When the governor visits, people take notice. When he talks, people listen. Mississippi governor Phil Bryant recently spoke about Milwaukee Tool’s investment to the area, the company’s innovative product offering, and he gave some first-hand accounts of personally using the reliable tools during a recent media event at its Greenwood, MS, facility. “I am proud of our sizeable financial investment to Milwaukee Tools here in Greenwood, Mississippi,” says Bryant. “We still think manufacturing is the key, and this is the workforce that builds America.”
The governor was in town to recognize Milwaukee’s commitment to the community and its continued commitment to the end user with a $47 million investment in U.S. operations over the last five years. Of that, $15 million has gone into its Greenwood, MS, plant, which manufactures Sawzall and Hole Dozer blades. “We believe that Greenwood is one of our top global facilities to deliver products,” says Scott Griswold, president, power tool accessories.
Opened in 2001 with 87 employees, the then 120,000-sq.-ft. Milwaukee Tool Greenwood manufacturing plant has grown to 390,000 sq. ft. and 670 employees with a 2015 expansion, and represents more than just a facility that makes saw blades. “Milwaukee is about people,” says Jack Bilotta, plant manager at the Greenwood facility. “We build products that people use to support their families.”
Milwaukee likes to think they do things a little differently, setting themselves apart from their competition, starting with the end user first and foremost. “We take an inside out approach. It starts with the end user first by delivering innovation with a design strategy that solves end user problems,” says Griswold.
Milwaukee relies on the feedback of end users from across the country that are using the tools, takes the feedback and relays it to the engineering team in Brookfield, Wis., which, in turn, is sent for manufacturing in Greenwood.
“When it comes to extreme cutting applications and versatility in a wide range of materials, carbide is a technology that can deliver longer life for the accessory. But not all carbide solutions are equal,” said John Rossi, director of Product Marketing for Milwaukee Tool.
The manufacturing of the Milwaukee Sawzall Ax with Carbide Teeth blade sets itself apart from its competitors by starting off with blank, level coil stock, and then a grinding process to form the teeth, which creates a uniformity and consistency in the blades. From there, carbide, a mix of carbon and tungsten, is welded into the teeth of the blade, and subsequently digitally printed and packaged for shipping. “Ultimately, it’s time, temperature and force that go into the carbide blade,” says Heath Nunnemacher, program manager.
Competitors, on the other hand, miss the consistency mark by milling the teeth into the blade, which allows the blade to become dull over time.
The Hole Dozer Hole Saw Blades
Inspired by its namesake the bulldozer, the Hole Dozer, launched in 2015, is built to withstand the most punishing applications. Equipped with the first ever lifetime warranty against tooth breaks, this hole saw brings unmatched durability and increased productivity to users across every trade. “The Hole Dozer provides unstoppable durability through demanding applications,” Ryan Rudzinski, product manager.
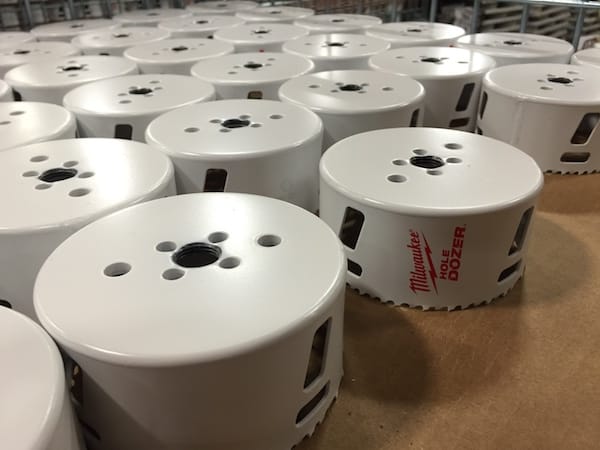
The inventory of Hole Dozer saw blades doesn’t stay at the facility very long; it includes a couple of days inventory.
The Hole Dozer Bi-metal Hole Saw demonstrates Milwaukee Tool’s continued commitment to delivering innovative accessory solutions to save time and increase productivity on the jobsite. “Bi-metal hole saws are unique, as they are a trusted hole making solution across a broad range of users. These users demand bi-metal hole saws that can cut through a breadth of materials for many different applications,” said Rudzinski. “Resulting from extensive jobsite research, the Milwaukee Hole Dozer delivers where all other hole saws have not. We were able to bring a fresh perspective to the category through a focus on the three main user needs when it comes to bi-metal hole saws: durability, life and plug removal.”
Join the conversation: