For professional tradesmen, managing labor costs is a balancing act. Cutting expenses too aggressively can compromise productivity and safety, while failing to optimize labor strategies can eat into profitability. The key is to implement smart, strategic measures that enhance efficiency without putting workers at risk.
Optimize Work Schedules For Maximum Efficiency
One of the most effective ways to reduce labor costs is by structuring work schedules to minimize downtime and maximize output. Poorly planned schedules often lead to unnecessary overtime, idle time, and workforce inefficiencies. To prevent this, tradesmen should:
- Analyze Workflow Patterns – Assessing job site productivity can reveal gaps where time is wasted. Identifying these inefficiencies allows for schedule adjustments that eliminate bottlenecks.
- Use Staggered Shifts – Instead of overloading workers during peak hours, staggered shifts can distribute labor more evenly throughout the day, reducing overtime costs.
- Leverage Skilled Labor Efficiently – Assigning the right workers to the right tasks prevents highly skilled professionals from performing lower-value tasks that could be delegated.
By streamlining work schedules, businesses can improve labor utilization, keeping costs in check without overburdening workers.
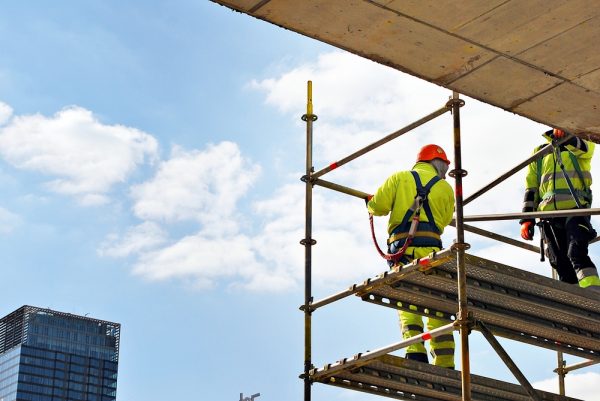
Implement Job Site Organization To Improve Productivity
A well-organized job site is critical for reducing wasted time and increasing efficiency. When workers spend less time searching for tools, materials, or information, they can focus on completing tasks more quickly and safely. Consider these strategies for better site management:
- Standardized Material Storage – Keeping tools and materials in designated areas prevents workers from wasting time locating necessary items.
- Clear Work Zones – Establishing specific zones for different tasks helps reduce confusion, streamlining movement and improving efficiency.
- Pre-Shift Planning Meetings – Holding a short daily meeting helps keep everyone up to date on their assignments while also preventing delays and miscommunications.
An organized work environment allows crews to stay on task, reducing unnecessary labor hours while maintaining safety and productivity.
Leverage Technology To Streamline Workflows
Technology is revolutionizing the trades, offering opportunities to cut labor costs while enhancing safety. Digital tools and automated systems can simplify tasks, reduce human error, and improve job site coordination. Some effective ways to leverage technology include:
- Project Management Software – Advanced platforms can help supervisors track progress, allocate resources effectively, and reduce scheduling conflicts.
- Wearable Safety Tech – Smart helmets, vests, and other wearables can detect fatigue or unsafe conditions, preventing accidents that lead to lost work hours.
- Automated Equipment and Robotics – In some cases, automation can reduce reliance on manual labor, completing repetitive tasks more efficiently and with greater precision.
By integrating technology, tradesmen can reduce time-consuming manual processes while maintaining a safe and structured job site.
Use Scaffolding and Modular Components To Reduce Labor Needs
Construction projects often require extensive labor for assembling and disassembling temporary structures. Using scaffolding components designed for quick assembly can cut labor costs significantly. Pre-engineered scaffolding solutions reduce setup time, allowing workers to focus on core tasks while maintaining site safety. Modular components also allow for faster adjustments and repositioning, reducing the amount of labor needed for modifications.
Monitor Performance And Continuously Improve Processes
To keep labor costs down while maintaining safety, businesses must consistently evaluate and refine their processes. Regular performance reviews and feedback loops help identify areas where improvements can be made.
- Track Labor Productivity Metrics – Use data to analyze how long tasks take and where inefficiencies exist.
- Encourage Worker Feedback – Employees on the ground often have the best insights into workflow improvements.
- Adapt To New Industry Practices – Staying informed about new labor-saving techniques and technologies allows businesses to remain competitive.
By continuously optimizing operations, tradesmen can maintain high standards of safety and productivity without incurring unnecessary labor costs.
Saving on labor costs doesn’t mean sacrificing safety or job quality. With the right approach and latest tech, we can come together to create an efficient and secure work environment.
AUTHOR BIO: Julio Black is the Head of Product Marketing at AT-PAC. He has 15 years of industrial and commercial scaffolding experience, along with technical expertise, a strategic mindset, and leadership skills. Black is committed to driving business results, fostering innovation, and creating exceptional customer experiences.
Join the conversation: