According to Forbes, the occupancy rate among US multi-family housing units rose to 96.9 percent in mid-2021, and the trend has continued post-pandemic.
With real-estate prices increasing sharply and rent costs reaching all-time highs, there’s more incentive than ever to renovate, update and repurpose commercial and light commercial facilities, whether properties include multi-tenant housing, mixed office space, retail locations, etc.
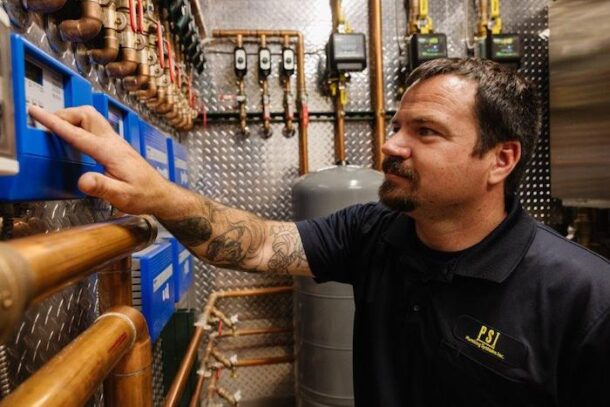
Brandon Content, at Plumbing Systems Inc., establishes a connection between several boilers and the tekmar control system that serves the large vacation home.
Compared to new construction, however, this leaves property owners, managers and mechanical contractors at a disadvantage: older but serviceable mechanical equipment can be difficult to integrate with a smart and connected control platform.
This may be especially true in northern climates, where hydronic systems have been the default source of space heat due to boiler efficiency, comfort, longevity and the ability to provide ample domestic hot water.
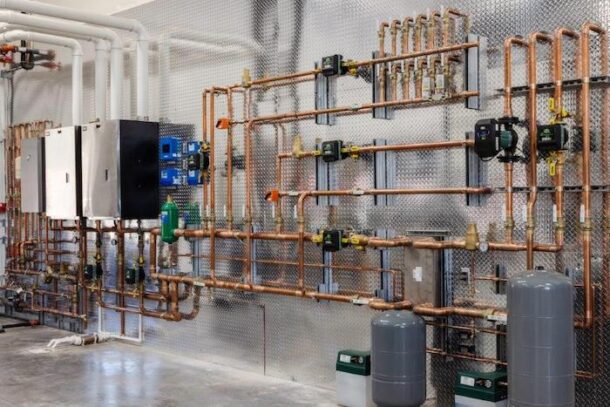
Staging and remotely monitoring boiler plants without a BAS installed has become easier than ever with next-generation control modules.
Older boiler plants generally lack connectivity in the 50,000-square-foot and under market, where installing a building automation system (BAS) may not be worth the expense.
James Dice, PE, CEM, CMVP, founder of Nexus Labs, recently wrote a white paper titled “The Untapped 87%: Simplifying Controls Technology for Small Buildings.” In it, the author explains that a 20,500 square foot building was retrofitted with a BAS by the United States Department of Energy’s Pacific Northwest Laboratory (PNNL) in 2010. Within the first two years, this lead to a 22% energy savings, 25% return on investment and a “dramatic decline” in occupant comfort complaints.
The white paper goes on to explain that buildings smaller than 50,000 square feet represent 94% of commercial buildings in the US, 44% of electricity use, and 44% of total energy use. Yet, only 13% of these buildings are equipped with a BAS.
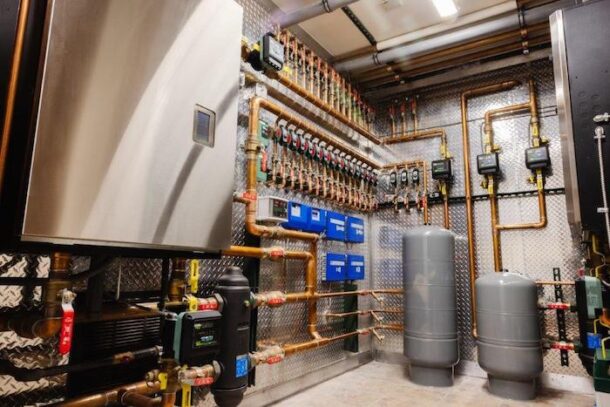
High-end vacation homes benefit from remote boiler system access, as well as most commercial systems.
The reason? BAS systems are either too complex or not cost effective enough for the average building owner. BAS frequently cost $50k to $100k, which exceeds the fiscal budgets of many building owners. In addition, they require an expensive annual service plan.
Because of this, there is massive opportunity to reduce energy consumption and simplify maintenance with the use of new, connected HVAC system controls without installing a BAS.
Aging boiler plants
Many commercial boiler plants feature multiple boilers for staged input or redundancy. Over the years, as various boilers were replaced, it’s not uncommon to have multiple different boiler models serving the same system.
For example, a system that was originally served by three conventional boilers of the same model might have been retrofitted with a single condensing boiler to replace two of the originals, while the third existing boiler remained in place for supplemental heat on design days.
In new construction applications or in systems where every boiler in the system is replaced, the boiler manufacturer’s onboard cascading controls are often used for lead-lag cycling of the units, though establishing remote access can still be a frustration.
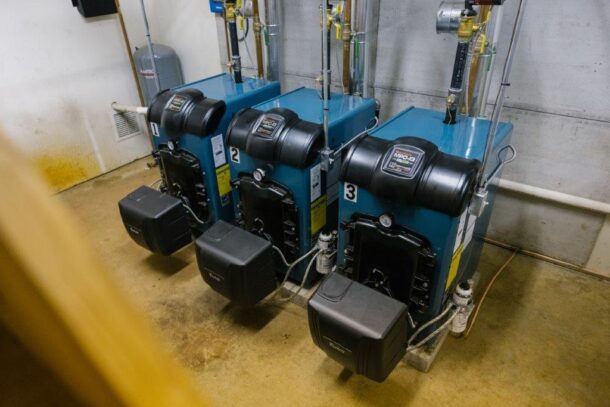
Three oil-fired boilers now serve a hydro-air system at a recreation building, using smart boiler controls to control all three units and provide remote access.
Fleet management is a major problem for facility managers. The heating system equipment is usually different in every building. This is due to the buildings being built and updated at different times, and buildings being acquired and sold by the management company.
So facility managers, property owners and mechanical contractors involved with light commercial systems too small to warrant the installation of a BAS are left asking how to control and remotely monitor their systems. If multiple properties are involved, the challenge is multiplied.
Evolving needs
“We’ve been building multi-stage boiler controls for over 30 years,” said Jay Vath, life cycle engineer at tekmar Control Systems. “There are a number of other control manufacturers with similar products, and for everyone in this market sector, the initial goal was to provide outdoor temperature reset for boilers that didn’t offer it.”
The demand for features in a boiler control package evolved along with the boilers themselves, along with the need for greater efficiency and control. Boiler manufacturers began offering outdoor reset and onboard staging across multiple, identical units. So the focus shifted to remote access, existing boiler plants, and the installation of hybrid condensing and non-condensing boilers plants.
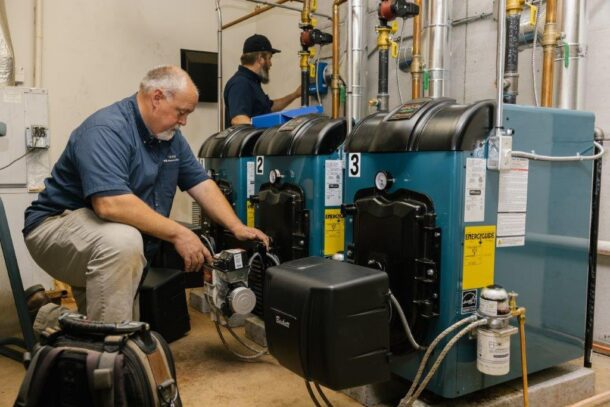
Firing a multi-boiler system
Control manufacturers introduced modules that offered some degree of remote monitoring capability for boiler plants, but one large issue remained: Many existing boiler plants included disparate models, often with decades separating them. There was no way to aggregate different brands and models onto a single, web-enabled control platform short of installing a BAS.
Long-sought solution
The primary drawbacks to installing a BAS solely for boiler plant control in a facility that otherwise doesn’t need it are the initial and maintenance cost, but equally important is the level of responsiveness on the part of the controls contractor. A BAS system creates an additional hurdle between the system and the service contractor. If an alert is generated by the boiler plant, the controls contractor – who may or may not be responsive in a reasonable amount of time – notifies the service contractor.
Eliminating the controls contractor and creating a direct conduit from the boiler plant to the service contractor reduces expense and expedites the service response.
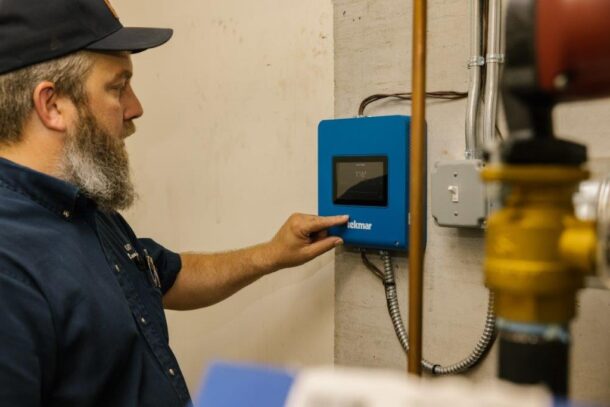
A service tech uses the boiler control to check system operation.
“This is a key consideration for any connected boiler control,” said Vath. “It puts power in the hands of the service contractor, while providing remote monitoring capability for systems that may feature a number of different boiler makes models.”
Tekmar’s Smart Boiler Control 294 is an internet connected control that can be accessed via any web-enabled device for remote boiler plant monitoring and control. A boiler wizard provides integration with thousands of boiler models, and various levels of control and permission can be set for specific individuals, such as the service contractor, a facility manager and the building owner.
Compound savings
“Installing a smart and connected boiler plant control system provides real potential to save money on energy and maintenance,” said Vath. “Compared to a fixed operating setpoint system, outdoor reset alone can save upwards of 30 percent in fuel expenses.”
But there are many other savings advantages, some not as easy to quantify. Automatic boiler and pump shutoff reduces energy use when the system isn’t needed. Short-cycling is reduced or eliminated. Rotating boilers balances runtime hours, providing maintenance and longevity advantages. Staging boilers correctly helps accurately match the heating input to the load. Conventional and condensing boilers in the same plant can be grouped together and staged independently, keeping the least efficient appliance offline until needed. Some savings though, take place outside the mechanical room.
“With the notifications and insight that web-enabled boiler controls provide, the service technician knows what’s needed in the event of an alert, which they receive via email, text or push notification,” said Vath. “For example, a pressure input could indicate that the expansion tank’s diaphragm is flooded, so the technician would know in advance to put a replacement in the truck. With remote monitoring, dispatching occurs quickly. Alternatively, if the control generates an alert on an issue that can wait until the next scheduled service interval, an unnecessary trip is eliminated. This kind of information reduces unnecessary expense and allows service professionals to be proactive. The Watts OnSite app provides notifications when boilers and pumps are due for servicing based on run time hours. This allows for the creation of scheduled maintenance plans.”
Using a flexible boiler plant control also offers cost saving options in the event of a retrofit. If the ability to connect an old boiler to a new control system is the only factor prohibiting a facility from leaving existing capacity online while retrofitting a portion of the mechanical system, that’s no longer a concern. New boilers can be paired with old boilers for backup heat, ultimately reducing the amount of new firing capacity needed.
Forward-backward compatibility
“For systems that already include tekmar boiler controls, updating the system with the 294 is simple,” said Vath. “All the equipment applications we’ve had in the past are covered by the 294.”
Similarly, the 294 can be quickly updated as new apps or other improvements are introduced. Updates and new features are sent to existing units as they’re developed. This is a big advantage for code compliance.
“In the future, if certain codes are accepted that require specific monitoring parameters, the 294 is designed to be updated to provide reporting as required.”
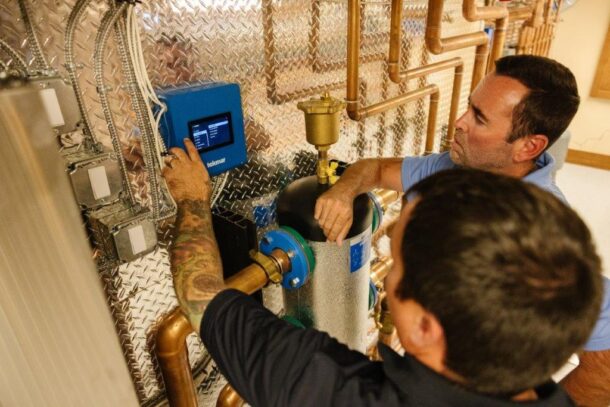
New hydronic system control packages are changing the way large residential and light commercial boiler plants are monitored and maintained.
This flexibility allows the owner to remain current, not just to become current now. It’s a matter of being proactive, not reactive.
For example, 30 U.S. municipalities across the US are currently phasing in higher standards for commercial real estate emission reductions and energy consumption. A long-known problem is that systems become less efficient over time due to poor maintenance. Remote monitoring is a key method to keep the boiler system operating at the designed efficiency.
Customized control
Web-enabled boiler controls offer a “BAS Lite” solution. With that comes substantial customization.
“The fact that dissimilar boiler technology is being controlled by a single system, tailored to the needs of an individual customer and property means that the control platform has to be extremely versatile,” said Vath. “For that reason, the 294 can be configured for many combinations.”
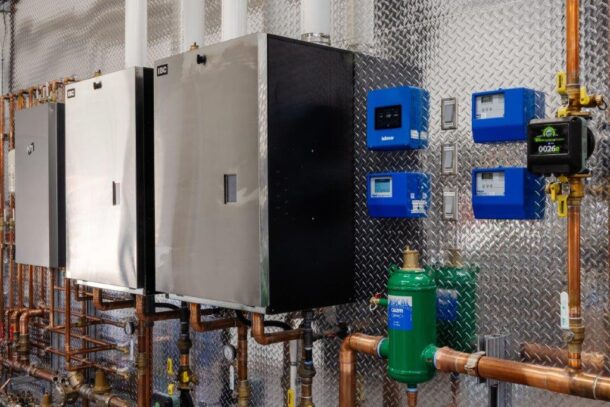
Staging and remotely monitoring boiler plants without a BAS installed has become easier than ever with next-generation control modules.
For example, a fixed “lead” boiler can be established, in the event that a draft is needed for one of the boilers in the system. A fixed “last” can also be established in the event that a conventional boiler is used only under design conditions, allowing condensing units to fire first.
Control can be established for firing rates or water temperatures, and the system can switch between the two depending on the call for heat. A DHW call may create a water temperature setpoint while a call for space heat may dictate boiler firing rate, and so on.
Security and ownership
Much of the remote access in buildings from the past 20 or 30 years was closed-loop, like key card room access, fire alarms, auto-dialers, etc. To provide full-featured remote access to a variety of team members, an internet connection is needed for a cloud-based platform.
“Fundamentally, where we’ve changed gears from what was done in the past is connectivity,” said Vath. “Once the 294 is connected via Wi-Fi or Ethernet, we use the Watts Onsite app or browser interface to remotely access the device with the ability to adjust every setting in the control. This has a great deal of value for property management groups that have a fleet of buildings, seeking control consistency across properties and boiler plants.”
Security is built into the control and into the Microsoft Azure platform that it operates on. Access is end-to-end encrypted, just like a banking app. Login information is specific to each individual on the team and does not need to be shared among members. The physical control also includes a passcode to prevent unauthorized access.
The program and information resident on the physical controller is a digital twin of the control on the remote device. The virtual device can be modified in real-time, immediately updating the physical device. This reduces trips to the property and allows every member of the team to access the system. Team members who have access to the digital twin can be added and removed, and different levels of access can be established for each.
The new control offers as many advantages to the owner as it does to the service professional. Ownership can be transferred in the event of property sale. Transfer of responsibility is quick and simple, if the service contract changes hands.
The property owner can also monitor and review the responsiveness of the contractor. An acknowledgement is logged when the service professional reviews the alarm. This allows the owner to see if they’re receiving the service they’re paying for.
Ultimate flexibility
Creating remote access for existing light commercial boiler plants requires a great deal of flexibility. Varying loads, miss-matched boiler models and different building codes to conform to all require a control package to be extremely flexible. Looking ahead, the potential addition of air-to-water heat pumps is something that a modern boiler plant control system has to be able to facilitate.
“The only constant is change,” said Vath. “Building owners change, technology changes, service contracts change, codes change. A modern boiler control package must adapt to these transitions.”
This piece was contributed by Eric Balt, technical sales manager for tekmar Control Systems and Mercedeh Fallahkhair, senior product manager for tekmar Control Systems
References:
Dice, J. “The Untapped 87%: Simplifying Controls Technology for Small Buildings”, Accessed June 2023
Cole, R. (2021, November 8). These are the Multifamily Trends Experts Are Predicting for 2022. Forbes.https://www.forbes.com/sites/reginacole/2021/11/08/multifamily-trends-in-2022/?sh=523a0e4b82bb Accessed June 2023
Sadovi, M. W. (2022, November 29). Five US cities target building energy use, emissions with fines. CFO Dive. https://www.cfodive.com/news/five-us-cities-target-building-energy-use-emissions-fines/637538/, Accessed June 2023