By Louis Free, AIA, URS Manager, Facilities Architecture/Engineering Services, New England
The Canadian Yukon can get mighty cold in the winter, but it can also get pretty chilly at the University of Connecticut, otherwise known as UConn.
To keep their students warm and comfortable, university officials determined that they needed to replace the existing heating/hot water systems in 12 student housing units known as the Hilltop Apartments. The problem was that this huge task had to be completed while the students were away for the summer, which put everyone on the project including mechanical contractor P & D Mechanical, Inc., Colchester, CT, on the fast track to get the job done on time for the students’ return for the fall semester.
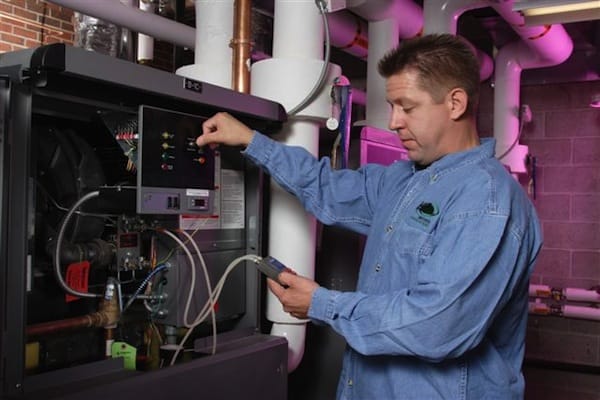
Installer Dave Warzecha, P&D Mechanical, checks the boiler operation.
The existing water heaters were coupled with fan coil units to provide space heating and domestic water needs. These needed to be replaced for safety and environmental reasons. Plans called for removal of the water heaters while leaving the fan coil heat exchangers in place. Renovations would also entail some re-piping of the buildings. Space heating and hot water would then be supplied by centralized boiler rooms at four of the 12 buildings.
Since there was no space for boiler rooms in any of the buildings, general contractor Dimeo Construction Company, Providence, RI, had to construct the rooms on the ends of the four buildings with underground piping supplying the other buildings.
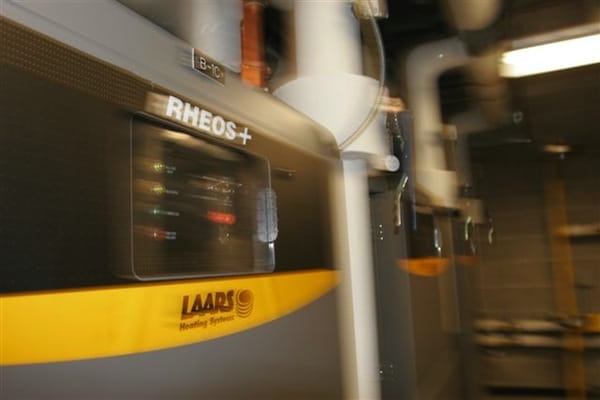
The redesign of the Hilltop Apartment complex was done by our architectural/engineering firm, URS Corp. in Rocky Hill, CT. Viktor Daragjati, PE, and I were among the firm’s team members responsible for the design of the new boiler systems for the twelve-building complex. Boiler options from four manufacturers were studied before settling on Rheos+ boilers from Rochester, NH-based Laars Heating System Company.
To make the new boiler rooms as inconspicuous as possible, we designed the rooms to match the exterior décor of the apartment buildings so they became simply an extension of the buildings. The overall size of the boilers meant space would only have to be added to four of the buildings instead of to each building.
One of the concerns was the need to match the aesthetics of the residential complex. The boilers we used have a very small footprint and generate a lot of capacity in a limited space, and that’s what we wanted. There were also some ornamental features added to make the rooms blend with the buildings. If you didn’t know anything about it, you would think they were part of the original building construction.
URS’ heat plant solution included the need for high-capacity, low mass boilers – not tandem, multiple boilers offered by one supplier. Space was at a premium. The need for low NOx emission levels and ultra-high fuel efficiency were also important issues. Basically, at the end of the day, we converged on Laars because for that particular application, it seemed to provide all of the capacity, efficiency and low emission that we were looking for.
One of the key stipulations by school managers was for boiler efficiency in the 95%+ range, and because of the low operating temperatures, the systems had to be condensing. Next, there was a concern at URS and the school about air pollution, so the boilers had to have lower than 10 ppm NOx emission rate. School managers scrutinized this very closely during the selection and submittal process.
The university has a cogeneration plant which requires the campus to meet a threshold emission limitation. The Laars boilers gave us low NOx emissions to begin with. Then with variable temperature control and increased efficiency resulting from operating in the condensing region, we would further limit those emissions, which we felt was a very important factor.
It was also important to have a system that would give the school redundancy and standby protection. So rather than choosing a five million BTU input boiler, we chose multiple boiler plants; the capacity and size of the boilers was a perfect fit.
Dave Warzecha, on-site project manager for P & D Mechanical, and his crews began by installing the site distribution piping, running it from the buildings to the boiler rooms, where the only holdup was the completion of the building additions to house the new boiler plants. This piping had to be covered by four feet of earth and have 1 ½ inches of insulation within the jacketing to meet energy code heat loss requirements. P& D’s contract was for the underground piping and the installation of the four boiler rooms.
Another contractor removed the old water heaters and rerouted piping within the buildings. Ultimately, P&D stepped in to complete the work on the last of the four-building complexes. Warzecha’s crews ranged from 37 to 40 people with a few more coming on to help when the completion of the last building group was added to the contractor’s schedule.
The project was divided between the two mechanical contractors because of the scope of the project and the need to have all the work completed in just two months.
While concealing the project as much as possible was the architects’ challenge, our team was faced with the challenge of finding spaces to run the new piping system. Piping was run in soffits through utility rooms, toilet rooms and over kitchen cabinets.
Three of the boiler plants are equipped with three 1.6 million BTU input Rheos+ boilers and the fourth has three 2 million BTU units. The boilers are being controlled by a building automation system (BAS) through a signal fed to each boiler. The BAS fires the boilers as need for both heating and domestic hot water. They are doing indoor/outdoor temperature reset for heating and they’re maintaining constant water discharge temperature when needed for domestic hot water production. Each boiler plant distributes hot water to two nearby buildings to limit the need for boiler rooms.
To dispose of potentially harmful acidic condensate from the condensing boilers, each boiler is fitted with a neutralizer kit from Laars. The condensate is run through a marble chip bath that neutralizes it from an acidic ph range of from 5.2 to 5.6 and then disposes of it down a typical sanitary drain.
The boilers have dedicated integral recirculating pumps with side-stream circulation. Some other manufacturers require you to provide those pumps separately and given our schedule, that was definitely a minus. The pumps take water out of the heating loop, warm it up, and return it to the primary loop.
The heating loop has its own secondary distribution pumps. These are variable speed pumps located in each of the three boiler rooms. The reason for this design is because of the high level of diversity you encounter during the various seasons of the year and especially as you go into the summer months when the buildings may not be fully occupied and the heating load is limited to domestic water demand.
The boilers’ ability to maintain discharge temperatures ranging from domestic hot water, to peak heating requirements provided the best demand-to-output capacity match at the most efficient energy level. Maintaining the highest efficiency level provides an additional way of controlling emission levels, because the more efficiently we operate, the less gas we burn and the fewer oxides we emit.
Temperature sensors feeding an energy management system from Andover Controls provide precise digital temperature control throughout the buildings. Students can change the temperature ±20 and building managers can override the system to accommodate students with special needs.
The Rheos+ boilers provide these features:
- Modulation of firing rate from 25% to full fire to match required heat loads and maximize efficiency.
- They have self-adjusting combustion systems for handling ambient conditions from sea level to 10,000 ft.
- They have a built in mixing system for low temperature return water protection while maintaining proper flow rates through the heat exchangers.
- They have a visible front control panel for easy diagnostics and access to internal electronics.
- And they have flexible vent and piping options for ease of installation and maintenance.
Students living in the Hilltop Apartments now enjoy the benefits of their retrofitted heating and domestic hot water systems. At last, there’s plentiful heat at UConn.
Join the conversation: