Managing waste effectively is crucial for every construction project, and plumbing and HVAC installations are no exception. Whether upgrading an HVAC system or replacing plumbing fixtures in Graniteville, proper waste disposal is necessary for maintaining a clean and safe work environment and complying with local regulations. Waste management solutions tailored to the specific needs of Read more
Whats New
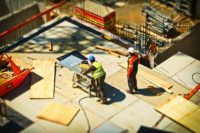
Managing waste effectively is crucial for every construction project, and plumbing and HVAC installations are no exception. Whether upgrading an HVAC system or replacing plumbing fixtures in Graniteville, proper waste disposal is necessary for maintaining a clean and safe work environment and complying with local regulations. Waste management solutions tailored to the specific needs of these projects can streamline the process, reduce delays, and promote sustainability. One such solution is cleanup dumpster rentals, which provide a convenient way to manage large volumes of waste while ensuring that the project site remains organized and efficient.
The Importance of Waste Management in Plumbing and HVAC Projects
Plumbing and HVAC projects typically generate considerable debris, including old pipes, fittings, insulation, and other materials. This waste can accumulate quickly, leading to cluttered workspaces and potential safety hazards. Without a well-organized waste management system, contractors may spend valuable time sorting and disposing of debris, which can delay the project and increase costs.
Effective waste management ensures that waste is disposed of properly, reducing the project’s environmental impact. Moreover, a streamlined waste disposal plan helps contractors focus on the project’s technical aspects without worrying about where to put leftover materials. By utilizing professional waste removal services, such as cleanup dumpster rentals, contractors in Graniteville can easily manage the waste generated during plumbing and HVAC projects, making the process more efficient and cost-effective.
Tailored Waste Removal Solutions for Plumbing and HVAC Projects
In Graniteville, one of the most efficient ways to manage waste from plumbing and HVAC projects is through specialized waste removal services. Local waste removal companies offer flexible dumpster rental options that cater to the needs of plumbing and HVAC contractors. These dumpsters come in various sizes, ensuring that there’s an option that suits the scale of the project. Whether a minor residential plumbing upgrade or a large-scale commercial HVAC installation, contractors can find a solution that fits their waste disposal requirements.
Additionally, many waste removal companies in Graniteville are well-versed in handling construction debris, including the materials typically found in plumbing and HVAC projects. For example, they are equipped to handle old pipes, ductwork, insulation, and other construction waste, ensuring that these materials are disposed of in compliance with local regulations. By choosing a company that understands the unique needs of plumbing and HVAC waste, contractors can avoid issues with improper disposal and ensure that they comply with environmental standards.
Enhancing Project Efficiency with Dumpster Rentals
The flexibility of cleanup dumpster rentals can significantly enhance the overall efficiency of plumbing and HVAC projects. By placing dumpsters strategically on the job site, contractors can keep their work areas clean and organized, which promotes a safer working environment. Workers won’t have to waste time walking long distances to dispose of materials, which helps maintain the project’s momentum. Instead, waste can be quickly and easily discarded in the designated dumpsters, allowing the team to focus on their tasks.
Furthermore, dumpster rentals offer a hassle-free disposal option that saves contractors from dealing with the logistical challenges of transporting waste to a landfill. Many waste removal services in Graniteville provide convenient pick-up and drop-off services, so contractors don’t have to worry about the logistics of getting rid of the debris. This level of service enables contractors to focus on their craft while waste management professionals handle the disposal side of the operation.
Conclusion
Waste management is crucial to any plumbing or HVAC project in Graniteville. By using tailored solutions such as cleanup dumpster rentals, contractors can streamline the waste disposal process, reduce project delays, and maintain a cleaner and safer work environment. Choosing the exemplary waste removal service ensures that the materials generated during the project are correctly handled and disposed of, contributing to the work’s efficiency and sustainability. This leads to successful project completion and helps contractors focus on delivering high-quality plumbing and HVAC services to their clients.
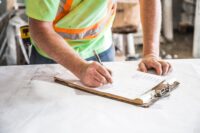
Being a contractor is a great way to make your living using your skills and experience right now. Sure, there’s a bit of stress, sweat, and probably more dust than you’d find under a five-year-old’s bed, but the perks outweigh the pitfalls, as you will see below… Freedom to Flex Your Creative Muscle People often Read more
Being a contractor is a great way to make your living using your skills and experience right now. Sure, there’s a bit of stress, sweat, and probably more dust than you’d find under a five-year-old’s bed, but the perks outweigh the pitfalls, as you will see below…
-
Freedom to Flex Your Creative Muscle
People often assume construction is just about following plans and stacking bricks. But contractors know the real secret: there’s a huge creative element hidden in those blueprints. You’re coordinating architectural design, choosing materials, and figuring out how to make unique client requests come to life (looking at you, rooftop mini-golf course). Each project is a puzzle waiting to be solved—a perfect playground for anyone with an innovative spirit and a knack for thinking outside the standard rectangular box.
-
Variety: Your Days Are Never Boring
If you can’t stand the monotony of doing the same thing day after day, commercial contracting is your ticket to variety galore. One week, you’re retrofitting a century-old building for modern tech; the next, you’re overseeing storage tank repair for a sprawling industrial complex. (Yes, that’s a thing. Contracts can take you to all sorts of unexpected corners, from big-box retail expansions to those top-secret research facilities you’re still not allowed to talk about.) Each project has its own quirks, keeping your brain engaged and your career feeling fresh.
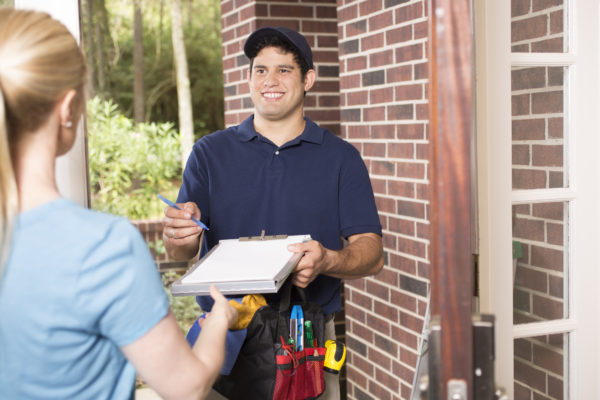
-
Be Your Own Boss—Kind Of
While you might be answering to clients, city inspectors, and your employees, there’s no denying the sense of ownership you get when you’re the head honcho on a commercial contracting project. You set your own schedule, hire your own team, and bring your unique style to the job site. Sure, deadlines and city ordinances might sometimes feel like your real bosses, but at least you won’t be stuck under fluorescent lights with a micromanager breathing down your neck. You call the shots—which means you decide when (and if) there’s time for a coffee run.
-
The Thrill of Tangible Results
In many office jobs, your day-to-day might boil down to a bunch of emails and spreadsheets that vanish into the digital abyss. Not so in commercial contracting. Whether you’re renovating a tired old warehouse or constructing a shiny new school, your work leaves an undeniable mark. People will literally walk through, sit in, and admire the buildings you’ve helped create. And that pride of craftsmanship? It’s like having your own personal highlight reel, except it’s made of concrete and steel for all the world to see.
-
The Opportunity for Big Bucks (If You’re Savvy)
Of course, we can’t overlook the potential financial rewards. Commercial construction can be lucrative, especially if you’ve got a knack for delivering top-notch work on time and under budget. While you’ll likely endure a few sleepless nights (and maybe more calls at 3 a.m. than your phone plan ever expected), the paycheck at the end of a well-run project can make those headaches fade away—at least until the next project’s chaos hits.
-
The Unmatched Sense of Camaraderie
Picture this: you’ve just spent weeks orchestrating heavy machinery, coordinating deliveries, and corralling a small army of workers, all to meet a looming deadline. Then, at the 11th hour, everything snaps together perfectly. The sense of victory you share with your crew at that moment is priceless. Commercial contracting fosters tight-knit teams that celebrate wins—and occasionally commiserate over late-night supply shortages—together. It’s like being part of a weird, high-stakes sports team, minus the athletic gear and plus a lot more mud.
-
Constant Learning Keeps You Sharp
If you’re the type who hates stagnation, you’re in luck. Every new building code, advanced material, or emerging technology presents a fresh opportunity to expand your skill set. Today, you might be mastering an eco-friendly insulation product; tomorrow, you’ll navigate new safety regulations for working at extreme heights. It’s like going to school forever—except you get paid, and you get to wear cool reflective vests instead of dealing with pop quizzes on Shakespeare’s sonnets.
-
Networking That Pays Off
From architects and engineers to city officials and future tenants, a commercial contractor’s daily to-do list includes meeting a wide array of people. Yes, some of these people might be slightly grumpy (especially if you’re behind schedule), but many can become invaluable resources and long-term business partners. Being a commercial contractor automatically puts you at the center of a network of professionals who might send more lucrative jobs your way if you impress them. Think of every project as a chance to expand your circle—and maybe score an invite to a fancy ribbon-cutting ceremony along the way.
-
Job Security in a Changing World
Even in an age of high-speed internet and remote everything, buildings aren’t going anywhere anytime soon. In fact, new structures are always popping up, and old ones always need fixing. Whether you’re delving into major overhauls of historical sites or helping a tech company build its brand-new campus, commercial contractors are never exactly short on opportunities. And with the rise in specialized needs (like making buildings more environmentally friendly), your skill set will only get more in demand.
Never considered contracting? Now might be the time!
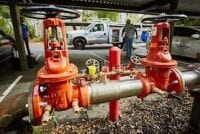
Although backflow repair seems difficult at first, good knowledge helps to turn this difficulty into a reasonable endeavor. Maintaining water purity and preserving health depend on a well-working backflow-prevention system. Hence, prompt repairs are essential. This handbook demystifies backflow repair by providing step-by-step directions, useful guidance, and fundamental safety measures to restore appropriate flow, therefore Read more
Although backflow repair seems difficult at first, good knowledge helps to turn this difficulty into a reasonable endeavor. Maintaining water purity and preserving health depend on a well-working backflow-prevention system. Hence, prompt repairs are essential. This handbook demystifies backflow repair by providing step-by-step directions, useful guidance, and fundamental safety measures to restore appropriate flow, therefore guaranteeing dependability of performance and efficiency.
Safety Measures and Basic Tools for Backflow Repair
To guarantee a good fix in backflow repair, strict safety precautions and the correct set of tools are needed. Designed to handle typical problems in these systems, basic tools include wrenches, pliers, sealant, and specialist backflow testing kits. In addition to repairs, expert backflow installation services require precision and high-quality tools to ensure proper setup and long-term functionality. Using excellent tools not only streamlines the repair procedure but also reduces the possibility of more harm while troubleshooting. Perfect adjustments and safe reassembly made possible by a well-equipped toolkit guarantee the system recovers its intended operation with little downtime.
Safety always comes first in any repair, especially with systems managing drinkable water. Turning off the main water supply is essential to stop unintentional floods or contamination even before repairs start. Gloves and safety goggles are among the protective tools to wear; all electrical connections have to be tightly separated. Following set safety procedures during backflow repair reduces risks and guarantees that every stage of the operation is carried out under supervision. These steps ensure the integrity of the water system as well as the repair staff, therefore enabling a seamless and safe repair process.
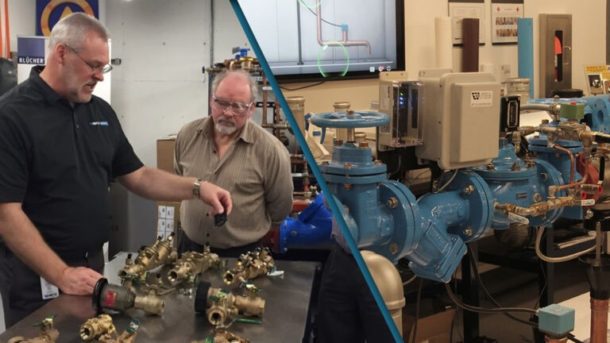
Methodical Approach for Backflow Repair
Backflow repair demystifies the procedure and guarantees complete system restoration via a methodical, step-by-step approach. The repair trip starts with a total water supply shutdown and then proceeds with a meticulous disassembly of the impacted valve components. Next is a thorough inspection of check valves, gaskets, and seals, looking for any wear or damage that can affect system operation. Every component is then cleaned, examined, and replaced as needed to guarantee that, prior to reassembly, every element satisfies the appropriate criteria.
Complete testing is crucial to verify that the backflow-prevention mechanisms operate as expected once the system has been rebuilt. Water quality analyses and pressure testing confirm that the repair has effectively removed contamination hazards and restored correct flow direction. Apart from verifying the completion of the repair, thorough testing gives a piece of mind, knowing the system is currently running without problems. This methodical strategy to repair promotes a better knowledge of the mechanics of the system, thereby facilitating future maintenance by means of efficiency.
Strategies for Preventive Maintenance to Avoid Problems Tomorrow
Avoiding recurrent backflow issues mostly depends on following a strong preventative maintenance schedule. Routine maintenance of backflow prevention systems and regularly planned inspections help to find early wear, corrosion, or possible failure. By treating small problems before they become more significant, preventive maintenance not only lowers the danger of contamination but also increases the system’s lifetime. A regular maintenance schedule is a proactive step that guarantees the system stays in the best operating order throughout time.
Apart from routine inspections, including contemporary monitoring technology improves preventative plans even more. Real-time water pressure and flow monitoring via automated alarms and digital tracking systems warn of any abnormalities that could point to developing problems. These sophisticated steps offer a whole picture of system performance and enable quick response as needed. Regular performance assessments and proactive maintenance together provide a strong basis for long-term water safety, therefore lowering both operating interruptions and expensive emergency repairs.
Understanding When to Consult Experts
While do-it-yourself remedies can fix minor backflow problems, other cases call for the knowledge of a qualified plumber or backflow specialist. Complicated issues, ongoing mistakes, or conflicting diagnosis findings usually point to expert help being needed. Expert specialists guarantee that the system is returned to its best by bringing to the repair process specialized tools and thorough expertise. Their knowledge enables a more precise diagnosis, and the use of sophisticated treatments may not be possible for a non-specialist.
Professional guidance suited to particular needs and thorough system reviews are two long-term advantages as well. Professional servicing not only ensures a high-quality repair but also lowers the danger of future problems by means of skilled maintenance suggestions. Understanding the limits of do-it-yourself projects and choosing expert advice when needed guarantees that the backflow system stays compatible with local safety rules, secure, and effective. This calculated move now guarantees ongoing, dependable water safety by safeguarding property and health alike.
Conclusion
Reliable backflow repair protects property, health, and water quality, therefore averting expensive harm. This all-encompassing strategy guarantees consistent water safety, therefore enabling property owners to have confidence and peace of mind for many years to come.
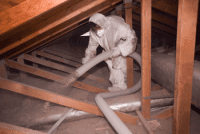
USA Spray Me is a leading company in the field of insulation, offering a range of high-quality spray foam and waterproofing solutions for residential, commercial, and industrial properties. Specializing in spray foam insulation and closed cell insulation, USA Spray Me provides effective solutions for energy efficiency, soundproofing, moisture control, and overall building protection. The company Read more
USA Spray Me is a leading company in the field of insulation, offering a range of high-quality spray foam and waterproofing solutions for residential, commercial, and industrial properties. Specializing in spray foam insulation and closed cell insulation, USA Spray Me provides effective solutions for energy efficiency, soundproofing, moisture control, and overall building protection. The company is known for its commitment to customer satisfaction, offering personalized services and innovative solutions that meet the specific needs of their clients. With a team of experienced professionals and cutting-edge technology, USA Spray Me ensures that each project is executed with precision and quality. The company’s reputation for excellence has made it one of the go-to choices for spray foam and insulation services in the United States, particularly in areas like San Francisco and the Bay Area.
Spray Foam Removal Companies: Ensuring a Clean and Safe Environment
While spray foam insulation is an excellent solution for energy efficiency and comfort, the removal of old or improperly installed spray foam can sometimes be necessary. Spray foam removal companies specialize in safely and effectively removing spray foam from various surfaces, including walls, ceilings, and floors. This process requires expertise and specialized equipment to ensure the removal is done without causing damage to the underlying structure.
Professional spray foam removal companies like USA Spray Me offer services that not only remove the foam but also provide a clean environment post-removal. This can be crucial in situations where spray foam was applied improperly or where property owners are renovating or upgrading their insulation systems. The benefits of hiring a spray foam removal company include:
- Safe and efficient removal: Experts use specialized tools to extract foam without damaging surfaces.
- Prevention of health risks: Improperly installed spray foam can lead to air quality issues, and removal ensures a safer living environment.
- Environmental responsibility: Professional companies can dispose of foam waste in an eco-friendly manner.
- Cost-effective solutions: Though removal can be an investment, it can also help save on future energy bills by enabling better insulation installation.
Closed Cell Insulation: A Game-Changer for Energy Efficiency
Closed cell insulation, one of the flagship services offered by USA Spray Me, is widely regarded as one of the most effective forms of insulation for a variety of applications. Unlike open cell foam, closed cell foam has a denser structure that provides superior insulation and moisture resistance. This makes it an ideal choice for homeowners, contractors, and building managers looking to improve energy efficiency and reduce utility costs.
USA Spray Me specializes in the application of closed cell insulation, providing clients with a durable, long-lasting solution that helps regulate temperature, reduce sound transmission, and prevent mold and moisture buildup. Some of the key benefits of closed cell insulation include:
- Superior thermal performance: Closed cell foam provides a high R-value, which helps to keep spaces warmer in the winter and cooler in the summer.
- Moisture resistance: Closed cell foam acts as a barrier to moisture, preventing mold growth and water damage.
- Increased structural integrity: The rigidity of closed cell foam enhances the strength of walls, ceilings, and roofs.
- Energy savings: By improving insulation, closed cell foam can significantly lower heating and cooling costs.
- Soundproofing qualities: Closed cell insulation helps in sound dampening, making it an ideal choice for buildings in noisy environments.
San Francisco and Bay Area: Leading the Charge in Thermal and Waterproof Insulation
San Francisco and the Bay Area are known for their progressive approach to sustainable construction and energy-efficient building solutions. The region is at the forefront of adopting advanced insulation and waterproofing technologies, and USA Spray Me is proud to be a part of this movement. In these areas, where seismic activity, varying weather patterns, and energy efficiency standards are of concern, USA Spray Me’s closed cell insulation and waterproofing solutions have become essential for both new construction and renovation projects.
In cities like San Francisco, energy efficiency is a top priority due to the high cost of living and environmental considerations. By investing in spray foam insulation and waterproofing services, residents and businesses in the Bay Area can enjoy a variety of advantages, including:
- Improved energy efficiency: Closed cell insulation helps to reduce heating and cooling costs, making it an excellent investment for long-term savings.
- Enhanced moisture control: With San Francisco’s damp coastal climate, preventing moisture intrusion is critical to preserving building integrity.
- Sustainability: The use of high-performance insulation materials contributes to a more sustainable and eco-friendly building practice.
- Seismic protection: Closed cell foam adds rigidity to structures, providing extra stability in the event of an earthquake.
USA Spray Me’s Excellence in the Bay Area: A Commitment to Quality
The professionals at USA Spray Me are known for their expertise in spray foam insulation, closed cell insulation, and waterproofing solutions throughout San Francisco and the Bay Area. Whether it’s a residential project or a large commercial venture, the team at USA Spray Me brings the same level of dedication and quality to every job. Their ability to adapt to local needs – such as compliance with energy efficiency regulations, moisture management, and seismic activity – sets them apart as leaders in the field.
In addition to the technical expertise, USA Spray Me prides itself on its customer-centric approach. They understand the importance of clear communication, timeliness, and attention to detail. The following are just a few reasons why USA Spray Me stands out in the San Francisco and Bay Area markets:
- Expertise and experience: A dedicated team with extensive knowledge of insulation materials, methods, and local building codes.
- Personalized services: Tailored solutions based on the specific needs of each client and building type.
- Sustainable and eco-friendly: USA Spray Me is committed to using environmentally friendly materials and techniques.
- Competitive pricing: Offering high-quality services at affordable prices, ensuring value for money.
- Commitment to safety: Following all safety protocols to ensure a secure work environment for both staff and clients.
USA Spray Me has built a reputation in the Bay Area for excellence in insulation and waterproofing, making them a go-to choice for property owners seeking long-lasting, energy-efficient solutions. The company’s expertise, high-quality services, and commitment to innovation have made them a trusted partner in improving the comfort, sustainability, and efficiency of homes and businesses throughout the region.
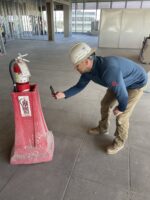
In 2023, 2.6 million people in the US faced workplace injuries and illnesses. The Bureau of Labor Statistics reported that over 5,000 people lost their lives to accidents – many of which were avoidable. OSHA, i.e., the Occupational Safety and Health Administration, has long played a vital role in preventing such tragedies. The organization lays Read more
In 2023, 2.6 million people in the US faced workplace injuries and illnesses. The Bureau of Labor Statistics reported that over 5,000 people lost their lives to accidents – many of which were avoidable.
OSHA, i.e., the Occupational Safety and Health Administration, has long played a vital role in preventing such tragedies. The organization lays down guidelines to make workplaces safer across sectors, from construction to manufacturing. However, all that may change in America’s new political reality.
The turbulent socio-political landscape in the US presents many challenges for contractors across industries. Sectors like construction and manufacturing are at greater risk due to the inherent nature of the tasks involved. Tied to this chaos is the overall growth of businesses and the prospects of employees and their families.
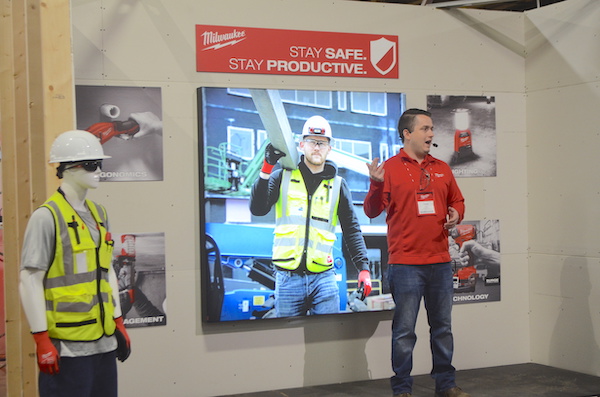
Is OSHA Under Threat?
Recently, Congressman Andy Biggs introduced a bill to abolish the OSHA: the Nullify Occupational Safety and Health Administration Act.
The bill argues that federal “meddling” in workplaces impedes growth. Further, it claims that OSHA’s rules are harsher for states with hotter climates, preventing optimal outdoor work.
One should note that heat-related illnesses are an established problem globally. The Center for American Progress finds that workers in construction sites and warehouses face more heat exhaustion and stroke incidents, especially with rising temperatures linked to global warming.
Supporters of nullifying OSHA argue that the regulations may be too stringent, stifling economic progress. The push for budget-cutting comes from the Department of Government Efficiency, led by Elon Musk.
Recently, the department shut down the US Agency for International Development (USAID). The move has faced plenty of controversy, with a federal judge ruling it likely unconstitutional.
It won’t be far-fetched to surmise that OSHA’s funding cuts may be in response to the agency’s past treatment of Elon Musk-led companies. OSHA has investigated several safety concerns at SpaceX and Tesla. After a worker died in Tesla, Texas, OSHA asked the company to pay a fine of $50,000. Tesla faced questions about inadequate protection against electrical and falling hazards.
Talks have also been rampant about cutting OSHA’s funding or budget allowance. The argument is that these budget cuts will promote economic growth in the country.
The Impact of Sidelining OSHA
The most dangerous impact will be on workers’ health and safety. Without adequate funding, the organization will struggle to partner with companies to ensure compliance with safety standards. Preventable accidents and deaths will mount, causing emotional and financial losses.
The present situation is troubling for contractors whose work requires a high degree of safety. A construction contractor cannot work peacefully if their team is susceptible to risks of falling and getting hurt from non-compliant equipment. Failing to label toxic chemicals and other common OSHA violations leads to several mishaps annually.
Another tangible effect of ignoring OSHA will be the rising number of worker compensation claims. Over time, the financial burden on companies will be immense. According to Conn Maciel Carey LLP, firms should follow a proactive compliance strategy. It can reduce accident rates and insurance premiums, besides improving the morale of the staff.
Moreover, one must note that the downtime due to workplace injuries will suppress economic growth. It goes sharply against what the proposed nullification of OSHA is supposed to promote.
Promoting Workplace Safety in a Turbulent World
Amid these developments, contractors will need additional caution to keep their teams safe. For example, they must prioritize training the workforce on safety protocols.
The 2024 World Risk Poll reported that 62% of the global workforce has never received workplace health and safety training. While it is alarming in itself, there’s more: people who don’t get training are less likely to report injuries and harm when they do occur.
Contractors must advocate for integrating safety throughout the business, encouraging managers to view it as a performance driver, not a constraint. A Harvard Business Review feature recommends that companies identify safety metrics and establish practices to improve safety in the workplace.
For example, a confidential hotline can allow workers to report violations without fear. Managers’ incentives can link to how well their team members follow preventive safety measures, like using outdated machinery.
Another potent approach is conducting expert-led safety audits. It can help your company identify areas of non-compliance, such as a specific facility or equipment. Accordingly, you can take immediate action to prevent an accident emanating from the risk.
Proactive measures are paramount to keep employees safe in stressful work environments. Basic steps like offering personal protective equipment can avoid respiratory problems in manufacturing facilities. Likewise, holding routine health evaluations can warn you of possible concerns like asthma.
Only time will tell how OSHA will fare in the US’s current environment, so precarious and volatile. However, one cannot deny that being lax about workplace safety can only be damaging for all stakeholders.
These times mandate greater vigilance and responsiveness from contractors. They must champion uncompromised safety for their teams, more so when the outside world places it on the backburner.