PEX Protects Pedestrians and High-End Flooring At City’s Prestigious Place Ville Marie
Every winter in Montreal, an army of municipal employees works around the clock, running one of the largest snow-removal operations in the world. Up to 3,000 personnel and 1,000 snowplows are mobilized to collect 300,000 truckloads of snow from 10,000 kilometers of city streets.
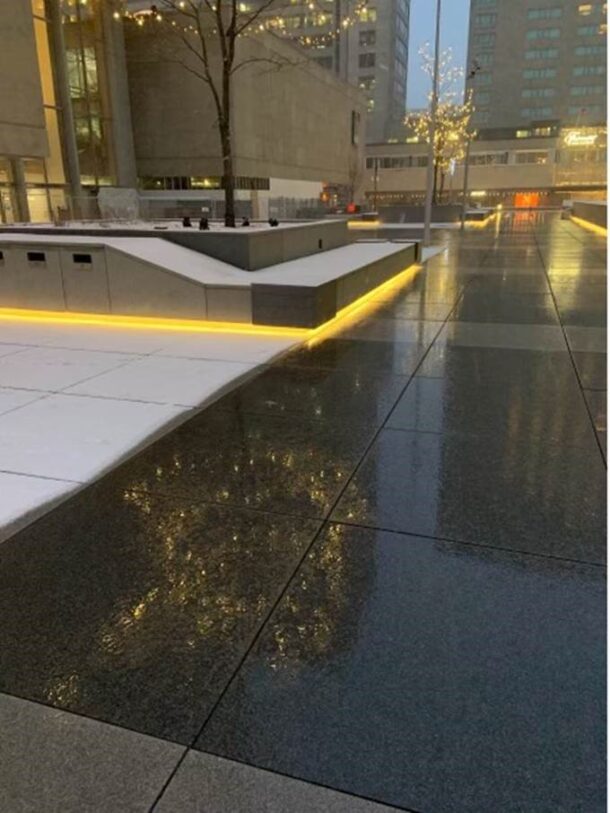
The volume of material is almost as impressive as the means in which it is gathered and disposed of — snow removal in Montreal is carried out with military-like precision. And in Montreal they don’t just plow the streets. They also plow the sidewalks. When Montrealers talk about snow removal, they mean getting rid of it, not just pushing it to the side of the road. Here’s how it works:
When significant snow is forecast, signs go up announcing on-street parking bans. The day of the event, tow trucks cruise the streets blaring a warning to vehicle owners still parked in snow-clearing zones. If the cars aren’t removed within minutes, they are towed. Snow is then plowed to the center of the street, where a giant snow blower sprays it into a truck, which transports the snow to one of the city’s 29 snow dumps. A convoy of dump trucks repeats the procedure.
This well-run system is required in a city known not only for its Stanley Cup-winning hockey franchise, the Montreal Canadiens (known to locals as “The Habs”), but its brutal winters. Sometimes, however, it just isn’t possible to use a mechanized army of plows and shovels.
Severe winters are etched into the memories of Montrealers, when large accumulations of snow and ice combined with high winds have destroyed power lines, leaving some areas without electricity for days and residents dying.
A particularly nasty cold spell occurred in 2015, when for 12 days straight, temperatures plunged below -20 Celsius, making it the coldest February in Montreal in more than 100 years.
Fortunately, the modernization of the city’s downtown has brought with it the construction of areas where Montreal inhabitants can go to enjoy a pedestrian experience free of snow and ice. One of those is Place Ville Marie (PVM), a large skyscraper and shopping complex. Its four towers and spacious Esplanade is a nexus for Montreal’s underground city, with indoor access to over 1,600 businesses, several subway stations, a suburban transportation terminal and tunnels extending throughout the downtown.
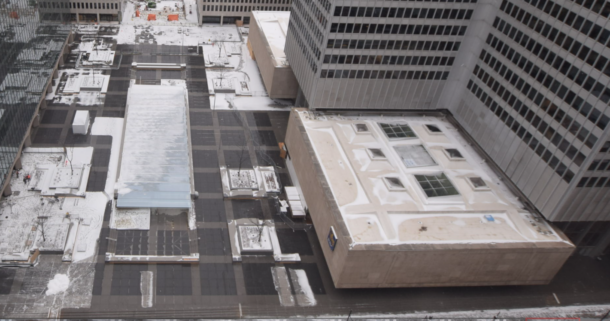
Designed by Henry Cobb, of award-winning New York architectural firm Pei Cobb Freed & Partners, Place Ville Marie was built in 1962 to serve as the official headquarters of the Royal Bank of Canada, which it remains today.
According to design historian Mark Pimlott, via Wikipedia, “The most radical aspect of the Place Ville Marie project was that nearly one-half of its 280,000 square meters area were beneath street level, deriving the obvious benefit of being protected from Montreal’s extreme winter and summer climate.”
At time of construction, the main tower was the tallest in the British Commonwealth and the third highest skyscraper on Earth outside the United States. As for its moniker, former Montreal mayor Jean Drapeau reportedly chose Place Ville Marie for the name of the Catholic colony founded by what is now Montreal in 1642.
Fast forward to 2017 when Place Ville Marie received a make-over thanks to real estate firm Ivanhoe Cambridge, whose $1 billion Projet Nouveau-Centre featured plans to refurbish its flagship downtown properties, including PVM, Fairmont The Queen Elizabeth Hotel, Maison Manuvie, and Montreal Eaton Centre.
A $200 million investment revitalized the Esplanade (the central public space between the office buildings) and renewed the commercial offerings at Place Ville Marie. To execute the historic project, Ivanhoe Cambridge called upon Montreal firms Sid Lee Architecture and Menkès Shooner Dagenais Létourneux Architectes.
“Our primary goal is for this civic space to be a catalyst for downtown social activity,” Jean Pelland, architect and senior partner, Sid Lee Architecture, said at the time. “Given the importance of this iconic space, we sought additional exposure to urban activity, making it more accessible and usable. Our major architectural interventions are in line with this desire for great openness.”
An important part of the project’s ethos to breathe new life into the area, and position it as a social, cultural, and commercial hub, was to install a snow and ice removal system.
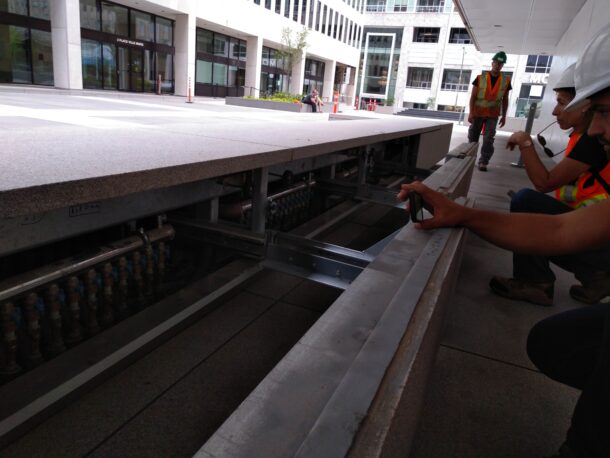
The restricted access for snow removal equipment, coupled with the upscale finish of the surface material, made mechanical and chemical snow removal at Place Ville Marie unfeasible. The owners turned to HeatLink Group, Inc. (Calgary, Alberta), a manufacturer and supplier of radiant hydronic heating/cooling and snow melt systems, to spec the job and supply the PEX-a tubing, loops and manifolds.
The Calgary-based company’s PEX-a snow and ice melt system eliminates the need for those other methods, helps to preserve the manufactured stone finish without abrasion caused by shovels or chemical attack from salt, and ensures pedestrians can safely and comfortably enjoy the space and use the stairs at any time of day or night in the wintertime.
At 120,000 square feet that would need nearly 50 miles of PEX-a tubing, the Esplanade at Place Ville Marie was the largest snow and ice melt project HeatLink had ever contemplated, certainly on par with the radiant heating/cooling system the company designed for the Vancouver Convention Centre. The six-floor facility is a global hub for conferences and trade shows; in 2010 it was used to host the medal ceremonies for the Winter Olympics. Place Ville Marie is comprised of pedestrian areas, stairs, and multiple levels of commercial space, incorporating a beautiful glass-roofed pavilion in the center.
The company worked closely with its distributor, Agence Jacques Desjardins Inc., and engineer Bouthillette Parizeau, to manufacture and supply 260,000 linear feet (79,300 m) of ¾-inch PEX-a tubing that was installed in 679 circuits or loops. A challenging aspect of this outdoor project was where to place the 77 supply and return manifolds, which distribute the heated fluid with 50 percent glycol solution to the numerous zones set up for snow melting. The 13-phase endeavor is the largest snow melt project in Montreal and ranks as one of the most extensive on the continent, according to the Plastics Pipe Institute, Inc., the major North American trade association representing the plastic pipe industry.
“The first hydronic snow and ice melting systems were installed in the 1930s using steel piping that was welded together and encased within concrete,” explained Lance MacNevin, P. Eng., director of engineering for PPI’s Building & Construction Division. “Those systems performed well and proved the concept, although the piping would start to fail after several years due to corrosion.”
Today, the majority of SIM systems utilize PEX – crosslinked polyethylene or PERT – Polyethylene of Raised Temperature resistance tubing. The PEX tubing used in this project is a flexible piping material with high temperature and pressure capabilities and incredible toughness.
“Hydronic SIM systems using fluid-filled pipes are known worldwide for their high degree of safety and convenience. Additional benefits include reduced liability, lower maintenance costs and long-term reliability, all important factors for building owners. Hydronic systems typically use far less energy to simply melt snow and let it flow down the storm drain than would be required to plow the snow and truck it away. Plus, because melting snow and ice prevents the need for salting and sanding, there is very low environmental impact, which fits in very nicely to Montreal’s sustainable development plan.”
The large surface area required thoughtful placement of manifolds to ensure efficient use of energy and tubing. The project used cleverly designed sliding panels to hide, protect and access manifolds that needed to be located close to pedestrian areas.
Manifolds ranged from four loops to 20 loops. In a couple of areas, two manifolds had to be joined together. “Snow melting systems require relatively high flow rates of heated antifreeze, as compared with indoor radiant heating systems, due to the energy requirements for melting snow during extreme weather events,” said Byron Stadnyk, HeatLink Group’s senior tech & design support. “Therefore, the tubing design has to allow for precise delivery of the heated fluid where it is needed, without incurring excessive pressure losses. There are engineering limits on how long the loops can be.”
All parties involved in the installation needed to make sure that the tubing loops followed the design specifications for on-center spacing, tubing patterns and circuit lengths. The nominal ¾ inch tubes at Place Ville Marie are spaced six inches (15 cm) apart. The project was designed to deliver a heat output of up to 150 Btu/h-sq.ft.
“You don’t want little piles of snow in between your loops, so adequate tube spacing is critical. The loop length has to be under a certain amount to make sure that selected circulator pumps can be used to efficiently deliver flow to all the areas as needed,” noted Mike Casavant, HeatLink’s technical manager. “There are a lot of technical constraints that people don’t even realize, that make a big, complicated project like this even more complicated.”
The tubing was positioned in a bed of leveling sand. It’s vital that the entire substrate be heated, along with the surface material, which at Place Ville Marie, consists of two-inch-thick manufactured stone.
“The challenge is to heat up the sand enough to be able to heat up the stone, to have high enough temperature at the surface to melt snow,” said Stadnyk.
The water-glycol supply is heated to 134 Fahrenheit (57 degrees Celsius) and pumped and distributed through the loops and manifolds to reach all of the heated areas. When snow begins to accumulate, sensors embedded in the surface stone activate the snow melting system. The heat sources are non-dedicated boilers that also heat the buildings.
With 260,000 linear feet of tubing installed underneath a finished-stone slab, it is important that the material is able to withstand the countless cycles of heating and cooling; nobody wants to be conducting an excavation to repair cracked tubing in the heart of downtown Montreal in the dead of winter. “The proven performance of HeatLink’s PEX-a tubing will ensure that such issues will not occur,” MacNevin stated.
A tekmar® Snow Melt Control 680 unit communicates with the building’s automation systems using BACnet® – the data communications protocol for building automation and control to provide alert notification, remote monitoring and adjustments. It uses sixteen tekmar Snow/Ice 090 Sensors to automatically detect snow or ice on the snow melting slab and meet demand on a priority basis.
According to PPI, PEX is a polyethylene material which has undergone a change in molecular structure using a chemical or a physical process whereby the polymer chains are chemically linked. Crosslinking of polyethylene into PEX for tubing results in improved properties such as elevated temperature strength and performance, chemical resistance and resistance to slow crack growth.
Casavant compares PEX tubing to the tires on a car. “A long time ago tires were just natural rubber and they would fall apart in short time. Charles Goodyear discovered that if he crosslinked the rubber through “vulcanization”, the modified rubber would resist the abuse of the roads and last much longer,” he said. “Standard thermoplastic materials can be heated and reformed into various shapes. Crosslinked polyethylene doesn’t do that. Once you’ve extruded the material into tubing, if you try to do anything to it, short of grinding it, it will always stay in the shape of that piece of tubing. You could heat it up and tie it into a knot, and you could even undo it, it’ll still be a piece of tubing. As long as you don’t cut the tubing, it will always hold its shape.”
The industry states that PEX tubing has an expected design life in excess of 50 years for projects such as this one.
“The success of the snow removal system at Place Ville Marie should encourage other engineers and architects to consider hydronic SIM systems for large public spaces, especially in downtown urban areas,” MacNevin stated.
“I think the more people realize that a job of that scale can be done, they’re not going to be afraid of it,” Stadnyk said.
“The high visibility and usage of this area will highlight the benefits of snow melt systems, not only to knowledgeable professionals in the heating industry, but also to the general public who will appreciate how accessible this space is in the winter. In the plastic pipe industry, our products and their benefits are largely invisible to the casual user, but in this case, people will notice immediately when they step from the snowy city sidewalk onto the PVM property,” said Casavant.
“It’s one thing to see a driveway being snow-melted, but it’s a very different thing to see this huge promenade where people are literally walking onto it from the city sidewalk, kicking the snow off of their boots and they don’t have to worry about slipping and sliding on the steps because the steps are all melted. I think they’re going to see that and say, ‘I love taking this route because of these reasons.’”
More information about SIM systems plus technical information can be found at the PPI Building & Construction Division’s website: https://plasticpipe.org/BuildingConstruction
Join the conversation: