Imagine threading or welding 4″ carbon steel pipes, 40 feet in the air. Sounds difficult, time-consuming and potentially dangerous.
All those pitfalls were avoided when a crew in Michigan used Viega MegaPressG fittings to pipe a new bean-roasting facility. The result was clean, attractive piping, a quick turnaround on project time, plus happy workers and owners.
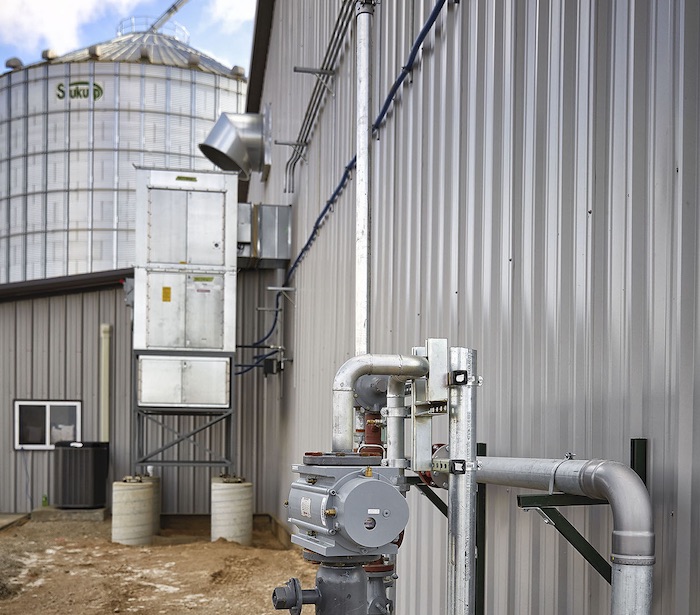
Viega recently added MegaPressG fittings in sizes 2½” to 4″ to its lineup, and Schreiner Mechanical out of Frankenmuth, Michigan, was the first to install them, putting a couple dozen of the larger-diameter fittings into a new build in Gilford.
The project that Steve Schreiner, owner of Schreiner Mechanical, and his crew went to work on was a soybean-processing facility. The soybeans are roasted and crushed, then the oil is removed and used for biodiesel fuel and other applications. The remaining product is used to feed dairy cattle, leaving zero waste.
“What the plant does is unbelievable,” Schreiner said. “It’s favorable to the economy, and the oil can be used for several different products. There’s no waste.”
At first, Schreiner Mechanical was asked to do some plumbing in the office of the plant. Then the project, and need for Viega fittings, started to grow. The contractor was tasked with creating a gas main and system
to supply the gas for the burners that roast the soybeans, plus they needed to plan for the plant’s future growth.
“The burners that are used are about 12 million BTU each, so they needed a high-pressure gas system in the plant feeding these machines,” Schreiner said. “That’s quite a large capacity, and in the future they’ll potentially have three more of these burners, so this gas system had to be designed to feed a tremendously large system.”
To do that, Schreiner Mechanical created a manifold with 4″ gas lines. Those lines work their way down to 2″ in size throughout the plant. It was the perfect place to put MegaPressG in larger-diameter sizes to work.
“Lines run throughout the plant for gas feeding the furnaces and rooftop units feeding other areas of the building,” Schreiner said. “There is probably about 500 feet of gas line with Viega fittings in this building.”
Schreiner will tell you he is “a Viega guy,” and when he began working on this project he was excited to hear that MegaPressG fittings in the larger sizes were on their way to market.
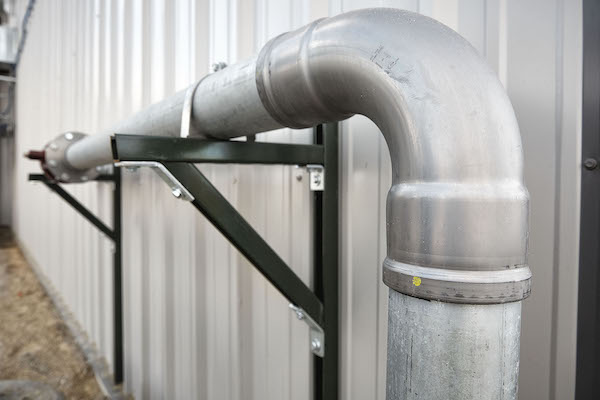
“If we’d had to thread this, it would have changed the whole philosophy on how to do things,” Schreiner said. “It would have made things 10 times more difficult, being 40 feet in the air, so we would have had to change the installation, plus it would have tripled or quadrupled the labor intensity. We’re talking about lift rentals and all things that come into play, plus the costs incurred for that, if we’d done it a different way than pressing. Threaded pipe would have been absurd.
“I’m excited that by using MegaPressG on this project, it was a time saver, a labor saver and safer than welding. The injury factor that can come up with different products is much bigger than with pressing. We would have had guys on the ground cutting and pre-fabbing pieces and then going up and down, but pressing in the air is much easier.”
In addition to providing the gas to the burners for the roasting in the plant, 2″ carbon steel lines with MegaPress fittings were also used for the oil line, moving the extracted crude oil from the beans into tanks.
Schreiner’s team is set up with Ridgid tools, and he said he feels that Ridgid and Viega together are the perfect combination.
“The Ridgid tool was a huge part of this successful application,” he said. “I’m passionate about the products I use, and when I find a good one, I stick with it.”
Viega District Manager Mike Norgan brought out the MegaPress XL PressBooster tool for Schreiner’s crew to use on the larger-diameter MegaPressG fittings, and Schreiner said it was simple to use.
“There was nothing more than smiles after using the tool,” he said. “Along with the large-diameter rings, it was easy and not cumbersome to use. Being able to press 12 or 14 large fittings in less than an hour is unbelievable.
“I tell people, ‘Look at what can be done [using Viega products]. This can be you and it’s this easy,’” he added. “Everybody’s hands are clean, there are no contaminants in the system, and there’s a lot to be said about that, having a contaminant-free system. When you have solder or threading oils or shavings, you have a high chance of contaminants, but with Viega, that chance is zero. I just cannot say enough about Viega. What we accomplished on this project with it is amazing.”