Commercial contractors in the mechanical, electrical and plumbing industry have been challenged by a shortage of skilled labor for several years. In the last 18 months, a perfect storm of unprecedented circumstances — among them are COVID-19, materials shortages, materials price increases and supply chain interruptions — has exacerbated the labor gap and pushed our Read more
Featured
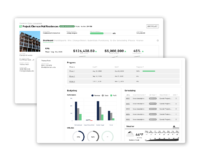
Commercial contractors in the mechanical, electrical and plumbing industry have been challenged by a shortage of skilled labor for several years. In the last 18 months, a perfect storm of unprecedented circumstances — among them are COVID-19, materials shortages, materials price increases and supply chain interruptions — has exacerbated the labor gap and pushed our industry into an ongoing state of crisis.
In addition to revealing deep structural vulnerabilities, the unforeseen difficulties of 2020 and 2021 have underscored the urgent need for commercial contractors to implement new efficiency strategies and processes in order to stay competitive. It’s more critical than ever that they find ways for their teams to operate more effectively and maximize productivity in order to shore up profit margins.
One of the top priorities throughout the industry is reducing the amount of time that team members spend on tedious, time-consuming tasks, freeing them to do the meaningful service work for which they’re trained and hired.
The specific needs of every contractor are different, depending on their company’s size, location, specialized focus and long-term goals. Nevertheless, a few proven strategies for streamlining and building efficiency apply throughout our industry and can, if implemented intentionally, make a noticeable difference in operations and show results for almost any contracting business.
Improve communication
Sounds easy, right? But teams working on commercial mechanical, electrical and plumbing projects face a host of obstacles to efficient communication. For contractors, maintaining effective open channels between jobsites and the office is a major ongoing challenge that creates friction and slows productivity. And since time is money, one of the simplest ways to increase profitability is get your communication processes down pat.
We know that an array of technology solutions are available to help field techs save time, reduce expenses, and generate more revenue. But they aren’t the only team members who can benefit from technology. Contractors whose technology investment is limited to an app for technicians could be missing a significant opportunity to increase their company’s productivity across the board.
Office staff plays a critical support role that makes field service calls possible. From scheduling and dispatch to sales, management and accounting, empowering the behind-the-scenes team to perform more efficiently and effectively is an essential component of any strategy for increasing revenue and supporting growth.
On top of that, the sheer number of stakeholders involved in a commercial project can complicate the flow of information, increasing the risk of delays, inaccuracy and cost overruns. Integrating an all-in-one system that connects field technicians, back-office staff, account managers, finance and accounting teams, owners, and customers fosters transparency and accountability, encourages faster decision-making and reduces errors, which all adds up to completing more jobs and staying under budget.
The best all-in-one operational software solutions for modern commercial contractors can help the average company save several hours of work a week, giving you and your team more time to focus on growth and increasing revenue opportunities.
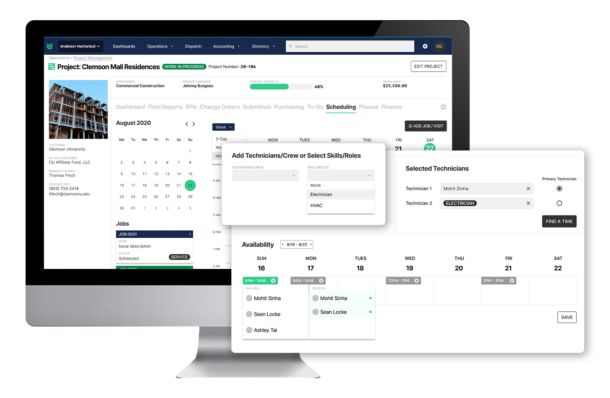
Streamline workflows
Guided and gated workflows help contractors develop standardized approaches for their field service teams for a variety of jobs and conditions. These automated workflows and associated benchmarks for performance contribute to operational efficiency across the board: techs can provide real-time information about every job at multiple points, building an internal knowledge base and full work history for each client.
Successful contractors are juggling multiple projects simultaneously. That can be difficult enough to manage, especially if you rely on manual processes. This can result in resource capacity shortages, scheduling conflicts, and missed deadlines. Pen and paper are dead; operational software can completely change the way your company gets work done. With software, all the essential information is organized in one place – all relevant data and information are just a few clicks away in one database that acts as your “single source of truth.”
With the right HVAC software in place, you can automate your operational processes, freeing up your employees to tackle more productive (and more lucrative) projects. For example, automated reporting makes it easy to measure productivity across the board, shining a spotlight on potential areas for improvement, while smart task lists and work queues make daily work prioritization a snap, so everyone can get right to work on the tasks that matter most. With project status always available at everyone’s fingertips, nobody wastes time manually checking on progress or sitting in meetings that are a waste of time.
Advanced field service management software provides sophisticated built-in automation for various tasks, including smart scheduling and dispatching, workforce and resource planning, live updates on field team status, and more. Integrated features combine quoting and invoicing, workflow management, asset tracking, and customer management, which allow for total visibility at a glance.
Crucially, these workflows enable the collection and analysis of critical job and customer data that empowers contractors to deliver best-in-class customer service and optimize operational efficiency.
Measure performance
Collecting data is the first step to making smart business decisions. Having the right data organized and accessible can supercharge a team’s productivity by providing key information about where your business stands in terms of costs, revenue, efficiencies, bottlenecks, and more so you can see how your crew is performing, which job types bring in the highest profit, and key areas for development (aka: your weakest link).
The top all-in-one platforms for our industry are designed to manage all your operations and deliver actionable data collected from all departments, customers, employees, and projects. All of this information is available in real-time, offering up-to-the-minute insights into any and all aspects of your business. There are endless possibilities for fast, accurate, accessible data and analysis that can improve performance and drive increased revenue and growth.
Using a reliable reporting system, commercial contractors can collect and understand the data they need to optimize their operational efficacy and ideally reach operational excellence. With in-depth insights into quotes, events, revenue, time, and maintenance, contractors can effectively identify bottlenecks and other issues. From there, they can take the necessary steps to eliminate those issues and get the most from their operations.
You hire your teams for their skill and experience. Every second they spend filling out paperwork or performing tedious data-entry tasks is a second when their value isn’t being realized. That’s frustrating for them — and expensive for you, especially during the current challenging economic climate. Reducing the amount of time that team members spend on tedious, time-consuming tasks and freeing them to do the meaningful service work they’re trained and hired for can distinguish the top service companies and position them for continued growth and success. The goal here is to achieve increased team morale, higher profit margins, and for business owners, a greater sense of confidence in scaling the business.
Author Bio: Alok Chanani is an entrepreneur who spent nearly a decade as the Founder/CEO of USA Commercial, a construction company that built apartment buildings in major cities across the US. During this time, Alok realized how innovative technology could change the lives of the specialty contractors he was working with and inspired him to launch an incredibly modern, robust software solution (what BuildOps is today). A former U.S. Army Captain, Alok served as an infantry platoon leader, combat engineer, and Unit Commander in Baghdad – spending a year moving large amounts of currency around Iraq. Alok has a BS from Cornell University, and an MBA in real estate from the Wharton School.
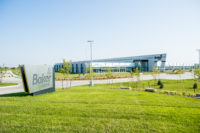
Conversations about the skilled labor shortage have become commonplace. And though high profile champions, like Mike Rowe, have given new visibility and importance to the looming challenge that threatens all trade professions nationwide, articles typically bemoan the lack of young people entering the trades while offering few solutions. The need for qualified technicians isn’t the Read more
Conversations about the skilled labor shortage have become commonplace. And though high profile champions, like Mike Rowe, have given new visibility and importance to the looming challenge that threatens all trade professions nationwide, articles typically bemoan the lack of young people entering the trades while offering few solutions.
The need for qualified technicians isn’t the only concern facing the trades, though. Others issues – such as quality of work and the time in which it’s completed – are as much a symptom of the first problem as they are challenges in their own right.
Many proactive, growing companies have squared off with the workforce shortage out of necessity, dealing it blows where they can. This often comes in the form of a bolstered recruiting game, or a train-your-own technician approach.
Local advocacy in high schools helps, too, though positive results come gradually as part of a longer-term effort. And, some companies implement systems and QC measures that help, to a degree at least.
If Baker Group, in Des Moines, IA, wasn’t already a mechanical force to be reckoned with over the past half century, this changed dramatically in early 2017.
Managers within the 650-person design-build firm, already intimately familiar with the advantages of prefabricating plumbing and mechanical systems offsite, made a bold move to expand their manufacturing space by nearly 150 percent. This, they say, has helped to solve several high-level concerns.

Baker Group is a 650-person, design-build mechanical firm in Des Moines, IA.
Manpower, quality, timeline
The decision to expand was made in order to produce higher quality products, in less time, without creating an unrealistic need for additional skilled manpower.
The firm’s new, 144,000 square-foot facility contains offices as well as manufacturing space, and is called Baker Group Advanced Manufacturing. As many as 75 craftsman can work during a single shift.
“We’ve done prefabrication work since the 1960s,” said Rob Cross, operations manager at Baker Group. “We added a large shop in 1998, and since then, we’ve steadily gained momentum. Our growth necessitated this new expansion last year.”
“The dynamic of the entire construction industry today is built on quality and speed,” says Tom Wengert, VP of Baker Group’s sheet metal business unit. “With this facility, we can prefab systems in a controlled environment, which improves quality while reducing labor costs.
“Additional benefits include increased safety, less congestion on construction sites, less jobsite trash and better scrap material recycling,” added Wengert.
While speed and quality are two major advantages to having a large manufacturing space at your disposal, the efficiency of off-site manufacturing means that fewer employees are needed to accomplish the same task.
Much of the in-shop sequencing implemented by Baker Group at the new facility was adapted from the automotive industry. For example, the flow of materials comes in west side of the shop and leave on the east side.
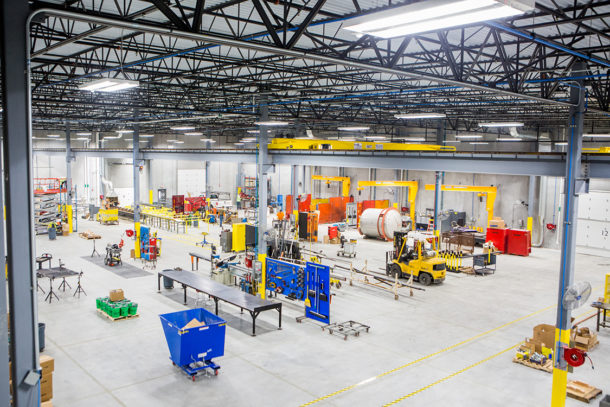
In 2017, Baker Group expanded their manufacturing space by 150 percent, or 144,000 square feet.
More than sheet metal
Completed in March of 2017, Baker Group Advanced Manufacturing includes 80,000 square-feet of fabrication space with almost 9,000 of that dedicated to multi-trade prefabrication alone.
The multi-trade space is located centrally among the sheet metal, piping and electrical shops. Here, trades work collaboratively in a weather-controlled environment to build to specifications and then ship to the job site.
The space features a 10-ton crane, allowing workers to construct large assemblies. By reducing on-jobsite time, this moves the entire construction timeline forward. The approach increases value to clients, and more than doubles Baker Group’s production capacity.
It’s in this centrally-located, multi-trade space that the various trades come together to assemble systems, sometimes even full mechanical penthouses. Welders work on framing and dunnage while pipefitters connect boilers, chillers, pumps and other equipment. Electricians wire the components and control technicians prepare everything to plug into a BAS.
“A good example of how we build to exact specifications in the shop can be seen in fabrication of gang restroom assemblies,” said Cross. “We can complete an eight-stall bathroom assembly in a little over a day, where it would take nearly a week onsite.”
Welders create an angle-iron framework, perfectly centering all the Watts closet carriers. Once assembled, the system is piped and hydro-tested. Waste water is also tested before the assembly is broken into several pieces for deliver to the job.
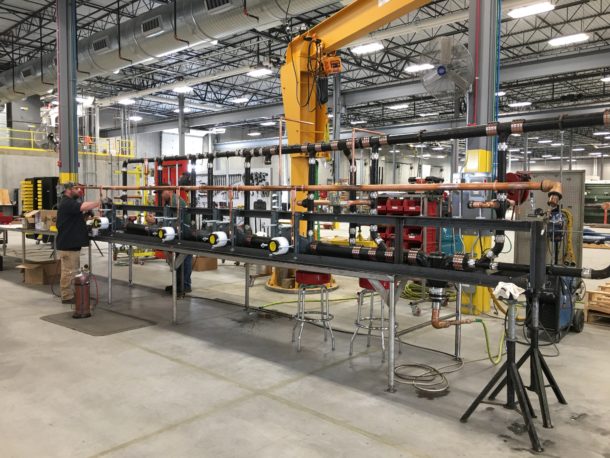
A Baker Group mechanic prefabricates large gang restroom assemblies at the new Advanced Manufacturing facility.
Baker Group has used the Watts back-to-back wall mounted, floor mounted and single closet carrier configurations for a wide variety of projects.
“We’ve standardized on the Watts carriers because the fab crews prefer them and they can be rapidly assembled,” said Cross. The Watts “industry standard closet carriers” come out of the box pre-assembled. The carriers feature a patented compression sealed nipple, which provides fast installation without the need for additional sealants. Adjustment is much easier than when threaded nipples are used.
“We never have any trouble with the closet carriers once they’re in the field, and the support we get from Jeff Howe, at Mack McClain & Associates – our manufacturer’s rep agency – is fantastic,” he continued
Cross has been with Baker Group for 23 years, and the relationship with rep firm Mack McClain goes back as long as he can remember. The firm supplies most of Baker Group’s plumbing components, including toilets, eyewash stations, backflow assemblies, drains and water heaters.
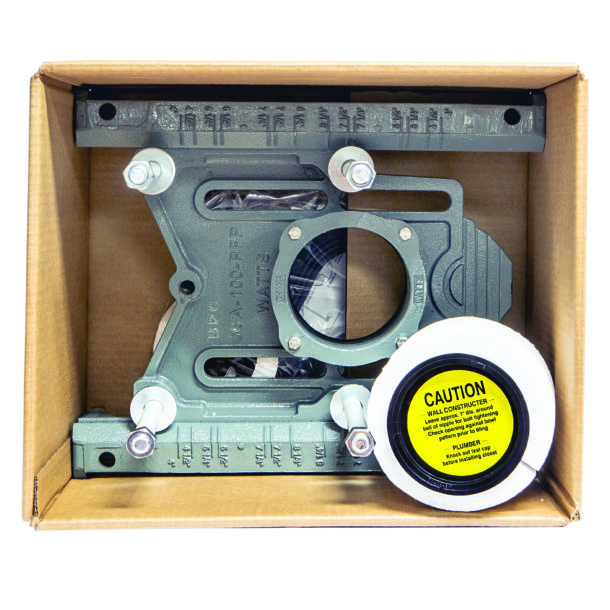
Baker Group has standardized on Watts closet carriers because the fab crews prefer them and they come out of the box pre-assembled.
Still adding capabilities
Toilet carriers aren’t the only plumbing systems that Baker Group prefabricates though. Like their ability to assemble boiler and chiller systems offsite, mechanics also build water service entrances, backflow assemblies, pump skids, pressure reducing stations and water purification systems. Once assembled, these items are broken down only as far as needed to be palletized, and the kits shipped to the jobsite.
“Every year we add something new to what we fabricate here on site,” Cross says, adding that Baker Group’s mechanical capabilities now include fabrication of ASME-rated vessels and components. “We’re equipped with the skills, knowledge, equipment and space to do this intricate and very strict code welding work.”
“Give us your biggest problem; the answer lies within the body of knowledge our people possess. We’ll find the solution,” he continued.
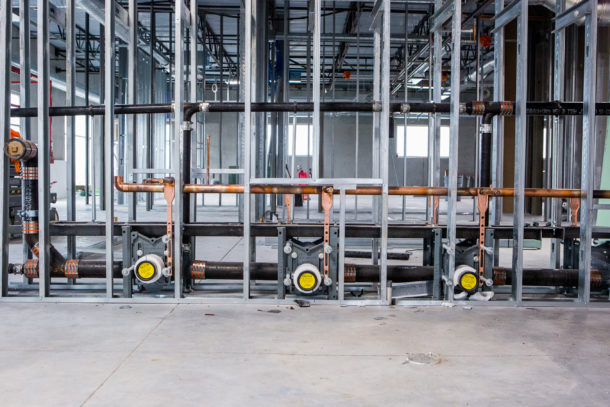
A premanufactured restroom assembly installed onsite.
Filling the new shop
While Baker Group Advanced Manufacturing allows the company to provide more capacity with reduced manpower, the need for new hires to fill the shop still requires ongoing effort.
“We’re a big local advocate for the trades,” said Cross. “We visit high schools and technical schools, invite people to take tours or do job shadowing programs. But we still can’t hire fast enough to fill the need.”
Baker Group is one of the largest, most capable design-build contractors in the Midwest, and they take that title seriously.
The content available on their website and YouTube channel speaks not only to potential clients, but also potential employees.
If the company’s dedication to recruiting parallels their insistence on delivering the best solution on time and on budget, staffing the new shop won’t be an unsurmountable task.
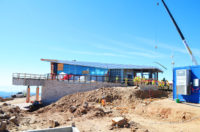
14,000-foot-elevation project uses ProPress The challenge of simply breathing at 14,000 feet in elevation, where the air is exceptionally thin, is tough enough. But add in the manual work done on a construction site, plus weather and Covid-19 precautions, and you’ve got a pretty challenging jobsite. This is exactly what crews from Olson Plumbing and Read more
14,000-foot-elevation project uses ProPress
The challenge of simply breathing at 14,000 feet in elevation, where the air is exceptionally thin, is tough enough. But add in the manual work done on a construction site, plus weather and Covid-19 precautions, and you’ve got a pretty challenging jobsite.
This is exactly what crews from Olson Plumbing and Heating dealt with on a recent project, the Pikes Peak Summit Complex, situated at 14,110 feet in elevation. Crew members who worked atop Pikes Peak in Colorado – at the highest ongoing construction site in North America – had to pass full physicals, were equipped with personal oxygen cans and watched each other closely.
“Any given day, you can almost guarantee that somebody on one of the crews – whether ours or someone else’s up there – would get altitude sickness,” said Dom Wilson, Field Foreman for Olson Plumbing and Heating. “We worked in the buddy system so you could recognize if your partner was not feeling well. What you think is a slight headache is really an attack of the altitude, and you need to get down to 11,000 feet and be evaluated by an EMT.”
The brand-new Summit Complex will replace the Summit House, built more than 60 years ago, and at 38,000 square feet, there was a lot involved with the new build. For contractors who had the ability, prefabrication of anything possible at a lower elevation was all but a necessity.
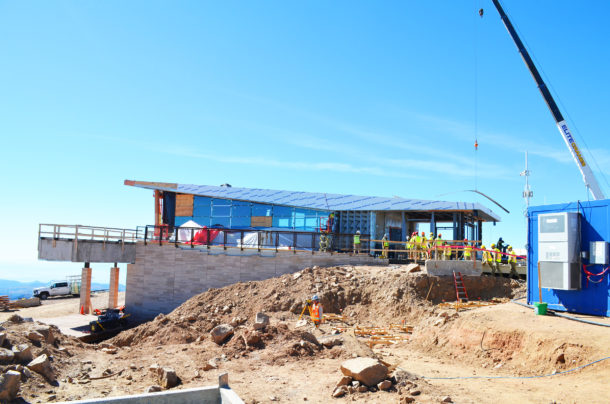
Enter Viega ProPress
The folks at Olson will tell you they use ProPress as often as possible, but using it on a job like the one, for “America’s Mountain,” was extra important. The ability to prefab so many of the pieces at their shop in Colorado Springs, and truck them up the mountain so there was less work to do at altitude, made perfect sense.
“We prefabbed all the domestic and hydronic piping, as much as we could, to minimize labor at the top,” said Josh Crippen, Superintendent at Olson. “We prefabbed our pump skids, all the water heater and boiler skids, all the waste and vent piping. As much as possible.”
Sections of pipe were then trucked up the mountain on special trailers purchased by the general contractor, GE Johnson Construction Company. Crippen said the trailers had movable axles to get through the switchbacks on the steep road to the top.
But before Olson could even think about putting together sections of pipe using ProPress, they first had to pass special specifications. The Summit Complex was constructed to meet The Living Building Challenge, which is one of the most rigorous proven performance standards for buildings.
Certain products are not accepted by the LBC, so there is a strenuous submittal process that Olson and the other subcontractors had to adhere to. Viega certifies many of its products, including ProPress, to the stringent LBC requirements.
Unique construction conditions
Work on the new Summit Complex began in 2018 when existing central utility plants were demolished and a temporary utility plant for blackwater was installed to keep the old Summit House operational during construction of the new building, about 100 feet away.
“Midsummer was a big race to get all of the in-floor heat in and get the foundation done and the building footprint excavated,” said Crippen. “We were really close – three weeks before the weather shut us down.
Regular Colorado weather, which can fluctuate from 30 to 70 degrees in a day, pales in comparison to the weather at the top of a fourteener (what Coloradans call the state’s 58 peaks that are 14,000 feet or higher) like Pikes Peak. While the temperature in Colorado Springs near the base of the mountain might be 30 degrees and sunny, the summit temperature is likely to be –20 degrees with howling winds and nothing to stop them.
And with such treacherous weather conditions, crews working at the summit had to always be on their toes. Crippen described spring and summer lightning storms as “unbelievable” and noted that if there’s lightning within 20 miles, everyone has to shelter in place to stay safe.
The added curveball of Covid-19 safety restrictions made things even more complicated. The logistics of getting everyone up the mountain safely, with vehicle capacities and mask requirements, was tough.
It was time for plumbing and piping in the summer of 2020, so that’s when the crews with Olson really got to work on-site. With a short window to get everything to the peak and in place, the clock was always ticking in the background.
Viega’s role
For the wastewater treatment facility at the summit, Viega ProPress Stainless connects the settling tanks and reclaimed water system. Blackwater is captured, treated through a chlorine UV light filter process and then – after about a year – the graywater can be reused to flush the toilets in the Summit Complex.
“This is not like your average gravity system for drainage!” said Crippen. “It’s a vacuum system like in an airplane or cruise ship. It’s part of the LBC and the green building, to be able to reuse materials. This build will be the first of its kind.”
There are settling tanks at the peak. Solids are pumped out to a truck (through copper with ProPress fittings) and taken down the mountain. The rest goes into other settling tanks where the treatment process begins.
Inside the Summit Complex are 37 water closets and 18 hand sinks. All of the bathroom facilities are serviced through copper with ProPress fittings. The entire building is heated from two electric boilers with 12 zones of in-floor heat, and the heating water is also supplied via ProPress.
The building has three sump pits to handle what Mother Nature provides, and that runoff water is pumped out through copper and ProPress as well.
Each year more than half a million people visit the summit of Pikes Peak. The new three-story Summit Complex will feature a large walkway as well as multimedia exhibits to tell the story and history of the mountain. These indoor and outdoor exhibits will also educate visitors about the climate and geography, recreational opportunities and conservation initiatives – like those of the LBC.
Final construction work was being completed at the Summit Complex in early 2021, with an anticipated open date of early summer 2021.
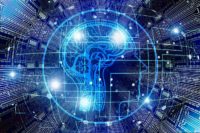
Engineering and construction (E&C) is one of the largest industries in the world, and yet, it has been one of the slowest to embrace digital change. The entire ecosystem represents 13% of global GDP, but the industry has seen meager productivity growth of 1% annually for the past two decades—and this is where disruptive technologies Read more
Engineering and construction (E&C) is one of the largest industries in the world, and yet, it has been one of the slowest to embrace digital change. The entire ecosystem represents 13% of global GDP, but the industry has seen meager productivity growth of 1% annually for the past two decades—and this is where disruptive technologies can make a difference. In 2021, construction contractors and engineering firms are starting to heavily invest in digital transformation to create new value across the entire supply chain and Kenny Ingram, VP of Engineering, Construction & Infrastructure at IFS, explains the four forces driving this shift.
According to an IDC study, digital transformation investment will increase to $6.8 trillion by 2023 as companies build on existing strategies and investments to become digital-at-scale future enterprises—and the E&C sector is no exception. Despite the global pandemic, the traditional brick-and-mortar industry is ready to enter the digital age—and an IFS study conducted in 2020 found that, despite regional differences, digital transformation spending among construction and engineering companies was surprisingly more robust than among companies from other industries.
Engineering and construction companies are now investing in disruptive technologies including building information management (BIM), artificial intelligence (AI), the internet of things (IoT) and innovative new mobile software solutions to replace legacy back-office systems and inject new value across the entire supply chain. According to McKinsey, E&C business are increasing productivity and value delivery, so they can outcompete their rivals, regardless of how quickly the market returns to or exceeds previous activity levels.
This digitalization of operational processes across engineering and construction companies is set to drive greater connectivity, and four key factors can be accredited for the increase in digital transformation investment.
Innovation in crisis – market changes require greater business adaptability
The E&C industry is particularly vulnerable to economic cycles—and the global economic changes caused by the COVID-19 pandemic has made digital investments more urgent, as companies try to find new ways to create and deliver value more efficiently.
Since the start of the pandemic, the industry’s traditional on-site workflows, which rely on paper trails and outdated communication methods, have not been able to mitigate the impact of lockdown and social distancing measures on construction activity. For instance, the RICS’ Global Construction Activity Index shows that 25% of projects have been put on hold, of which only 20% of projects on hold are expected to restart immediately with an average 131-day delay anticipated—costing projects, time and money. To combat the continuation of economic uncertainty, many companies are starting to realize that digital technologies provide the solution.
As E&C companies, particularly in North America, explore new ways to unlock operational efficiencies with reduced manpower, recent developments in 5G are having a significant impact on the industry. For instance, the network slicing capability of 5G enables data collection, capture and analysis to increase the visibility over the health, location, status and specifications of assets and projects. This can improve on-site monitoring to better inform decision-making across all stages of a project and minimize issues and changes during construction. 5G has the potential to create fully connected construction sites that can navigate the challenges of the current climate—and E&C companies are starting to respond with investment in cutting edge technologies.
Enhancing productivity with transformational technology
A separate McKinsey report found that firms which introduced digital systems for procurement, supply-chain management, better on-site operations and increased automation had improved productivity by 50% over firms that relied on analog solutions. Some of these transformational technologies include AR/VR, AI, IoT and machine learning, which according to the IFS study, will increase in importance in the next two years.
Construction projects are often impacted by time and cost overruns, but with this tech, companies can modernize each operational stage, from planning to execution. AR/VR, for instance, may already be helping companies deal with the challenges of project delivery during the pandemic by providing a dynamic format for BIM. In the field, the related technology of remote assistance is growing in popularity in field service settings like those a mechanical contractor may face in discharging maintenance agreements, or an EPCI contractor may encounter as they support projects in the field. Research indicates that this trend will continue as AR/VR is expected to become a key component in most construction projects within 10 years.
The digital workplace can make or break the employee experience
Given recent technological advancements and changes in consumer behavior, E&C companies are recognizing that digital technologies will help retain in-house expertise and play a crucial role in creating a more connected and engaged workplace. In fact, that 60% of enterprises will invest heavily in digitalizing the employee experience in 2021.
Across the supply chain, E&C companies traditionally operate in deeply entrenched business siloes, and survey data has shown that a large proportion of reworks are caused by miscommunication between teams. For instance, site workers will often not notify the supplier of any defective products, which means that on-site workers will need to either fix the products or wait for replacements—this can increase labor costs and create further projects delays.
This is where investment in digital technologies can create opportunities for greater collaboration and keep more projects on track and within budget. Cloud-connected mobile apps, for example, can be used to send feedback between teams and tag defects against specific elements in the BIM model before storing the information in a centralized data system. This input can significantly help companies reduce defects and the likelihood of unplanned rework—helping to improve operational efficiencies and the employee experience.
Industry sophistication is not a given, but country-dependent
Unlike other industries, most construction and engineering work is performed in-country and heavily influenced by cultural factors. This has led to stark regional differences in the degree of technological and business sophistication across the industry. In the UK for instance, government policy to improve construction productivity has led to heavy investment in building information management (BIM), while across the Atlantic there is no equivalent progress being made. According to a McKinsey report, economic value lost by the United States construction industry is the largest in the world at $58 billion versus $46 billion for all of Europe—and experts believe a lack of systems to effectively tackle the problems of the business is responsible for this variation.
Similarly, the adoption of modular or off-site construction across the industry is having a significant impact on how E&C companies invest in digital transformation. In this type of construction, companies rely on enterprise systems to reduce the cost and risk of projects, while increasing productivity, quality and safety. However, some countries have made further progress than others, particularly in the offsite building of new single-family homes. According to Boston Consulting Group research, only 2% of new homes in the United States were built offsite in comparison to 11% in the United Kingdom, and 20% in Germany and Japan respectively.
The digital roadmap for E&C is set and its incumbents must respond to thrive
The E&C industry, most notably in the United States, is well-known for its conservative stance on tech investment, but companies are starting to realize that this reality has the potential to compromise their future survival. Construction projects are increasing in both complexity and scale, and therefore require this sector to adopt new ways of thinking and working with digital technologies.
Construction and engineering companies that don’t take risks when it comes to their digital transformation and carry on as they are will cease to exist in five years. It is no longer a matter of if or when construction will be affected—change is already here and digital transformation investment is an essential component.
To take advantage of the increase in demand for construction services, E&C companies can no longer ignore the radical changes that are taking place within the industry. Digital technologies have become the new building blocks for optimizing operational efficiencies and securing competitive advantage—and this development is coming a lot more quickly due in part to the immediate demand and supply shocks of the pandemic.
AHR Expo Announces Open Call for the 2022 Innovation Awards; Entries Accepted through August 3, 2021
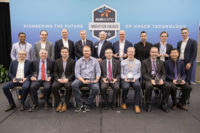
The AHR Expo (International Air-Conditioning, Heating, Refrigerating Exposition) 2022 Innovation Awards call for entries is now open. The annual competition, held in conjunction with the Show, honors the most innovative and original products, systems and technologies in HVACR. Exhibitors are encouraged to submit new or upgraded products to compete. Entries will be accepted through August Read more
The AHR Expo (International Air-Conditioning, Heating, Refrigerating Exposition) 2022 Innovation Awards call for entries is now open. The annual competition, held in conjunction with the Show, honors the most innovative and original products, systems and technologies in HVACR. Exhibitors are encouraged to submit new or upgraded products to compete. Entries will be accepted through August 3, 2021. The 2022 AHR Expo will be hosted at the Las Vegas Convention Center in Las Vegas, NV January 31 through February 2, 2022. To request more information about the Innovation Awards, or to receive forms for entry, please email Kim Pires at kpires@iecshows.com.
“First and foremost, we are thrilled to gather again in Las Vegas for the 2022 AHR Expo. Despite not coming together in 2021, we celebrated ten outstanding category winners and the Product of the Year, Infinitum Electric’s IEq,” said Mark Stevens, Manager of AHR Expo. “This competition celebrates the HVACR industry’s most innovative solutions through leadership in design, construction and execution. Each year we look forward to seeing the advancements in HVACR through the snapshot that the Innovation Awards provides. It is an excellent indicator of the exciting Show ahead.”
In 2003 the AHR Expo debuted the Innovation Awards as a means to highlight those in the HVACR industry creating innovative solutions for new and existing challenges and new avenues for growth. They aim to honor the most inventive, useful and original products, systems and technologies pushing boundaries and disrupting the market today.
Entries are evaluated by a panel of third-party ASHRAE members with over 20 years of professional engineering experience. The review process includes points tallied based on application, innovation, value and market impact. Winners are selected from ten industry categories, including: building automation; cooling; heating; indoor air quality; plumbing; refrigeration; software; sustainable solutions (formerly green building); tools and instruments; and ventilation. Winners and finalists demonstrating superior innovative design, creativity, application and performance will be recognized at the 2022 Show, on the AHR Expo website and social media channels, as well as in industry media coverage leading up to the Show.
An overall Product of the Year will be selected from the pool of category winners and will be announced at the Show. This prestigious honor is awarded based on exceptional leadership in HVACR innovation.
Eligibility and general information about the 2022 Innovation Awards
- The competition is open to exhibitors with a confirmed space contract, as well as a deposit payment on file for the 2022 AHR Expo.
- Eligible products include those that will be exhibited at the 2022 AHR Expo in Las Vegas and must be available for sale by January 2022.
- Exhibitors are permitted to submit one product per category.
- Product entries are limited to one product category.
- Products that have previously won an AHR Expo Innovation Award are not eligible, however, those products that have previously been named a category finalist may be re-entered.
- Completed entry forms, along with a non-refundable $100 entry fee, must be submitted by Tuesday, August, 3, 2021.
- One winner from each category will be selected. An overall Product of the Year award is selected from all category winners and announced at the 2022 Show.
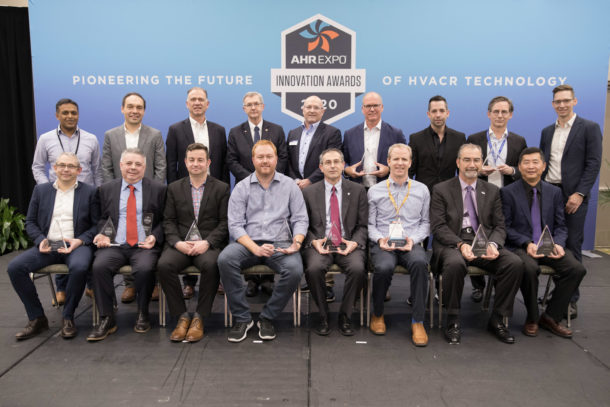
Entry fees for the 2022 Innovation Awards (approximately $20,000) will be donated to a charitable organization serving the local Las Vegas area community. The donation is generally used to provide HVACR repairs or upgrades. Each year, the AHR Expo works to select a charitable organization within the area where the Show is held.
“This past year has been a catalyst for new ways of thinking and adapting,” continued Stevens. “Our industry has risen to the challenge and provided critical solutions to help us move forward. HVACR is an area of exciting innovation on the global stage and we can’t wait to see what awaits us on the Show floor in Las Vegas.”
Registration for the 2022 AHR Expo is expected to open in July of 2021. Visit the AHR Expo website for updates and to sign up for the Show newsletter.
ABOUT THE AHR EXPO
The AHR Expo is the world’s premier HVACR event, attracting the most comprehensive gathering of industry professionals from around the globe each year. The Show provides a unique forum where manufacturers of all sizes and specialties, whether a major industry brand or innovative start-up, can come together to share ideas and showcase the future of HVACR technology under one roof. Since 1930, the AHR Expo has remained the industry’s best place for OEMs, engineers, contractors, facility operators, architects, educators and other industry professionals to explore the latest trends and applications and to cultivate mutually beneficial business relationships. The next Show, co-sponsored by ASHRAE and AHRI, will be held Jan. 31 – Feb. 2, 2022 in Las Vegas, and is held concurrently with ASHRAE’s Winter Conference.
For more information, visit ahrexpo.com and follow @ahrexpo on Twitter and Instagram.