Manufacturing has always been a cornerstone of progress, constantly evolving to meet the demands of a changing world. Among the many advancements that have shaped this industry, precision cutting stands out as a transformative innovation. From its early manual origins to today’s highly sophisticated automated systems, precision cutting has redefined efficiency, accuracy, and the quality of manufactured goods. Modern manufacturers rely on tools that can handle complex designs and tight tolerances, ensuring that production remains competitive and sustainable. One notable player in this space is Pacific Trail Manufacturing, whose innovative solutions exemplify the cutting-edge nature of this field.
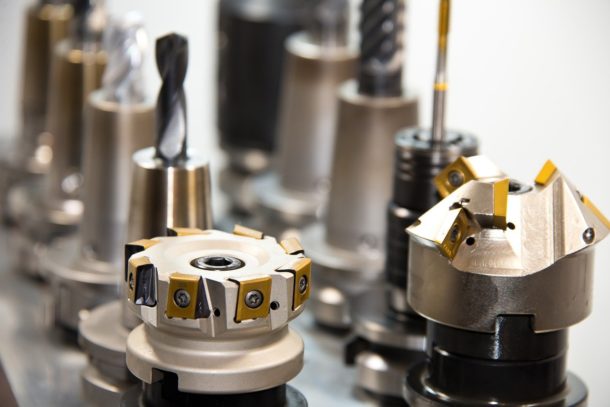
The Early Days of Cutting in Manufacturing
Precision cutting techniques can be traced to crude instruments such as hammers, chisels, and saws. These tools were all hand-operated; a great deal of skill and physical effort was needed to make even the most basic of parts. That is why when the requirements for manufacturing increased during the Industrial Revolution, the necessity for better cutting was questioned. This period witnessed mechanical cutting tools operated by steam or simple motors and was more precise and faster than hand tools.
However, early mechanical cutters retained low, precise control until the mid-twentieth century. There were still problems with accuracy for the operators, which sometimes resulted in wasted material or poor-quality products. It was only in the Industrial Revolution, specifically, the use of machine tools in the later part of the nineteenth and beginning of the twentieth century, that producers started attaining scale precision. Screw machines, stamping machines, milling machines, lathes, and drills were necessary for making standardized parts for mass production and global markets.
The Rise of CNC Technology
A manufacturing sector revolution occurred in the mid-twentieth century with the introduction of Computer Numerical Control (CNC). While prior machines could only mechanically follow instructions, the CNC machines could do this with a high degree of accuracy. This enabled manufacturers to develop complex designs and produce items with that design uniformly across many units.
CNC technology also helped eliminate human error because machines could work on them for extended hours and with great precision. Aerospace and automotive industries, and electronics,s in particular, are some industries that embraced CNC cutting tools due to their capacity to produce highly complex parts. This innovation also widened the district of cutting tool applications to metals, plastics, and composite materials, among others.
Manufacturers could still improve productivity if CNC were integrated with modern software. Specifically, engineers could draw their components on CAD software and translate these designs to CNC machines. This interaction between hardware and software has persisted as a mainstay for development in precision cutting.
Functions of Laser and Waterjet Cutting
Laser and waterjet cutting have become more precise, especially in recent decades. Laser cutting involves focusing light and using it to cut through materials with a lot of precision, which is useful when cutting thin or complex shapes. It is highly appreciated in medical device manufacturing, where the allowable deviations are negligible.
Waterjet cutting, however, uses high-pressure water with garnet particles for abrasive cutting of a broad range of materials. On the other hand, waterjet systems do not cause thermal distortion as laser cutting systems cut materials. This versatility has made the waterjet cutting method popular across the construction industry and even aerospace.
Laser cutting has remained equally essential for manufacturers looking for precision and speed with flexibility from waterjet cutting. Organizations such as Pacific Trail Manufacturing still rely on these technologies to offer solutions to various industry needs.
Automation and the Future of Precision Cutting
Precision cutting and automation are becoming an essential part of the manufacturing industry as it progresses. Some of the work scientists could not accomplish earlier can now be done by robotic systems fitted with perfect sensors and artificial intelligence algorithms. These systems can be set up to respond to changes, and thus, the production lines can be maintained optimally.
One of the most inspiring trends is the IoT application of Industry 4.0, where cutting tools are smartly interconnected. Intelligent factory machines can enable information gathering and provide solutions for operating to achieve maximum efficiency, decrease loss, and determine when a machine requires servicing. Such high connectivity guarantees that precision cutting will remain integral to contemporary production processes.
Technologies such as additive manufacturing or 3D printing and hybrid machining will likely serve as an addition to cutting processes. With the help of cutting and material deposition, the manufacturers can create lightweight, durable, and cheap parts simultaneously.
Conclusion
The history of precision cutting in manufacturing is a part of the human desire for improvement. From mere hand tools to today’s complex CNC, laser, and waterjet systems, every innovation has been achieved based on another to change the future. Thus, precision cutting will remain a critical force for the industry as driven by automation and connectivity. Pacific Trail Manufacturing is one of the companies that embodies the idea of developing new tools that will help manufacturers face the future and achieve success with incredible accuracy.
Join the conversation: