It happened again. Another 5-alarm fire at an apartment complex leaving nearly 450 people without a roof over their heads. This is a direct quote from the news report:
“Nassau County Assistant Chief Fire Marshal Michael Uttaro says firefighters found plumbers tools in the building in a vacant apartment where the fire is believed to have started on the second floor. He said the fire may have been started by plumbers using torches.”
Torches are expensive.
Thanks to our friend Robert O’Brien for bringing this to our attention, you can see the initial report here: Workers likely caused 5-alarm blaze in Hempstead apartment building: Fire Marshal
This headline flashed across my news feed earlier in the month: Fire in three-story Plainfield home caused by plumber sweating pipes, officials say. You can read the article here but, the title pretty much says it all.
Again, I can’t help but think that torches are expensive. Especially when you start comparing them to a $1500 press tool and all the headline they’ve caused in the last fifteen years since we first started using them.
Let it be known that I am not making light of the fact that people have lost their homes or may have been hurt in fires caused by an accidental fire. I’m just pointing out that, in those situations, and if soldering were not the only method/option to complete the job, that pressing likely would not have burned down those properties.
Having shared this opinion to the masses, I have no doubt had the opportunity to talk with and hear from those with the opposite opinion when it comes to pressing piping systems. The majority of those in opposition share their feelings of how it “takes no skill to pull a trigger” and “soldering is a skill and without it all craftsmanship is lost on the job.” Really?! No skill is needed and all craftsmanship is lost if I don’t use my torch and subject an 80-year-old house to an untimely demise?
I’ve tried taking many different approaches in response to skilled tradespersons telling me I “must have no pride in my work” for choosing to forgo the flame and instead pull a trigger. I’ve tried explaining how the higher cost copper press fittings are practically a non-factor when comparing the time saved and higher profits in my pocket.
I’ve explained how, after 10 years of teaching apprenticeship classes that, I still teach new apprentices how to properly assemble and solder copper tubing and fittings because we will always have the need for the skill. None of this seems to make my side of the argument any stronger, considering every time I put the discussion out there again there seems to be plenty of opposition coming at me with the same flat arguments about skill and expense.
So, having explained why I chose to be more profitable and the safety factor of press systems over flame, I guess I’d like to touch on the skill and craftsmanship topic once more.
To those contractors, journeyman, apprentices, onlookers and armchair quarterbacks who insist the downfall and final nail in the coffin of true skilled pipe trades workers will be the press fitting system I have a few questions for you:
Do you think it takes a skill no mere-mortal can obtain to solder a copper joint properly?
The importance you place on this exact act of everyday job performance is so high that I began to think I might possess some sort of super human strength and power. I guess anyone could watch a 3.5 minute YouTube video on the techniques and steps of proper joint assembly, but would anyone be able to pull it off on the job? Not according to those who think pressing be damned.
Staying one step ahead and increasing efficiency because of modern technology says more to one’s character in today’s business world than holding onto to the myth that knowing how to solder or, even knowing how to solder well is a skill only beholden by the greatest craftsman and women ever to set foot on the jobsite.
Finally, the argument for the lack of craftsmanship on all jobs that have not been soldered on. We share photos and articles of jobsites built by world-class craftsmen and women. These jobs almost always contain piping systems employing the most modern of materials and joining techniques. The days of welding carbon steel pipe for commercial distribution headers are all but entirely eliminated and have been replaced with PP-R heat fusion and copper/steel press systems.
Does anyone arguing the lack of craftsmanship think for a second that investors and owners would throw millions of dollars of capital investments into a building contain the least amount of skill level and pride needed to open the doors and commence business? No, they wouldn’t even consider that. Instead they are demanding the best of the best in materials and installation. Even they know that old technology like soldering and threading and welding just won’t hold a candle to the industry’s modern materials replacements.
I just cannot agree with the opposition on this subject. Not when my competition is ready to push me out of the way at their earliest convenience if I were to take longer on my jobs. The market tends to weed out those who are not willing to change; those persons not willing to accept the advancement of plumbing and heating systems. I think it’s time to put this argument to rest. I’ve said my piece, you’ve said yours. The industry has moved in the direction of change, so it’s either time to get on board or get out of the way.
/rant
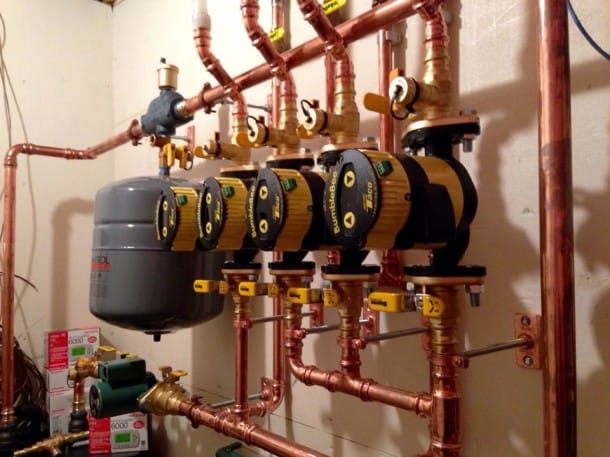
We install entire boiler and plumbing systems without ever using a torch. Of course this is nothing new to the majority of plumbing and heating contractors who are staying ahead of their competition.
Join the conversation: