Mechanical Hub presents this multi-part series on pressing technology. Mechanical Hub has featured a Q&A with the leaders in pressing technology. Press technology is gaining momentum as the preferred choice in pipe joining. Introduced into the North American market in 1999 by Viega, pressing is gaining acceptance as the most efficient and cost effective method of joining piping materials. Press currently makes up nearly 12% of the copper fitting market, and that number is expected to rise with contractor education and training.
Mechanical Hub recently talked with Naomi Greene, product specialist, NIBCO Inc., to learn more about what they are doing in this growing market.
MH: Name some applications in which pressing is ideal?
Greene: Press is ideal for new commercial construction — hotels, apartments, condominiums, schools, hospitals — for both plumbing and HVAC applications. Press is also being more widely used in repair, maintenance and remodel, especially in older buildings where open flame is a potential hazard.
MH: What is the scope of press piping? Copper, PEX, Stainless, Iron, etc.?Greene: Copper is primarily used for commercial construction and PEX for residential construction. However, installers are using stainless steel press for specific applications such as industrial, and new press fittings are now on the market for use with black iron pipe.
MH: Are your pressing tools proprietary? Or can they be interchangeable with other manufacturer's pressing clamps and fittings?
Greene: The NIBCO tools are interchangeable with other manufacturer’s fittings and jaws ONLY for sizes ½” – 2”. For NIBCO fittings and valves in sizes 2 ½” – 4”, ONLY NIBCO pressing tools and chains (jaws) will work.
MH: I have heard the pressing is used predominantly in Europe. Why has it taken the North American market so long to catch on?Greene: Pressing technology has been used in Europe for approximately 30 years. The types of buildings and the construction processes in Europe differ in certain ways from the U.S. European apartments/flats are typically smaller and more compact, and the methods they use to heat and cool are different. I believe these cultural differences moved them to look for more friendly joinery methods sooner. The U.S. typically lags behind Europe in its adoption of more progressive technologies, and the construction methods used in the U.S. have not been as challenged until recently, with more and more regulation requiring no flame in occupied spaces, for example. For the U.S. market, the benefits of press technology are very focused on time and cost savings for the installer.
MH: To that last point, can you guesstimate the pressing market in the U.S. as opposed to sweating and other pipe joining methods?
Greene: I believe that the pressing market in the U.S. is still fairly small, and that pressing technology is in its infancy stage, with vast opportunity for growth. It is just a guess, but I would say that the pressing market (all types of press – including PEX) is about 20% of the total market of pipe joining methods.
MH: Is pressing technology continually evolving? (effectiveness, ergonomics, weight, cordless & battery efficiency, larger pipe diameters, etc.)
Greene: Yes, it definitely continues to evolve. Different types of materials are becoming available (stainless, carbon steel, etc.), as well as more efficient and more powerful tools and tool accessories for working in tight spaces. Also, features are being added to the products such as leak detection and crimp detection, which help the installer find un-crimped fittings during system testing. The range of diameter sizes has been fairly stable, but I believe that larger diameters will be available for pressing at some point in the future.
I have used the pressing tools so the obvious question would be, why wouldn't contractors use pressing technology?
Greene: There are a few reasons that hold contractors back from using press.
• One is the cost of the tools — they are fairly expensive, especially for the smaller plumbing contractor and depending on the work load. The initial investment can be prohibitive. However, the tools have to be considered an investment over the long term — they will last a long time, and will pay for themselves very quickly with the labor time savings and cost savings with each job.
• Some engineers and contractors are still skeptical of the pressing technology. They require more time to pass until the technology has proven itself.
• The cost of the fittings and valves are more expensive than solder products, etc., so this keeps some installers from using press. If they consider the “total installed cost” of the project, including the labor component, the total cost is much less than a project using solder in spite of the higher material cost of press. For more info, www.nibco.com.
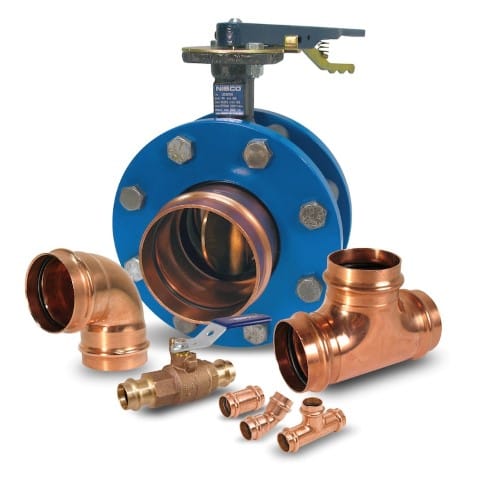
Drive your business forward with the NIBCO® Press System® and its new leak detection feature allowing you to quickly identify uncrimped connections during system testing for consistent joint quality, fewer callbacks and reliable performance. Only NIBCO offers a single-source package of press valves, fittings and tools, saving you valuable time on job sites with easy installation for a perfect fit every time, up to 95% faster than solder.
Join the conversation: