Beginning a contracting business is an endeavor that has the potential to be both exciting and profitable; nevertheless, it does take careful preparation and thought. In addition to selecting the appropriate location, other important considerations include locating dependable suppliers and recruiting experienced employees. It is essential to have a solid understanding of the costs involved Read more
Whats New
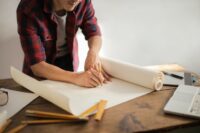
Beginning a contracting business is an endeavor that has the potential to be both exciting and profitable; nevertheless, it does take careful preparation and thought. In addition to selecting the appropriate location, other important considerations include locating dependable suppliers and recruiting experienced employees. It is essential to have a solid understanding of the costs involved in launching and successfully operating a contracting firm. There are many other fees to consider, ranging from marketing and licensing to equipment and insurance. When you first get started in the contracting business, there are a lot of expenses that you’ll need to consider, and this article will go over some of the most crucial ones.

Start-Up Costs for a Contracting Business
Equipment
When first getting started in the contracting business, one of the major costs is purchasing necessary tools. Depending on the kind of independent job you’ll perform as a contractor, you may need a wide array of equipment, machines, and vehicles. A landscape contractor, for instance, may need lawnmowers, edgers, and trimmers, but a general contractor may require power tools, scaffolding, and heavy equipment. Researching the apparatus you will need and adjusting your budget appropriately is essential.
Insurance
When beginning a business, contractors should include a budget for insurance costs. It is common practice for laws to mandate that contractors carry liability and workers’ landscaping insurance. Property damage and bodily harm sustained due to the contractor’s work are covered by liability insurance. If an employee has an injury, workers’ compensation insurance will help reimburse them for any medical costs and missed pay. Depending on the specifics of their line of work, contractors may want additional forms of insurance other than what’s required by law.
Licensing and Permits
Obtaining the proper licenses and permissions is an important stage in beginning a contracting business, and this phase is one of the fundamental processes. To lawfully run a contracting firm, you must comply with all applicable state and municipal regulations. In most cases, this requires securing a contractor’s license, a company license, and, if necessary, specific permissions. Since every state and local jurisdiction has its standards, it is essential to research these requirements early on in the process.
To receive some licenses, you may also need to demonstrate that you fulfill particular educational or experience criteria. It is essential to create a budget that accounts for the costs associated with obtaining these licenses and permissions since doing so may include payment of fees and a protracted application procedure. Your company will be operating lawfully if you comply with these rules, which will also protect you from any possible penalties or legal action that may be taken against you.
Marketing and Advertising
Marketing and advertising promotion are necessary for a contracting business to be successful. To expand your company, you must establish a solid brand presence and market your services to prospective customers. This may be accomplished via a variety of methods, including the development of a website, the production of brochures and business cards, and the placement of advertisements in regional newspapers or online directories. You may exhibit your work and engage with prospective clients via social media channels like Facebook, Instagram, and LinkedIn. Reaching your ideal customers and expanding your company are both possible outcomes of a marketing and advertising strategy that has been well-developed. It is essential to prepare a spending plan for these costs and to keep close track of your return on investment.
Overhead Expenses
Overhead costs may soon become a significant portion of any contracting business’s revenue. Rent, utilities, office supplies, and accounting or legal fees are all examples of overhead costs in addition to licensing, insurance, marketing, and advertising. You can better plan and manage your money with a precise budget that accounts for all of these costs. Renting office space or a warehouse might significantly increase your fixed expenses. It’s important to maintain a record of your money going out and coming in so that you may change your spending habits and financial plan as needed. Doing so will help your contracting firm succeed financially and endure into the future.
Conclusion
Breaking into the world of contracting may be a successful and satisfying endeavor, but it is essential to have a solid understanding of the costs involved—everything from the tools and insurance to licenses and advertising. By carrying out in-depth research on these costs and developing a comprehensive spending plan, you can ensure that the various expenses bound to arise are accounted for. With the insight provided in this article, you’ll be much better equipped to take control of your finances and build a successful independent contracting business.
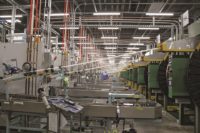
If you worry that your manufacturing process isn’t the best that it can be then you have nothing to worry about. It has never been easier for you to make some improvements, and if you follow this guide, you should find that you can save money while making your whole process more efficient. Avoid Wasting Read more
If you worry that your manufacturing process isn’t the best that it can be then you have nothing to worry about. It has never been easier for you to make some improvements, and if you follow this guide, you should find that you can save money while making your whole process more efficient.
Avoid Wasting Material
Waste is a very broad term, and it can refer to energy, materials or even man-hours. One of the biggest kinds of waste however would be material. If you want to stop your company from wasting a lot of material, then one thing you need to do is focus on the design. You need to use less material from the get-go. Designing parts using value engineering or DFM can really improve your yield, and this can work in your favour. Make sure that you also recycle scraps, and any factory returns that you have. Even if you are not able to use the recycled material yourself, it is often possible for you to sell it to someone who can. Essentially, you can turn waste into profit. If you aren’t sure where you are wasting materials, then you need to look over your manufacturing process. Using software is also very useful, so keep that in mind. If you want to get access to great software, then be sure to check out Digital Twins for Manufacturing.
Improve Training
It’s safe to say that right now, there is no substitute for real-world training. Make sure that you take stock in your team and that you train them across various processes. If you can do this, then you are bound to see an improvement. If everyone on the factory floor has a very good idea of the process, from start to finish then they will know how their roles support the bigger picture.
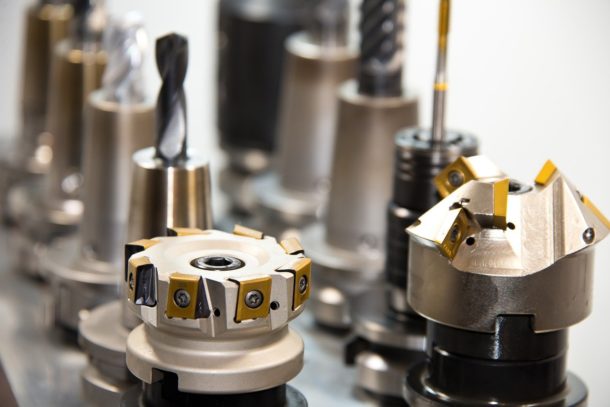
Quantify Everything
Assign a point, or even value to every single part of your manufacturing process. Sure, it’s easy to document material costs, but you also need to take into account man hours, equipment wear-and-tear and even obsolescence. If you can assign a number to every aspect of the process then you will be able to make it way easier on yourself, and you will also be able to see which areas require your immediate attention.
Be Organized
If you want your workspace to be efficient, then you have to be organized. Take a look around your factory floor right now. Do you see any hand tools? Are they easy to locate? Do you have waste that is piling up everywhere? Everything in your business should have a home, and it should be obvious to your team where that home is. If it isn’t then this is a major sign that something has to change. If you do not put in the work to make a change now then this could be draining your business time, energy and resources, so make sure that you are mindful of that where possible.
Standardize your Work
It’s safe to say that your team will have their own approach to things, but when it comes to the world of manufacturing, there isn’t a whole lot of room for being individual. Even simple tasks have to be somewhat standardized so that you can maximise efficiency where possible. If you do this then you will soon find that you can reduce downtime and you can also rocket the general product quality you are putting out.
Cellular Manufacturing
Another thing you can do is try and adopt the process of cellular manufacturing. This is a very useful method and to adopt it, you simply need to group any similar processes together. This methodology involves you dividing a workspace and then splitting it up into cells. You will need to assign each one a set of tasks. The employees and the machines that work within that realm will be capable of carrying out a vast range of jobs, but ultimately, they can be allowed to focus on just one responsibility if required. If you can do this then you will be able to facilitate tasks such as maintenance or re-calibration, purely because everyone has a great deal of understanding regarding their role and how they fit into your company operation.
So, as you can see, it’s never been easier for you to boost your manufacturing process and if you follow this guide, you will soon be able to take advantage of the many benefits. Why not see if you could make a positive change to your business today?
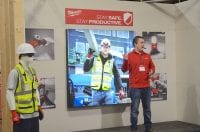
Safety is a crucial priority in every workplace, but it becomes a particularly pressing concern in high-risk environments, especially when working at high elevations. The hazards of working at heights are well-documented and include falls, slips, and trips, among others. In such an environment, ensuring the safety of workers is essential, particularly for those whose Read more
Safety is a crucial priority in every workplace, but it becomes a particularly pressing concern in high-risk environments, especially when working at high elevations. The hazards of working at heights are well-documented and include falls, slips, and trips, among others. In such an environment, ensuring the safety of workers is essential, particularly for those whose job involves working at height.
Whether working on a building construction project, cleaning windows on a skyscraper, or painting a bridge, workers who perform tasks at heights need specialized gear from Lakeside Hire to safeguard them against fatal injuries. Therefore, employers must take proactive steps to protect their employees from falls, slips, and trips when working at height. Workers need to be equipped with the right tools to carry out their job safely, and preventing accidents is worth all the effort.
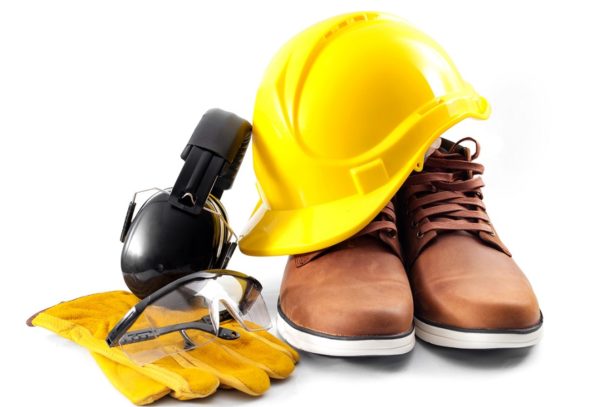
Identifying Hazardous Environments
Protecting workers in high-risk environments is a critical responsibility of every employer. The successful management of hazards requires a systemic and sustained approach that is geared toward identifying and mitigating potential risks that could lead to accidents and injuries. One of the most important steps in this process is identifying hazardous environments. This involves an objective and detailed assessment of the workplace environment to identify potential hazards to workers, such as unstable surfaces or dangerous machinery.
Assessing Risks and Making Adjustments
Assessing risks and making adjustments are crucial steps in protecting workers in high-risk environments. Employers have a responsibility to identify and analyze potential hazards associated with their work sites and to develop strategies to mitigate them. This process can involve conducting risk assessments, creating safety protocols, and training staff on best practices for working at heights. Making adjustments may include the following:
- modifying equipment or work processes
- selecting appropriate protective gear
- regularly reviewing and updating safety procedures
Effective risk assessment and adjustment require collaboration between employers and employees, with a focus on identifying and resolving any possible dangers before they can cause harm.
Utilizing Appropriate Equipment
When working in high-risk environments, appropriate equipment is essential for protecting workers from hazards related to height. This equipment should be selected based on the specific needs of the job and the hazards present. For example, if employees are working at heights where a fall would be deadly, full-body harnesses or safety nets may be necessary.
Conversely, if the height is only a few feet, guardrails or toeboards may suffice. It is important to select equipment that meets safety standards and is in good condition. Additionally, workers should be properly trained on how to use equipment and should inspect it before each use to ensure it is functioning properly. Utilizing appropriate equipment can greatly decrease the risk of injury or death when working at heights.
Developing Comprehensive Safety Protocols
Developing comprehensive safety protocols is crucial for protecting workers in high-risk environments. The first step is to identify all potential hazards that workers may encounter, such as falls, electrocution, or exposure to hazardous substances. Once these hazards are identified, specific safety measures can be established to prevent accidents and minimize injuries. This may include creating designated work areas, installing safety equipment such as grab bars and harnesses, or developing emergency response plans.
It is important to involve workers in the development of safety protocols to ensure they fully understand the measures put in place and can provide feedback based on their work experience. Regular training and communication on safety protocols must also be a priority to maintain a safe work environment. By developing and implementing comprehensive safety protocols, employers can demonstrate their commitment to employee safety and reduce the risk of accidents and injuries in high-risk environments.
Training Employees in Proper Procedures
Training employees in proper procedures is an essential aspect of ensuring safety in high-risk environments. Regardless of the nature of the work, every employee must be trained on the potential hazards and the protective measures that must be taken. This training should include both theoretical and practical components, such as lectures, hands-on demonstrations, and simulations.
Employees should be made aware of the potential risks specific to their job roles and given clear instructions on how to deal with emergencies. It is essential to provide refresher training as needed to ensure that employees remain up to date with safety procedures and respond effectively in any situation. This investment in training can significantly reduce the risk of accidents, prevent injuries, and support a positive safety culture in the workplace.
In Conclusion
Protecting workers in high-risk environments should always be a priority for employers. Height and hazard safety practices are essential to ensuring the safety of workers in dangerous jobs. Implementing effective training programs, using appropriate safety equipment, and following safety guidelines are some of the ways to minimize the risks. By doing so, employers can show their commitment to the safety and well-being of their employees while creating a safer work environment for everyone.
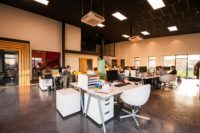
Your business office is an integral part of your company as it’s the face of the organization. How you present that business is influential and can either sway your reputation in a positive way or a negative one. With that being said, anything that you can do to the office, in the way of upgrades Read more
Your business office is an integral part of your company as it’s the face of the organization. How you present that business is influential and can either sway your reputation in a positive way or a negative one.
With that being said, anything that you can do to the office, in the way of upgrades and updates is worthwhile. You want to be seen to be keeping up with your competition and setting a good example of a business that looks after itself both on the inside and out. Whether you are changing things in manufacturing with an engineering change order or you are upgrading the furniture for better storage, there are plenty of changes and upgrades that will benefit your business in a big way.
Let’s take a look at what updates and upgrades your office can make this year.
Replace any old technology with new upgrades
Technology is important for many businesses nowadays and chances are, your business is heavily reliant on technology of many kinds. When it comes to your employees and their use of technology, it’s important to provide them with the very best kit so that they can do their jobs effectively.
What tends to happen when employees are operating on slow or basic equipment, is that their working day becomes less productive. They’re unable to get as much done because they’re constantly encountering slow-loading systems and errors on their screens.
If that sounds like a current issue some of your staff are having, then it may be necessary to replace any and all old technology that is currently in operation. Work with your building operations team or the IT team if they’re responsible, to update any tech that’s seen better days.
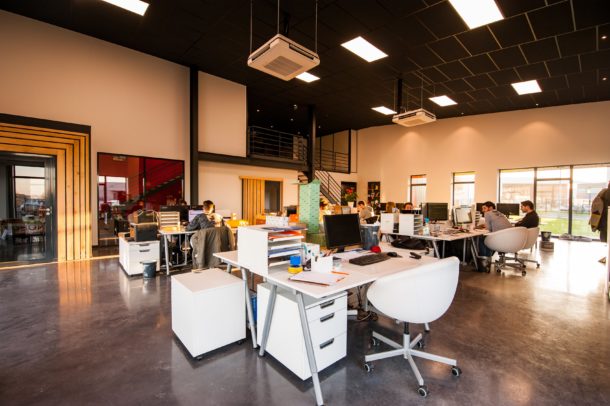
Keep the air clean
The cleanliness of your workplace is important because it not only impacts your staff but it also creates a poor impression with any clients or customers coming into the building. The quality of your air is an important one for the sake of your employees’ health.
If you’re not minimizing the spread of bacteria or air pollution within the atmosphere, then you could be doing more damage than good. You may want to think about how you’re keeping your air clean and whether there’s more that can be done.
What do your air filtration systems look like? Are they brand new or are they outdated and in need of repair? Perhaps it’s a simple case of the air filters needing replacing? If that’s the case, then it’s definitely worth looking at custom filters, rather than having to mess around with finding the right size and shape.
While on the topic of keeping the workplace clean, encourage your employees to be proactive in their cleanliness. You may also want to ramp up workplace cleaning schedules so that it’s helping to contribute to a cleaner environment.
Update communal areas to make them more comfortable
Communal areas are meant for everyone, which means everyone has an equal responsibility to ensure they’re well looked after. However, even when they’re looked after properly, the furniture and general decor of the place may be in need of a bit of TLC.
Office furniture can become damaged and tired over the years, which is why it’s important to try and update these spaces as and when it’s necessary.
Think about investing in your communal areas so that they’re a lot more comfortable to lounge in. Not only is this important to your employees when taking their much-needed lunch breaks, but it’s a space that clients and customers can enjoy too.
If broken furniture is the norm in your communal areas, correct this immediately.
Strengthen the security of entries and exits
As a business, security is a priority, especially as you don’t know who might be watching your business from the outside. The more popular your business gets, the more it’s likely to be targeted by burglars or those who simply want to wander in without the authority to do so.
Strengthening the security of your entries and exits is definitely necessary. Consider what processes you have in place for employees and guests entering and leaving the building. Is it a keycard system and do you have a reception team manned at the entrance at all times?
Is there a need for a security guard? It’s worth making these considerations and vamping up your security as and when it’s required.
Create more open workspaces
Workspaces should be a place where everyone can feel connected. As an organization, it may benefit you to look at working in more open workspaces, rather than confining your space with too many walls that separate team members.
It might not be needed for everyone but where a collaborative workspace is required, knocking down a few walls and opening up the space completely might be just what’s needed.
Ask your employees whether an open workspace would work for them or if they prefer to current setup. After all, you don’t want to disrupt the current working situation if your employees have no problem with it.
Provide privacy with more meeting rooms
Alternatively, your business premises might be missing a bit of much-needed privacy. If some of your employees are struggling to understand what’s been said on the phone with a client, or you’re finding all of the meeting rooms are always occupied, there might be a need for more meeting rooms.
Of course, privacy is an important part of an employee’s working day, so it’s necessary to provide that privacy where you can. Again, this is a query you might want to pitch to your employees before moving forward with the updates.
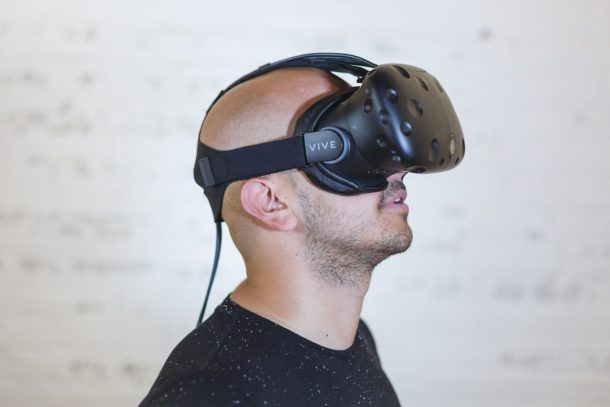
Invest in automation, AI, and virtual reality
Coming back to technology, one of the great upgrades you can make to your technology kit is investing in automation, AI, and virtual reality. These are three big technologies that are changing businesses across the world. If your business isn’t embracing any of these, then it’s definitely worth giving them a go.
AI and virtual reality in particular will continue to be relevant to businesses as the digital age advances.
If you’re looking to do some necessary updates and upgrades to your office, prioritize them for this year.
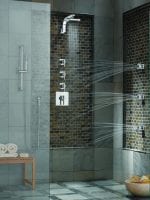
When looking to increase their home’s value, people often focus on cosmetic updates. They prioritize things like repainting the walls or replacing countertops with new, shiny ones. While these improvements are nice to have, they’re often not worth the cost or hassle. Focusing on your strategic home improvement projects can help increase your home value Read more
When looking to increase their home’s value, people often focus on cosmetic updates. They prioritize things like repainting the walls or replacing countertops with new, shiny ones. While these improvements are nice to have, they’re often not worth the cost or hassle.
Focusing on your strategic home improvement projects can help increase your home value. These areas include the basement, garage, attic, and more. Have a look at the details below to learn more!
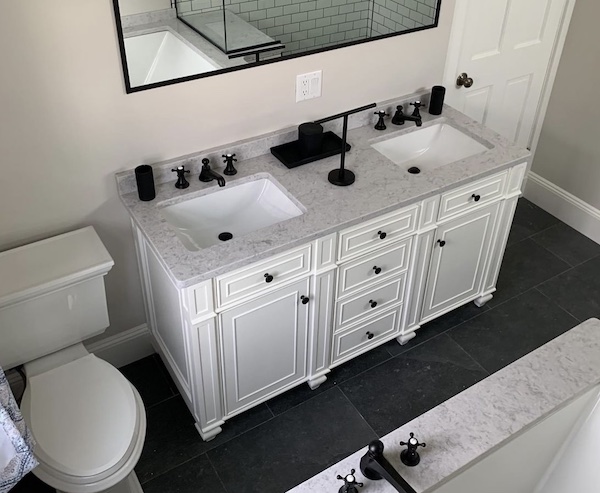
1. Replace an Aging Roof
Replacing an aging roof is one of the most strategic home improvement ideas that increase your home’s value. Today’s roofing shingles and materials often last longer, come in appealing designs, and are much easier to maintain. So this can provide a huge boost to the overall value of your home.
Quality roofing products also come with long-term warranties. This can offer financial protection in the event a replacement is necessary in the future.
Replacing an aging roof can also provide energy efficiency enhancements so you can continually save on energy costs. You can even experience better insulation, ventilation, and airflow.
2. Add a Deck or Patio
Decks and patios are attractive features in any space. They give you an outdoor living area to spend time there with family and friends.
A deck, when properly designed and constructed, adds living space to an existing home. It also increases the valuation of the property and gives you a resale value.
Patios offer an accessible, fashionable, and useful outside area and can increase the aesthetic appeal of the home. Patios are inviting, build visual appeal, and can offer additional gathering space.
Both decks and patios are smart investments that can make your home more attractive to potential buyers. It also adds a touch of class and beauty, which can significantly increase the curb appeal of your home.
3. Put in a Swimming Pool
Pools are often sought-after upgrades by potential buyers. They are a luxurious element that creates a great entertainment center in your backyard. So having a pool incorporated into your home’s design can greatly increase its appeal, making it a great asset to any property.
When installing a pool, make sure that the size and shape are appropriate for the yard and that all local regulations are adhered to. Use quality materials and finishes, such as stone, tile, and stonework. Then, create an attractive surrounding environment that complements the pool.
Ensure that you have a properly functional and energy-efficient pool pump. Note that the installation of items like pool covers and automated timers can further reduce energy costs.
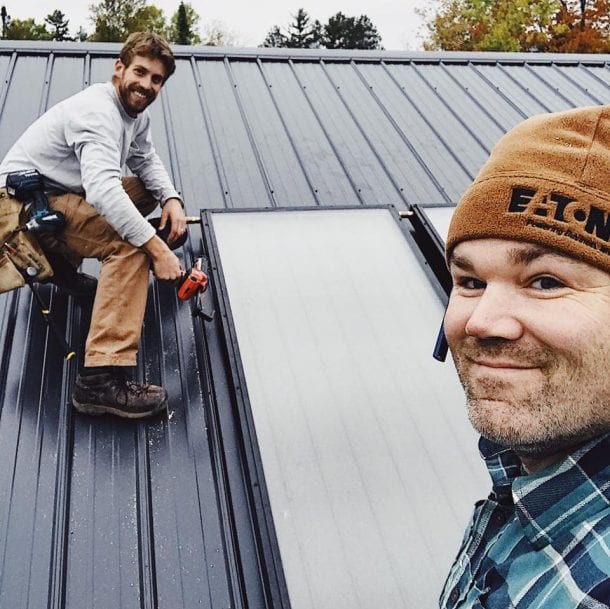
4. Go Green With Solar Energy
Solar energy is a renewable and clean source of energy that you can use to power various systems of your home. This includes appliances like your AC system, lights, and water heater.
Installing solar energy systems also reduces your electricity bill and helps the environment. Not to mention that solar energy systems last for many years and may qualify you for certain credits and discounts.
On top of that, solar energy can increase the resale value of your home. To learn how it works and other benefits that you can receive, you can look for more helpful information from here.
5. Convert a Room Into a Home Office
Converting a room into a home office not only increases the functionality of your home but also increases its value significantly. It allows for a productive work and study environment located in the comfort of one’s own home or away from distractions if the situation calls for it.
One great aspect of converting a room into a home office is the ability to customize it with focus-friendly features. You can add natural lighting, organizational features, and built-in technology. You can even do many conversions cheaply and easily to create a cozy workspace.
Regardless of the style you want to go for, you just need the right amount of research, organization, and planning. With these factors, you can turn an unused room into a home office.
6. Open up the Floor Plan
Opening up the floor plan involves tearing down walls to create larger living areas. This allows more natural light to enter and improves the energy efficiency of your home.
When opening up the floor plan, you should focus on creating a sense of spaciousness while maintaining essential elements. To begin, consider removing any internal walls or partitions that block off areas of the home. If possible, think about using sliding doors or folding walls that you can open and close as needed.
To provide a feeling of continuity, choose a paint color that runs throughout the house. Use décor elements to add interest and style. Furniture should be strategically placed to maximize the openness of the space.
Strategically placed rugs will do wonders for defining and defining certain areas of the room. You should also use lighting to create different zones within the floor plan. For example, up-lighting for furniture and task lighting for areas that require greater visibility.
7. Finish Your Basement
Finishing your basement creates additional living space for you and your family, as well as potential rental income. You can do this as simply as possible, like installing the proper systems. Add electricity, an HVAC system, plumbing, and insulation to ensure that the basement space is highly functional.
You can also enhance its value through additional features such as a wet bar, media center, or fitness room. You can customize the basement to make it fit your lifestyle and needs.
8. Convert the Attic Into a Living Area
Converting the attic into a living area is one of the best home improvement projects that can significantly increase a home’s value. Attics have the potential to be inspiring, livable spaces that are truly unique to the rest of the house. You can transform it into an additional bedroom, living space, or even an office.
Depending on the current state of the attic, updating the insulation and wiring are necessary steps. Adding windows, flooring, and drywall further creates a livable and warm atmosphere. Without compromising the charm of the attic, you could also fit in modern amenities like heating and ventilation.
The attic can also be a great spot for extra storage. Plus, you can take advantage of unique styles like exposed beams, skylights, and other details that you can’t find anywhere else. It’s not just a bonus living area, it’s a bonus living area that will instantly add value to any home.
9. Renovate Your Bathroom
One of the strategic home renovation ideas is to renovate your bathroom. Many modern buyers are looking for luxury bathrooms with the latest features. So making the upgrade to maximize a home’s value.
You need to replace old and outdated fixtures. Freshen up the overall look with new tile, flooring, and fresh paint. Then, add storage space like cabinets, drawers, and closets.
After the renovation is complete, you can also enjoy a more personal, relaxing, and functional space – a true win-win! You will be able to enjoy your morning rituals in a better space.
10. Refinish Your Hardwood Floors
Refinishing your hardwood floors is one of the best strategic home renovation projects you can do. It can give your home a refreshed look and improve the overall atmosphere.
Refinishing can help restore them to their original beauty and make them look new again. That is a benefit that many homeowners appreciate because it can help to hide signs of aging, wear, and tear.
It also protects the wood’s surface and helps maintain the aesthetic value of the room. Plus, it adds a finished, highly attractive look that adds warmth and character to the space.
Just make sure that you hire a professional when you are refinishing your hardwood floors. This is because a knowledgeable contractor guarantees a successful result.
11. Upgrade Plumbing and Electrical Systems
Upgrading the plumbing and electrical systems ensures that the systems meet modern standards. This also helps your system function more reliably than before. Replacing obsolete wiring and adding additional outlets can even help improve safety and reduce risks of fire.
Newer, more efficient water lines reduce water waste and cut down on water bills. Improved drainage systems can help prevent water damage and preserve the functionality of fixtures in the long term.
Not only can modernizing your home’s plumbing and electrical systems increase the value of your home, but it can also make it look more up-to-date. It can prevent potential issues or mishaps down the road and even qualify your home for better insurance.
Try These Home Improvement Projects Now
Strategic home improvement projects can be a great way to increase the value of your home. But it’s important to carefully consider projects that provide a meaningful return on your investment. At the end of the day, you need to base the decision on your individual needs.
So don’t delay. Today is the day to get started on improving the value of your home. Contact a professional contractor and get started on the path to a more valuable home!
For more informative articles like this, check out the rest of our site now.