The AHR Expo (International Air-Conditioning, Heating, Refrigerating Exposition) 2022 Innovation Awards call for entries is now open. The annual competition, held in conjunction with the Show, honors the most innovative and original products, systems and technologies in HVACR. Exhibitors are encouraged to submit new or upgraded products to compete. Entries will be accepted through August Read more
Featured
AHR Expo Announces Open Call for the 2022 Innovation Awards; Entries Accepted through August 3, 2021
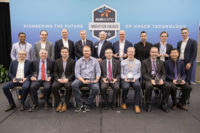
The AHR Expo (International Air-Conditioning, Heating, Refrigerating Exposition) 2022 Innovation Awards call for entries is now open. The annual competition, held in conjunction with the Show, honors the most innovative and original products, systems and technologies in HVACR. Exhibitors are encouraged to submit new or upgraded products to compete. Entries will be accepted through August 3, 2021. The 2022 AHR Expo will be hosted at the Las Vegas Convention Center in Las Vegas, NV January 31 through February 2, 2022. To request more information about the Innovation Awards, or to receive forms for entry, please email Kim Pires at kpires@iecshows.com.
“First and foremost, we are thrilled to gather again in Las Vegas for the 2022 AHR Expo. Despite not coming together in 2021, we celebrated ten outstanding category winners and the Product of the Year, Infinitum Electric’s IEq,” said Mark Stevens, Manager of AHR Expo. “This competition celebrates the HVACR industry’s most innovative solutions through leadership in design, construction and execution. Each year we look forward to seeing the advancements in HVACR through the snapshot that the Innovation Awards provides. It is an excellent indicator of the exciting Show ahead.”
In 2003 the AHR Expo debuted the Innovation Awards as a means to highlight those in the HVACR industry creating innovative solutions for new and existing challenges and new avenues for growth. They aim to honor the most inventive, useful and original products, systems and technologies pushing boundaries and disrupting the market today.
Entries are evaluated by a panel of third-party ASHRAE members with over 20 years of professional engineering experience. The review process includes points tallied based on application, innovation, value and market impact. Winners are selected from ten industry categories, including: building automation; cooling; heating; indoor air quality; plumbing; refrigeration; software; sustainable solutions (formerly green building); tools and instruments; and ventilation. Winners and finalists demonstrating superior innovative design, creativity, application and performance will be recognized at the 2022 Show, on the AHR Expo website and social media channels, as well as in industry media coverage leading up to the Show.
An overall Product of the Year will be selected from the pool of category winners and will be announced at the Show. This prestigious honor is awarded based on exceptional leadership in HVACR innovation.
Eligibility and general information about the 2022 Innovation Awards
- The competition is open to exhibitors with a confirmed space contract, as well as a deposit payment on file for the 2022 AHR Expo.
- Eligible products include those that will be exhibited at the 2022 AHR Expo in Las Vegas and must be available for sale by January 2022.
- Exhibitors are permitted to submit one product per category.
- Product entries are limited to one product category.
- Products that have previously won an AHR Expo Innovation Award are not eligible, however, those products that have previously been named a category finalist may be re-entered.
- Completed entry forms, along with a non-refundable $100 entry fee, must be submitted by Tuesday, August, 3, 2021.
- One winner from each category will be selected. An overall Product of the Year award is selected from all category winners and announced at the 2022 Show.
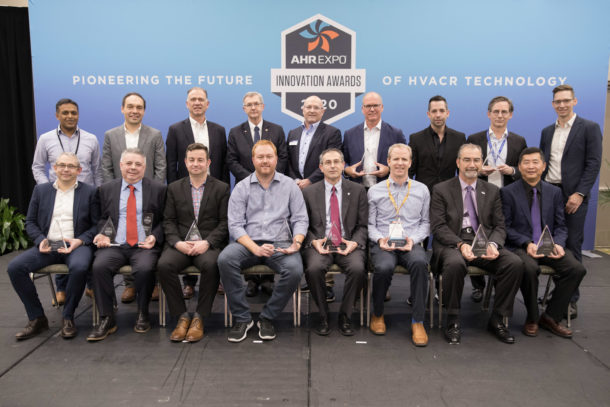
Entry fees for the 2022 Innovation Awards (approximately $20,000) will be donated to a charitable organization serving the local Las Vegas area community. The donation is generally used to provide HVACR repairs or upgrades. Each year, the AHR Expo works to select a charitable organization within the area where the Show is held.
“This past year has been a catalyst for new ways of thinking and adapting,” continued Stevens. “Our industry has risen to the challenge and provided critical solutions to help us move forward. HVACR is an area of exciting innovation on the global stage and we can’t wait to see what awaits us on the Show floor in Las Vegas.”
Registration for the 2022 AHR Expo is expected to open in July of 2021. Visit the AHR Expo website for updates and to sign up for the Show newsletter.
ABOUT THE AHR EXPO
The AHR Expo is the world’s premier HVACR event, attracting the most comprehensive gathering of industry professionals from around the globe each year. The Show provides a unique forum where manufacturers of all sizes and specialties, whether a major industry brand or innovative start-up, can come together to share ideas and showcase the future of HVACR technology under one roof. Since 1930, the AHR Expo has remained the industry’s best place for OEMs, engineers, contractors, facility operators, architects, educators and other industry professionals to explore the latest trends and applications and to cultivate mutually beneficial business relationships. The next Show, co-sponsored by ASHRAE and AHRI, will be held Jan. 31 – Feb. 2, 2022 in Las Vegas, and is held concurrently with ASHRAE’s Winter Conference.
For more information, visit ahrexpo.com and follow @ahrexpo on Twitter and Instagram.
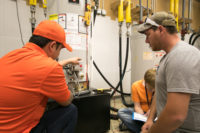
Ongoing training is an essential pillar of the skilled trades. Trades professionals who proactively engage with opportunities to learn about new processes and new technology deliver better experience and workmanship, make more educated decisions, complete more work in less time and establish trust with customers. In short, ongoing training helps create the right conditions for Read more
Ongoing training is an essential pillar of the skilled trades. Trades professionals who proactively engage with opportunities to learn about new processes and new technology deliver better experience and workmanship, make more educated decisions, complete more work in less time and establish trust with customers.
In short, ongoing training helps create the right conditions for positive business growth.
Unfortunately, for a variety of reasons, our industry has not traditionally made non-required continuing training a priority. Many skilled tradespeople are reluctant to pursue the opportunities made available by professional organizations, trade associations and manufacturers. Business owners and leadership teams often fail to invest in training for their technicians and office staff. Additionally, the current COVID-19 crisis has had an enormous impact on the nature of training in the industry.
Virtual training offers convenience and accessibility, but in-person, hands-on engagement has proven to be the most effective and preferred method of training for skilled trades professionals. While the best examples of virtual training can replicate some of the elements of live, personal interaction by providing opportunities for direct feedback and questions, the vast majority of virtual training options are pre-recorded. The effective elimination of live training by safety concerns, travel restrictions and social distancing is yet another huge COVID-19-related challenge our industry faces.
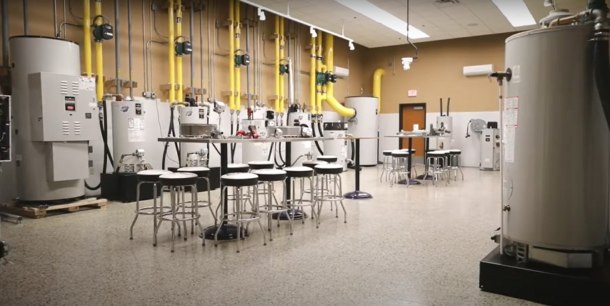
What training is and isn’t
Our industry may be short on training, but we use the word a lot. In fact, it’s one of the most overused terms in the skilled trades professions, primarily because we apply it to many things that aren’t training.
Training is not just information sharing. Training involves both the sharing of information and action.
When you’re weight training, you don’t watch it on a screen. You might review proper form and execution, but weight training is an action. It’s exactly the same for professional technical training in the trades. Training involves watching and then doing, learning through hands-on experience. Many people have pursued a career in the trades because they like to work with their hands and learn by doing.
Many trades professionals have demonstrated initiative and embraced the virtual training that has sprung up in the last year. Video tutorials and webinars have value in introducing technicians to new equipment, processes and concepts, but that’s only half of the full training experience. Following up virtual training with hands-on practice is essential for fully translating information into actionable skill. As the pandemic slows, expect in-person training to boom as agents look to validate the practices and concepts seen on the screen. Trades people are looking forward to mixing it up, getting back to their roots and making things happen.
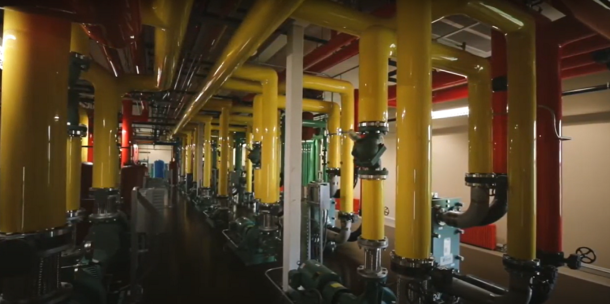
A “traditional” industry
If you surveyed the skilled trades right now and asked what the biggest barrier to training is right now, most professionals would say they’re too busy and don’t have enough people. It’s true that the labor shortage is a lasting challenge, but there may be deeper reasons for training hesitance.
In my early days as an HVAC technician, I learned the ropes working with a specific manufacturer. I was loyal to that manufacturer, but I had less confidence working with other companies’ products. We do what we know how to do. A related fact is that we don’t like to admit to ourselves or others what we don’t know or are unsure about. Many people in today’s world, not just in the skilled trades, feel incredible pressure to already know everything they need to know.
In the trades, an unfortunate result is that too many professionals wrongly calculate that by exposing themselves to training, they’re also revealing what they don’t know. Getting them to understand that it’s OK not to know something is a major obstacle for trainers and business owners.
Many trades people value their personal experience in the industry over formal ongoing training. While experience on the job is critical, so is continuing engagement with new technology and processes.
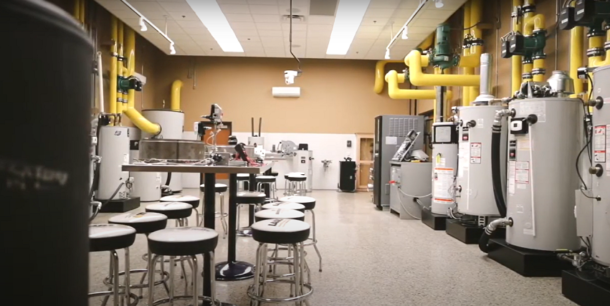
The critical carrot
We know why training is important. We know what it can be worth. How do you convince the industry to commit to training as a critical element of our industry?
You have to have a carrot.
There has to be something at the end that makes it worthwhile, whether it’s recognition within the company, financial reward or added benefits. The difference in experience and training is reflected in the different labor rates for a master plumber and a journeyman. The recognizable difference in skills and knowledge typically sets a master apart.
The more relevant the carrot is to the training, the more effective it will be in the long run. More training can put a technician in position to earn more money as a local expert, and that’s a gift that keeps on giving.
Confidence is at the very top of the list of advantages resulting from quality training. When technicians have a solid foundation of up-to-date skills, customers end up paying for service they’re satisfied with. Confident techs deliver better experience and build relationships.
The better trained a contractors’ team is, the fewer mistakes they’ll make. With training, techs work more quickly and more accurately and in the end are more cost effective.
Dustin Bowerman is director of corporate training and product support for Bradford White Corporation, a full-line manufacturer of residential, commercial and industrial products for water heating, space heating, combination heating and storage applications. For more information, visit www.bradfordwhitecorporation.com.
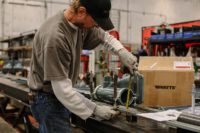
Southland Industries was founded in Long Beach, California, in 1949 as a Southern California-based supplier of residential heating solutions. After years of growing organically and expanding their services and capabilities, they are now one of the nation’s largest MEP (mechanical/electrical/plumbing) building systems experts. Today, Southland has 3,200 employees who serve most of the East and Read more
Southland Industries was founded in Long Beach, California, in 1949 as a Southern California-based supplier of residential heating solutions. After years of growing organically and expanding their services and capabilities, they are now one of the nation’s largest MEP (mechanical/electrical/plumbing) building systems experts.
Today, Southland has 3,200 employees who serve most of the East and West Coast regions, as well as a Mountain West Division with offices in Tempe, Arizona and Las Vegas. The company’s capabilities encompass everything within each stage of the building lifecycle, including customized engineering, construction, building automation, service, and energy solutions.
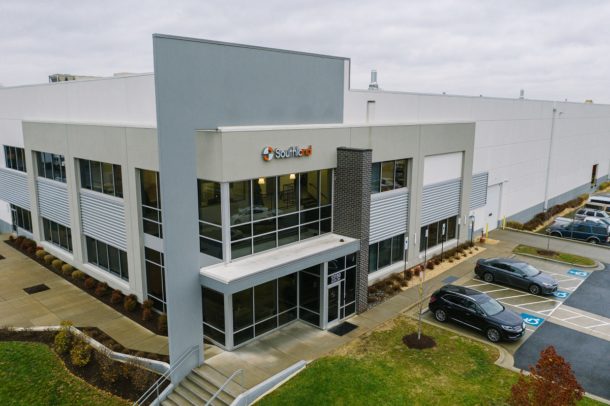
“When Southland expanded to the East Coast in the mid-1990s, we were the first true design-build contractor in the area,” explained J. Gilbert, Mid-Atlantic Division plumbing supervisor. Gilbert has been with the company for 12 years and has presided over substantial growth during his tenure.
“At that time, other installers had no choice but to hire outside professional firms for design and engineering work,” continued Gilbert. “We had that capability in-house, which really set us apart from the competition. We’re now one of the largest MEP firms in the country.”
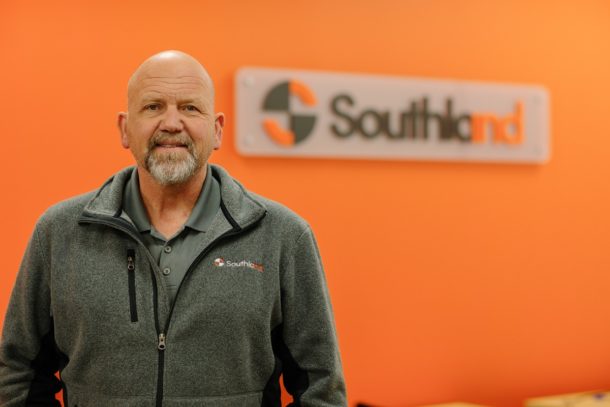
J. Gilbert, Mid-Atlantic Division plumbing supervisor.
According to Mike Dye, senior purchasing agent, much of Southland’s work in the Mid-Atlantic region includes government contracts, data centers, and pharmaceutical and educational customers. The company’s ability to bring every element of a project into consideration, including building automation and energy solutions, is a big advantage for large corporations and government agencies.
Professional plumbing
In 2017, Southland outgrew its existing offices and fabrication shop in Lorton, VA, and moved to a new facility in Laurel, MD.
The new facility, like all others owned by Southland, is a one-stop-shop for mechanical customers. The building’s 240,000 square feet is occupied by administrative offices, an engineering department, a sheet metal shop, mechanical piping (hydronic) fabrication space, plumbing, and a process piping area. It houses 100 union workers, including 30 plumbers.
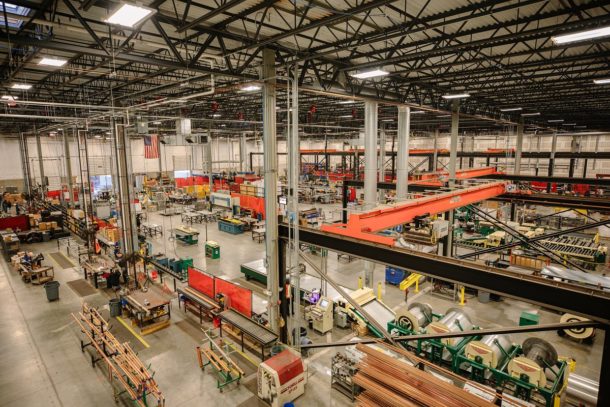
“Southland Industries pre-fabricates components for every single project we’re on, and plumbing pre-fabrication is no exception,” said Gilbert. “The ability to work in a controlled environment, minimize jobsite waste, and reduce onsite labor is a huge advantage.”
One of the company’s most frequently used plumbing products are commercial water closet carriers. As one would expect, they’re used on every job. Dye purchases hundreds each year through local manufacturer’s representative, The Joyce Agency, based in Chantilly, VA.
“The QT QuickTurn™ closet carrier is one of dozens of Watts products we source through Kevin Cerretani at The Joyce Agency,” said Gilbert. “Its design expedites both the prefabrication process here at the shop and the final installation in the field.”
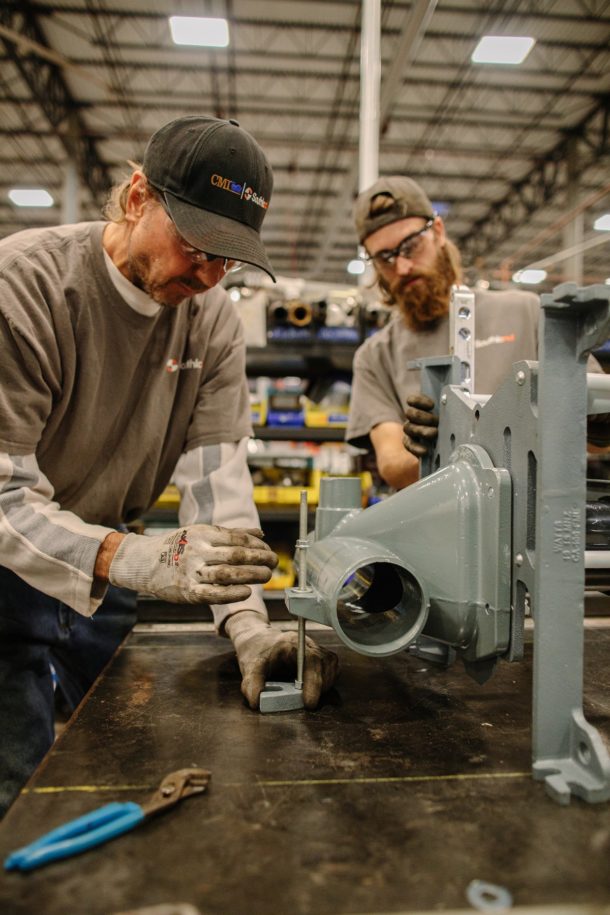
Plumber Joe Gencavage assembles many of the carrier systems in the fab shop. There, water supply, vent, and waste water piping is cut to length, attached to the carriers, and disassembled for later use in the field.
“The enamel finish on the QT QuickTurn carrier is great, as are the no-hub vent and wastewater connections and the dual threaded boss for supply water pipe support,” said Gencavage. “For install crews, the ability to adjust the face plate left and right makes the job easier. Same goes for the side-facing carrier support legs. It’s a nicely streamlined design.”
The new carrier system was one of several new products brought to Southland by The Joyce Agency in 2019.
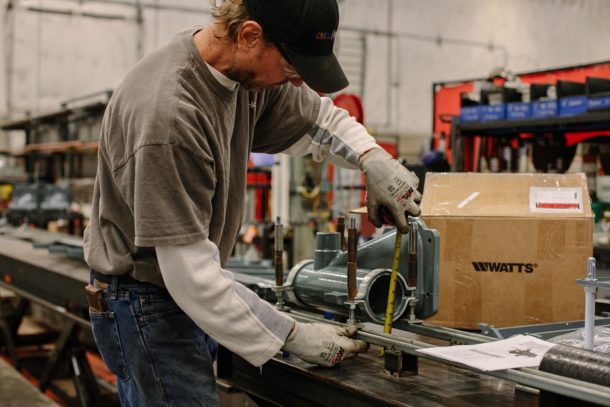
Partnered for growth
“We’ve had a strong relationship with Southland for 15 years,” said Cerretani, who’s been with The Joyce Agency for 29 years. “I think that has been one source of success for both companies.”
The Joyce Agency’s plumbing division provides pipe, water closet and lavatory carriers, drainage products, flush valves, plumbing fixtures, sinks, water coolers, electric tankless water heaters, safety equipment, steam components, acid waste piping and laboratory fixtures to Southland. The agency’s main facility in Chantilly has three divisions: plumbing, architectural products, and HVAC.
“We’re very happy with the Watts products and the breadth of their line, but one of the biggest advantages of buying Watts products for us comes through our relationship with The Joyce Agency,” said Gilbert. “We can count on them to get products to us in a timely manner and provide exceptional service.”
The Joyce Agency represented a different carrier line for 23 years, switching to Watts six years ago. Cerretani has found that many of the costly options offered by other manufacturers are standard features in the Watts line.
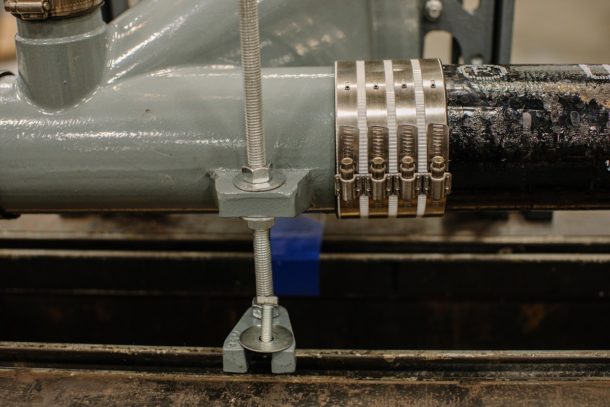
“The epoxy coating on the carriers is one example of a Watts standard feature,” said Cerretani. “Another feature we like on the QT QuickTurn is the O-ring seal and ABS nipple. Pushing the nipple into place is much faster than threading the nipple into place.”
“The true superstars in the supply chain are the folks in our quotations group, the commercial inside sales group, and our warehouse personnel,” continued Cerretani. We have an open line of communications with the folks at Southland to streamline the process of product selection, submittals, and providing the right material on time. I’m blessed to work with the professionals at Southland, as well as my Joyce Agency associates.”
“Watts and The Joyce Agency both really set themselves apart when it comes to customer service,” said Dye. “They’re the experts, and we lean on them both during the design phase and beyond.”
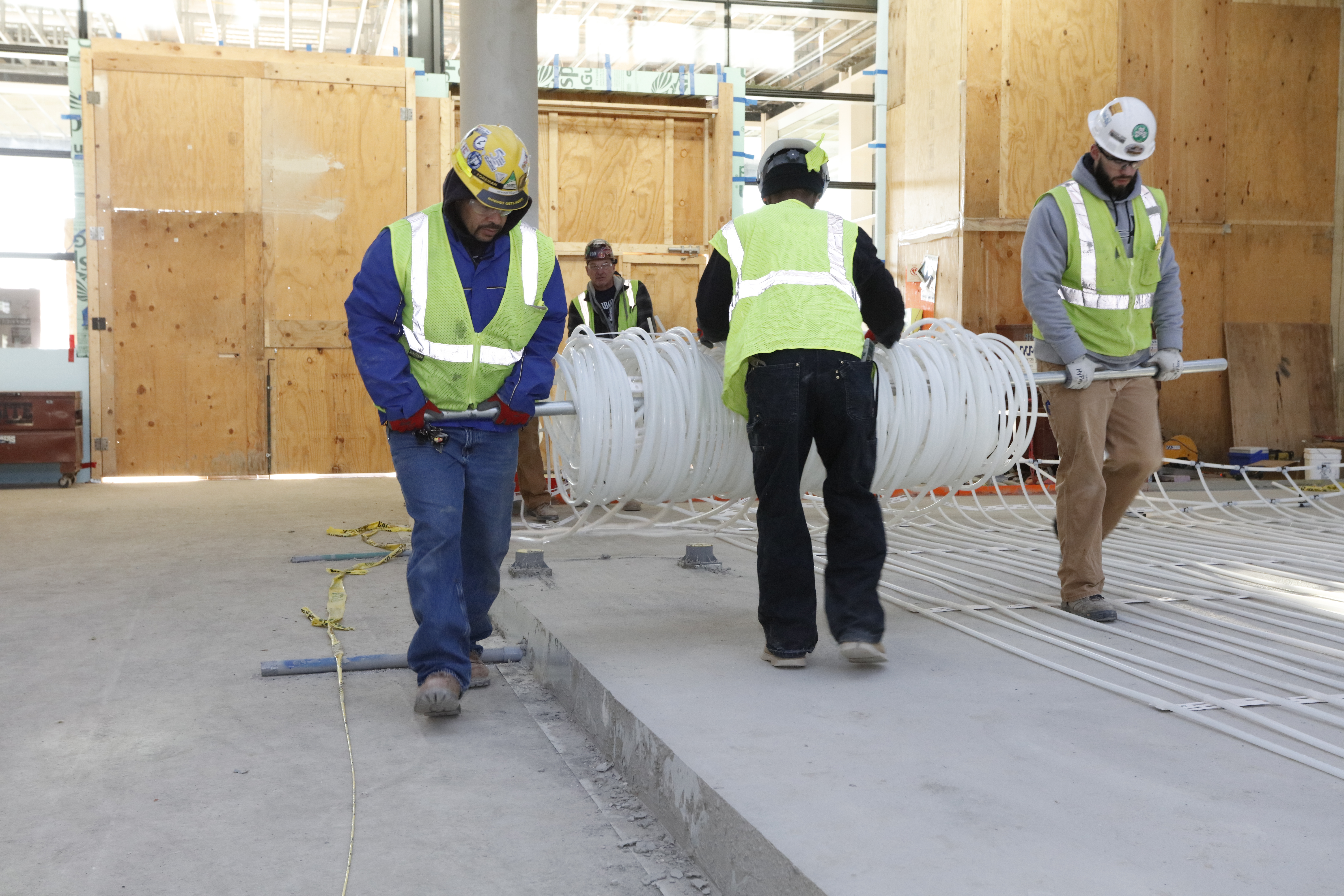
Designed by Lord Norman Foster of Britain along with architects from DLR Group | Westlake Reed Leskosky, the $515 million Health Education Campus for the Case Western Reserve University and Cleveland Clinic in Cleveland, Ohio, provides a state-of-the-art learning space to usher in a new era of teaching for medical, nursing, dental, physician assistant and Read more
Designed by Lord Norman Foster of Britain along with architects from DLR Group | Westlake Reed Leskosky, the $515 million Health Education Campus for the Case Western Reserve University and Cleveland Clinic in Cleveland, Ohio, provides a state-of-the-art learning space to usher in a new era of teaching for medical, nursing, dental, physician assistant and social work students.
The campus features a 485,000-square-foot Sheila and Eric Samson Pavilion and a 132,000-square-foot School of Dental Medicine to treat patients under the supervision of dental faculty. The pavilion features a 27,000-square-foot central atrium that draws maximum light from a specially engineered roof. It also includes a $5 million conference center with a 7,000-square-foot auditorium and a 4,800-square-foot lecture hall.
With all the expansive spaces and high ceilings, the buildings required a heating and cooling system that would provide exceptional comfort along with energy efficiency. To ensure occupants’ comfort and the buildings’ improved indoor environmental quality (IEQ), the design included a radiant heating and cooling system from Uponor, featuring Wirsbo hePEX™ pipe in a custom-designed, prefabricated network of Radiant Rollout™ Mats.
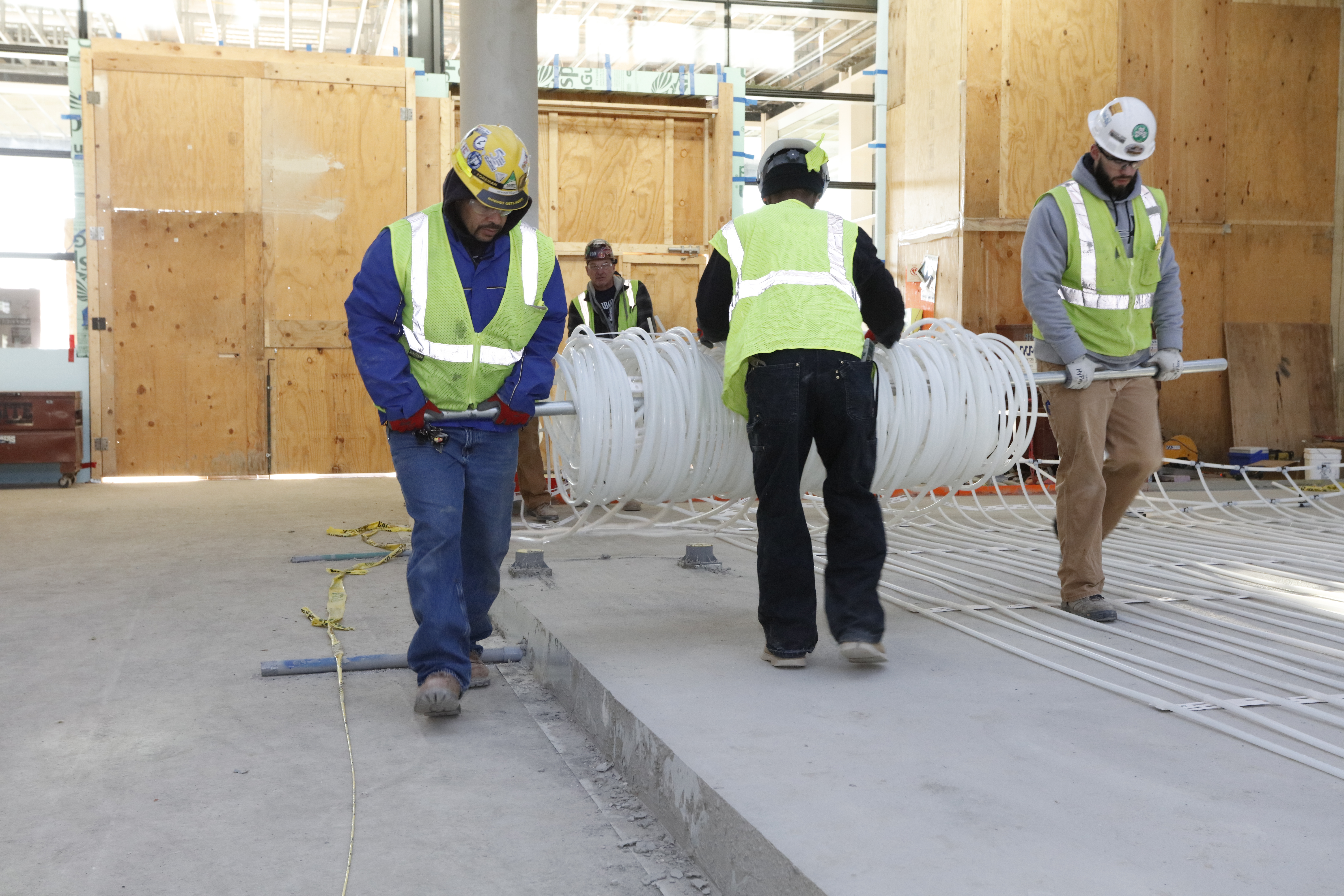
Cleveland Health Education Clinic, Ohio | Radiant floor heating install with Radiant Rollout Mats in 2018
Efficient installation solution saves time, reduces materials, and protects workers
Designed for large-scale radiant heating and cooling commercial projects, Radiant Rollout Mats provide faster, easier, more consistent radiant heating and cooling installations that can save up to 85% in installation time and add greater job-site safety for workers.
The mats arrive on the job site in large rolls that installers simply unroll and fasten to the concrete surface. The solution reduces wire ties and staples by up to 40%, which also limits bending, kneeling, and body strain for workers.
Already pre-pressurized at the factory, the mats have the option to include a reverse-return header, which can reduce required manifold ports by more than 60%. There is also the option to connect directly to traditional radiant manifolds to meet project specifications. The mats feature Wirsbo hePEX™ oxygen-barrier PEX pipe connected to ProPEX® engineered polymer (EP) fittings, which are safe for burial in the slab.
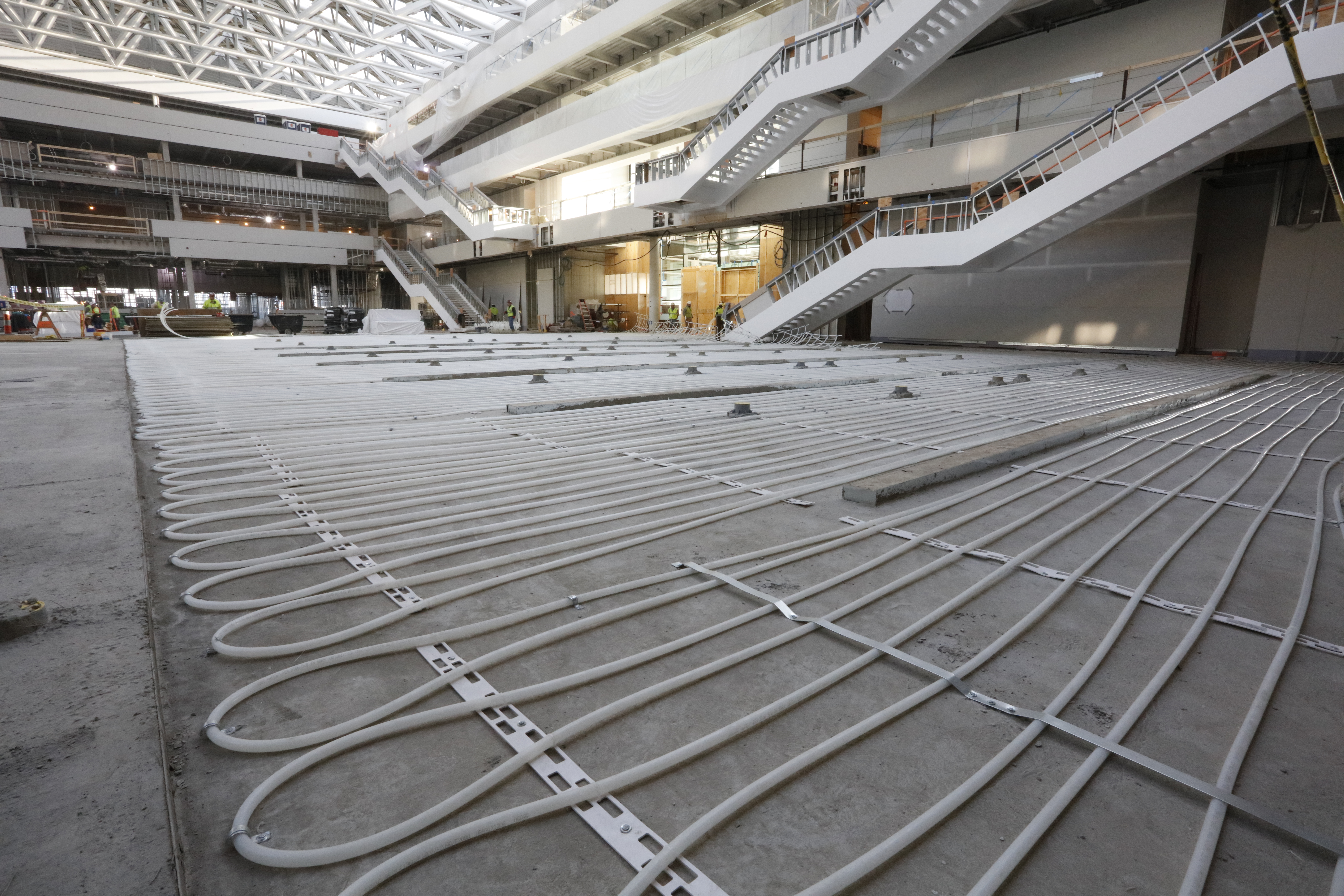
Cleveland Health Education Clinic, Ohio | Radiant floor heating install with Radiant Rollout Mats in 2018
Watch this time-lapse video to see how quickly installers were able to expedite the Wirsbo hePEX piping installation in the Health Education Campus project using the Radiant Rollout Mats, installing 55,860 lineal feet of pipe in just eight days.
With the faster installation, there was less impact to the concrete pour schedule, helping to keep the project on track, and workers were able to install easier with less strain on their bodies.
Healthier, more energy-efficient comfort with radiant
With a newfound focus on indoor environmental quality for commercial — and especially healthcare — buildings, radiant is quickly becoming the heating and cooling system of choice for large commercial structures.
For the end user, the radiant heating and cooling system provides greater comfort using less energy. That’s because the heat-transfer capacity of water in a hydronic radiant system is 3,500 times greater than air. Thus, a radiant system that uses a circulator to move water (in lieu of a fan to move air) can achieve the same heat transfer using significantly less energy. This means occupants are more comfortable and building owners benefit from lower energy costs.
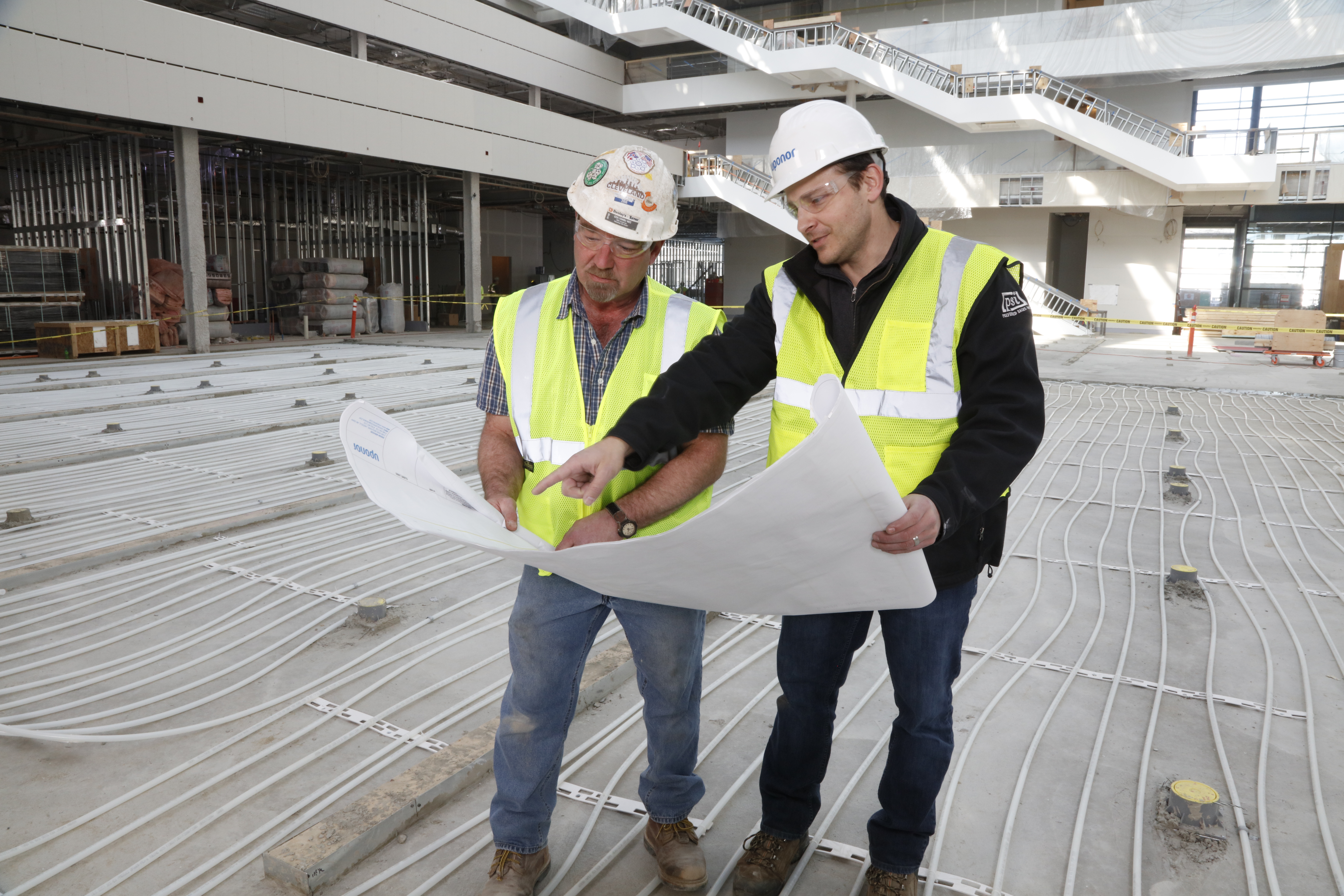
Cleveland Health Education Clinic; Ohio; Radiant floor heating install; Radiant Rollout Mats; RROM; 2018 install
Additionally, because hydronic radiant heating systems use pumps to move water instead of fans or blowers to push air, the system does not circulate viruses, allergens, or odors throughout the indoor space. This provides better indoor air quality, which is especially important in healthcare facilities.
Lastly, because radiant keeps the comfort near the floor where people are located, it provides an even, consistent temperature without hot or cold spots in a space. And, because radiant systems are designed in zones, it offers maximum occupant comfort control for each individual space — another important benefit for occupants in healthcare buildings.
To learn more about PEX piping solutions for healthcare applications, including domestic water, hydronic distribution, and radiant heating and cooling, visit uponor-usa.com/healthcare. To learn more about the benefits of radiant systems in commercial applications, visit the Uponor Commercial Radiant Solutions page.
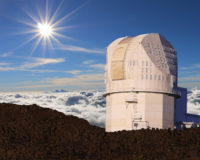
The National Science Foundation’s Daniel K. Inouye Solar Telescope in Maui, Hawaii, uses the largest mirror of any solar telescope in the world. Thanks to its 13-foot-wide mirror, it collects seven times more sunlight than any other solar telescope, producing the clearest, highest-resolution images ever taken of the sun. Not surprisingly, a solar telescope of Read more
The National Science Foundation’s Daniel K. Inouye Solar Telescope in Maui, Hawaii, uses the largest mirror of any solar telescope in the world. Thanks to its 13-foot-wide mirror, it collects seven times more sunlight than any other solar telescope, producing the clearest, highest-resolution images ever taken of the sun.
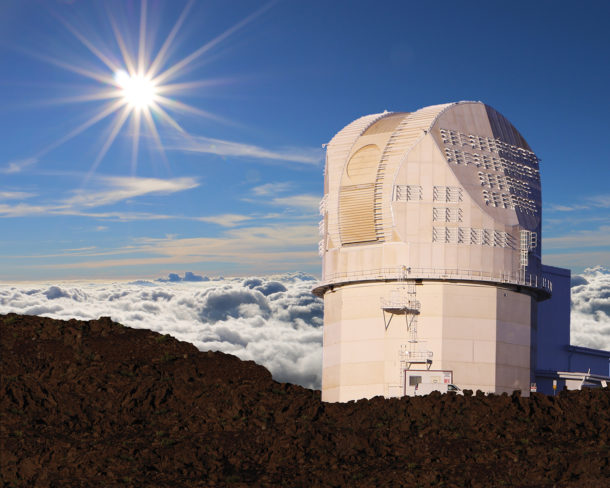
Photos courtesy of NSO/AURA/NSF
Not surprisingly, a solar telescope of this size produces a lot of heat. With a working lifespan of about 50 years – after more than two decades of planning by the National Solar Observatory and its partners – there is a lot that goes into keeping the telescope cooled so it can provide groundbreaking scientific insights.
And that’s where Viega comes to the table.
An enormous, unique project
Eventually, there will be more than seven miles of thermal piping within the telescope and support buildings, explained Lou Szabo, Facility Thermal Systems Site Coordinator for the National Solar Observatory. He spends his days helping to finish construction and commissioning the equipment that recently began collecting images of the sun.
Much of the piping was prefabricated years ago, as various parts of the facility and telescope were being built (construction has taken about 10 years). Traditional methods, mainly welding, were used. But then the project came to a crossroads.
“As the various science instruments are installed and other devices added to the telescope, the final piping needs to be completed or modified, and oftentimes in close proximity to optics or one-of-a-kind electronics that are worth millions of dollars – things that would take many years to reproduce if damaged,” Szabo said. “We can’t have any joining methods that use heat or fumes. It has to be a very clean process.
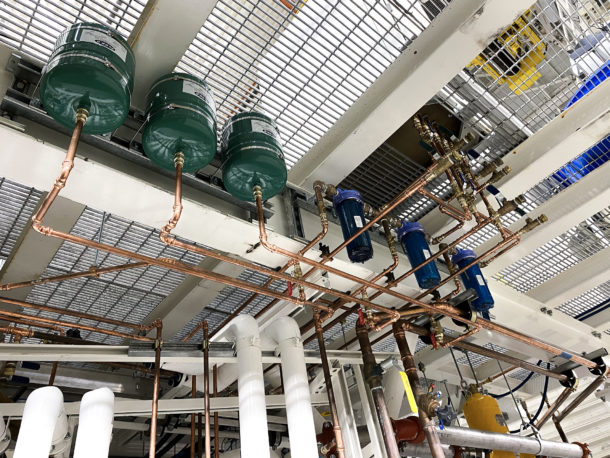
“The only way to install these remaining piping runs is with a joining system that meets the ‘no heat, no fumes, no dust’ requirements – and Viega hit that mark. We can go into these critical areas with very little equipment and complete press joints within inches of sensitive equipment, and the crews don’t have to worry about damaging it.”
As the need for a press-fitting solution surfaced, Szabo was already aware of Viega. He’s been in the piping trades for more than three decades and had previously used Viega.
He also knew that Viega had a large variety of fitting choices and, more importantly, offered plenty of technical support.
“When I presented the press system to the lead engineers and the decision-makers, I had to bring the best system I knew of,” he said. “Viega had been around the longest and had the best technical support if we had a question or got into a bind. We knew we had the reliability of the system behind us. It was really the only choice. I wouldn’t have been comfortable with others.”
Another factor to account for is the ozone conditions. The telescope is located at Haleakalā Observatories, at 10,000 feet in elevation, on the island of Maui. This location allows for great conditions for observing the sun but brings with it other unique elements, too.
“There is a high ozone content in the atmosphere here. Ozone was attacking a lot of rubbers and things, so we use HNBR sealing elements in all of our fittings,” Szabo said. “Some of the coolants we use are more exotic, and the HNBR holds up.”
The bulk of the coolant used is Dynalene HC20. The manufacturer lists both HNBR and EPDM as compatible materials, but the EPDM seal isn’t as resilient with the ozone presence, so Viega’s HNBR sealing elements are the right fit.
Inner workings of the telescope site
A series of primary loops come from the main mechanical/utility building, where all the chillers are located. The loops run to heat exchangers, followed by secondary and tertiary loops. There are dozens of pumps and tanks involved in the complex setup.
Piping in the system includes everything from 6” carbon steel piping to ½” copper tubing. Stainless steel is also used. The miles of piping run coolants and air to keep the telescope project at an appropriate temperature and to keep everything working smoothly. Viega ProPress fittings up to 3” in diameter and MegaPress fittings as large as 2” are used throughout the site.
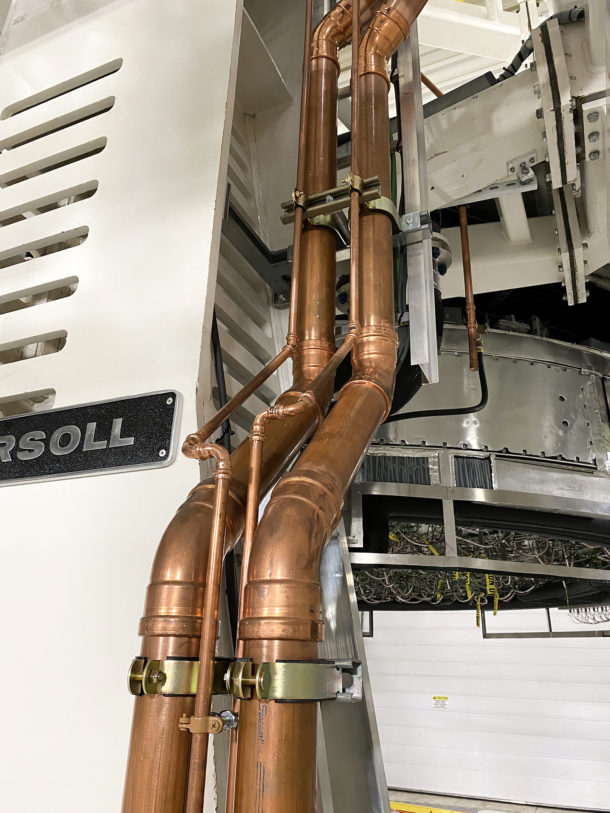
The mirrors and transfer optics are cooled in a variety of ways, including cooled liquid and air. For example, air a few degrees below ambient temperature is typically blown on the back of the mirror cells.
The Dynalene coolant runs at a very low temp, some as low as –2 degrees F, some around 45 degrees. The coolant is also environmentally friendly, which was important for the culturally sensitive site that carried with it many environmental guidelines. Propylene glycol mixtures are also used in some of the scientific chillers.
“A challenge we have in the middle of the Pacific is having fittings available, and that’s why we try to keep our setup as simple as we can,” Szabo said. “It’s also why we went with MegaPress and ProPress. Much of it is available on the islands, whereas other systems are more difficult to get.
“We try to keep a stock of certain fittings and materials on hand and stay ahead of the game. Oftentimes we’re looking at a two- to four-week lead time to get less-common fittings to the island. Thankfully our supplier, PACE Supply, can often get us common fittings within a couple of days.”
Szabo said they strive to keep the piping runs as simple as possible to both limit flow restriction and allow the use of standard elbows, adapters, tees and couplings, which are more readily available on the island.
One-of-a-kind solar research
Plans for the Inouye Solar Telescope (named for the late Daniel Inouye, the U.S. Senator from Hawaii who played a crucial role in getting finances approved for the project and was a big advocate of STEM and science) started 25 years ago. Dr. Claire Raftery, Head of Education, Outreach and Communication for the National Solar Observatory, said innovating how to build something so complicated – and then get it funded – was a massive undertaking.
There was an extensive survey done to determine the location of the telescope. A few hundred sites worldwide were reduced to a short list of 72, which was whittled down to a six. From there, only three met the specific requirements that scientists were looking for, and the location in Maui was chosen.
The Inouye Solar Telescope’s unique location combines clear and vivid blue skies needed to observe the faint corona of the sun with a high elevation and low air turbulence of the atmosphere above the telescope. Thanks to all these things, the telescope can produce the best images of the sun ever taken so that scientists can learn more about the dynamic star.
“We’re studying an object that there’s still a lot of mystery around. Many questions remain unanswered because we don’t yet have the capability to answer them,” Raftery said. “We need more detail, higher resolution – and these are things this telescope will bring to the table. It’s really a fortuitous time to be working in the solar physics industry.”
The telescope is expected to be operational for at least 44 years – four solar cycles – which is one of the benefits of ground-based astronomy, Raftery explained.
“We can expand the abilities of this project much longer than we could from space,” she said. “It’ll never really stop being finished. We can adapt and improve. The team will continue to bring new science experiments online through the life of the telescope.”
Part of the federal requirements from the National Science Foundation include returning the site back to the way it was found, so in 50 years they won’t simply turn off the lights and walk away, but instead the project will eventually be removed from the site after it has run its course.
But with that prospect decades into the future, for now everyone involved with the project is exhilarated as the telescope begins recording images of the sun.
“I remind the crews that they are the only ones in the entire world working on this unique system,” Szabo said. “This is truly a one-of-a-kind project.”