In the world of construction, efficiency is the name of the game. Time is money, and delays or inefficiencies can quickly eat into profits. The question that arises is: how do you achieve that? Streamlining construction operations is essential for staying competitive and profitable in this industry.
In this article, we’ll explore various ways to simplify construction operations, focusing on relevant examples of how innovation can make a difference. Efficiency is not only about cost savings but also about delivering high-quality projects on schedule, meeting client expectations, and reducing the environmental footprint of construction activities. By examining these aspects, we can understand how to achieve efficiency in construction operations.
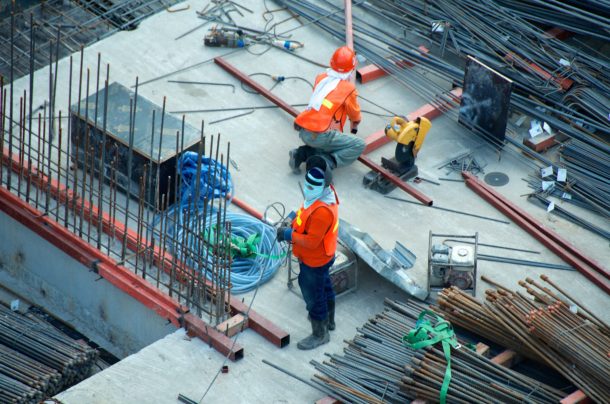
1. Optimizing Material Handling
Efficient material handling is a cornerstone of streamlined construction operations. Traditional methods often involve manual labor, which is time-consuming and prone to errors. This is where innovation comes into play. Ingenious devices have been developed to simplify moving and disposing of materials on-site.
These devices are designed to load materials quickly and can be transported by forklift or other machinery. The real magic happens when it’s time to unload. These devices tip with a simple lever pull, dumping their contents precisely where needed. This innovation eliminates the need for manual shoveling and labor-intensive material handling, saving time and reducing the risk of injuries. It’s a prime example of how investing in equipment can streamline construction operations.
2. Effective Waste Management
Waste management is another area where construction operations can be streamlined for efficiency. Construction generates a significant amount of waste, from discarded materials to debris. Handling and disposing of this waste can be challenging with the suitable systems in place. For instance, sturdy self-dumping hoppers play a vital role in waste management. By making collecting and transporting waste materials easy, they ensure that the job site remains clean and organized. These hoppers can be used in recycling efforts, further reducing waste and promoting sustainability. In addition to self-dumping hoppers, modern construction companies can benefit from implementing effective recycling and waste disposal strategies. This reduces the environmental impact and improves efficiency by keeping the work area clutter-free.
3. Streamlining Communication
Effective communication is the backbone of any successful construction project. Miscommunications can lead to costly errors and delays. To streamline operations, it’s essential to establish clear lines of communication among all team members. In today’s digital age, construction companies can use project management software and mobile apps to enhance communication. These tools allow for real-time updates, document sharing, and instant messaging among team members, on-site or in the office. When everyone involved in the project can access the latest information and communicate seamlessly, decisions can be made more quickly, and problems can be addressed promptly. This reduces downtime and keeps the project on track.
4. Efficient Equipment Utilization
Construction equipment is a significant investment, and maximizing its utilization is crucial. Underutilized or idle equipment represents wasted resources. To streamline operations, construction companies should have a comprehensive plan for equipment management. Regular maintenance and preventive measures can extend the lifespan of equipment, reducing the need for costly replacements.
Furthermore, tracking equipment usage and scheduling maintenance can help ensure that machines are in optimal condition when needed.
Additionally, some construction firms have embraced the concept of equipment sharing or renting. This allows them to access specialized equipment for specific tasks without the burden of ownership. It’s a cost-effective approach that minimizes downtime and optimizes resource allocation.
5. Lean Construction Principles
Lean construction is a philosophy that aims to minimize waste and maximize value in construction projects. It focuses on eliminating activities and processes that do not add value to the project. One of the core principles of lean construction is “pull planning.” Instead of pushing workers to complete tasks on a predetermined schedule, pull planning involves having workers pull functions as they can complete them. This ensures that work is done efficiently and with minimal downtime. Lean construction also emphasizes continuous improvement through feedback and collaboration. By involving all stakeholders in the planning and decision-making, construction companies can identify bottlenecks and inefficiencies and work together to find solutions.
6. Employee Training and Development
Streamlining construction operations isn’t just about technology and equipment; it also involves investing in your workforce. Well-trained and motivated employees are likely to work efficiently and contribute to the project’s success. Offering ongoing training and development opportunities can help employees stay up-to-date with the latest construction techniques and technologies. This improves their skills and boosts their confidence and job satisfaction. In addition, involving employees in the decision-making process and valuing their input can lead to innovative ideas and process improvements. After all, the people on the front lines often have the best insights into what can be done to streamline operations.
7. Strategic Planning and Risk Management
Every construction project comes with risks, from weather-related delays to unforeseen issues on the job site. Strategic planning and risk management are essential for minimizing these risks and maintaining project efficiency. A thorough risk assessment at the beginning of a project can help identify potential challenges and allow for contingency planning. This proactive approach can help construction companies mitigate risks and reduce the impact of unforeseen events. Moreover, having a well-defined project schedule and budget, regularly monitoring progress, and adjusting as needed can keep the project on track. Effective risk management is all about being prepared and adaptable.
Conclusion
Learned a few things about construction efficiency? All in all, streamlining construction operations for efficiency requires a multifaceted approach. It involves optimizing material handling, improving waste management, enhancing communication, utilizing equipment effectively, embracing lean construction principles, investing in employee training and development, and implementing strategic planning and risk management. It’s essential to recognize that efficiency improvements can be achieved in various aspects of the construction process. By adopting these strategies and continually seeking opportunities for improvement, construction companies can stay competitive, reduce costs, and deliver projects on time and within budget. Efficiency isn’t just a buzzword; it’s a fundamental principle for success in the construction industry.
Join the conversation: