The word separation was being used in hydronic circles back when I started in the business. Of course, I am old, so there is that. Many manufacturers and trainers are in the separation bandwagon now, rightfully so, from my view. Let’s take a look of how the word and the technology come together. The action of moving of being moved apart will work to describe the value of separation in hydronics or piping systems in general.
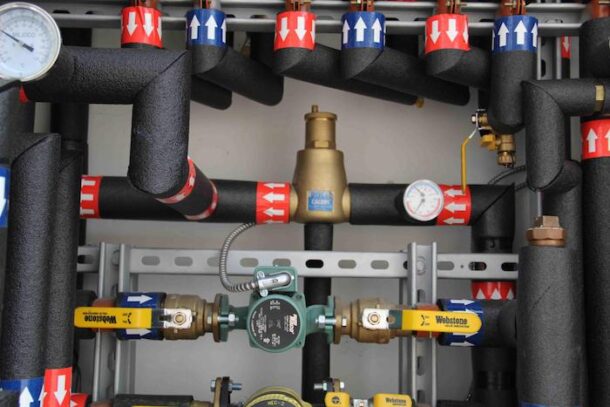
Photo: Bayshore House (Newport Beach, CA) Submitted by: David Mayo
Back in the day, we used a device called an air purger. We’ve all seen them, sometimes described as a camel hump. Commonly made from a casting, the “air purger” basically builds a wide spot in the road. As such, as fluid flows through it, the speed or velocity slows. Slowing the fluid allows air to rise up to the top of the “hump” to be vented away. It can, and does, some air removal in a system. A few important details. It likes to have some straight piping upstream, maybe 18” or so. This helps get the air going to where it can best be removed, at the top of the piping.
The velocity or speed is also critical. Water or fluids, flowing above 4 fps feet per second, tend to blow through the camel hump like bad leaves in the desert. Lastly, they have a tougher go grabbing the micro bubbles. If you fill a glass at the kitchen sink and notice cloudy water at first, those are micro bubbles. In your glass, since the top is open, this air escapes. It escapes quickly as the pressure has been taken off the fluid form when it was captive in the piping under 60 psi, or some pressure.
Some smart fellow decided there must be a better way to rid 95% or more of all air out of a closed loop piping system. The wide spot in the road had validity. Why not put something inside that wide spot to aid the collection. The microbubble resorber was born. The “stuff” in the chamber becomes a coalescing media. Simply the air bubbles, of all sizes cling to the media inside instead of blowing through like grass through a goose.
The concept works amazing well. Air can be successfully removed in a matter of minutes or hours on larger systems as it passes across the coalescing media. The microbubbles that were present in systems with camel humps, now have been captured and removed.
View this post on Instagram
Why all of a sudden is this so “in Vogue”? High efficiency boilers are one great reason to use microbubblers. The fluid content is way down, the HX metals are much thinner, and the flame is in close proximity to the boiler wall. As such, any layer of micro bubbles stuck on the metal surfaces reduce or impede the energy from the flame getting to the fluid. You have a miniature bubble wrap layer around the boiler surfaces if you are not getting the small air gone.
You may have seen failed mod con boilers. Darkened, brown or black metal instead of shiny stainless or aluminum. That HX has been overheated. Often lack of flow is to blame. And also, often the lack of flow is related to air bubbles slowing or stopping the perfect contract between fluid and hot metal surface. You take an efficiency hit also when you have this going on in your boilers. Circulators, the wet rotor type, especially like to be free of air, both from a performance and lubrication standpoint.
So, doesn’t it make sense that the same phenomena happen in your heat emitters? Microbubble air layers in your radiators, fin tube, air handler coil, coil in your indirect tanks.
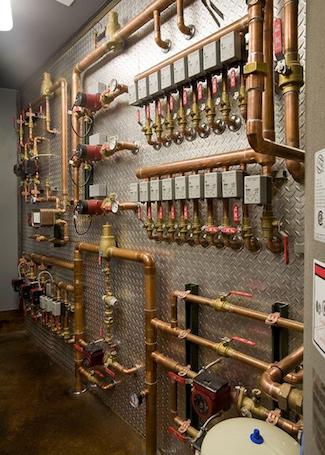
Telluride Custom Home (Telluride, CO) Submitted by: Pete Cassidy
The microbubble resorbers aka air separators bring a few other advantages. They do not require straight piping upstream to work efficiently. This can be a big asset when you need to cram 10 lbs. of potatoes in a 1-pound sack, i.e., small mechanical closets. They are not as sensitive to over-pumped conditions, high velocities above 4 fps for example. The large chamber combined with the media inside work together to grab bubbles from speeding fluids. They are brass or composite construction, so corrosion issues are mitigated. Ever see a camel hump with the air vent port rusted close when you pull the 1/8 auto vent off the top? It was handicapped from first installation; the plugged vent hole renders it a “boat anchor.”
Yeah, I know they cost more than a chunk of iron than your great grandfather used his entire career, but times have change, my friends. Why not give your customers a system with the very best equipment and conditions to be highly efficienct. A simple device that removes 95% of air in systems almost instantly is what you need to consider.
So, you took my suggestion and STILL have an air/ noisy system. Now what? Look for places where air is getting in. Yes, air can enter a closed loop system, even a pressurized one. Those float type auto air vents allow air to move in both directions, in and out. IF one were to be installed in a point in the system that sees sub-atmospheric conditions you are seeping air into the loop. The most common occurrence is when you have the expansion tank misplaced. This can get worse with high heads circulators creating large pressure differential. The tank MUST be on or near the suction side of the circulator(s) to avoid pulling a vacuum in your system. Make it right or cap off auto vents in the negative pressure part of the system.