By Jana Summey
A few months after the “reopening” of the economy, understandably, business owners and government officials welcomed a return to normalcy. However, new and different risks are faced when reopening dormant buildings with stagnant water systems.
Several weeks of zero flow, low flow, and tempered water can result in microbiological growth, leeching heavy metals, and corrosion within our plumbing systems.
Planning is key
Let’s take a close look at steps building facility managers should consider in order to maintain water quality and safety in plumbing systems of unused or slightly used buildings (as defined by industry organizations including NSF International, Centers for Disease Control and Prevention (CDC), and the International Association of Plumbing & Mechanical Officials (IAPMO).
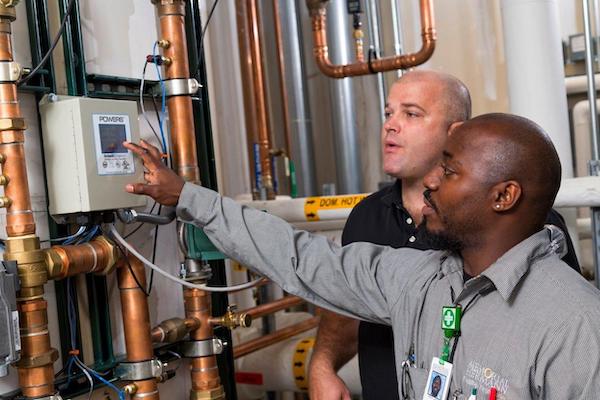
The IntelliStation digital water mixing system delivers mixed hot water throughout a hot water recirculation loop in commercial and institutional facilities. This digital solution can be integrated into a building automation system (BAS) to allow facilities managers to remotely monitor and control water temperatures.
Begin by documenting protection measures for staff and visitors. Consider working with a water quality expert or consultant. And, ask the local water utility the following questions:
- Have there been any recent water supply disruptions?
- Have standard checkpoints been inspected?
- What is the current disinfectant concentration?
If one isn’t already in place, create a map of the building’s plumbing system.
Before the initial flush, sketch out the building water system to identify low-use water outlets. Map out a flushing regimen in a unidirectional process starting at the water supply’s point-of-entry, to the peripheral distalpoints, and point-of-use outlets such as faucets and showerheads.
In large buildings, the water supply is often designed in zones and branches, such as different wings. Typically, each wing or set of branches will be served by the same riser. When mapping out the plumbing system, always start from the outlet nearest the water supply and proceed to the most distal outlets. Along this route, the flushing regimen should include the entire recirculating loop, both cold and hot water, all associated equipment and appliances, and all outlets including faucets, showerheads, eye wash stations, ice machines, hot tubs, therapy pools, and water features.
Establish or reestablish a flushing and cleaning regimen. Flushing is important because it clears out the low-quality water that accumulated during low use and replaces it with high-quality water from the municipal supply. The fresh water helps mitigate loss of protective scale as well as biofilm growth that emerged while the water was stagnant.

After the initial flush, ongoing flushes should be scheduled; continual flushes help to repair destabilized scale and minimize biofilm growth. Watts’ OneFlow System, shown here, uses a specially designed media where scale forming molecules are transformed into harmless crystals that won’t stick to pipes and components, eliminating scale for good.
These conditions need to be addressed because they proliferate the growth of Legionella and other waterborne pathogens, creating a high-risk environment for those with compromised immune systems. Proper flushing is a multi-step process including an initial flush, sequenced flushing, cleaning of fixtures and equipment, testing and monitoring, and additional flushing as needed.
Initial flushing and cleaning must be completed before resuming normal building operations. The sooner flushing is begun, the better. If possible, have staff start flushing now, even if the building’s reopening date is still unknown. The earlier a flushing regimen is initiated, the sooner water quality will return to normal. Prior to flushing, appropriate training for staff should be completed and PPE (personal protective equipment) should be provided. Guidance for this can be found on OSHA’s website.
It’s vital to flush the entire piping system from point-of-entry to point-of-use. This includes all water outlets, utility sinks, hose taps, piping currently used, as well as piping and fixtures in place for future installations. However, it doesn’t hurt to take special notice to the parts of the water system that have the greatest opportunity to make people sick. These include:
- Faucets used for drinking water or food preparation
- Drinking fountains
- Ice machines and refrigerators with ice makers
- Showers
- Kitchen sink sprayers
- Water features that generate aerosols (fountains, spas, etc.)
- Parts of the water system used by children, the elderly, and other susceptible people
An initial flush clears out contaminants that accumulated during stagnation and draws in fresh, high-quality water to the piping. Cleaning the fixtures removes contaminants from the complex internal structures at the point of discharge. Flushing requires an initial flush to get out low-quality water and contaminants, and follow up flushes that may bring the building back to pre-COVID-19 water quality. Ongoing flushing draws particles through and out of the system and brings in disinfectant from the municipal system that can help control biological growth. The longer service is interrupted, the more effort will be required for restoration.
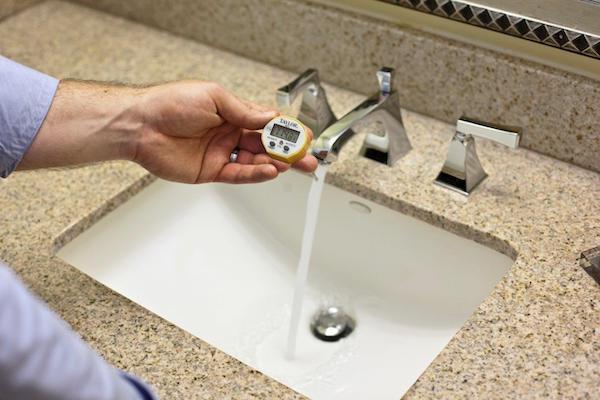
Once the building is reopened, conduct normal process of ensuring tempering valves are maintaining the desired temperature.
Flush zone by zone, starting with the zone closest to the water building supply. In each zone, start with the cold water plumbing first, followed by the hot water. Within the zone, open taps starting with the outlet closest to the zone origin, working toward the farthest point. Flushing should not end until the farthest point-of-use tap has flushed for a minimum of five minutes, and the cold water temperature at the most distal tap is constant.
In order for flushing to be most effective, consider the following:
- All valves should be in a fully opened position during the entire flushing process
- All aerators should be removed. If continued use is planned, clean or replace the screens prior to reinstalling the aerators
- Showerheads and faucets should be disinfected and sterilized. Consider replacing outlets if vulnerable populations have access
- Prior to operating the system after flushing, adjust valves back to normal operating positions
As part of the flush, all locations where water is stored should be identified, drained, and flushed with clean cold water. Examples include humidifiers, ice machines, and dishwashers. Most buildings have some form of water treatment in their plumbing system such as filters and water softeners. These should run as normal, be included in the flush, and should not be bypassed.
Once flow has returned after this initial flush, all hot water tanks should be drained. Temperature should be maintained, and the heater should not be turned off. Continual operation is important to prevent microorganisms from growing. Make sure that water heat storage temperature are sufficient to kill bacteria (131 to 140°F).
After the initial flush, ongoing flushes should be scheduled; continual flushes help to repair destabilized scale and minimize biofilm growth. The American Water Works Association (AWWA) recommends continued flushing for a minimum of 12 weeks. This allows the protective scale to re-stabilize and for harmful lead particles to be washed through the plumbing system.
Recommendations for ongoing flushes include:
- Open each point-of-use tap at least once per day
- Flush the entire building once per week during ongoing flushing
- It is not necessary to drain water storage during ongoing flushing
- Continue to flush the cold and hot water systems separately; cold first, hot second
Monitoring and testing
Monitoring and testing should start for Legionella, other bacteria growth, and disinfectant levels prior to the initial flush, throughout the ongoing flushing, and on a predetermined schedule going forward. Monitoring and testing are the only ways to know the health of the plumbing system.
At the end of the initial flush, disinfectant levels should be checked. The concentration level of chlorine, the most commonly used disinfectant, should be measured at the point-of-entry and in the cold water of the most distant tap of each zone after the tap is flushed. Comparison of the point-of-entry concentration to the distal tap concentration will give an indication of the protection being provided to the entire plumbing system.
If other disinfectants are used, such as monochloramine, be sure to measure and compare its concentration at point-of-entry and distal outlets. Water temperature should be regularly tested and recorded.
The system should be tested for Legionella by a certified laboratory. Many facilities will choose to work with a consultant for this process. Samples should be collected at least 48 hours after final flushing and return of normal operation of the water system. Multiple samples should be collected to ensure accuracy and prevent false negative results. Samples should be taken at multiple locations throughout the system, from point-of-entry to point-of-use.
Hyperchlorination or shock disinfection should be conducted if testing proves unacceptable levels of Legionella. This is where a higher than normal level of chlorine is flushed through the plumbing system for a specific length of time, and the water temperature is raised for rapid kill. The cold water system should be flushed from point-of-entry to point-of-use, including all fixtures. The water should reach a CT of no less than 3,000 mg-min/L. “CT” value is the concentration of disinfectant and contact time with the water being disinfected.
Systems that have high levels of Legionella, or are known to have heavy biofilm, may require even higher CT targets. Higher chlorine dosage may allow for shorter disinfection contact times. Always take proper precautions to ensure there is no inadvertent exposure to occupants. Strict access controls should be in place. Conduct testing to ensure chlorine levels are in normal ranges at the conclusion of treatment. When hyperchlorination is complete, the system should go through an additional thermal flushing.
Even if unacceptable Legionella levels are not found after thermal flushing, hyperchlorination should still be considered, especially in buildings where high risk or immune compromised populations could be exposed.
Following, adjusting, and creating a water management plan
A facility management team should record all monitoring and testing practices including the frequency, locations, and results. If there is a water management plan, those findings should be integrated into the record keeping portion of the plan. If a water management plan does not exist, we strongly encouraged the creation of one. Most healthcare facilities are required under the Centers for Medicare & Medicaid (CMS) mandate to have a water management plan. Failing to do so can cause a facility to lose Medicaid and Medicare reimbursements.
Implementing a water management plan as outlined in ASHRAE 188 will help maintain a high-quality level in a building. The Centers for Disease Control (CDC) has developed a water management plan toolkit based on ASHRAE 188. The toolkit aids in the understanding of risk levels of different building types and devices and walks step by step through the requirements of a healthy water management plan.
Maintenance and Recommissioning
As part of the process of reopening a building, all mechanical equipment should be inspected. Examples include cooling towers, boilers, pumps, backflow preventers and digital mixing stations. Essentially, the water systems and equipment should be recommissioned as if it were a new building. Make sure any scheduled maintenance that may have been missed during building closings are completed and recorded in accordance with normal practices.
Some general guidelines include:
Digital thermostatic mixing
During/before closing
- Drain the piping system prior to closing if planning for a long-term building closure
- If draining the system isn’t an option, increase production and storage of hot water above 150° F, and keep the building pump running at full temperature by bypassing a TMV or setting the DMV to full hot
- Conduct a periodic purge of all dead legs to keep the system reasonably clean
At reopening
- Conduct either a high temperature water purge, hyperchlorination shock, or both
- Generally, calibration of mixing valves is not needed
- Once the building is reopened, conduct normal process of ensuring tempering valves are maintaining the desired temperature
Backflow
- Conduct a visual inspection
- If the water supply was completely shut off and the pressure decreased, all reduced pressure zone units need to be repressurized correctly, and the relief valve should be closed
- All pressure breaker valves also need to be repressurized correctly and the relief valve should be closed.
- The pressure breaker valve should be spill resistant, but it should still be checked
Gas connectors
- Assuming equipment has been turned off, a device such as FloPro™-MD can assist with a startup check to ensure each piece is operating at manufacturer’s specification
- Verify proper gas supply to any gas burning appliance with a BTU rating of 325,000 BTU’s or less, whether it is in a commercial kitchen or not
Drainage systems
- For general drains, there are no special requirements. However, a visual inspection should be part of the reopening plan
Stainless steel piping and drainage systems
- Other than the absence of water in the traps from either back siphonage or evaporation, stainless steel piping systems require no special considerations when being returned to full service after periods of non-use
- Stainless steel pipe and fittings are resistant to corrosion caused by decomposition of organic matter and the subsequent formation of hydrogen sulfide gas or microbiologically-influenced corrosion
Rainwater harvesting
- Purge the system via the hose bibs or flush out the system by opening the flush valves to create a steady flow of water
- Check the tanks to ensure the aerator is functioning and the inlet pre-filter is in service
Water quality solutions
For most water quality devices, it is a good idea to flush the unit. However, it’s always best to consult manufacturer guidelines for each device.
UV systems
- Inspect to ensure the light is working correctly
- Check to make sure any scheduled maintenance wasn’t missed
- Visually inspect the vessel
Sediment/point-of-entry filtration
- Visually inspect
- Clean any clogs and replace filters when needed
Point-of-use filters
- Visually inspect
- Clean any clogs and replace filters when needed
- Check to make sure any scheduled maintenance wasn’t missed
Measuring instrumentation
- In measuring instruments such as the CIX Instrument from HF scientific (chlorine measurement), there is a potential for reagents to crystallize in the tubes if there is a sudden loss of power or power is off for an extended time
- During inspection, in the rare event that crystallization has occurred, the unit needs to be primed and reagents replaced
Snow melt
- The snow/ice detector should be cleaned with soap and water
- Inspect the control display to ensure there are no error messages due to faulty sensors
Water Heaters
- Determine if the manufacturer recommends draining the water heater after a prolonged period of non-use
- Ensure that all maintenance activities are carried out by professionals or according to the manufacturer’s instructions
- Make sure the water heater is set to at least 122°F and consider higher temperatures (131°F -140°F) for a quicker kill
- Ensure that measures are taken to prevent scalding if the water heater is set to >130°F
- Wipe down the outside and control with disinfectant
- Conduct proper startup by authorized service agent
- Conduct a significant blowdown of all components
- Check combustion and calibration, perform all safety device testing, and verify all system operating parameters are correct and functioning
Additional Equipment to Be Inspected:
Hot tubs, spas, therapy pools
- Check for existing guidelines from local or state regulatory agency(ies) before opening for use
- Visually inspect for slime and biofilm prior to refilling
- Perform a hot tub/spa disinfection procedure before use per CDC guidance
Cooling towers
- Revisit startup and shutdown procedures
- Follow manufacturer guidelines and industry best practices
- Visually inspect for slime and biofilm prior to use
- Assuming the cooling tower has been well maintained, proceed with disinfection procedures. Guidance can be found from the Cooling Technology Institute: http://www.cti.org/downloads/WTP-148.pdf
Maintaining system after reopening
Planned and detail cleaning should be part of the reopening process. This includes proper maintenance of all equipment and fixtures, and the replacement of filters from point-of-entry to point-of-use. Be sure to follow manufacturer guidelines and contact the proper authorities when necessary.
Twenty-four hours before reopening the building, it’s recommended to conduct a round of checks. Bring the hot water system back up to 140° F. Open all outlets and flush until they reach a minimum of 131° F. After flushing, conduct a final round of sampling to ensure there is no contamination.
Once the building has resumed normal operation and the water system is back to standard function, the main priority will be maintaining water system quality and safety. If there is no water management plan prior to the disruption, create one immediately. This should include a schedule for monitoring and testing disinfectants, bacteria levels, and water temperature. Follow the plan, document activities, and adjust as needed. If an issue arises, promptly address it and notify authorities if deemed necessary.
If the building is scheduled to reopen within one month, continue a normal control regimen if possible. If the time to reopen the building is unknown, or if its scheduled to reopen longer than 1 month away, there are precautions that can be taken during that time to increase water quality prior to pre-open flushing and chlorination.
Consider the following:
- Conduct low-usage weekly maintenance
- Conduct weekly visual inspections
- Initiate operation of moving parts such as pumps for at least 10 minutes per week to prevent seizure and failure
- Increase water temperature to 140° F for at least 1 hour per week to reduce bacteria growth
- If equipment such as a water heater has a thermal sterilization cycle, utilize it per manufacturer recommendations
- Maintain normal disinfectant levels
- Flush outlets on a weekly basis
- Ensure all storage maintains proper disinfectant levels
- Document all activity, monitoring, and testing
- If it is decided to close certain systems, drain and dry if possible
If the decision has been made to not heat water within the plumbing system during closure, then consider the following:
- Close the building and do not drain the system
- Turn off storage tanks, drain, and the water supply
- Consider conducting thermal flushing and hyperchlorination prior to shutdown
If a building is not being fully shut down but will be under low-use conditions, consider the following options to maintain the system:
- Flush cold water systems on a regular schedule to maintain temperature and disinfectant. Free chlorine residual should be at or above .2 mg/L
- Monitor and maintain the hot water system at distal outlets
- Monitor and record supply water temperature and disinfectant concentration
- Restrict access to any unused portions of the building
- Document all monitoring, testing, and maintenance
Additional Resources
There are a multitude of tools and guidance to assist in maximizing water safety and minimizing water risks when preparing to reopen an unused or slightly used building:
- CDC Toolkit: https://www.cdc.gov/legionella/wmp/toolkit/index.html
- Preventing Legionnaires’ Disease: A Training on Legionella Water Management Programs: https://www.cdc.gov/nceh/ehs/elearn/prevent-LD-training
- Hotel Guidance: Considerations for Hotel Owners and Managers: How to Prevent Legionnaires’ Disease: https://www.cdc.gov/legionella/wmp/hotel-owners-managers.html
- From Plumbing to Patients: https://www.cdc.gov/hai/prevent/environment/water.html
- Preventing Occupational Exposure to Legionella: https://www.cdc.gov/niosh/docs/wp-solutions/2019-131/default.html
- CDC Model Aquatic Health Code
- CDC Healthcare Water System Repair and Recovery Following a Boil Water Advisory or Disruption of Water Supply
- ASHRAE Standard 188: Legionellosis Risk Management for Building Water Systems
- ASHRAE Guideline 12: Minimizing the Risk of Legionellosis Associated with Building Water Systems
- Cooling Technology Institute Legionellosis Guideline 2008 (WTP-148)
- Cooling Technology Institute Legionellosis Guideline 2019 (GLD 159)
Learn more about ensuring safety in commercial buildings by mitigating the risk of Legionella and other waterborne bacteria at www.legionella-strategies.com.
Jana Summey, MBA, Watts Healthcare Vertical Market Manager, has nearly 20 years’ experience in the MEP (mechanical/electrical/plumbing) design and architectural design industries. She is a popular speaker on mitigating Legionella through a multi-barrier approach in on-premise plumbing systems – from point of source to tap. Recently Jana navigated her mother through the experience of being exposed to Legionnaires’ as a hospital patient, gaining valuable insight into the serious threat Legionella poses for at-risk populations.