Similar to the way the rest of the world was impacted, employers and employees of the propane industry in Canada found that the COVID-19 pandemic brought with it a tremendous disruption to normal working patters. As the numbers of new infections continue to decline in most regions across the country, there are still longer-term safety concerns – many of which also include social distancing policies – that will likely alter the way propane workers operate in the foreseeable future. Technological solutions can help overcome some of the most challenging aspects of resuming and maintaining normal operations.
For many employers, addressing the question of how to bring propane workers back to the job in a safe and healthy manner presents a tremendous challenge. Contactless and remote solutions may be ideal for propane work, as these platforms provide a way to still effectively get the propane to end users despite any challenges that may be encountered while also preventing unnecessary physical contact.
Contactless technologies have the unique capacity for propane workers out in the field – even those who are not fully trained yet and those who are not familiar with the details involved and the safety issues that can arise when transporting and filling propane tanks. They can use the platform to connect with experts in the home office to clarify any questions that may arise in the normal course of doing their duties. In addition to the safety benefits offered by reducing physical contact, you can also make sure that any employees can get immediate access to safety experts who can walk them through any hazardous situations that may be encountered when filling and transporting pressurized propane, such as a leak or threat of combustion. And while it may be tempting to think that the same functionality can be achieved through a standard video call, contactless technology offers so much more.
In addition to functionality that supports HD-quality video calls, these technologies feature a unique drawing tool that works directly on the live video feed to make clear notes on the live screen, to put a circle around the targeted area or to sketch an arrow to pinpoint the precise areas of concern. Taken together, these features empower employees in the field and those in the office to work closely together without physical proximity, but still in a way that ensures problems are identified and resolved quickly. Workers get correct answers immediately in a way that addresses the uncertainty that may arise from a standard video feed. This uncertainty poses a huge problem when safety concerns arise or may arise if one step in a process is completed incorrectly or ignored. Anyone working with propane on a regular basis understands that a safe situation can quickly change – and it’s worth having immediate contact and clear guidance on how to best remedy any safety threat that may emerge.
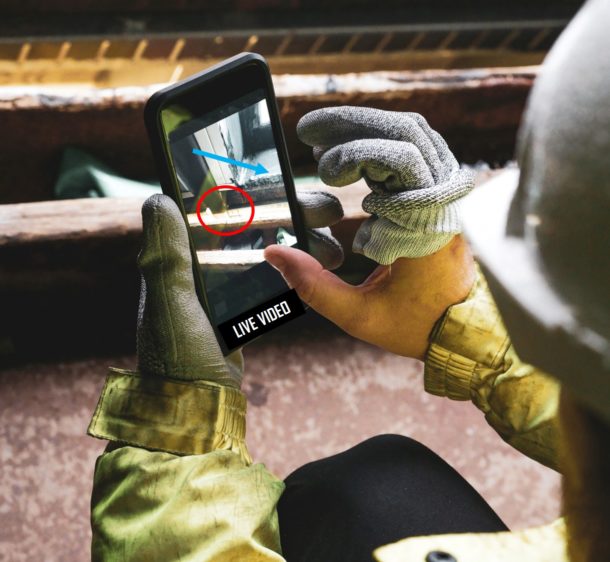
For example, contactless technologies can clarify any questions that arise while on the job site in real-time, ensuring that processes are followed correctly, and questions are answered quickly. During the transport and filling of propane tanks, questions often arise about the differences in tanks and how to correctly align any valves or hoses to ensure that the tank is filled properly. Additionally, workers may have questions when they encounter older tanks and fittings that may not be in great condition. When questions like this arise, the field workers can show his supervisor a live video stream of the area in question and then use a digital drawing tool on the actual video to circle or point to the exact connectors, hoses, valves, etc. needing to be addressed so they together ensure the propane is delivered safely. This type of immediate and clear communication can ensure that workplace conditions remain safe for employees, without losing productivity by waiting for clarification.
However, before jumping in and implementing any new communication platform, companies should proceed cautiously given security concerns – which became paramount during the COVID-19 pandemic. Many companies made quick changes to enable a remote workforce, but unfortunately, this led to many hacks and data breaches. Without proper security protocols in place, there is always the danger that a video meeting could be hacked, which can lead to a devastating data breach for contractors and construction companies working on highly sensitive projects.
While the promise of contactless solutions is great, it’s still vital to ensure that these platforms are deployed in a secure environment. Companies should take precautions to ensure they are only working with trusted and reputable industry experts that can identify potential security concerns and ensure they are addressed fully. This is the best way to protect your company from a costly and reputation-damaging data breach.
Shifting to new working environments will be a challenge for companies in the propane industry. The best way to ensure your continued success is by identifying tools and resources that can be implemented in a way that promotes remote working and social distancing policies. Contactless technology also has the added benefit of enhancing workplace safety, which is crucial in an industry that has the potential to be dangerous.
Contactless solutions will likely play a big role in the transformation of these industries, to both meet the immediate safety concerns that arose from COVID-19 and to address long-term safety goals of the industry. They can be highly effective at both ensuring work still gets done on pace with project timelines and that it gets done with expert oversight and the safety guidance necessary. Now is the time to prepare for the future and begin to explore ways that contactless solutions can address the unique needs of your company in its new working environment.
Larry Dorie, CEO and Co-Founder of RHUB Communications, creators of one of the most secure on-premise web conferencing and remote support tools for enterprise organizations.
Join the conversation: