For residential-only contractors, multi-family heating projects have a unique set of challenges. These jobs progress like commercial projects and need to be designed as such. Of course, they’re still residential in nature, but for the most part, it’s commercial work.
J.A.M. Plumbing & Heating, Inc. has built an interesting space in the skilled workforce of Rockland County, N.Y. The company is small, when compared to most commercial/industrial contractors in New York. And they’re very good. The owner, Joe Mezzasalma, started the firm in 2003.
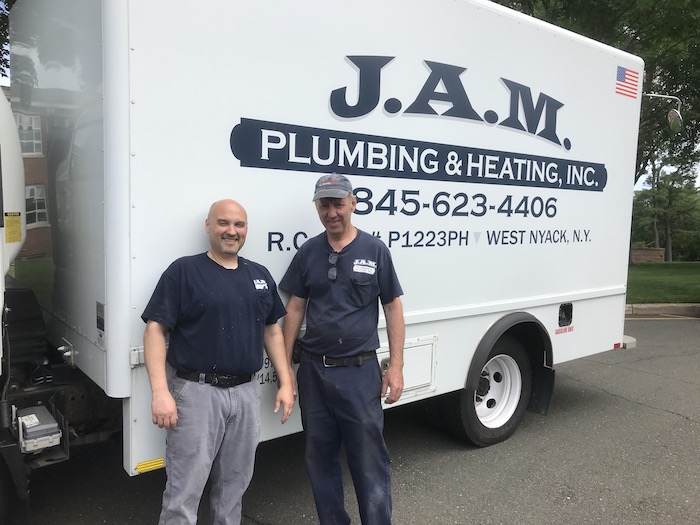
Joe Mezzasalma (left) with Master Plumber John Schauder.
“People don’t hire J.A.M. if they’re simply price shopping,” said Tom Dwyer, at rep firm Venco Sales, who has known Mezzasalma for 12 years. “Joe is a craftsman. People hire him because they know he can make a difference.”
J.A.M. never works outside of Rockland County. In fact, the four-person crew, which includes Mezzasalma, is almost exclusive to five towns; Orangeburg, Sparkill, Tappan, Blauvelt and Piermont. There’s more than enough work without travelling farther.
Multi-family service and replacement
One of J.A.M.’s areas of expertise is multi-family housing. And there’s plenty of it in Rockland County, as far as suburban areas go. Blue Hill Commons is a condominium neighborhood built in the 1970s with 15 buildings. They range in size from four to 12 units per building.
“We’ve done service work at Blue Hill Commons for more than a decade,” said Mezzasalma. “Each year, we assess the health of the boiler systems and, if needed, schedule replacements.”

The Blue Hill Commons building #3 mechanical room before J.A.M. conducted a retrofit.
After 30 years in service, the boiler in building #3 was showing its age. The nine-unit condo building was served by a single large boiler and an indirect tank. Fin tube radiation is installed with zone valves on each apartment, one zone per apartment.
“Tom Dwyer visited the job with me in September of 2020,” said Mezzasalma. “He sized and designed the new system. It was his idea to use two boilers instead of one, for efficiency and little redundancy.”
Dwyer’s plan was to install two, 140-MBH X-2 boilers, made by U.S. Boiler Company. Because the budget didn’t have room for condensing boilers, the new system could still have two stages of input by placing the cast iron Series X-2 boilers in a lead-lag-rotate configuration with an external staging control.
Work began in October and was finished in two weeks. Heat wasn’t needed at the time, and DHW was temporarily supplied with an electric water heater.
The hardest part of the job was getting the old boiler out and the new boilers in. The basement mechanical room can only be accessed through a tight stairwell. The existing chimney was used to vent both X-2 boilers, and J.A.M. installed a new indirect water heater.
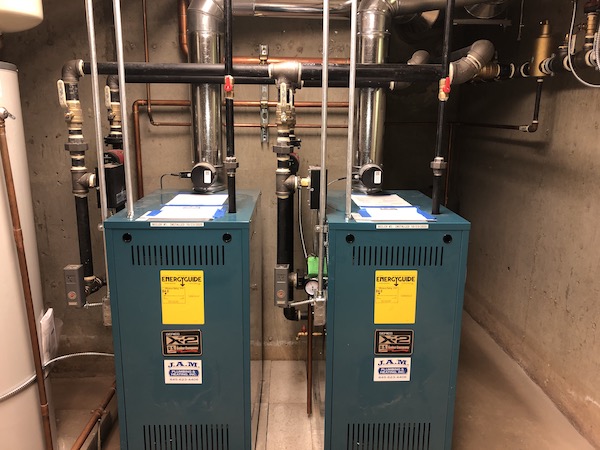
J.A.M. installed two X-2 cast iron boilers, made by U.S. Boiler Company.
“This was out first time I using the X-2, and I’ll use it again,” said Mezzasalma. “It’s everything a cast iron boiler should be; simple yet compact, with easy-to-access controls.” The Series X-2 is available in seven sizes from 70 to 280 MBH. Design of the American-made, cast iron heat exchanger promotes turbulent water flow for efficient heat transfer, providing an impressive 84 percent AFUE.
Because four buildings are tied to the same gas meter, there was no way to quantify gas savings. After one winter in service, and a winter in which many residents stayed home, no complaints came in.
“No news is good news,” said Mezzasalma. “You never get positive feedback, either, so silence is golden. I have to hand it to Tom on the design of this system. He didn’t want to want to replace one large boiler with another single boiler, and I know, whether the gas savings are immediately evident or not, we’ll be saving gas in Building #3.”
Educational work
Shortly before J.A.M started the Blue Hill Commons project, the company was busy with a larger project at St. Thomas Aquinus College (STAC), in Sparkill, NY. College expansion required a new dorm building.
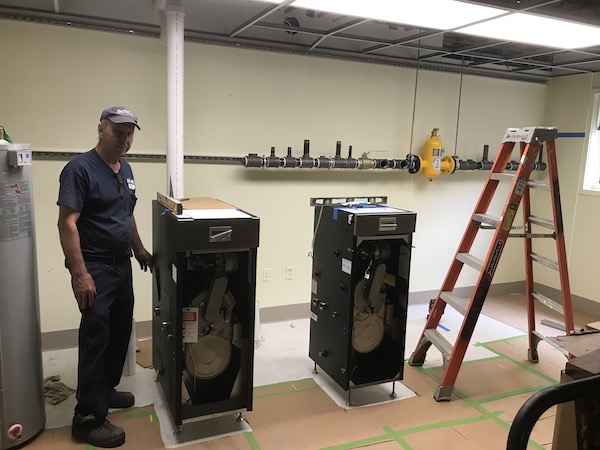
Master Plumber John Schauder assembling a boiler room at St. Thomas Aquinas College, including two large Alpine boilers, made by U.S. Boiler Company.
“We’re on the college’s preferred contractor list, so we got a call when they built the new 36-room dormitory,” said Mezzasalma. “The engineer actually asked us which condensing boiler we preferred to use, and he designed the system around that, U.S. Boiler Company’s Alpine mod-con.”
J.A.M.’s work on the dorm included all plumbing in addition to the hydronic system, which serves the building’s common areas and provides DHW. The two common areas each include a fan coil unit, and individual dorm rooms are heated and cooled with PTAC units.
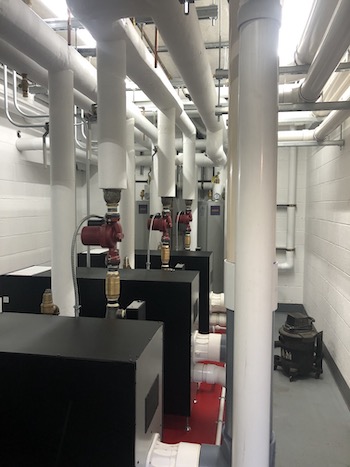
A boiler room with multiple Alpines that J.A.M. previously completed at St. Thomas Aquinas College.
Two, 210-MBH Alpines boilers were installed on the second floor, along with a 34-gallon instantaneous indirect tank.
“Weight was a consideration for everything in the mechanical room, due to its second story location,” explained Mezzasalma. “That’s one reason we installed the Alpine boilers and was also a consideration when the water heater was selected. The Alpine boilers each have a five-to-one firing ratio, so by pairing them, the system effectively has a 10-to-one turndown. The 410 MBH input provides ample capacity to heat the space and create 15 GPM of domestic hot water. After all, there are 36 bathrooms in the building.”
Other than weight, we chose the Alpine because we trust the unit,” he continued. “We’ve installed them in much larger multi-boiler systems before. The controls are great, it’s easy to service, and it’s very efficient.”
The project started in March of 2020 and culminated in August. COVID halted progress entirely at one point, and created scheduling conflicts throughout the project. Weather was an issue too. As luck would have it, heavy rain complicated the outdoor plumbing portion of the job.
Tom Dwyer conducted system start-up before the fall semester began. The building was ready, whether or not students would return, or learn from home.
Today, J.A.M. Plumbing & Heating, Inc. is currently installing two more Alpines at the college and rezoning the Romano Student Center. Stellar craftsmanship, paired with solid product and design support, wins and keeps big customers.