When you Need an Alternative to Brazing HVAC/R Joints
While there will always be a need to braze, more and more HVAC/R contractors are also taking advantage of the time and cost savings – and proven reliability – of RLS press fittings. They connect in seconds, without the need for a torch, gas, nitrogen and everything else required for brazing (including hot work permits and fire spotters).
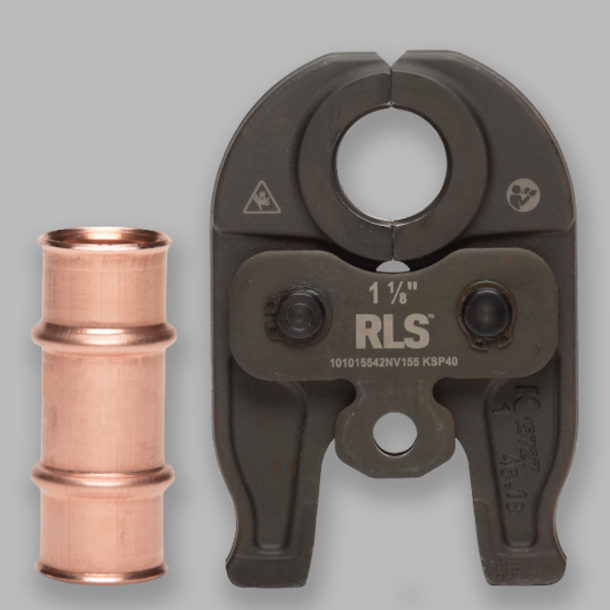
Whether you prefer to press every joint possible, or only to use the press tool in certain situations, there is a role for pressing in most HVAC/R service and installation businesses. In fact, there are many times when pressing is the ideal solution:
- Hospitals and other buildings that don’t allow open flames
- Areas where burn permits and fire spotters are required and costly
- When brazing too close to insulation, walls and other flammable materials would be dangerous
Proven by more than 10 million fittings installed.
While some were skeptical when RLS fittings were first introduced in 2015 (originally under the ZoomLock brand), the technology is now well proven and accepted, with more than 10 million fittings installed successfully around the world. Designed specifically for high-pressure HVAC/R systems, RLS fittings feature a patented double circular press that results in two 360˚ metal-to-metal connections, creating a permanent mechanical joint every time, with no leak paths.
A wide range of valuable benefits.
From faster installation, to increased safety, to avoiding dragging tanks and other brazing equipment to the jobsite, RLS fittings offer many advantages:
- Connections in 10 seconds
- UL Listed to 700 psi
- No gas or brazing materials
- No flame, no fire hazards
- No burn permits
- No fire spotters
- No nitrogen purging
- Works in tight spaces
- Millions of fittings installed
- Made in America
Learn more at rapidlockingsystem.com and become an RLS Certified installer at training.rapidlockingsystem.com.
Join the conversation: