Managing energy consumption and choosing the right energy supplier is a crucial task for businesses in the UK. As energy costs continue to rise, finding ways to unlock cost savings and reduce environmental impact has become more important than ever. In this article, we will explore the common challenges faced by UK businesses in this Read more
Whats New
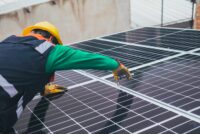
Managing energy consumption and choosing the right energy supplier is a crucial task for businesses in the UK. As energy costs continue to rise, finding ways to unlock cost savings and reduce environmental impact has become more important than ever. In this article, we will explore the common challenges faced by UK businesses in this area, provide insights into the various energy supplier options available, discuss key variables to consider when choosing a supplier, highlight the benefits of conducting an energy audit, and provide an overview of the energy regulatory landscape in the UK.
Click here to unlock more cost-saving information.
Challenges Faced by UK Businesses
-
Rising Energy Costs
UK businesses face the challenge of increasing energy costs, which can significantly impact their bottom line. According to recent statistics, UK energy prices have risen by over 40% in the last decade, putting businesses under financial pressure.
-
Complex Energy Market
The energy market in the UK is complex, with numerous suppliers offering different pricing structures and contract terms. Navigating through this complexity can be overwhelming for businesses, making it difficult to find the most cost-effective and suitable energy supplier.
-
Environmental Concerns
With growing environmental consciousness, businesses are under pressure to reduce their carbon footprint and opt for greener energy options. However, identifying suppliers that offer renewable energy solutions can be challenging without proper guidance.
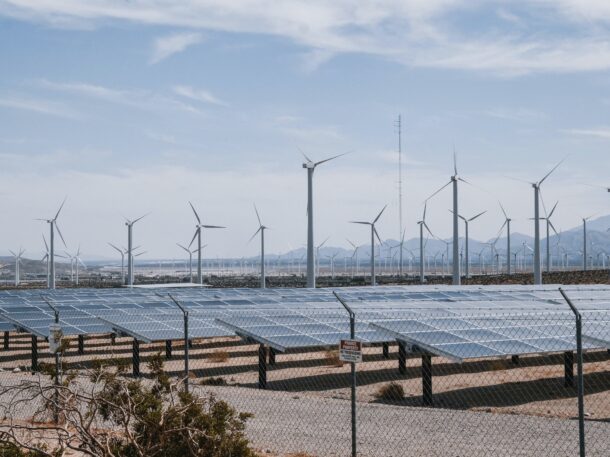
Key Variables to Consider
-
Rate Type
Businesses can choose between fixed-rate tariffs, which provide price stability for a specific period, or variable-rate tariffs, which fluctuate with market prices. Assessing the business’s budget and risk tolerance will help determine the most suitable rate type.
-
Contract Length
Suppliers offer various contract lengths, typically ranging from one to five years. Longer contracts may provide price stability but restrict flexibility. Shorter contracts offer more flexibility but may have variable pricing.
-
Green Energy Options
Businesses aiming to reduce their carbon footprint can opt for suppliers that offer renewable energy solutions. These suppliers generate electricity from renewable sources such as wind, solar, or hydro power, helping businesses contribute to a sustainable future.
Conducting an Energy Audit
-
Energy Assessment
Businesses can make accurate assessments of their energy needs and usage by conducting an energy audit. This involves analyzing historical energy consumption, identifying areas of inefficiency, and recommending energy-saving measures.
-
Benefits of Energy Audit
Energy audits help businesses identify cost-saving opportunities, reduce energy waste, and improve overall energy efficiency. By implementing energy-saving measures, businesses can lower their energy bills and reduce their environmental impact.
Energy Regulatory Landscape in the UK
-
Government Initiatives
The UK government has implemented various initiatives to promote energy efficiency and renewable energy adoption. These include the Climate Change Levy, the Renewable Heat Incentive, and the Smart Metering Programme, all aimed at reducing energy consumption and carbon emissions.
-
Regulations and Compliance
Businesses in the UK must comply with regulations such as the Energy Savings Opportunity Scheme (ESOS) and the Streamlined Energy and Carbon Reporting (SECR) framework. Compliance with these regulations not only helps businesses avoid penalties but also encourages them to adopt energy-saving practices.
Evaluating Supplier Reliability and Customer Service
When choosing a business energy supplier, it’s essential to evaluate their reliability and customer service. Consider the following factors:
-
Supplier Reputation
Research the supplier’s reputation by reading customer reviews, testimonials, and industry reports. Look for feedback regarding the supplier’s reliability in delivering consistent energy supply and their responsiveness to customer inquiries and concerns.
-
Customer Support
Assess the quality of customer support provided by the supplier. Are they easily reachable through multiple channels such as phone, email, or online chat? Do they have a dedicated account manager for business customers? Prompt and efficient customer support is crucial for resolving any issues or addressing billing queries.
-
Emergency Response
Inquire about the supplier’s emergency response procedures. How quickly can they address power outages or other energy-related emergencies? A reliable supplier should have robust contingency plans in place to minimize disruptions to your business operations.
-
Additional Services
Some energy suppliers offer additional services such as energy management tools, energy efficiency advice, or sustainability programs. These value-added services can further support your business’s energy optimization efforts.
Negotiating Contracts and Pricing
Negotiating contracts and pricing with energy suppliers is an essential step in securing favorable terms for your business. Consider the following strategies:
-
Multiple Quotes
Obtain quotes from multiple suppliers to compare pricing and contract terms. This will provide you with leverage during negotiations and ensure you are getting the best possible deal.
-
Contract Flexibility
Negotiate contract terms that align with your business’s needs. Consider factors such as contract length, exit clauses, and renewal options. Flexibility is crucial to adapt to changing market conditions or business requirements.
-
Price Review Mechanisms
Discuss price review mechanisms with the supplier. Some contracts include provisions for periodic price adjustments based on market fluctuations. Understanding these mechanisms can help you anticipate future pricing changes.
-
Contract Renewal Strategy
Develop a contract renewal strategy that allows you to review and renegotiate terms well in advance of the contract expiration. This ensures you have sufficient time to explore other options and negotiate better terms if needed.
Tracking and Monitoring Energy Usage
To optimize energy consumption and identify potential areas for improvement, businesses should establish effective energy tracking and monitoring systems:
-
Smart Metering
Install smart meters to track energy usage in real-time. Smart meters provide accurate data and allow you to monitor energy consumption patterns, identify peak usage periods, and make data-driven decisions to reduce wastage.
-
Energy Management Software
Consider utilizing energy management software or platforms that enable you to track and analyze energy data efficiently. These tools can provide insights, generate reports, and highlight areas where energy-saving measures can be implemented.
-
Employee Engagement
Involve employees in energy-saving initiatives by promoting awareness and providing training on energy-efficient practices. Encourage them to contribute ideas and suggestions for improving energy efficiency within the workplace.
-
Regular Monitoring and Benchmarking
Continuously monitor and benchmark your energy consumption against industry standards and best practices. Regularly review energy data and compare it with previous periods to identify trends, set targets, and track progress toward energy-saving goals.
Conclusion
Choosing the right business energy supplier in the UK involves evaluating supplier options, considering key variables, conducting energy audits, and staying informed about the regulatory landscape. Additionally, businesses should assess supplier reliability, negotiate contracts, track and monitor energy usage, and plan for the future. By adopting a comprehensive approach and making informed decisions, businesses can unlock cost savings, reduce environmental impact, and navigate the dynamic energy market with confidence.
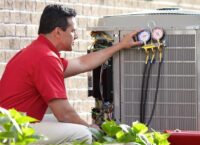
When it comes to maintaining a comfortable and energy-efficient home, proper HVAC (heating, ventilation, and air conditioning) maintenance is crucial. Painesville residents know how extreme weather conditions can affect their comfort, making it essential to keep their HVAC systems in top shape. Regular maintenance not only ensures optimal performance but also extends the lifespan of Read more
When it comes to maintaining a comfortable and energy-efficient home, proper HVAC (heating, ventilation, and air conditioning) maintenance is crucial. Painesville residents know how extreme weather conditions can affect their comfort, making it essential to keep their HVAC systems in top shape. Regular maintenance not only ensures optimal performance but also extends the lifespan of your HVAC system, saving you money in the long run. In this article, we will provide you with expert tips on HVAC maintenance from an expert provider of HVAC services in Painesville, OH.
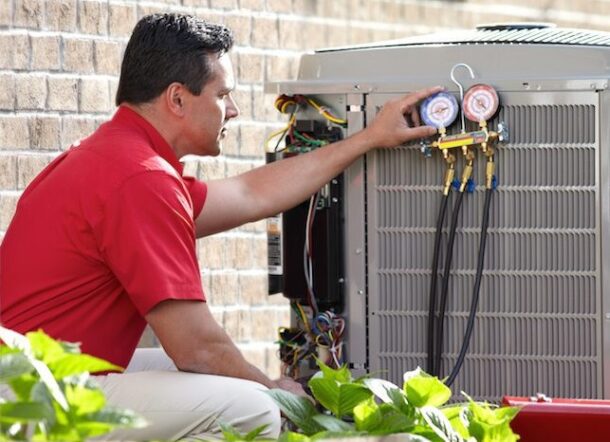
1. Change Your Air Filters Regularly:
One of the most important maintenance tasks for your HVAC system is changing the air filters. Dirty filters restrict airflow and reduce the efficiency of your system. Ideally, filters should be changed every one to three months, depending on the type and usage of your system. Regular filter changes will improve indoor air quality, prevent system breakdowns, and save energy.
Here are some tips to help you know if a filter needs changing:
- Check the Filter’s Appearance:
Inspect the filter visually to see if it appears dirty or clogged. Over time, filters accumulate dust, dirt, and debris, causing them to become discolored and less effective. If you notice a significant build-up on the filter, it’s a good indication that it needs to be replaced. - Assess Airflow:
A clogged or dirty filter restricts airflow, making your HVAC system work harder to distribute air throughout your home. If you notice reduced airflow from the vents or weaker air pressure, it may be due to a dirty filter. Check the filter and replace it if necessary to restore proper airflow. - Monitor Energy Bills:
An inefficient HVAC system can result in increased energy consumption and higher utility bills. If you notice a sudden spike in your energy bills without any other apparent reason, a dirty filter could be the culprit. By regularly replacing your air filters, you can help maintain the energy efficiency of your HVAC system and keep your bills under control. - Consider Household Factors:
Certain factors in your household can affect how quickly filters become dirty. If you have pets, live in an area with high pollen counts, or have multiple occupants in your home, the filters may accumulate debris more rapidly. In such cases, it’s recommended to replace the filters more frequently to ensure optimal performance.
Remember, the frequency of filter changes may vary depending on the type of filter and your specific circumstances. It’s advisable to refer to the manufacturer’s recommendations for guidance on the appropriate replacement interval. Regularly changing your air filters will improve indoor air quality, prevent system breakdowns, and promote the longevity of your HVAC system. By following these tips, you can stay on top of filter maintenance and ensure that your HVAC system operates at its best capacity.
2. Keep the Outdoor Unit Clean
The outdoor unit of your HVAC system can accumulate dirt, leaves, and debris over time. Regularly clean the area around the unit and remove any obstructions that may restrict airflow. Make sure to turn off the power before cleaning and avoid using a pressure washer, as it can damage delicate components.
3. Clean the Indoor Vents and Registers
Dust and debris can accumulate in the indoor vents and registers, affecting the air quality and overall performance of your HVAC system. Regularly vacuum the vents and registers to remove any build-up. You can also use a damp cloth to wipe away any stubborn dirt. Clean vents and registers allow for proper airflow and help maintain a comfortable indoor environment.
4. Schedule Professional HVAC Inspections
While there are many maintenance tasks you can perform yourself, it is crucial to schedule professional HVAC inspections at least once a year. Certified technicians can identify potential issues, clean and lubricate components, and ensure that your system is operating at peak efficiency. Regular inspections help catch problems early on, preventing costly repairs down the line.
5. Check and Calibrate Your Thermostat
A malfunctioning thermostat can lead to inconsistent temperatures and higher energy bills. Regularly check your thermostat’s batteries and replace them if necessary. Additionally, verify that your thermostat is calibrated correctly to ensure accurate temperature readings. If you notice any irregularities or have an outdated thermostat, consider upgrading to a programmable or smart thermostat for added convenience and energy savings.
6. Keep the Condensate Drain Line Clear
The condensate drain line removes moisture from your HVAC system. Over time, it can become clogged with debris, leading to water leaks and potential water damage. Check the drain line regularly and clear any blockages using a mixture of bleach and water. Ensuring proper drainage helps prevent issues with humidity levels and maintains the efficiency of your system.
7. Lubricate Moving Parts
HVAC systems have several moving parts that require lubrication to reduce friction and ensure smooth operation. Consult your system’s manual to identify which components require lubrication and use the appropriate lubricant. Regular lubrication extends the lifespan of these parts and prevents premature wear and tear.
8. Insulate and Seal Ductwork
Leaky ductwork can significantly reduce the efficiency of your HVAC system. Inspect your ductwork for leaks and seal them using foil tape or mastic sealant. Properly insulated ducts prevent air leaks and help maintain consistent temperatures throughout your home, reducing energy waste and improving comfort.
9. Keep the Outdoor Coil Clean
The outdoor coil, also known as the condenser coil, is responsible for releasing heat absorbed from the indoor air. Over time, it can accumulate dirt and debris, hindering its performance. Regularly clean the outdoor coil using a soft brush or a specialized coil cleaner. Ensure the power is turned off before cleaning and be gentle to avoid damaging the delicate fins.
10. Consider a Maintenance Agreement
To ensure consistent HVAC maintenance and avoid overlooking important tasks, consider signing up for a maintenance agreement with a reputable HVAC company. These agreements typically include regular inspections, priority service, discounts on repairs, and peace of mind knowing that your system is in expert hands.
Conclusion
Proper HVAC maintenance is vital for Painesville residents to stay cool and comfortable in their homes. By following these expert tips, you can optimize the performance of your HVAC system, improve indoor air quality, and extend its lifespan. While many tasks can be done by homeowners, it is essential to schedule professional inspections and maintenance to address complex issues and ensure optimal performance. Don’t wait until your system breaks down; invest in regular HVAC maintenance to save money in the long run and enjoy a comfortable home all year round.
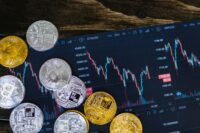
The impact and importance of technology in the 21st century are unrivaled. It is an industry that has grown rapidly over the years and influenced lifestyle, finance, education, medicine, innovation, and other industries in the world. Digital technologies are everywhere; you can see their influence in different areas such as streaming, social media, robotics, smartphones Read more
The impact and importance of technology in the 21st century are unrivaled. It is an industry that has grown rapidly over the years and influenced lifestyle, finance, education, medicine, innovation, and other industries in the world. Digital technologies are everywhere; you can see their influence in different areas such as streaming, social media, robotics, smartphones, digital television, and finance. Digital technologies have enhanced lives, strengthened economies, and made trade simple, easier and accessible.
The introduction of digital currencies has been at the center of this digital revolution. For a long time in human history, not so many people thought of the possibility of a global currency with uniform value everywhere. Interestingly, that’s what we have now, and from 2009 when the first coin was created, it’s been one level of advancement to another for the cryptocurrency market.
A cryptocurrency is a form of digital currency that can be bought, stored, and exchanged on platforms through a digital wallet. They are also called virtual currency as it is an electronic form of money; its access is restricted to digital phones and computers. Anyone can buy Litecoin crypto at Paybis or any other digital currency from their mobile device while on their beds. Buying, selling, saving, and other transactions can only be done online.
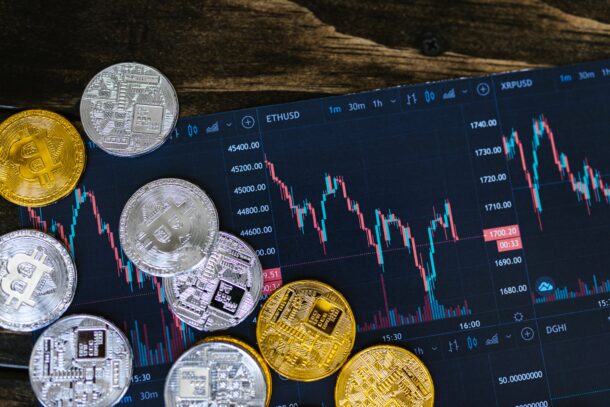
What Is Cryptocurrency?
A cryptocurrency is a digital form of money that uses cryptography to create and manage its currency, verify, and secure transactions in a network. Crypto spending is mostly an unregulated form of currency that can purchase goods and services and trade profits.
An important factor about crypto is its driving prices and the high volatility that accompanies these prices. Its value appreciates and depreciates quickly; it is volatile. Crypto uses blockchain, a decentralized technology, to manage and record transactions. There are over fifteen thousand cryptocurrencies in the market; the most popular, however, are Bitcoin and Ethereum.
Other currencies that have grown exponentially over the years include Dogecoin, Litecoin, USDT/Tether, to mention a few.
Impacts of Cryptocurrency on the World Economy
Cryptocurrency has helped improve the way people store, create, and transfer value. Some of the many ways cryptocurrency continues to impart the world include:
- Financial inclusion: the decision to invest in cryptocurrency is available to everyone and not limited or restricted to social class, gender, ethnicity, or race.
- Financial freedom: crypto allows users to trade money without the influence and extra cost of a brokerage like the traditional banks. Cryptocurrencies do not have any ties with juridical authorities such as the central banks that control the traditional banking system.
- It is an alternative to traditional means of money transactions. Because of its decentralized nature, users can easily transfer and receive money globally. Users can save money anywhere in the world without distance or banking-related restrictions.
- It is a career path for people with mathematical skills, which reduces unemployment. Trading and mining crypto is a career choice for people.
How Does Cryptocurrency Work?
To trade crypto like Bitcoin, Ethereum, or Litecoin, you need a digital wallet and an exchange account. Digital wallets are like online deposit boxes on an app that can store your crypto. You then create an account on an exchange platform app to transfer money to buy your cryptocurrencies. Popular trading exchange apps merge a wallet and an exchange account.
Benefits of Cryptocurrencies
- Cryptocurrencies are legit means of saving money. People perceive crypto as investment assets due to its ability to rise in value, although it generates no cash flow. To make a profit trading crypto, you have to sell it for a higher price than you bought from the cryptocurrency market.
- The cryptocurrency market is available to users round the clock since it is digital. Users do not have to visit physical banks to trade crypto and can be accessed through smartphones and computers.
- Cryptocurrency transactions are not regularized or conducted through central banks, which reduces transaction fees for money exchanged online.
- People can trade, travel and buy products using crypto.
- Cryptocurrency uses blockchain to process transactions that are more safe and secure than another payment system.
- Cryptocurrency is easily converted into cash. A user can buy Litecoin and convert it to cash without impacting the market price.
Future of Cryptocurrencies
The future of crypto largely depends on how people welcome it and use it. Crypto is not isolated; it has to be traded and used by humans. The reception of crypto as a digital currency is divided into two, the pro-crypto side, who welcome it and see it as a better alternative to traditional currency, and those against it who perceive it as difficult, unstable, and risky.
A major obstacle to the growth and expansion of crypto is government regulation and legalization. Crypto is projected to be the future. People are investing in it as its value increases.
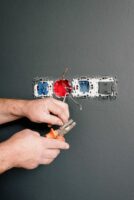
When it comes to electrical work in either residential or commercial settings, it is imperative to ensure that every aspect of the job is carried out with precision and safety as the top priorities. There are simply too many potential hazards and risks involved in working with electricity that must be approached with the utmost Read more
When it comes to electrical work in either residential or commercial settings, it is imperative to ensure that every aspect of the job is carried out with precision and safety as the top priorities. There are simply too many potential hazards and risks involved in working with electricity that must be approached with the utmost care and attention to detail. At the same time, it is essential to maximize efficiency and productivity to minimize the impact of any electrical work on daily activities or operations. Achieving the perfect balance between safety and efficiency in electrical work requires the highest standards of quality and expertise from both the electricians and the materials used in every project.
From understanding the importance of proper planning and communication to utilizing the latest tools and techniques available, every step of the process must be carefully considered and executed with skill and precision. Also, electrical installation should be done using only the highest quality components and materials that meet necessary safety requirements. This ensures that all wiring, fixtures, and other components are up to code and operate as expected for a long time.
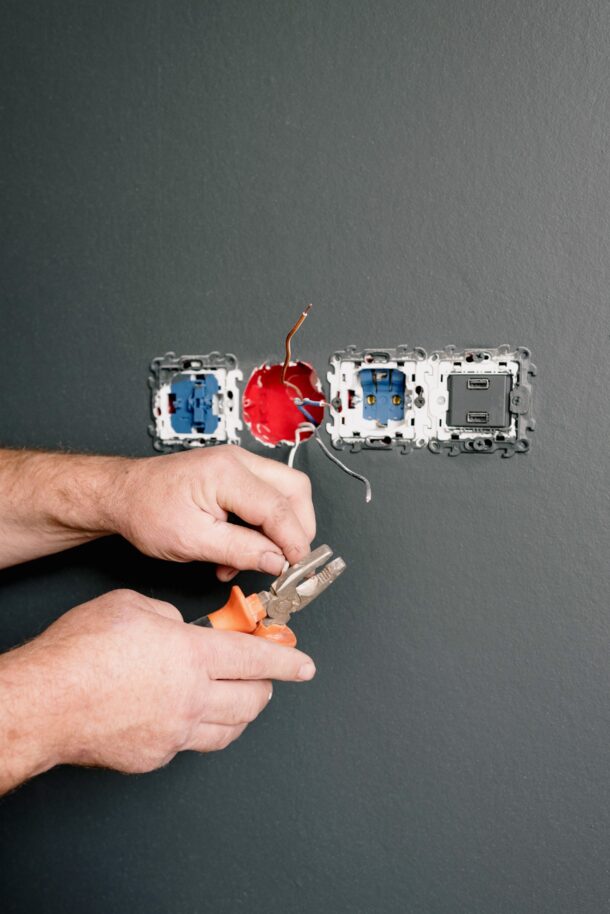
Understanding the Importance of Quality Materials and Workmanship
When it comes to electrical systems, using inferior materials or not following proper techniques can result in serious safety hazards and costly repairs down the line. Quality materials and workmanship can help ensure that electrical systems are installed and maintained correctly, reducing the likelihood of potential hazards like shocks, fires, and power outages. Additionally, using quality materials and workmanship can improve the overall efficiency and performance of electrical systems, reducing energy waste and potentially saving businesses money on utility costs over time.
Examining the Advantages of Engaging a Qualified Electrician
Engaging a qualified electrician has numerous advantages, including ensuring the safety and efficiency of your electrical system. Qualified electricians are well-trained and skilled to handle all electrical issues and can easily identify potential hazards that an untrained individual may overlook. They also understand and follow all safety procedures, codes, and regulations in place to ensure that electrical work is done safely and correctly. Furthermore, hiring a licensed electrician ensures that the work done is in compliance with electrical codes and regulations, giving you peace of mind and avoiding penalties or fines for non-compliance.
Taking Steps to Prevent Common Electrical Hazards
Shoddy wiring can cause a fire or electric shock, leading to serious injury or death. It is vital to have a qualified and licensed electrician assess and repair any faulty wiring, as well as regularly inspect all electrical systems to ensure that they meet strict safety standards. In addition to fixing faulty wiring, there are other steps that can help prevent electrical hazards, such as regularly checking and replacing damaged cords, avoiding the use of extension cords whenever possible, and ensuring that all electrical equipment is properly grounded.
Ensuring Electrical Systems Are Functioning Optimally
This requires the expertise of licensed, experienced electricians who have a thorough understanding of electrical codes and standards. Regular inspections and maintenance are necessary to identify and address potential issues before they become major problems. This includes checking circuits for overloading or shorts, inspecting wiring for damage or corrosion, and testing circuit breakers and other safety devices.
In Conclusion
Quality electrical work is crucial for maintaining safety and efficiency in any residential or commercial property. It’s important to hire licensed and experienced electricians who can provide reliable and secure electrical solutions. Professional electrical work can also help prevent costly repairs and downtime. By prioritizing quality electrical work, property owners can ensure the safety of their residents or employees while also maximizing their energy efficiency to lower energy costs.
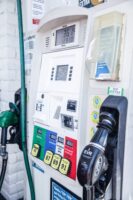
We’ve all been there, standing at the gas pump, watching the numbers tick higher and higher, and wondering how we can save on our gas bills. With the ever-changing oil prices and regional variations, it can be challenging to keep track of the best ways to cut down on fuel expenses. But don’t worry, we’ve Read more
We’ve all been there, standing at the gas pump, watching the numbers tick higher and higher, and wondering how we can save on our gas bills. With the ever-changing oil prices and regional variations, it can be challenging to keep track of the best ways to cut down on fuel expenses. But don’t worry, we’ve got you covered.
In this comprehensive guide, we’ll explain the factors that determine the cost of gas, how it varies seasonally and regionally, and discuss ways in which you can reduce your gas bills. We’ll break down the expenses step by step to show how small savings on every gas trip can add up over time. Read more here
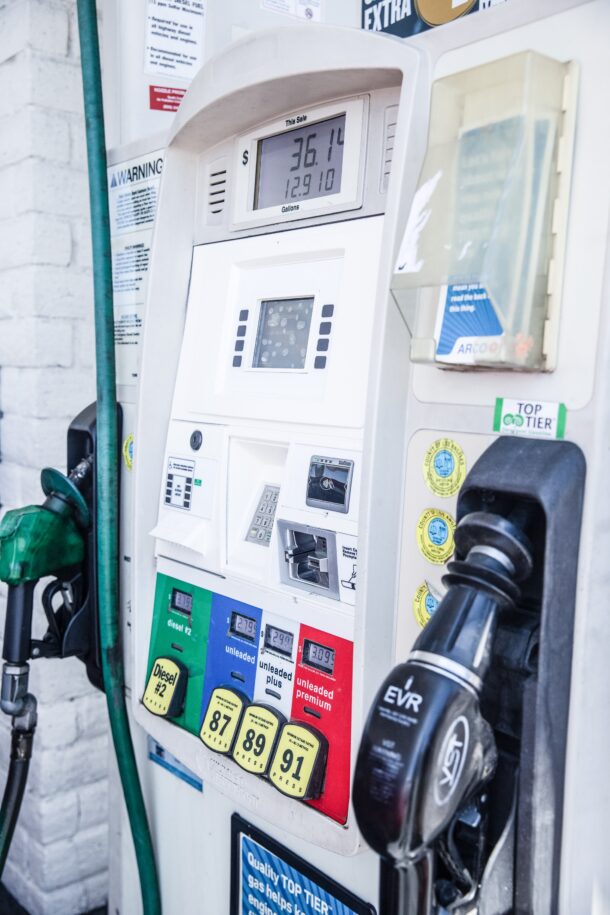
Factors That Determine the Cost of Gas
Before diving into the tips and tricks for saving on gas bills, it’s essential to understand the factors that influence gas prices:
1. Crude oil prices: The cost of crude oil is the primary factor affecting gas prices. Crude oil prices are determined by supply and demand, geopolitical events, and natural disasters, among other factors.
2. Refining costs: After being extracted, crude oil needs to be refined to make gasoline. The price of refining is affected by a number of variables, including the type of crude oil, local environmental laws, and refinery capacity.
3. Taxes: Federal, state, and local taxes can significantly impact the price of gasoline.
4. Distribution and marketing costs: These costs include transporting gasoline from refineries to gas stations, as well as marketing and advertising expenses.
5. Regional factors: Gas prices can vary based on the region due to differences in state taxes, transportation costs, and regional supply and demand.
6. Seasonal factors: Gasoline prices often fluctuate seasonally, with higher prices during the summer months due to increased demand and the use of more expensive summer-blend gasoline.
Tips for Reducing Your Gas Bills
In today’s world, there are tons of ways to save on gas bills. For every expense, there are always a number of ways to reduce them, and the same is true for gas bills. Here are some tips and tricks that can help you cut down on fuel expenses:
1. Regular Car Maintenance
One of the most effective ways to save on gas is by keeping your car well-maintained. A well-tuned engine, clean air filter, and properly inflated tires can improve your car’s fuel efficiency, resulting in lower gas consumption. As stated by the U.S. According to the Department of Energy, correcting a significant maintenance issue, like a broken oxygen sensor, can increase your mileage by as much as 40%.
2. Drive Efficiently
Adopting fuel-efficient driving habits can lead to significant savings on your gas bill. Some tips for efficient driving include:
- Accelerate gently and avoid sudden stops.
- Maintain a steady speed and use cruise control when possible.
- Avoid excessive idling, as it wastes fuel.
- Remove unnecessary weight from your car, as heavier vehicles consume more fuel.
- Use your car’s air conditioning sparingly, as it can increase fuel consumption.
3. Plan Your Trips
By combining errands and planning your trips efficiently, you can minimize the time spent driving and reduce your gas consumption. Try to avoid peak traffic hours, as stop-and-go traffic can be particularly fuel-inefficient.
4. Carpool
Carpooling with friends, family, or coworkers can significantly reduce your gas expenses. By sharing rides, you’ll not only cut down on your fuel consumption but also reduce wear and tear on your vehicle.
5. Choose Alternative Routes
Sometimes, taking a slightly longer route with fewer stops and less traffic can actually save you fuel and money. Consider using a GPS or navigation app to find the most fuel-efficient route for your trip. For example, Google Maps has a feature that will show you the best route based on fuel-efficiency. This can help you save time and money on your trips.
6. Consider an eco-friendly vehicle
Switching to a more fuel-efficient or eco-friendly vehicle, such as a hybrid or electric car, can lead to substantial savings on your gas bill. While the upfront cost of these vehicles may be higher, the long-term savings in fuel costs can make them a wise investment. In addition, many states and local governments offer tax credits or incentives for purchasing green transportation.
Breaking Down the Expenses: How Small Savings Add Up
To demonstrate the potential savings that can be made by following these tips, let’s break down the expenses step by step:
- Regular car maintenance: Let’s say your car gets 25 miles per gallon (MPG) and you drive 12,000 miles per year. If you improve your fuel efficiency by just 10% through regular maintenance, you could save approximately 48 gallons of gas annually. At an average gas price of $3 per gallon, that’s a yearly savings of $144.
- Driving efficiently: By adopting fuel-efficient driving habits, you could potentially increase your MPG by up to 15%. For our example car, this would result in an additional annual savings of around $216.
- Carpooling: If you carpool with one other person, you could effectively cut your gas expenses in half. In our example, this would translate to an annual savings of approximately $900.
- Choosing alternative routes: By taking more fuel-efficient routes, you could potentially save an additional 5% on your gas bill. This equates to an annual savings of around $72 for our example car.
By following these tips, you could potentially save over $1,300 per year on your gas bill. That’s money that could be put towards a vacation, a home improvement project, or even an eco-friendly vehicle.
In Conclusion
Saving on your gas bills doesn’t have to be complicated. By understanding the factors that influence gas prices and implementing fuel-saving strategies such as regular car maintenance, efficient driving, carpooling, and choosing alternative routes, you can keep your gas expenses in check.
Remember, every little bit counts when it comes to saving on gas bills, and the more proactive you are in addressing your fuel consumption, the more savings you’ll see over time. So, start implementing these tips today and watch your gas bill shrink before your eyes! With a clear and optimistic outlook, you’ll be well on your way to a more fuel-efficient and cost-effective life on the road.