Managing a successful manufacturing business involves streamlining your output, revenues, ensuring client satisfaction, and promoting efficient business operations. Global supply chains and product demands were on a steady rise until COVID-19 disruption. With the market and businesses gradually moving to normalcy, productivity increase and operational efficiency will be vital for improving manufacturing productivity. Here are some practical ways to enhance your manufacturing productivity.
Ensure easy access to digital communication tools
As a team leader in a manufacturing company, there are tough decisions you may take. From improving on and off-site workers to giving your team a chance to be innovative, you need to keep yourself ahead of the competition. Employee access to systems that enable them to perform effectively and efficiently is one sure way to enhance manufacturing productivity levels. You can achieve this by integrating mobile solutions and cloud services to increase your production line efficiency even outside the workplace. This promotes remote access to information and improving their work-life balance.
Embrace artificial intelligence
Successful businesses that engage in manufacturing across industries leverage technology to ensure stress-free access to collaborations, communication, and data. Companies must embrace AI mechanisms and tech tools to increase productivity, meet deadlines and schedules, and enhance teamwork. AI-enabled manufacturing tech can get remote and on-site workers the most updated analytics in real-time to manage manufacturing timeframes or scheduled equipment maintenance. AI provides mobility and a significant amount of data and can accomplish more in less time. This will likewise ease the workload, reduce time-wasting activities, and intensify productivity.
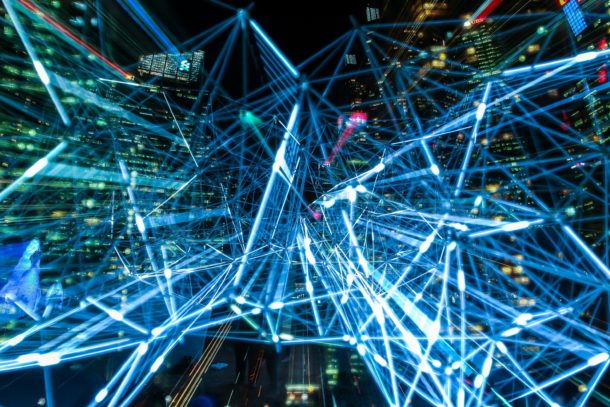
Maintain optimal inventory
You’ll need a proper storage and utilization plan if you have a lot of inventory. Optimizing your inventory is particularly essential when you are adopting a lean manufacturing principle. The lean concept was documented in the early 1900s. Still, it took off in the 1930s after Toyota founder Sakichi Toyoda, chief engineer Taiichi Ohno and his son Kiichiro Toyoda produced the Toyota Production System (TPS).
The lean manufacturing principle seeks to minimize wastage and costs while maximizing productivity and continuous quality improvement. Therefore, it is prudent to monitor rejection rates, falling quality, and delayed deliveries to rectify them with your supplier or possibly find a new one. It is also best to request assurances that deliveries will continue unabated, especially when your supplier is undergoing any significant change like selling to another firm.
Implement a mobile communication strategy
You can accomplish so much with internal mobile communication than just information management and sharing. An excellent internal communication plan can promote community development among employees and foster good relations, which is vital for achieving team goals. Internal communication systems are an essential business component, particularly for frontline workers. This is similar to how mobile devices have transformed and simplified individual lifestyles. For a manufacturing business, this can be revolutionary. Since most non-desk workers have limited access to email, implementing an excellent mobile communication strategy is critical for keeping regular contact across the organization.
There are many ways an operational internal mobile communication impact manufacturing productivity, including;
- Empowering frontline production staff to contribute valuable insight and ideas for superior innovation.
- Breaking down hierarchies and information feeds for smooth, effective collaboration and real-time interactions for quick problem-solving.
- Building a single data and system portal with the company for complete business access and ensuring an all-in-one interface for their tools.
In the present era of AI, AR, VR, and chatbots, industry 4.0 is here. Emerging operational technology is changing procedures for cutting, machining, and producing quick, safer, and more efficient manufacturing productivity. These advancement calls for different skills to work in an IoT environment. With an excellent mobile communication tool, manufacturing businesses can upgrade their present workforce with regular training and education. This enables them to step up and keep pace with the innovative devices.
These current jobs must foster more profound employee commitment since workers are freed from repetitive production lines. Investing in continuous workforce training means your workers can have more independence through higher cerebral jobs, translating into a higher productivity rate.
Capitalize on the latest manufacturing trends
Keeping up with the most recent manufacturing tech trends is among the ideal approaches for improving efficiency in manufacturing. For instance, businesses now adopt industry-defining technology to manufacture products like the dart pod to enhance user experience. Therefore, it is vital to stay alert and competitive with present digital innovation. Machine learning, Augmented Reality (AR), the Internet of Things (IoT), and many others are among the most popular tech trends in the industry.
Commit to planned maintenance
Disregarding regular maintenance is the quickest way to slow your business productivity—downtime for scheduled maintenance costs considerably less than downtime due to worn-out or broken equipment. Breakdown may come at the worst possible time, which is why you must schedule your maintenance. For planned maintenance to be effective, you should;
- Schedule regular preventative maintenance.
- Train all machine operators on troubleshooting and maintenance processes.
- Identify the best maintenance times using data from floor and workflow procedures.
- Avoid skipping or delaying maintenance.
A Preventive maintenance plan guarantees that your hardware keeps on running without any surprise work halt or downtime.
Remove any unused machinery
A few bits of unused hardware can be a real drag for your manufacturing productivity. It doesn’t simply create a mess but can take a chunk of the hard-earned cash in maintenance cost, which doesn’t do your profits any good. So clutter is something you should certainly avoid. In addition to getting rid of any pointless machinery, hardware parts, and tools, you may consider choosing between equipment loans or leasing to avoid getting stuck with outdated machinery in the future.
With the above tips and pointers highlighted here, you should have a solid foundation for improving your manufacturing productivity. To reemphasize, these are selected means since there is no single answer for increasing your manufacturing productivity levels. Therefore, it is practical to be creative and keep note of the workings of your particular business and industry.
Join the conversation: