International Training Institute, Copper Development Association provide training
Detroit—The International Training Institute (ITI), the education arm of the unionized sheet metal and air conditioning industry, and the Copper Development Association (CDA) recently facilitated a soldering certification class for members of Sheet Metal Workers Local 80 in Detroit. The class, heavily requested by local contractors, certified 23 members (11 of which were local apprentices).
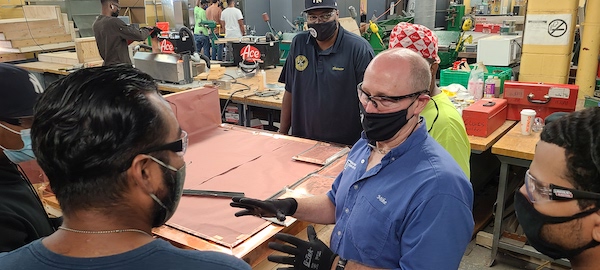
Contractors requested the class because the skill set is required for projects in the area, such as the restoration of the Michigan Central Station, the historic former national hub and passenger rail station in downtown Detroit. Built in 1914, the building was purchased by Ford Motor Company in 2018. C.A.S.S. Sheet Metal, one of seven Michigan contractors in attendance, is currently working on the project. Glenn Parvin, owner of the company, predicts 35,000 pounds of copper will be used to restore the building’s roof.
“The train station was the catalyst for making the soldering certification class happen,” Parvin said. “My involvement with the soldering process and getting a standard established started more than 15 years ago. So, this was a feel-good moment in time.”
The class was instructed by Larry Peters, CDA project manager of building construction, and ITI personnel, including Chris Caricato, field staff and architectural specialist; Mark Van Avery, field staff and welding specialist; and Mike Shields, full-time apprenticeship instructor from Sheet Metal Workers Local 12 in Pittsburgh. The goal was specific — train members to become certified solderers in the American Welding Society (AWS) B2.3: 2018 Specification for Soldering Procedure and Performance Qualification.
To prepare them for the soldering certification process, members received architectural training utilizing mockup structures to install a copper flatlock soldered seam roof system, which covered how to solder the seam in a field condition. The training also introduced members to the fabrication and installation techniques and the components within this type of roof system. Members then received extensive soldering training on how to solder a three-quarter-inch copper flatlock seam in the flat position requiring the solder to reach beyond the third seam leg as well as how to solder a 1-inch lap seam in the vertical position, requiring a 100% fully sweated joint.
The mockups give participants a real-world experience and allow them to accurately hone their skills. The class also offered a foundation of training that can be continuously built upon, depending on the project requirements. Training such as this not only gives the participants a new skillset, it allows contractors the opportunity to bid on this type of work where previously they could not, said Matt O’Rourke, training director for Local 80.
“Any time we can add a new little niche of training into our curriculum or into our area of expertise, it makes our members more marketable, improves their skills and gives them confidence,” he added. “We have the ability to come up with other processes if job specifications require it.”
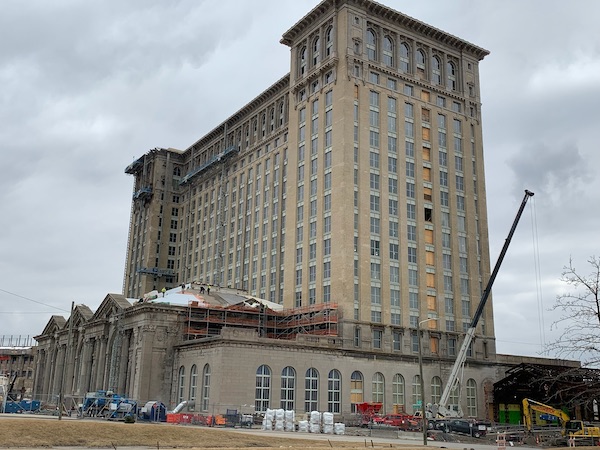
Architectural sheet metal workers will tell you one source of pride is to point out past projects on a city’s skyline and say, “I did that.” And projects like the train station could last generations, Peters said. When performed properly, soldered flatlock seam joints have been studied, tested and proven by a third-party engineering firm commissioned by the ITI to withstand in-service cyclical thermal loads that exceed the minimum requirements for the intended in-service lifecycle of 75 years without failure.
“It was great to work with the professionals from ITI and Local 80, and especially to engage apprentices as they strive to gain and demonstrate soldering proficiency,” Peters said. “I’m sure they all gained considerable confidence. They will take this knowledge into the field, experiencing satisfaction knowing their copperwork could very well last 100 years or more.”
Contractors in attendance included C.A.S.S. Sheet Metal, Liberty Sheet Metal, JD Candler Commercial Roofing Company, T.F. Beck Company, Detroit Cornice & Slate Co., ChristenDETROIT Roofing and Sheet Metal Contractors and LaDuke Roofing & Sheet Metal.