Known as quick-connect, push-on or push-fit, these breakthrough plumbing products are often at the center of plucky online debates. Since entering the U.S. plumbing market in 2004, the design and technology of push-to-connect fittings have revolutionized the industry as a quick, reliable, tool-free solution for connecting small potable water pipes. Driven by feedback from plumbers Read more
Featured
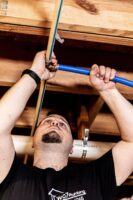
Known as quick-connect, push-on or push-fit, these breakthrough plumbing products are often at the center of plucky online debates. Since entering the U.S. plumbing market in 2004, the design and technology of push-to-connect fittings have revolutionized the industry as a quick, reliable, tool-free solution for connecting small potable water pipes. Driven by feedback from plumbers, this product class has evolved robust designs made of materials like rubber, silicon, brass and stainless steel, incorporating key components such as o-ring seals and gripping mechanisms.
But are they best used only as a temporary fix as some users claim, or can you count on them for a variety of long-term uses? We let the facts flow freely so you can make an informed decision on whether to give these fittings a try.
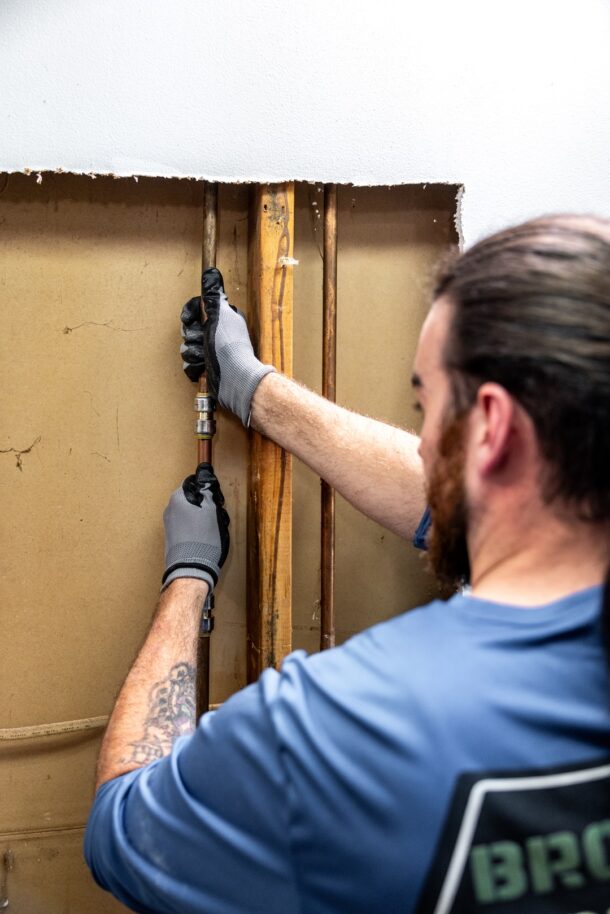
Rapid Adoption and Evolution
Two decades of innovation have made push-to-connect fittings indispensable for applications ranging from residential plumbing to advanced manufacturing. The most common uses are in residential service and repair, including some new builds. They went through a lead-free transition to newer models that are stronger and more durable, accelerating adoption further.
The American-made SharkBite Max model sets the industry standard with a stainless-steel retainer around the outside and a pressure rating of 250 psi. This doubled the burst pressure limit of the original model, the most popular push-to-connect fitting. A deeper insertion depth allows the new model’s steel teeth to engage the pipe more effectively, creating a stronger connection that eliminates the need for an interior tube liner.
Primary Benefits and Advantages of Push-to-Connect Fittings
Using push-on fittings means shorter installation times, fewer errors to correct, and easy, versatile disconnections and reconfigurations. No soldering, crimping, glue or special tools are needed for installation. Unlike conventional approaches, the pipe doesn’t need to be dry before making a connection. Water can be pouring out of a pipe and these fittings can still be quickly connected without a tool, even in a tight space, making them an excellent option for pipe repairs.
Knowing leaks and pipe aging are inevitable, it’s a good practice to keep some push-fit fittings handy. If it’s a failed joint pinhole leak, a push-to-connect fitting can be a fast, reliable and inexpensive solution, especially in areas where pipes are prone to freezing and bursting.
Other strengths of today’s push-fit models include:
- Perfect for transitioning between pipe materials, including copper, PVC, PEX, CPVC, PE-RT and HDPE (SDR-9)
- Fitting rotates around the pipe even after it’s connected
- Strong manufacturer warranties (SharkBite Max warranty is 25 years)
- Code approved to be buried underground (when wrapped in silicone tape) or installed behind walls
- Compliant with all regulatory changes
The simplicity and efficiency of push fittings have streamlined a handful of core plumbing tasks and even helped address labor shortages by making it easier to get new plumbers out in the field performing repairs quickly. They’ve also made basic and emergency plumbing repairs accessible to DIYers. However, despite their versatility, they’re not ideal for every situation.

Drawbacks, Limitations and Criticisms
Push fittings must be used in the right way to capitalize on their advantages. In the rare case when there’s a problem, installing them improperly or in a spot they’re not designed for is almost always the cause. By keeping a few points in mind, you can make the right decision every time on when and where to use them.
Here are the main things to consider for a smooth experience:
Initial Cost: The best push-to-connect fittings can be a bit pricier than soldering or crimping. You’ll save big on labor installing them faster, but the upfront cost per fitting can be higher.
Compatibility Limits: While leading push-fit fittings are compatible with almost all pipe types, they don’t work with everything, like galvanized steel or flexible hoses. And they still require specific fittings for certain transitions, like polybutylene to CTS tubing. This adds a step to some jobs and possibly to inventory management.
Not for All Applications: Standard push fittings are certified for potable water and radiant heating installations, limiting their use in industrial plumbing. Exceeding the certified limits (250 psi and 200°F for Max fittings) can lead to failures, so they’re not suitable for all high-pressure or high-temperature applications.
Designed for Single Use: While push-to-connect fittings can be removed if you need to adjust or test, they’re not designed to be reused multiple times in permanent installations. The integrity of the seal may be compromised with repeated removal and reinsertion.
Spotting Leaks: All push-to-connect fittings rely on o-rings for sealing. If the fitting isn’t installed correctly — such as failing to deburr the pipe — or gets jarred out of place inadvertently, the o-ring can get damaged, potentially leading to leaks. Although rare, leaks inside the fitting can be tougher to spot, so they might not be noticed immediately.
You’re best off choosing manufacturers that are transparent about the materials they use in their fittings, especially the o-rings since they keep the seal. For example, SharkBite Max o-rings are made of a specific type of rubber called EPDM (Ethylene Propylene Diene Monomer), chosen for its durability, flexibility and chemical resistance:
- EPDM is known for its resistance to aging and degradation, making it suitable for long-term plumbing applications
- It maintains its flexibility even at lower temperatures, ensuring a good seal
- EPDM is specifically selected for its resistance to chloramine, a disinfectant chemical often added to municipal water
Of these concerns, leaks are the most hotly debated. Some professionals still hesitate to use push-to-connect fittings behind walls because of concerns about long-term reliability and potential hidden leaks. But after two decades of continuous improvement and in-wall use by plumbers in homes and other buildings across America, these isolated instances can always be traced back to user error. Common causes of fitting failure include:
- Pipe that is unevenly cut, not deburred or not free of debris, potentially preventing a secure seal
- Using the wrong fitting for the wrong application
- Not marking the insertion depth to ensure that you pushed the pipe all the way into the fitting
- Not wrapping fittings in silicone tape that protects it from soil contaminants
- Rough or repeated disconnection
When it comes to quality, the widespread adoption of push-to-connect fittings speaks for itself. But don’t take anyone’s word for it. Test them out for yourself and you’ll see why they’ve become so popular with pros everywhere.
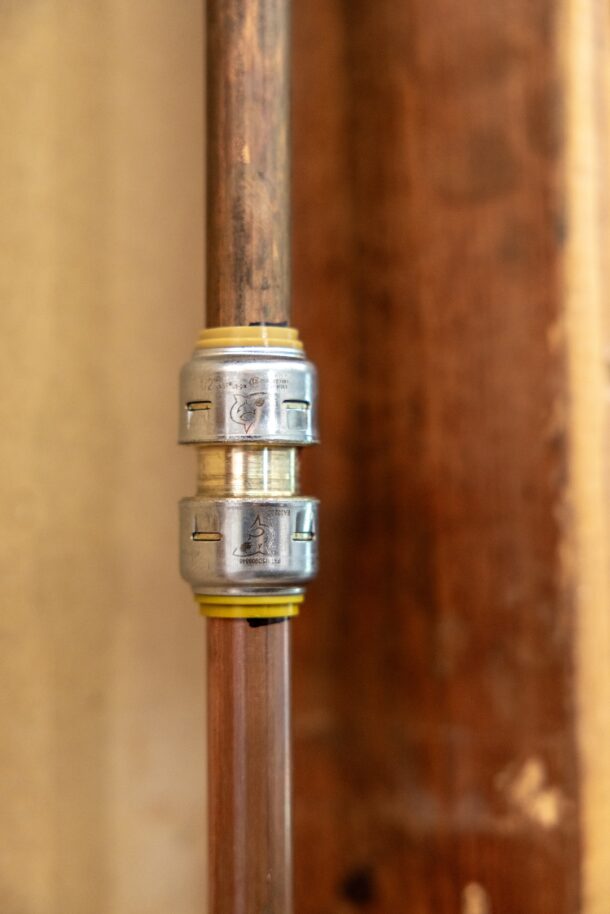
Plumbers Shape the Evolution of Push-to-Connect Technology
You can play a role in shaping this product’s evolution by sharing your thoughts and experiences directly with manufacturers. The best way to help drive the evolution of plumbing technology is for plumbers of all skill levels to share and connect online—post product reviews and reach out with comments and questions on social media or through company websites. Equipment manufacturers can serve you best when they hear from you often, and the most innovative tend to be more responsive to feedback.
Some manufacturers have employees who will share free resources like training materials and demonstrations to help plumbers integrate their game-changing products. If you ask nicely, they might even send someone to walk the job site with you when they can. Dropping the company a line on your favorite social channel is a great way to make another connection that’s built to last.
Written by Matt Glenn, senior product manager at RWC, a market leader and manufacturer of water control systems and plumbing solutions for residential, commercial and industrial applications.
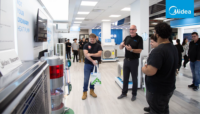
National HVAC Tech Day on June 22nd is the perfect time to acknowledge the dedicated HVAC technicians who work tirelessly to ensure our comfort, often in extreme conditions and challenging environments. This year, Midea, a leading innovator in air treatment solutions, is spotlighting its commitment to the future of the HVAC industry through recent and Read more
National HVAC Tech Day on June 22nd is the perfect time to acknowledge the dedicated HVAC technicians who work tirelessly to ensure our comfort, often in extreme conditions and challenging environments. This year, Midea, a leading innovator in air treatment solutions, is spotlighting its commitment to the future of the HVAC industry through recent and ongoing donations to trade schools and colleges, plus advanced training programs and partnerships aimed at promoting sustainability and technological innovation.
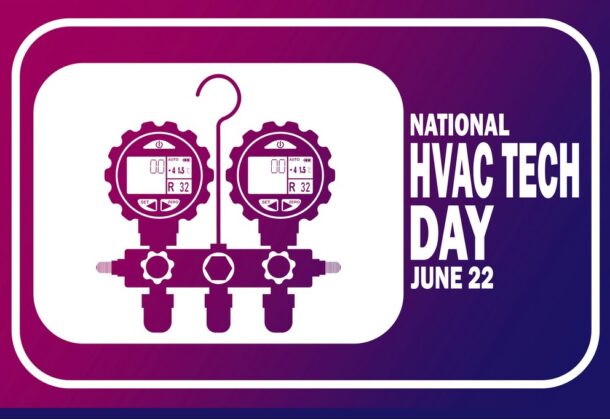
Supporting Career and Technical Education
Midea is dedicated to empowering the next generation of HVAC professionals by educating trade students and donating its advanced heat pump technology to organizations in need, such as the Midea EVOX Central Heat Pump/AHU system with auxiliary heater, Midea IN One-Way Cassette and Midea All Easy Pro High Wall systems.
Institutions like Prosser Career Academy, Chicago Builds, Remington College and Laredo College were exposed to Midea at the 2024 AHR Expo, where Midea participated in a workforce development panel and spoke to over 100 students about career opportunities for technicians and how the professional HVAC landscape is evolving. This initiative led to further collaboration between Midea and these institutions, which were impressed with Midea’s industry expertise and technical leadership. Realizing a need for modern heat pump technology in these training facilities, Midea donated its products at no cost. Now, the donated Midea systems will be used in Career and Technical Education (CTE) classes for installation training, Digital Multi-Meter training and visuals throughout multiple units.
Midea is also active on LinkedIn, posting educational content about its own technology and the industry at large, as well as highlighting its efforts to shape the next generation of HVAC technicians.
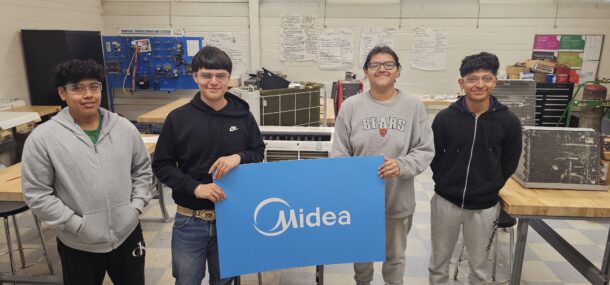
A Hub for Training and Education
One of the standout facilities that encapsulate Midea’s commitment to education and training is its flagship showroom, training and distribution center in Fresh Meadows, Queens. This facility serves as a dynamic hub for Midea’s sales, training and service operations. Here, contractors and consumers can interact with, learn about and purchase Midea’s full suite of advanced heat pump products. The showroom not only supports sales and installation services but also functions as an educational center, providing heat pump training, technical communications, consumer tours and collaborations with utilities with utilities like Con Edison and PSEG. Additionally, it serves as a meeting spot for architects, interior designers and Con Edison consultants to provide comprehensive consultation solutions for homeowners, solidifying Midea’s role as a leader in the HVAC industry.
The New York showroom hosts training classes almost every weekend that provide contractors with hands-on experience and professional knowledge about high-efficiency heat pump technology applications and installation, as well as regional home energy incentives. This ongoing commitment to training ensures that both new and seasoned HVAC professionals are well-versed in the latest advancements and best practices in the industry. The facility is also open to the public with on-site staff that can explain the technology and its benefits to the layperson.
Midea was recently honored as the designated brand for instruction at the largest professional training school in New York, the Electrical and HVAC/R Training Center. The program kicked off with a full-day training session at Midea’s showroom in Queens.
Midea was chosen for these initiatives due to its advanced heat pump technologies, comprehensive heat pump product line and active involvement in heat pump education. Midea’s cutting-edge products and commitment to advancing the industry make it a trusted partner for institutions and initiatives aiming to promote sustainable HVAC solutions. Midea’s active participation in public education efforts, including speeches at industry events like the AHR Expo and collaboration with various associations, further cements its position as a technical and thought leader in the heat pump industry that is rapidly growing and evolving.
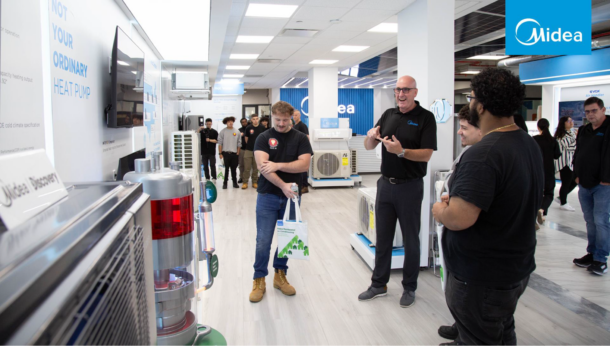
Industry Thought Leadership
Midea participates in key industry events such as the AHR Expo, the PSEG Electrify Long Island Conference and the Urban Future Lab event at NYU Tandon with a focus on supporting heat pump education and adoption. Midea’s leadership, including Senior Product Manager David Rames and CEO of Ai-Midea Air Conditioning Corp., Dr. Wenqing Zhang, have played key speaking roles showcasing the company’s technological advancements and role in technician training. These engagements provide a platform for Midea to promote its innovative products and to emphasize the importance of energy efficiency and sustainability in the HVAC industry in front of important industry figures.
Involvement in Industry Associations
The Midea America Research Center (MARC) team is actively involved in numerous associations that push and establish heat pump adoption standards, including ACCA (Air Conditioning Contractors of America), HARDI (Heating, Air-conditioning & Refrigeration Distributors International) and PHCC (Plumbing, Heating, Cooling Contractors Association). By contributing educational content for these organizations and exhibiting at their marquee events, Midea contributes to shaping industry standards and promoting the adoption of energy-efficient technologies.
Commitment to Sustainability and Innovation
Midea’s efforts extend beyond product innovation. The company actively participates in initiatives like the “Clean Heat for All Challenge,” in which it was chosen to provide 20,000 packaged window heat pump units to public housing facilities in New York City. This project supports New York’s Climate Leadership and Community Protection Act and aims to significantly reduce greenhouse gas emissions by 2030. Midea is also a member of the newly formed Heat Pump Action Team (HEAT), an EPA-led initiative that brings together heat pump manufacturers to promote the training, marketing, sales and promotion of heat pumps. Through these efforts, Midea is not only investing in cutting-edge technology but also supporting educational programs and empowering those who will keep our homes and businesses comfortable for years to come.

Celebrating HVAC Technicians
As we celebrate National HVAC Tech Day, let’s recognize the significant contributions of HVAC technicians. By investing in education, technology and sustainability, Midea is paving the way for a brighter, more efficient future in the HVAC industry.
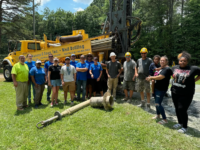
Partnership between Xylem, Chris Long Foundation’s Waterboys initiative and Water Well Trust brings clean water access to Goldston family Jessica Sales and her three children in Goldston, North Carolina, will have secure access to safe and reliable water next week, thanks to a recent collaborative effort. Xylem Inc., the Water Well Trust (WWT) and Waterboys Read more
Partnership between Xylem, Chris Long Foundation’s Waterboys initiative and Water Well Trust brings clean water access to Goldston family
Jessica Sales and her three children in Goldston, North Carolina, will have secure access to safe and reliable water next week, thanks to a recent collaborative effort. Xylem Inc., the Water Well Trust (WWT) and Waterboys – a charity initiative founded by two-time Super Bowl Champion, Chris Long – provided a comprehensive upgrade with all necessary equipment and installation for drilling a new well and building a pump house. Additionally, project partners contributed by installing a front door screen, placing pavers and planting flowers and shrubs. Local distributor Hughes Supply Pinehurst, well driller W.W. Maness & Sons Inc Well Drilling, pump installer Clearwater Solutions and the Vinyl Institute, which donated PVC piping material, all donated their time and services to complete the project.
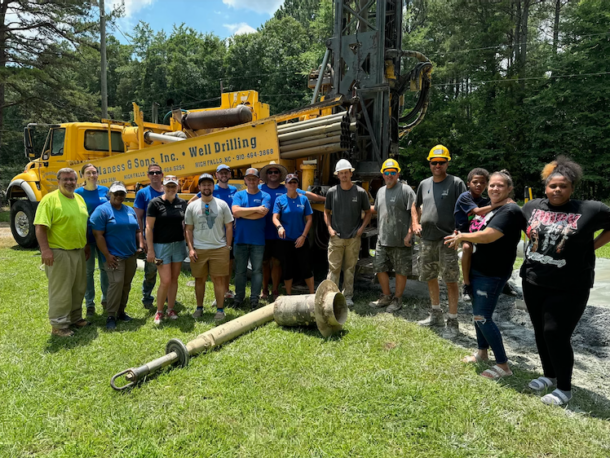
“Being involved in this project to provide the Sales family with reliable water access is incredibly meaningful for us. As a family business that’s been around since 1950, we take great pride in giving back to our community,” said Chris Maness, W.W. Maness & Sons Inc Well Drilling. “This project highlights the importance of ensuring that everyone has access to clean water, especially in areas where it can be difficult to find. We’re dedicated to using our expertise to make a positive impact. Having our entire team on-site ensures that we can get the job done right to support this family in need.”
Sales is a certified nursing assistant working at two hospitals and single mother of three. Prior to the well upgrades, she experienced a severe water shortage due to the failure of their home’s 38-year-old well, drilled in 1986. Despite multiple repairs, the well continued to run dry every morning since Sales first purchased the property in 2021. As a result, the family, including Devan (17), Asia (14) and Jayviann (6), struggled to meet their daily needs with only 30 jugs of water on hand, insufficient for basic hygiene and laundry. This crisis was especially challenging as one of Sales’ children has epilepsy, requiring consistent care, and making their life increasingly difficult without a reliable water source.
“After being in the house for a month or so, I started having issues with the water going out and the well running dry. My family and I have been struggling, sometimes having water and other times going weeks without it. We’ve had to rely on friends and family for basic needs like showering, laundry and washing dishes,” said Sales, WWT beneficiary. “The support from the Chris Long Foundation and partners is a tremendous blessing that has lifted a huge burden off our shoulders. We are incredibly grateful.”
The Sales family’s well upgrade marks the 17th HometownH2O project, an extension of its domestic water initiative working alongside WWT and Xylem to provide clean, sustainable water to communities in need. Water scarcity issues currently leave more than 2.2 million Americans without access to clean water, making this joint effort between Long, his Foundation’s Waterboys initiative and Xylem a vital resource for families across the country.
“Being on-site and witnessing the transformation that clean water access brings to the Sales family is truly inspiring. At Xylem, our mission is to solve water challenges and partnering with the Water Well Trust and the Chris Long Foundation’s Waterboys initiative enables us to do just that,” said Susan O’Grady, senior director of marketing, building services and agriculture, Xylem. “Seeing the relief and gratitude of the Sales family reinforces the importance of our work and motivates us to continue bringing sustainable water solutions to those in need.”
“Access to safe drinking water is a fundamental right that no family should have to go without. Our collaboration with Xylem, Water Well Trust and other partners on this project has been incredibly rewarding,” said Chris Long, founder of the Chris Long Foundation. “Seeing the positive impact it has on the Sales family reinforces our commitment to bringing lasting water solutions to those in need. Through our HometownH2O program, we are changing lives here at home, one well at a time.”
Xylem, in conjunction with its Goulds Water Technology brand, is engaged in regular water well initiatives to provide secure water access to rural areas, striving to increase public awareness of the challenges surrounding lack of water access. For more information about the Chris Long Foundation’s HometownH2O projects, visit waterboys.org/hometown.
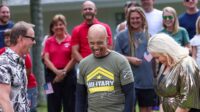
Service Experts is proud to announce their partnership with Military Makeover with Montel® on Lifetime TV. Military Makeover, a home improvement series, celebrates military families through home makeovers across the country. “We are grateful to play a small part in the meaningful work being completed by the Military Makeover team,” said Service Experts Chief Operating Read more
Service Experts is proud to announce their partnership with Military Makeover with Montel® on Lifetime TV. Military Makeover, a home improvement series, celebrates military families through home makeovers across the country.
“We are grateful to play a small part in the meaningful work being completed by the Military Makeover team,” said Service Experts Chief Operating Officer Cary Reed. “Many of our Service Experts employees are veterans themselves, and we are committed to supporting the military community through our ongoing partnerships with programs like Hiring Our Heroes. Being a part of the Military Makeover mission gives us another way to serve this community.”
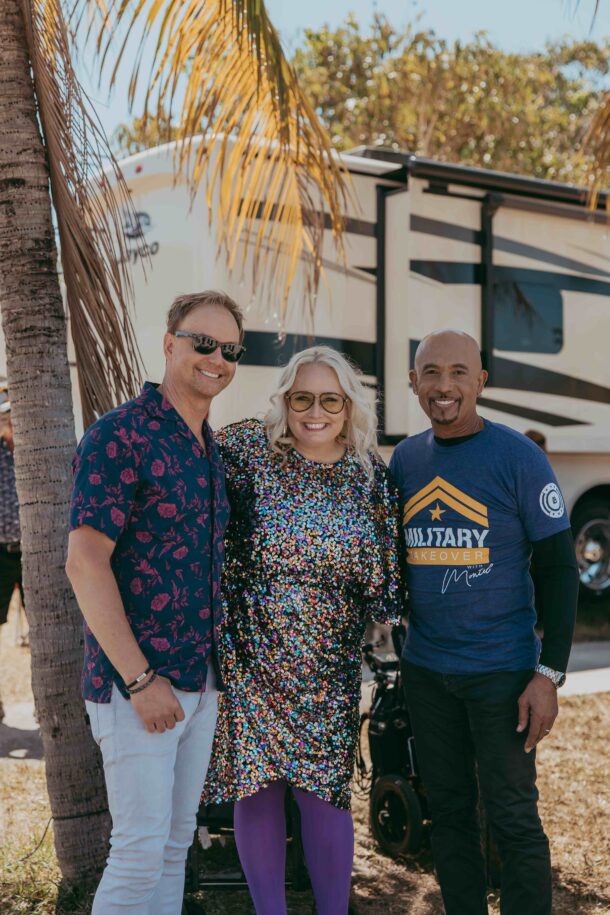
Military Makeover is led by talk show legend and military advocate Montel Williams, a veteran of both the Military Makeover with Montel. The show enlists conscientious designers, contractors, landscapers and other home improvement professionals to transform the homes and lives of military families across the country.
“We are thankful for the partnership of Service Experts and look forward to working with them to provide comfortable and safe homes,” said EVP of Programming, Jack Schwartz. “Their wide array of offerings will allow us to make these deserving families feel right at home.”
“For our part in the makeovers, we will be providing the families with anything they need to transform their home into a haven of comfort, well-being and energy efficiency,” said Reed. Service Experts, which has over with 98 locations across the country, is the leading provider of total home comfort in the U.S. HVAC installation and repair, plumbing, connected home automations and solar energy solutions are just a few of the services the company provides. “Our team will address each family’s individual needs to determine how we can help transform their home,” said Reed. “We look forward to giving this gift of total home comfort to these deserving families.”
Military Makeover with Montel® will premiere later this year on Lifetime TV.
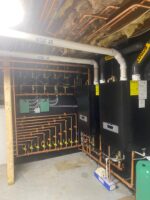
By Thomas Renner Any couple will tell you an enduring relationship depends on effective communication. So, too, do some home heating systems. Jeff Potvin came across this scenario in a project at a six-bedroom, 6-bath house in Andover, Mass. Potvin, the owner of Jeff Potvin Plumbing & Heating in Methuen, replaced two 150k BTU boilers Read more
By Thomas Renner
Any couple will tell you an enduring relationship depends on effective communication. So, too, do some home heating systems.
Jeff Potvin came across this scenario in a project at a six-bedroom, 6-bath house in Andover, Mass. Potvin, the owner of Jeff Potvin Plumbing & Heating in Methuen, replaced two 150k BTU boilers and a 75-gallon natural gas water heater. He chose two HTP Elite Ultra high efficiency condensing boilers as the alternative.
“The two new boilers will communicate with each other and increase efficiency, which will save the homeowner on his heating bill,’’ Potvin said.
No Ordinary Home
The residence where Potvin installed the boilers is no ordinary home. Built in 1954, the home is located in one of the state’s most historic towns just 20 miles north of Boston. The structure sits on 1.4 acres and extends across more than 7,800 square feet, including a sunroom, multiple fireplaces and is a mile away from Phillips Academy, a prestigious private high school. The school’s graduates include 2 former Presidents, George H.W. Bush and George W. Bush, Humphrey Bogart, Jack Lemmon and Bill Belichick, among others.
The challenge Potvin faced in the project was establishing communication between an outdoor sensor and the aquastat that were on air handlers to help reach the correct temperature. Aquastats are used in hydronic systems and adjust the temperature of the water in the boiler based on the outdoor temperature.
“We needed to move a few dip switches on the board to get it to work properly,’’ Potvin said.

The setup will increase efficiency and save the homeowner money on monthly heating bills. It will also heat domestic hot water and keep the home at a better temperature.
Project scope
The units provide hot water and heat for the home. Potvin said it is unusual, however, to replace three heating elements and get the same firepower with just two.
“It is unusual to change a water heater to a storage tank,’’ he said. “We completed the job during the summer, so no heat was needed.”
But the homeowner should realize some important benefits, according to Potvin.
“The two new boilers communicate with each other and increase efficiency,’’ Potvin said. “That will save the homeowner with the heating bill. The boilers have a larger BTU and will heat up faster and more efficiently. It will heat domestic hot water and keep the home at a better temperature.”
An Elite Solution
Potvin chose the HTP Elite Ultra boilers for other projects and knew it would be a good fit for this application.
The calling card for the Elite Ultra is a proprietary heat exchanger. The XtraTech Durable Stainless Steel Heating Technology exchanger ensures maximum quality at the heart of the boiler and resists corrosion to guarantee reliability for years.
The design provides increase in water flow, which creates more internal turbulence, scrubs the internal walls and reduces heat exchanger deposits to ensure a longer life span for the boiler.
Deposit buildup is a major problem in boiler operation. Scale and sludge deposits in boilers impede heat transfer, which leads to higher energy costs and can cause a loss of equipment operation and premature failure.
Boiler deposits can include calcium, magnesium, iron, copper, aluminum and others. Water treatment options can help reduce scale buildup, but those annual expenses can reach between $1,000-$2,000. Annual maintenance on the boiler will also help, but service calls can also reach more than $600.
The pipe surface on the Elite Ultra is up to 150 percent larger than conventional designs and ensures extremely low pressure water pressure drop. “The heat exchanger guards against corrosion and guarantees a long lifetime for the boiler with less maintenance,’’ Potvin said.
The boiler has a 10:1 turndown ratio that limits short cycling and provides more efficient energy consumption. The boilers rated thermal efficiency is among the highest in the industry at 96%. Adding the outdoor sensor provides the opportunity to increase that efficiency by reducing the delivered water temperatures to match the load based on outdoor temperature. This feature allows homeowners to save even more money on their monthly energy bills.
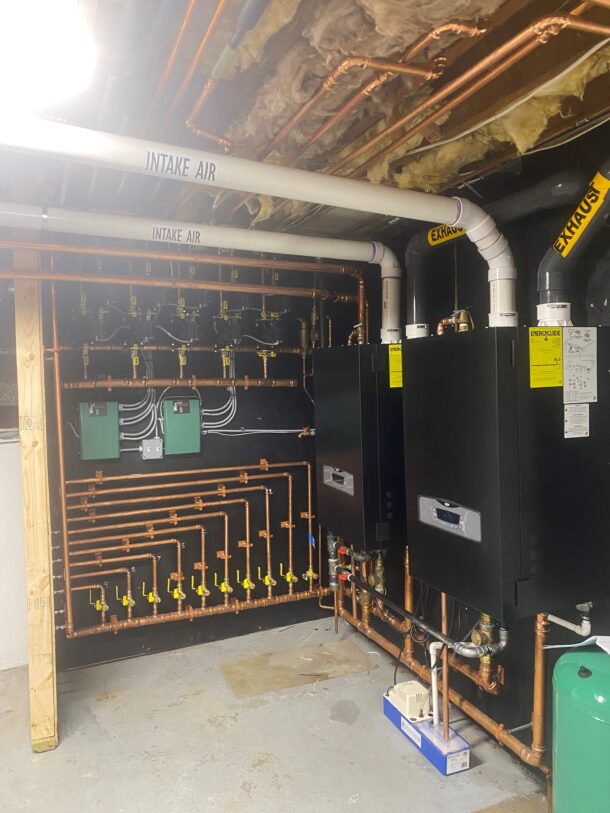
Two HTP Elite Ultra high efficiency boilers were installed in a Massachusetts home by Jeff Potvin Plumbing & Heating. The boilers replaced two 150K BTU boilers and a 75-gallon natural gas water heater.
Additional Advantages
The boiler also offers whisper-quite operation and an HTP Link that lets the homeowner control boiler operation from anywhere. With the link, homeowners can view boiler parameters and status, receive boiler text and e-mail updates, and access the unit and troubleshoot issues without having to be onsite, as long as the unit is connected to Wi-Fi and registered.
“We have used these HTP products in the past found it to be a great product,’’ Potvin said. “We also found tech support to be very good.”
Home and hot water heating can be especially challenging in Massachusetts, where temperatures fluctuate wildly from season to season, and sometimes daily during transitional periods. Having an efficient system on a large residence will generate considerable savings for the homeowner.
“Projects such as this can be challenging to find the proper solution,’’ Potvin said. “We think the homeowner will be quite satisfied with this product for years to come.”
Thomas Renner writes on building, construction, engineering and other trade industry topics for publications throughout the United States and Canada.