Pantheon 2023 put those thoughts to rest. More than Read more
Solutions will Equip Trade Contractors with Powerful Tools to Run and Grow Their Businesses
Mechanical Hub was onsite last week at ServiceTitan Pantheon 2023, its annual user conference, and if there was ever any doubt or fear that artificial intelligence (AI) was coming to the trades, Pantheon 2023 put those thoughts to rest.
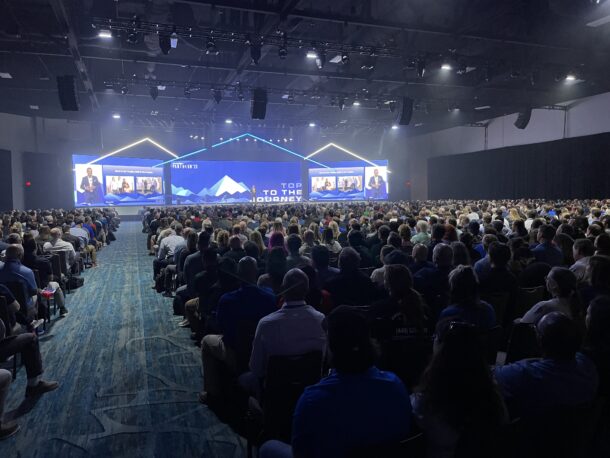
More than 1,500 service contractors, ServiceTitan team members and exhibiting partners spent three days exploring the “Journey to the Top” theme, which included more than 50 sessions to help contractors stay on track with next-level training, tools, and insights. In addition to the sessions, attendees enjoyed networking events, product plaza exhibit space, keynotes from industry VIPs and a closing fireside chat with tennis great Venus Williams.
“Over the past year, the world has seen a dramatic acceleration in AI advancements and ServiceTitan is making sure that the trades industry will be at the forefront of this technological revolution,” said Vahe Kuzoyan, president and co-founder at ServiceTitan.
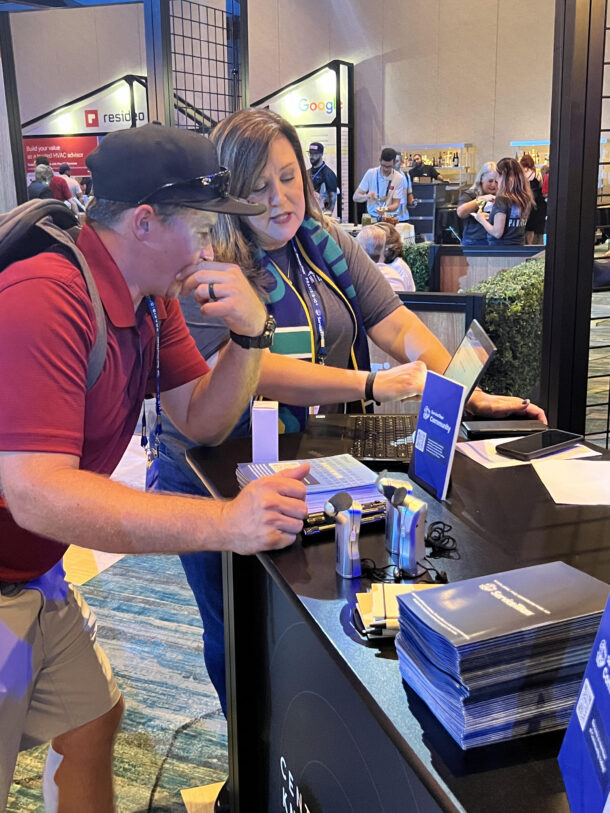
To ensure Kuzoyan’s statement rang true, ServiceTitan introduced a suite of new products to empower residential and commercial contractors with groundbreaking technology to supercharge their businesses. Powered by Titan Intelligence, the company’s own AI solution purpose-built for the trades, these new cutting-edge solutions allow its customers to automate, predict, and optimize across their entire business.
Several of the new AI-powered products introduced at Pantheon include:
- Ads Optimizer maximizes the ROI of every dollar spent on an advertising campaign by educating Google Ads to focus on potential customers who are actively looking for service providers while avoiding users who aren’t. The feature also predicts which zip codes will have the most demand and automatically prioritizes ads for those specific locations.
- Dispatch Pro runs thousands of scenarios to get the right technician to the right job, allowing dispatchers to invest more time delivering a superior customer experience. Dispatch Pro’s algorithm also finds the best technician for every job based on the technician’s specific set of skills, recent sales performance, proximity to the job, and more – all to maximize profit.
- Integrated Financing gives contractors the tools they need to grow their business and protect their margins. The feature allows ServiceTitan’s customers to strategically control plans from multiple preferred financing providers on a single job, improving their customers’ approval rates. It also gives technicians confidence in offering plans that will ultimately win more high-value jobs easily.
- Second Chance Leads automatically detects unbooked phone calls from potential customers within minutes of the call ending, and specifically flags missed calls that the algorithm believes can be saved. The tool works in the background to identify missed opportunities, so ServiceTitan customers don’t have to.
“At ServiceTitan, AI means ‘Automated ROI,’” said Ara Mahdessian, co-founder and CEO of ServiceTitan. “We want to automate all the inefficient processes that steal precious hours away from contractors and their teams every single day, and at the same time provide actionable insights and powerful features to meaningfully grow their revenue. Our AI-powered tools allow our customers to focus their time and energy on what they’re best at, and most passionate about — solving problems for their customers and delivering the best quality service.”
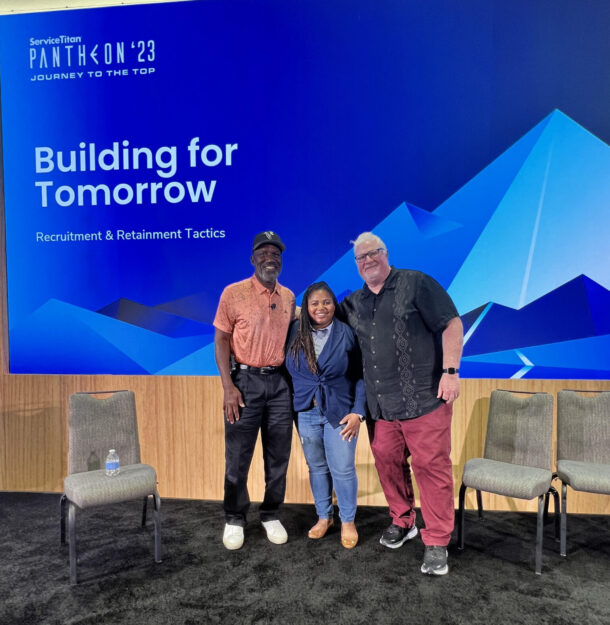
While the session and networking was top-notch, Mechanical Hub was also selected as a session leader. They worked with Pfister Faucets and American Plumber Stories to present, “Building for Tomorrow: Recruiting & Retainment Tactics.” The session highlighted Universal Plumbing’s Larry Jones, CEO and Shalanda Morris, Business Manager, and discussed their best practices finding, training and retaining employees. In addition, we looked for answers to address major roadblocks in recruitment, and shared some creative strategies to help contractors find their next rock star employee. A packed crowd of contractors also got to watch season four, episode one of American Plumber Stories.
Mike Prencavage Jr., owner of The Family Plumber, Los Alamitos, Calif., shared, “I attend pantheon for inspiration and motivation to grow my company. Being surrounded by great leaders and business owners in the industry does so much to rejuvenate my drive to succeed. AI will help streamline not only front office processes but also front line sales interactions. It’s important to never loose sight of the ‘customer experience’ and I feel that AI will only help to improve that high level of service. Servicetitans projected plans to incorporate these AI features are only going to help the industry and better the homeowners experience overall.”
For those that don’t use ServiceTitan and have never attened a Pantheon, it’s a learning and networking event for contractors of all sizes and experience in the home and commercial service industry. While most attendees are business owners, managers, IT professionals, or members of the finance team, all trades professionals are invited and encouraged to attend.
ServiceTitan was founded in 2007, and helps residential contractors manage a range of tasks including booking jobs, dispatching technicians, processing payments and overseeing marketing campaigns.