My company, Foley Mechanical, Inc. was invited to bid on a large commercial radiant project in a new healthcare facility being built in suburban Maryland, about 20 miles north of Washington, D.C. We would be the subcontractor of the primary mechanical contractor. After considering doing the work in house, the primary contractor decided it would be quicker and easier to bring us in as radiant is our specialty.
We submitted a proposal and were awarded the contract. As this was a commercial project, full documentation was required which included design, shop drawings, and submittals. The radiant tubing manufacturer, Mr. PEX, was instrumental in working with me to put together the design and submittal package. After several revisions, the design package was approved and materials were ordered.
Several coordination meetings were held on site to determine scheduling, installation techniques, installation sequence, coordination with the concrete sub and other trades, and manifold locations.
We installed radiant floor heat in two areas of the building: the cafeteria, which is slab on grade, and the main entry mezzanine, which is concrete poured over steel decking. It was imperative for system operation to specify the correct insulation. We used 2” extruded polystyrene under the slab on grade zone. The mezzanine zone will have spray foam insulation under the steel decking.
Scheduling was critical. We had one day for rough-in on each zone. We arrived on site at 6am for a mandatory safety meeting. Full safety gear was required: work boots, hard hats, safety vest, eye protection and ear protection. The first step was mounting the manifolds. Then we started laying the loops, 14-loops for the first zone and 10-loops for the second zone.
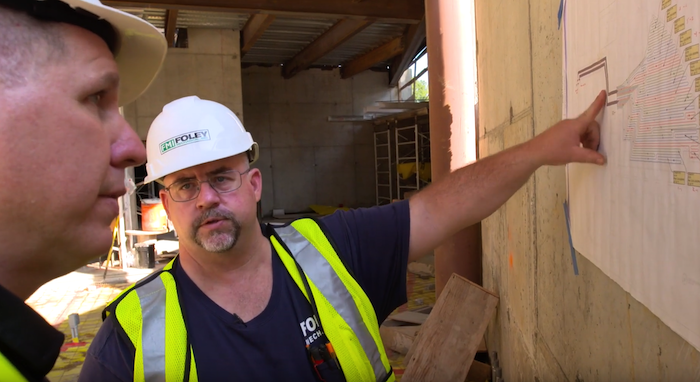
We invested in three Pex-Gun tie tools to increase speed and productivity over cable ties or squiggies. One man lays out the tubing while two men follow behind tying the tubing to the rebar with the Pex-Guns. The tubing installation follows a scaled tubing layout design provided by Mr. Pex. Another man attaches the tubing to the manifolds. This set-up makes quick work of tubing rough-in. My crew really liked the flexibility of the Mr. Pex tubing and the simplicity and ease of installation of the Mr. Pex manifolds.
After the tubing rough-in was complete, the entire system was pressurized with air to 100 PSI. It had to hold pressure for 24 hours before the concrete was poured. This pressure test was observed and documented by the primary mechanical contractor, the GC and the owner’s agent/engineer.
The concrete slab was poured the next morning. We had one of our techs on site to confirm the pressure test and observe the pour. This was a pumped pour so we wanted to make sure the concrete was poured without damaging the tubing. Pressure was monitored continuously during the pour. A repair kit was on hand in case the tubing was cut or damaged. Luckily, it was not needed.
Both slabs were poured without incident and are holding pressure. We will return when the building is complete and the mechanical system is started. We will flush and purge the radiant loops, coordinate the controls and motorized valves, and test & balance the radiant system. We have 10-turn balance valves on the return mains. In addition, the Mr. Pex manifolds allow for micro-balancing on each loop.
The building owner is looking forward to warm comfortable floors once the building is occupied. By partnering with the mechanical contractor, we both came out ahead. The job was done quicker and easier as we do radiant on a regular basis. We could not have done it without the help and support of Mr. Pex.
Dan Foley is owner of Foley Mechanical, Lorton, Va.