Managing a construction fleet involves a unique set of challenges that can significantly impact efficiency, cost and project timelines. From dealing with equipment downtime to navigating complex compliance requirements, fleet managers in the construction industry face numerous hurdles. Understanding these pain points can help professional tradesmen optimize their fleet operations and improve overall job site productivity. Here, we explore the top pain points for construction fleets and offer insights into addressing these issues.
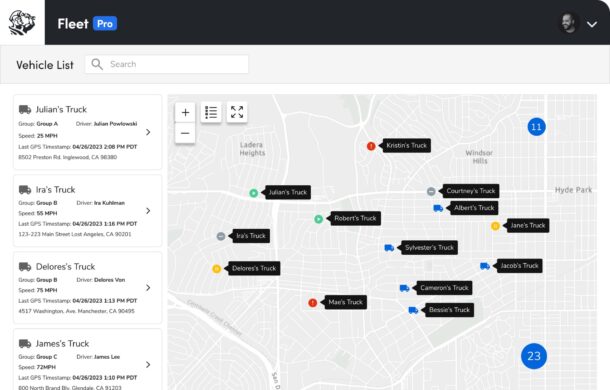
Equipment Downtime
One of the most critical challenges for construction fleets is equipment downtime. When machinery breaks down or is unavailable, it can halt projects, leading to delays and increased costs. Several factors contribute to equipment downtime:
- Maintenance Issues: Regular maintenance is essential, but unexpected breakdowns still occur. Without a proactive maintenance schedule, minor issues can escalate into significant problems, leading to prolonged downtime.
- Lack of Spare Parts: Delays in obtaining necessary spare parts can extend the time equipment is out of service.
- Operator Error: Inadequate training or operator mistakes can lead to equipment damage and downtime.
To mitigate these issues, fleet managers should implement a robust preventive maintenance program, ensure a steady supply of spare parts, and invest in comprehensive training for equipment operators. Using asset maintenance software can also streamline these processes and reduce downtime.
Rising Maintenance Costs
Maintenance costs for construction fleets are on the rise due to several factors, including:
- Aging Equipment: Older machinery often requires more frequent and costly repairs.
- Complex Technology: Modern construction equipment comes with advanced technology, which, while improving efficiency, also increases the complexity and cost of maintenance.
- Labor Costs: Skilled technicians are needed to perform maintenance, and their labor costs are rising.
Fleet managers can address rising maintenance costs by strategically planning equipment replacement, negotiating better rates with suppliers, and using data analytics to predict costly repairs.
Fuel Management
Fuel is a significant expense for construction fleets. Inefficient fuel use can lead to increased costs and environmental impact. Key fuel management challenges include fuel theft, inefficient fuel use, and lack of monitoring. Implementing fuel monitoring systems, educating drivers on efficient driving practices, and securing fuel storage can help manage fuel costs effectively.
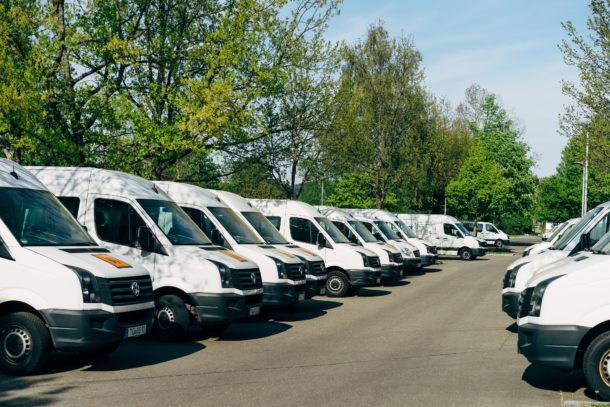
Driver Management
Managing drivers in a construction fleet comes with its own set of challenges:
- Driver Shortage: The industry faces a shortage of qualified drivers, making it difficult to find and retain skilled personnel.
- Training and Compliance: Ensuring that drivers are properly trained and comply with regulations is critical for safety and efficiency.
- Performance Monitoring: Tracking driver performance to ensure adherence to safety and operational standards can be challenging.
Fleet managers can overcome these challenges by investing in driver training programs, implementing driver incentive schemes and using telematics to monitor driver performance.
Compliance With Regulations
Compliance with regulations is a major concern for construction fleet managers. Regulations cover a wide range of areas, including:
- Safety Standards: Ensuring that all equipment and operations meet safety standards is essential to avoid penalties and accidents.
- Environmental Regulations: Compliance with emissions standards and other environmental regulations is increasingly important.
- Record Keeping: Maintaining accurate records for inspections, maintenance and driver hours is mandatory and can be time consuming.
Staying updated with regulatory changes, using fleet management software to streamline compliance tasks and conducting regular audits can help manage regulatory compliance effectively.
Data Management
In the modern construction fleet environment, data plays a crucial role. However, managing and utilizing data effectively can be challenging:
- Data Overload: The sheer volume of data generated by modern fleet management systems can be overwhelming.
- Integration Issues: Integrating data from various sources into a cohesive system can be difficult.
- Actionable Insights: Turning raw data into actionable insights requires specialized skills and tools.
Fleet managers can address data management challenges by investing in advanced fleet management software that offers data integration and analytics capabilities, and by training staff to interpret and act on data insights.
Construction fleet managers face numerous challenges, from managing equipment downtime and rising maintenance costs to ensuring compliance with regulations and effectively managing drivers. By understanding these pain points and implementing strategic solutions, tradesmen can optimize their fleet operations, reduce costs, and improve efficiency on the job site.
Sam Kraft is Content and Communication Manager at Whip Around. Kraft brings 13-plus years of copywriting experience to Whip Around, where he’s immersed in “all things fleet” on a daily basis. He’s the go-to guy for fleet technology insights, breaking down industry trends and making sure fleet managers get the information they need to keep their equipment safe, compliant and productive.
Join the conversation: