Optimizing the mechanical supply chain in today’s fast-paced manufacturing landscape is more critical than ever. Businesses face increasing pressure to reduce costs, minimize production delays, and maintain high product quality. Manufacturers must adopt efficient production methods that enhance speed, precision, and reliability to stay competitive.
One of the most effective ways to streamline the mechanical supply chain is through injection molding. This manufacturing process enables companies to produce high-quality parts at scale while maintaining cost efficiency. With its rapid production capabilities and material versatility, injection molding has become an essential tool for companies looking to improve supply chain efficiency and meet growing market demands.
By leveraging advanced manufacturing solutions with RapidDirect, businesses can accelerate production cycles, minimize material waste, and enhance product consistency. These benefits make injection molding an indispensable part of modern supply chain optimization, ensuring seamless operations from prototyping to full-scale production.
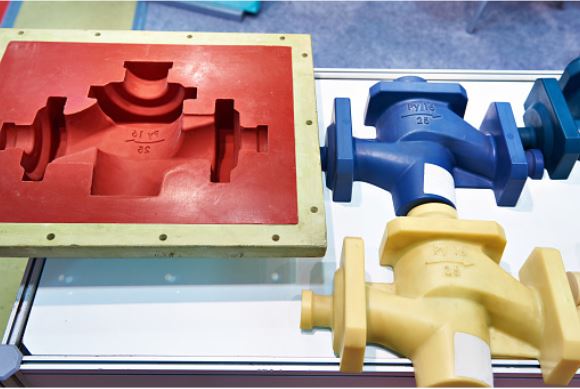
Understanding Injection Molding in Supply Chain Management
What Is Injection Molding?
Injection molding is a manufacturing process that involves injecting molten material—typically plastic, metal, or rubber—into a pre-designed mold to create precise and repeatable parts. This technique is widely used in industries such as automotive, aerospace, consumer goods, and medical devices due to its ability to produce large volumes of high-quality components with minimal waste.
The process follows a simple yet highly efficient cycle:
- Clamping – The mold is securely closed to prepare for material injection.
- Injection – Molten material is injected into the mold cavity at high pressure.
- Cooling – The material solidifies and takes the shape of the mold.
- Ejection – The finished part is removed, and the cycle repeats.
This automated process allows for fast, consistent, and scalable production, making it a key driver of supply chain efficiency.
Why Injection Molding Enhances Supply Chain Efficiency
Injection molding offers several advantages that directly contribute to a more efficient mechanical supply chain. Some of the primary benefits include:
- High production speed – The automated nature of injection molding significantly reduces manufacturing time compared to traditional methods like CNC machining or 3D printing.
- Cost-effective mass production – Once the mold is created, the per-unit cost of production decreases significantly, making large-scale manufacturing highly economical.
- Material versatility – A wide range of thermoplastics, elastomers, and composites can be used, providing flexibility for different applications.
- Minimal waste – Unlike subtractive manufacturing processes, injection molding generates very little material waste, improving sustainability and cost-efficiency.
- Consistency and repeatability – The process ensures that every part is nearly identical, reducing defects and quality control issues.
By integrating injection molding into their supply chain, manufacturers can achieve faster production cycles, lower costs, and greater reliability, ultimately improving their overall operational efficiency.
Key Ways Injection Molding Optimizes the Mechanical Supply Chain
1. Faster Production and Reduced Lead Times
Time is a crucial factor in supply chain management. Delays in manufacturing can lead to production bottlenecks, missed deadlines, and increased costs. Injection molding offers a high-speed production process that minimizes lead times, ensuring that products are manufactured and delivered on schedule.
Since injection molding is an automated and continuous process, it allows manufacturers to produce thousands—even millions—of parts with minimal human intervention. This significantly reduces the time spent on manual assembly and inspection, enabling companies to meet tight deadlines and keep up with demand fluctuations.
Furthermore, digital manufacturing advancements, such as rapid tooling and AI-driven process optimization, further accelerate production cycles. By leveraging these technologies, businesses can increase efficiency and maintain a smooth supply chain workflow.
2. Cost Savings Through Mass Production
One of the biggest advantages of injection molding is its ability to significantly reduce production costs—especially for high-volume manufacturing. Once the initial mold is created, the cost per unit drops drastically, making it one of the most cost-effective manufacturing methods available.
Here’s how injection molding drives cost savings:
- Lower labor costs – Since the process is automated, minimal manual labor is required.
- Economical material usage – Injection molding minimizes waste, reducing material expenses.
- Efficient production cycles – The ability to produce thousands of identical parts quickly leads to better economies of scale.
Compared to other manufacturing methods like CNC machining, where each part is individually cut from a solid block, injection molding produces complex geometries with minimal waste. This efficiency translates to lower costs and higher profitability for manufacturers.
3. Consistency and Quality Control
Inconsistent product quality can lead to costly rework, delays, and customer dissatisfaction. Injection molding ensures high precision and repeatability, making it an ideal solution for industries that require strict quality standards.
Key factors that contribute to superior quality control in injection molding include:
- Precision molds – Advanced mold design and tooling ensure that each part meets exact specifications.
- Automated quality checks – AI and machine vision systems can detect defects in real time, reducing errors.
- Consistent material properties – The controlled injection process ensures uniformity in texture, strength, and performance.
By maintaining tight tolerances and strict quality control, injection molding helps manufacturers eliminate defects, reduce waste, and enhance product reliability, leading to a more efficient and streamlined supply chain.
4. Enhancing Supply Chain Flexibility with Injection Molding
Rapid Prototyping and Design Iterations
Modern injection molding techniques, such as soft tooling and 3D-printed molds, allow manufacturers to develop and test multiple iterations of a product before committing to mass production. This reduces the risk of design flaws and ensures that the final product meets both performance and cost expectations.
Scalability for Variable Demand
Market demand can fluctuate due to seasonal trends, economic shifts, or unexpected global events. Injection molding provides a scalable solution that enables manufacturers to ramp production up or down as needed without excessive lead times or resource wastage.
5. Sustainable Manufacturing with Injection Molding
Material Efficiency and Waste Reduction
Injection molding minimizes waste by allowing excess material to be reprocessed and reused, reducing raw material consumption and supporting eco-friendly manufacturing practices.
Energy-Efficient Production
Modern injection molding machines consume less power, particularly with electric and hybrid systems, making them more sustainable and cost-effective in the long run.
6. Overcoming Supply Chain Challenges with Injection Molding
Mold Development Costs and Lead Times
To mitigate high mold costs, businesses can use rapid tooling and modular mold designs to reduce expenses and improve production agility.
Supply Chain Disruptions and Material Shortages
Diversifying suppliers and considering alternative materials can help manufacturers maintain stable production despite fluctuations in material availability.
Quality Control and Process Optimization
Automated inspection systems and AI-driven monitoring help maintain consistent product quality, preventing costly defects and production delays.
Conclusion
Injection molding is a powerful manufacturing method that significantly improves the efficiency, flexibility, and sustainability of the mechanical supply chain. By leveraging its ability to reduce lead times, lower costs, and ensure consistent product quality, manufacturers can streamline their operations and stay competitive in a rapidly evolving market.
As businesses continue to face supply chain challenges, adopting innovative injection molding solutions will be key to maintaining efficiency and profitability. Companies that integrate advanced technologies, sustainable practices, and strategic supplier partnerships will be well-positioned for long-term success.
By optimizing supply chain operations with injection molding, manufacturers can drive higher productivity, reduce waste, and meet growing market demands with precision and reliability.
Join the conversation: