Among hydronic/plumbing and mechanical professionals, there are a few trade pros who make their craft into an art form. Their work is so refined and deliberate that the finished work takes on the appearance of mechanical mastery.
Tradesman and mechanical artist Orest Omeliukh is one of those. He’s drawn inspiration from the European approach to mechanical system design, though with his own flair.
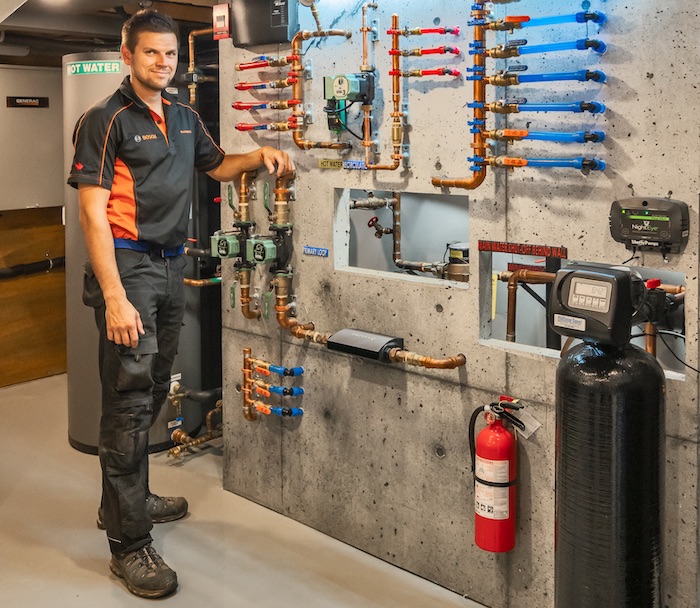
Orest Omeliukh
Across the big pond, hydronics are prolific, and mechanical components often see more human interaction than in North America. Components are sleek and clean looking, and installed within the occupied space instead of being relegated to cramped, dungeonesque mechanical rooms where resident spiders are rarely disturbed.
Omeliukh, who founded Blackrock HVAC Ltd. in 2014, was born in Ukraine, immigrating to eastern Canada at the age of three. His father was a tradesman who came to Canada to work on massive district systems.
“My Dad has designed underground steam mains up to 16 feet in diameter,” said Omeliukh. “He came here, to Mississauga, Ont., with 20 other mechanics, engineers and pipefitters. Half of those men stayed and raised families.”
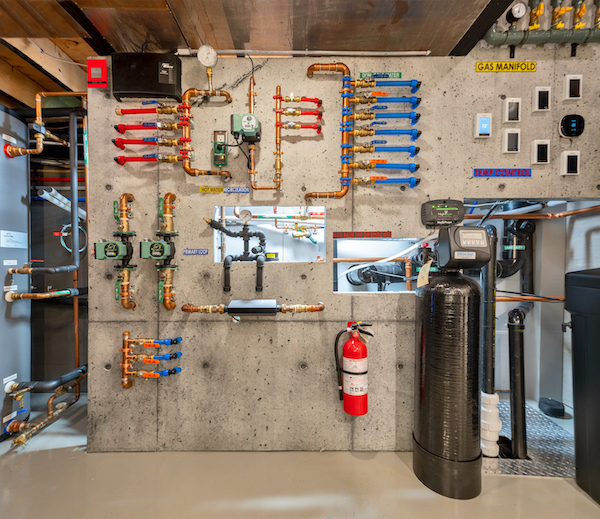
Recent trips back to Ukraine, Switzerland, Germany, and various other European countries left an indelible mark on Omeliukh’s style of work.
“I build the Bentley of HVAC systems,” he explained. “The systems are complex in regard to what they accomplish, but they’re very simple for the service contractor and the homeowner. I only take on two custom home projects per year, and each is unique and aesthetically pleasing. But form follows function.”
Every Blackrock mechanical room has four key elements: components and system design that provide absolute premium comfort and efficiency, a feature wall, painted floors and LED lighting.
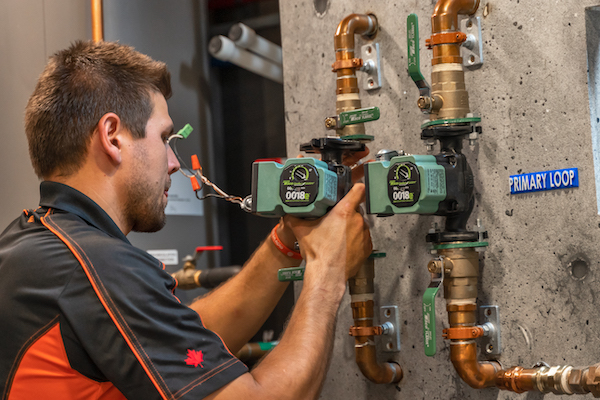
Orest Omeliukh, owner of Blackrock HVAC Ltd., finishes installing several circulators at the Gonell’s mechanical room.
In late 2017, Blackrock was approached by a custom builder, Gonell Homes, for a full gut remodel of a home in one of Tornoto’s older neighborhoods. Omeliukh had done work for the general contractor before, and the company’s owner, Will Gonell, hired Blackrock to design and install the comfort systems for his own residence.
“Will has been a mentor to me in a lot of ways,” said Omeliukh. “He’s an former U.S. Marine, so he has a very direct way of explaining things. He teaches and motivates simultaneously, with a wisdom beyond his years. When he asked me to build the mechanical system in his own home, he gave me full artistic license.”
War against bulkheads
Gonell’s two-story, 3,000-sq.-ft. home was stripped to the studs. The second floor was expanded to include a new master suite. Spray foam insulation and new windows were added throughout, and the domestic hot water recirculation line was insulated. Greatly reduced heat loss—Check.
The concept that evolved between Gonell and Omeliukh was to use six zones of radiant in-floor for primary heat, and a seventh zone served by a hydronic air handler, which shares high velocity ductwork with a heat pump. Domestic hot water is also provided by sidearm tank. Snowmelt in the driveway also draws from the condensing boiler in the basement, meaning that Blackrock had to provide four different water temperatures.
“This job was unique in that it was an old home,” said Omeliukh. “I wanted to show off the mechanical equipment within the mechanical space, yet eliminate it from view elsewhere. I call it ‘The War Against Bulkheads.’”
For air conditioning and backup heat, Blackrock installed a 2.5-ton Midea heat pump condenser paired with a Unico high-velocity air handler, allowing the branch ducts to be run within 2×4 stud walls. Proprietary sound attenuator branch ducts provide quiet airflow.
This air handler, along with the home’s Lifebreath HRV and an AprilAire 800 steam humidifier, is installed in a smaller mechanical space in the attic. Splitting the mechanical components between the basement and the attic was a tactic that helped Omeliukh win the War Against Bulkheads.
Masterpiece
“The basement mechanical room is the showpiece here,” Omeliukh. “Everything was selected carefully for function, then assembled in a manner that catches the eye, and provides ample room and lighting for service work. I used a ‘bunker’ theme here, as the room is like none other in the house, and really feels like a high-tech bunker.”
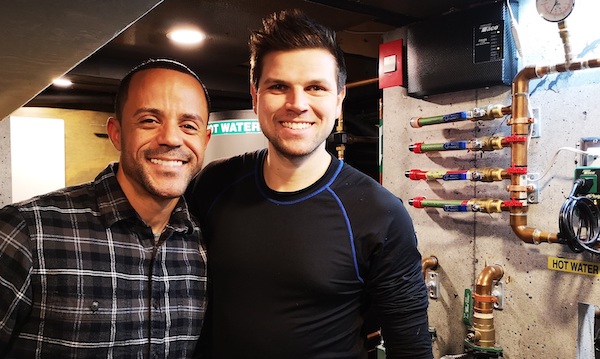
Will Gonell (left) with Orest Omeliukh in Gonell’s mechanical room.
Blackrock started with plywood walls covered in a very convincing poured concrete mural, giving the impression that each penetration was neatly core-drilled. In the past, he’s used murals portraying graffiti, art by Picasso, and a map of the Canadian Shield.
The 160 MBH IBC condensing boiler is piped primary-secondary. Omeliukh has calculated that the home’s heating load will only require 40 percent of the boiler’s capacity. When DHW or snow melt calls, the boiler will fire at 100 percent for rapid recovery. The rest of the time, it coasts along at low-load, condensing as intended.
The primary loop is circulated by a Taco Comfort Solutions 0018e circulator with Bluetooth capability. An identical pump is used on the 80-gallon indirect tank. This allows Blackrock to select between multiple constant speed, proportional pressure, and constant pressure modes as well as activeADAPT™, Taco’s self-adjusting proportional pressure mode.
The secondary loop consists of the eight heating zones: six radiant, one for the hydronic coil and one for the master bathroom towel rack. These zones are pumped by a pair of Taco VT2218 circulators, and use Zone Sentry valves for control. With the temperature sensing radiant circulators, Blackrock maintains a 20°F Delta-T. The zone valves are wired to expandable Taco zone controls, which communicate with tekmar WiFi thermostats.
“I use a lot of Taco products because of their reliability,” said Omeliukh. “They’re simple, the tech support is great, and the company culture breeds innovation and long term relationships.”
From the radiant manifolds in the downstairs mechanical room and two remote manifolds hidden neatly in the house, half-inch PEX was installed at nine-inch centers. This was poured over with a thin layer of Agilia lightweight concrete for optimal thermal performance and floor rigidity.
The system was designed with a -21°C (-6°F) outdoor design temp, and the boiler responds to actual conditions via outdoor reset for any heat call except DHW. Omeliukh insists the servicing the system is simple. He’s taken steps to ensure that those who come after him—whether a service tech or a homeowner —will agree.
Every zone features a label that was 3D printed in the Blackrock studio, and each loop has a pair of isolation valves. One wall of the mechanical room features a black box, wrapped in carbon fiber and illuminated with LEDs. This was for aesthetic purposes—simply to hide wires and piping that would otherwise clutter the installation. The box also contains piping and wiring diagrams.
“Unlike some contractors, I want the homeowner to be able to tweak the system or make adjustments in the event of an emergency,” explained Omeliukh. “And if a technician other than myself is going to work on it, I want to make their experience a good one.”
Pushing the limits
When Omeliukh dusts off his hands after a job, he goes home knowing that he’s done everything possible to deliver premium value. This mean taking extra, unconventional steps.
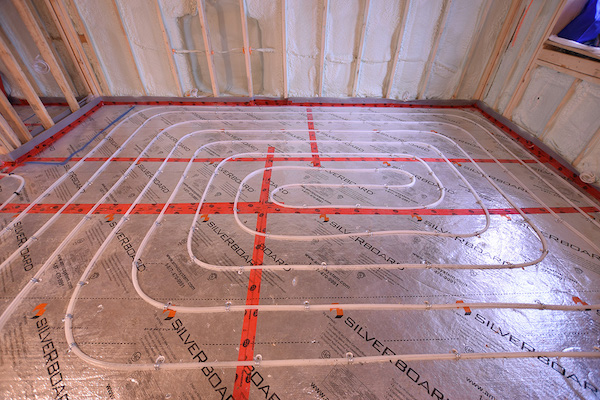
Gonell wanted discrete HVAC: highly visible only in the mechanical area, and invisible elsewhere. So, no t-stats; instead, Blackrock installed flush mount tekmar 084 sensors throughout the home. The tiny sensors are installed in a small indent in the drywall, then mudded and painted over. Wired to the tekmar 562 T-stats in the mechanical room, this approach allows occupants to manipulate temperature in any zone via an app, whether they’re sitting in the kitchen or at a tiki bar in Fiji.
The need for comfort paralleled Gonell’s desire for aesthetics. After installing radiant systems for years, Omeliukh’s recent visit to Germany reshaped the manner in which his company installs radiant tubing.
“If you look at an in-floor system through a thermal camera, you’ll find that loop ends are significantly cooler than the supply side. Most radiant installers use the “serpentine” method of laying tubing. While this is fast and easy, it tends to group all of the hottest pipe together, and same with the cooler loop ends. Lately, we’ve been using the ‘counter-flow’ layout, which is common in Europe.”
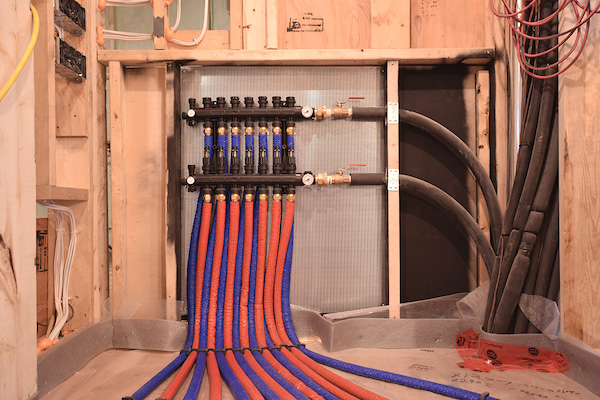
Blackrock insulates the pipe near his manifolds to avoid overheating the area.
The counter-flow design takes more planning and a little more time to install, but it alternates the warmest portions of a loop with the coolest across the floor. This provides even heat distribution across the floor.
“I like to push the limits on all our installations – it forces us to grow and develop new skills,” said Omeliukh. “On this job, that included a third tubing layout, which we’d never tried before: double-wall serpentine.”
The master suite featured two exterior walls. The double-wall serpentine method places the warmest portion of the radiant loop in close proximity to exterior walls, concentrating the most heat in the area with the most heat loss. It required some extra thought, and Omeliukh and his partners—as he calls the other HVAC tradesmen that he collaborates with on extensive projects—to pull tubing and re-staple it on one occasion.
Green elements
A tight building envelope, the latest condensing boiler technology and a full suite of ECM-powered circulators were just the starting point for efficiency at the job Omeliukh has dubbed “Operation Gonell.” He wanted maximize the efficiency.
The HRV is a whole-house system, connected to each of the home’s five bathroom fans. This is required by Ontario Building Code, but Blackrock took energy recovery one extra step. The unit is just an HRV chassis. During the summer, an ERV core is installed in the unit. Come heating season, the ERV core is swapped with an HRV core. This method provides optimal energy transfer regardless of outdoor conditions.
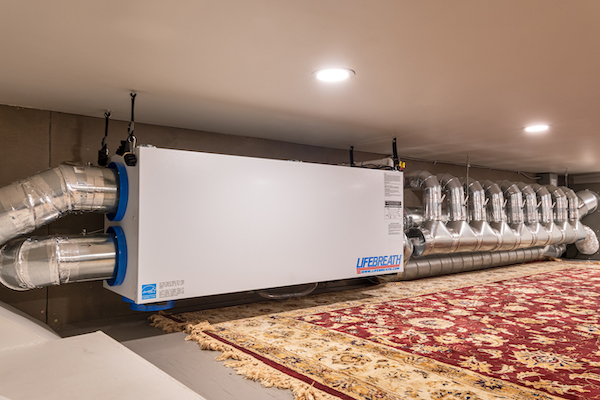
The HRV, Unico air handler and the steam humidifier share an impressive, insulated mechanical space in the attic, technically making that room an occupied space. So it needs to be conditioned during the winter. Blackrock had a plan for this.
“Boiler rooms are inherently warm,” said Omeliukh. “Too warm, for most of the winter. So we installed a central bathroom exhaust fan in the boiler room to move “free” warm air into the attic mechanical room. It’s energized by a thermostat when the temperature in the boiler room reaches 78°F, and does a fantastic job of maintaining a conditioned atmosphere in the attic. Blackrock calls this use of waste heat a “hybrid innovation.”
Finally, Blackrock took several steps to ensure that domestic hot water is provided efficiently. DHW lines were insulated, and the Taco 006e3 circulator used for recirculation is plugged into a SmartPlug control.
Using a sensor that mounts to the hot water supply pipe, the SmartPlug “learns” the daily hot water usage pattern in a home and adjusts the circulator run time to deliver hot water when needed. When usage patterns change, the SmartPlug adjusts run times automatically.
Blackrock also installed a ThermoDrain DHW preheat system. It includes a three-foot section of copper drain with an integral copper coil, and is installed on the main plumbing stack. Supply water to the water heater first passes through the ThermoDrain, collecting waste heat from the stack as an occupant showers. The Gonell home has five residents, with two teenagers, so being able to collect some of the heat is a bonus.
It’s pretty common to receive HVAC permit drawings that don’t reflect the structure or meet mechanical space requirements – especially on renovation projects,” said Omeliukh. “Because of that, communication between the designer, all the trades, and the equipment manufacturers was crucial on this project.”
“Gonell and I both wanted to use the best of the best component on this system,” he continued. “He gave me free reign to push my limits and incorporate everything I wanted to. From there, we just let all the elements fall into place.”