Bozeman, Montana is a city on the move, no doubt about it. As the nearest major passenger airport to Yellowstone National Park and the city nearest Big Sky Ski Resort, “Boz-Angeles” is currently growing at a rate of 3.2% annually. Its population has increased by 42.9% since the most recent census, which recorded a population of 53,293 in 2021.
Of course, housing demand is rising, so the addition of a five-story mixed-use residential building fit in well with the City of Bozeman’s vision for its future downtown and added much-needed housing stock. The Merin is a mid-rise building that features 31 living units above two ground level retail spaces, with 35 parking stalls. Encompassing over 71,000 sq. ft., it will also feature a courtyard, and private balconies for the residential units.
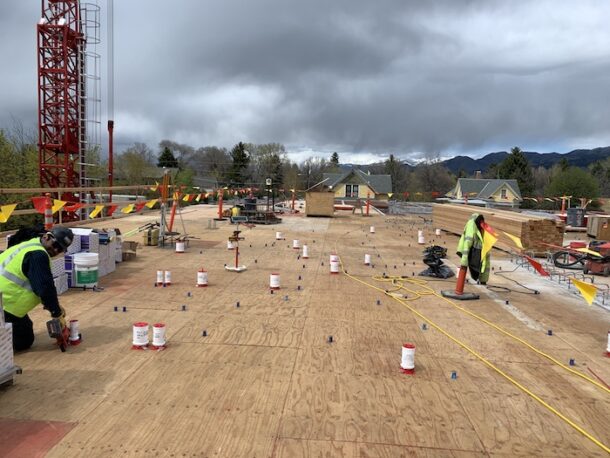
The ability to laser scan the building to get extremely accurate measurements on floor and wall penetrations allowed Harvey’s Plumbing to accurately model and then prefabricate and quickly install the plumbing using Allied BIM software.
DCI Engineers designed the primary framing systems for The Merin’s podium-style construction (post tensioned concrete slab design for the ground level and wood framed above-grade levels). The engineering team also designed the building’s cantilever sizes to maximize the efficiency of the concrete slab and provided maximum economy of the post-tensioned concrete system by coordinating regular column spacing for the ground floor layout.
Plumbing planning
The project ground broke in the fall 2019 and was off to a good start when ownership changes jostled the plumbing installation schedule. The project used Aquatherm polypropylene piping for the domestic cold-water mains, Uponor PEX in all the units, PVC for the drain and waste, and cast-iron risers on toilet stacks, with copper stub outs coming off the water heaters.
Harvey’s Plumbing, a Bozeman-based, full-service plumbing and mechanical contractor was tabbed for the project’s plumbing installation (Harvey’s was subsequently purchased by Bozeman-based Williams Plumbing and Heating). Harvey’s had recently completed three similar projects in the Bozeman area, so the project was straightforward, and there was an established process for the plumbing installation, resulting in less time spent modeling the plumbing system design. Still there were challenges.
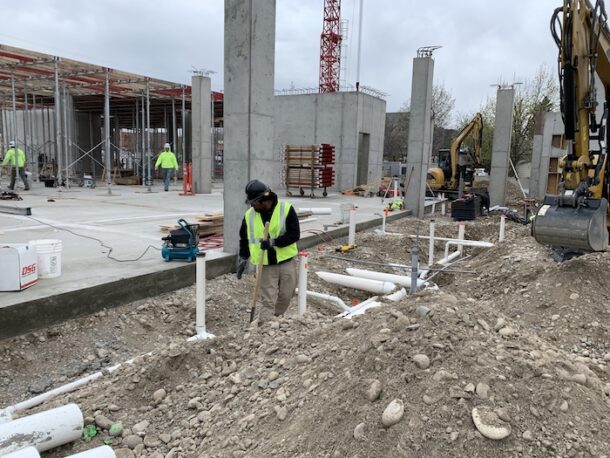
Harvey’s Plumbing saved an estimated 20% on the Merin job by prefabricating plumbing assemblies and spools in the shop using Allied BIM software and an automated laser positioning system.
According to Mitch Rausch, Director of Preconstruction for Williams Plumbing/Harvey’s Plumbing; “It’s a pretty typical downtown Bozeman multifamily condo unit and it worked out pretty well. The only real issue we ran into on that job were owner finish changes and material delays.”
By June of 2020 COVID had become a factor and while the pandemic didn’t necessarily slow the job down, it did cause a staffing issue for Harvey’s. “We definitely had to deal with lack of manpower just because it seemed like we always had one guy out for about a year.”
Harvey’s crew mix on the project included a superintendent, two then-recently tested plumbers, two apprentices, and two laborers. “We had a pretty young crew over there and that’s where that modeling really kind of benefited us,” he added.
Modeling efficiency – through software
The modeling of the plumbing system’s design was much quicker and more efficient on this project because Harvey’s was able to maximize its laser positioning system, a semi-automatic TigerStop saw, by connecting it to Allied BIM. Allied BIM is a new design-to-fabrication software program created by Bob Harvey, (previous owner of Harvey’s), and Brian Nickel (who had been Harvey’s Virtual Design & Construction Manager).
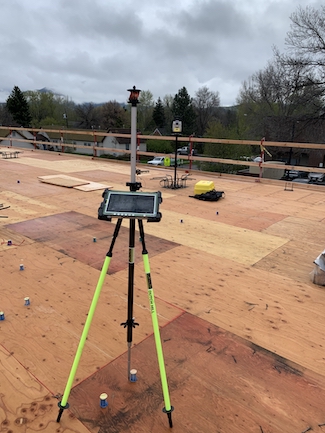
Allied BIM software and an automated laser positioning system help tremendously with building efficiency.
The duo cofounded Allied BIM in 2019 with the intent of improving the prefabrication process in the PHVAC, electrical, siding and framing, and modular building industries. “The machine shop is disconnected from the designers, and the field is disconnected from the shop, and we saw a way to build it better,” Nickel said of the venture.
While Harvey’s had been honing its modeling and prefabrication processes for years, for a shop its size, it was far head of the industry back in 2019. Traditionally, prefabrication shops get a designer’s drawings on a thumb drive or sheets of paper and a fabricator manually enters those instructions into a machine, which cuts the parts. A single error in that process can lead to expensive mistakes, such as ordering too many materials by as much as 40%, as well as huge material-waste-ratios.
Allied connects digital models directly to prefabrication machinery, eliminating errors and waste, while improving safety, trackability, and connectivity. According to Harvey, using traditional manual workflows, designers can send a fabrication shop about 10 drawings a day, but with Allied BIM’s automated data flow, they can send as many as 80 spools a day — an 800% productivity gain. Plus, the connectivity allows data to flow bidirectionally, allowing the fab shop to send the design team real-time updates and requests for additional instructions.
Software solves staffing shortage
Harvey’s had used Allied BIM on some of these previous similar condominium projects but connecting it to the TigerStop was what prompted a huge change in productivity. “At that time, we were still fully Harvey [not yet part of Williams], so we were a pretty small shop at the time, and in order to get the prefab done we would have to pull the plumbers off of the jobsite, bring them into the shop, and have them prefab it,” Rausch explained.
“We didn’t have dedicated fabricators. That’s about the time we started to add them. We had one part-time guy in the summer, he didn’t have a lot of experience, but he did some of it. And then if we’d pulled two key guys away from the jobsite, the general [contractor] would get upset even though we’re still making progress on the project. But it allowed us to do that pretty efficiently without losing too much presence on the jobsite.”
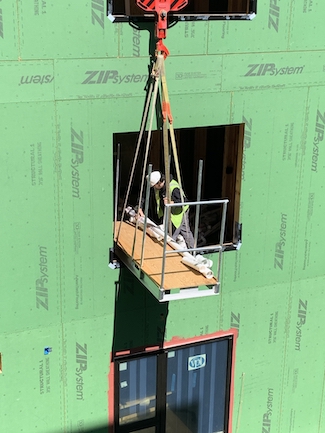
A load of PVC is lifted into place for unloading into a second-floor window at The Merin. According to Harvey’s Plumbing’s Mitch Rausch, the ability to get the right prefabricated assemblies to the right spot on the job provided a huge savings.
Improved safety was also a bonus. Using Allied BIM and the semi-automatic TigerStop allowed non-jobsite personnel to cut, prep and place the parts in bins so that they could be shipped to the jobsite where field installers could just plug them in. “It allowed us to really ‘lean up’ what we were doing and fit some stuff into our schedules that normally we wouldn’t be able to, and that the project schedule wouldn’t have really allowed us to do,” Rausch added.
Harvey’s Visual Design & Construction Engineer, Baylie Frost, performed all the modeling on The Merin project. “She was the only one working on modeling it, and she only had so much time, and she was also helping as project manager,” Rausch said. “So, if we were to tie her up making spool sheets, we would’ve had to add another BDC [building design construction] person to that project without Allied.”
Frost estimated that her spooling time on the project was reduced by 50% or more thanks to using Allied BIM, and labeling the spools was completed at least 10 times faster than the traditional method, while it also provided major organizational benefits.
Rausch also explained that using the Allied modeling and the TigerStop saw allowed them to limit wasted pipe sections to “just very, very small wafer pieces of pipe.” “I bet there’s at least 20 to 30% there in savings in PVC.” He added that an even larger savings came from fabricators not wasting time trying to salvage smaller pieces of pipe. “Traditionally, you’re going to have scraps and you’re going to have to pick up that scrap and try to cut up that scrap and use it. And that’s where you waste your time.”
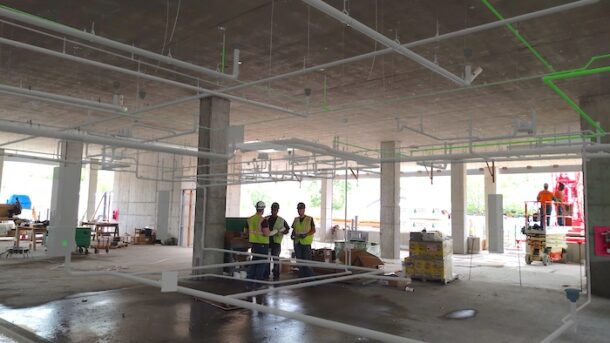
Allied BIM software, laser scanning, and a Microsoft HoloLens mixed reality headset allowed the Harvey’s team to be very exacting when it came to the design and installation of The Merin’s plumbing system, delivering a profitable project, and meeting a tight deadline.
With Allied BIM and an automated saw, the operator does not need to pull out a tape measure, hold it to the pipe, and mark it, he or she can just focus on the saw. Thus, they’re less likely to incur an accident. “It’s taking some of that ‘thinking’ and some of that extracurricular stuff you’d have to do away, so you can really focus on just cutting the pipe,” Rausch said.
Additionally, Harvey’s was able to streamline their bid on the job knowing that they would be achieving some time, labor, and material savings thanks to their model-to-design process. While there were several mitigating factors on The Merin project, Rausch said that when it comes to modeling and exporting a design, spooling it, prefabricating it offsite and installing on a jobsite, that 20% labor savings are extremely realistic.
Savings trips up and down the stairs
Rausch explained that Allied BIM also helped enormously with the organization of piping materials. “With this job, there are five flights of stairs in them. And you’ve got to go up and down the stairs every time you don’t have a part or piece you’re fitting. And if we can model it and fab it and get everything grouped together in a nice, clean kit and get everything into that room at one shot, just saving a couple trips up and down the stairs every day for 8 to 10 guys, makes or breaks a job.
So, it’s the efficiency you gain by that. Out of everything we do, if we could have everything sitting there for the plumber to install in that unit, it saves trips looking for parts, having the wrong part, having something messed up. That’s the difference between making money and not making money, 100%.”