Machine breakdown can be a major obstacle for virtually any organization. It can result in bottlenecks that compromise production and worker safety. It also increases maintenance costs, penalties, unscheduled downtime, and other issues. The following tips are crucial for any organization working to prevent machine breakdown:
Adherence to Manufacturer’s Instructions
The technicians’ failure to follow the manufacturer’s instructions is one potential cause of machine breakdowns. It is astonishing to learn that many operators never examine machine instructions, and some aren’t even aware that they exist!
These manuals provide all the important information that technicians need for safe operation, including calibration requirements, checklists, troubleshooting advice, etc. It’s only natural that strict adherence to these suggestions will likely decrease malfunctions.
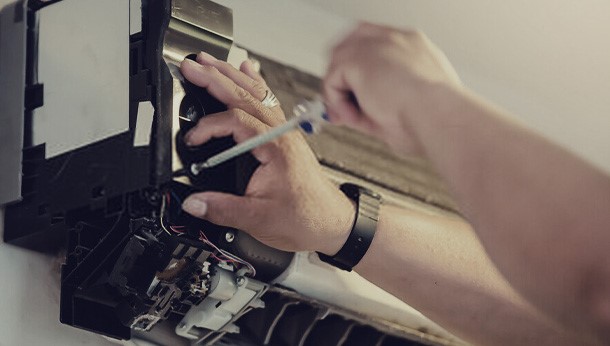
Train Relevant Staff Members
Heavy manufacturing equipment is significantly impacted by human error, which may result in unforeseen malfunctions and safety problems. Therefore, it is essential to train both technicians and machine operators to avoid unexpected equipment failure.
Also, the maintenance team should be highly knowledgeable about machinery components, while the operators should have sound instruction on how to utilize the production machinery safely and successfully. It’s crucial to have training sessions to make sure that all staff members are informed whenever upgrades or modifications are made to the equipment.
Additionally, businesses may conduct tests, interviews, or mini-examinations to determine how well their staff members are acquainted with the machinery.
Don’t Overwork the Equipment
Even the most high-performing component of a machine has limits. Many machines have a lifetime after which they may break down, lose effectiveness, or need replacement. Others provide specifics on how much work they can do. However, businesses that routinely push equipment to its limits risk shorter lifespans, breakdowns, overheating, unresponsiveness, or even early death.
However, businesses that routinely push equipment to its limits risk shorter lifespans, breakdowns, overheating, unresponsiveness, or even early death.
This one can be fixed quickly. Make sure that the workloads placed on your machines are less than the maximum allowed. Buying new equipment may be a safer and less expensive alternative if you need to achieve quotas or boost output since overworking existing equipment may result in costly delays and unforeseen machine problems. It’s far better to have a spare robotic stone saw waiting in the wings than it is to over-use your current one and end up with nothing at all.
Work on Preventive Maintenance
Preventative maintenance is carrying out actions in advance to reduce unplanned machine downtime and avert machine malfunctions. All machines require routine maintenance to keep them in good working order and spot potential issues before they occur. For instance, if a regular maintenance checkup reveals a problem with the equipment; technicians may then plan and start working to fix the issue before it gets serious.
Businesses that monitor, update, inspect, and repair their machinery often create the perfect environment for achieving objectives and minimizing downtime. Additionally, such firms may enhance maintenance management by using turnkey manufacturing solutions to keep pertinent machine information organized and everyone on the same page.
Create a Comprehensive Inspection Checklist
Unplanned downtime and more frequent failures are consequences of poorly maintained equipment. Therefore, to minimize this risk, establish a thorough inspection checklist. A detailed and structured inspection checklist will ensure that all required inspections are carried out, and that possible issues are immediately detected and resolved.
Making a thorough inspection checklist might require some work. However, the following guidelines will assist you to get going:
- Start with the fundamentals.
- Sort the list of items into categories.
- Put similar objects together.
- Determine which places need an inspection.
- When describing the regions you’re inspecting, use images or diagrams.
The following are specific items you should include in your inspection checklist:
- Equipment security features.
- Electrical components and wiring.
- Lubrication points.
- Belt tensions.
- Inventory of replacement components.
These are only a few fundamental beginning points; your inspection checklist should be as comprehensive as possible to fit your particular manufacturing process.
Be Proactive, Not Reactive
Reactive maintenance may be expensive since it causes production to stop and also creates bottlenecks. On the other hand, proactive maintenance considers staff observations of the environment and the state of the machinery to prevent minor difficulties from developing into major concerns. Monitoring the whole process and putting the data together to understand what’s occurring on the shop floor are the first steps in adopting a proactive mentality.
A proactive strategy represents a significant, extensive transformation. Also, it is less likely for an unforeseen failure to occur when a machine is operating at its best since it is smoother and makes fewer mistakes.
Conclusion
Machine breakdown is a menace to production because it affects more than just one stage of the process. A holdup in one area is likely to have a huge impact on other parts of the production line. Therefore, identifying ways to prevent machine breakdown is crucial to reducing downtime and meeting production goals.
Join the conversation: