While the Army Corps of Engineers has been busy constructing makeshift hospitals, temporary structures and retrofitting existing structures—such as McCormick Place in Chicago and New York’s Javits Center—in response to the COVID-19 crisis, modular construction has taken center stage. In fact, prefabrication and modular construction has been trending, and according to the Dodge Data & Read more
Featured Articles
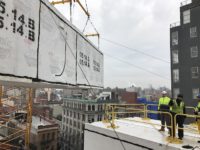
While the Army Corps of Engineers has been busy constructing makeshift hospitals, temporary structures and retrofitting existing structures—such as McCormick Place in Chicago and New York’s Javits Center—in response to the COVID-19 crisis, modular construction has taken center stage. In fact, prefabrication and modular construction has been trending, and according to the Dodge Data & Analytics SmartMarket Report “Prefabrication and Modular Construction 2020,” prefabrication and modular construction are poised to transform several sectors of the construction industry.
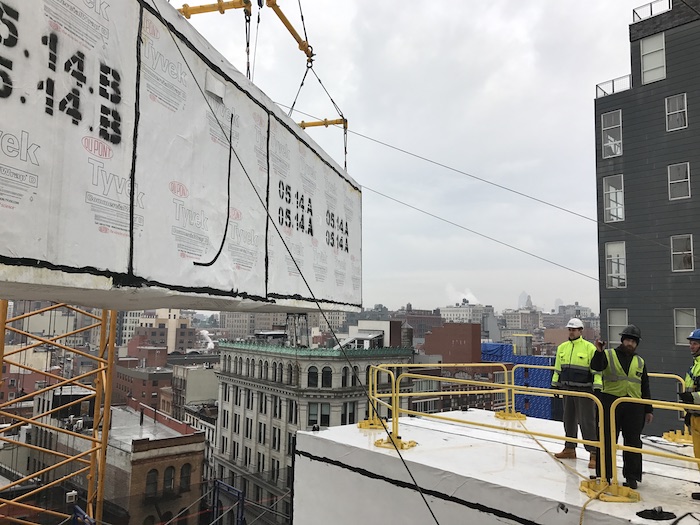
Members of GC The Rinaldi Group oversee the placement of modular boxes at the citizenM Bowery Hotel. Photo credits: citizenM, Chris Cooper, SBJ Group
The Dodge report shows that architects, engineers and contractors that have used these methods plan to significantly increase their engagement with them, especially for healthcare facilities, hotels and motels, multifamily projects, and college buildings and dormitories. Critical trends in the construction industry, such as shorter project schedules and workforce shortages, are several drivers of wider use of these methods, and technology—like building information modeling—is enabling increased use. Growth is seen among those doing modular construction in the use of full volumetric approach, in which entire parts of buildings—such as bathrooms or hotel and hospital rooms—are delivered preconstructed onsite and assembled together.
Looking towards the future of the building, modular construction stands out, and if you need an aluminum geodesic dome, this website offers innovative solutions that perfectly align with the principles of modular construction.
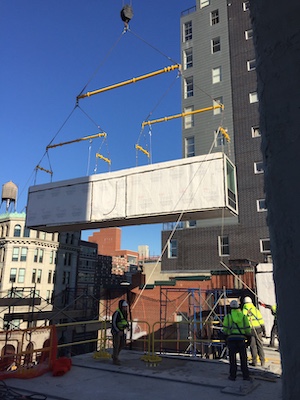
Photo credits: citizenM, Chris Cooper, SBJ Group
McKinsey and Company, a global management consulting firm, projects that modular construction could claim $130 billion of the market by 2030 in the United States and Europe at moderate penetration, delivering annual cost savings of $225 billion. Furthermore, modular construction could scale to an industry that represents more than $100 billion in U.S. and European real estate, delivering $20 billion in annual savings.
Originally designed as a conventional poured-in-place concrete building, citizenM decided to have the building redesigned using modular construction using imported steel boxes. Because of the change in structural system, the double height mechanical room, originally located on the 18th floor, was moved to the 3rd floor, and a three-foot-thick concrete “mat-in-the-sky” was poured on the fourth floor, on which the modules are stacked.
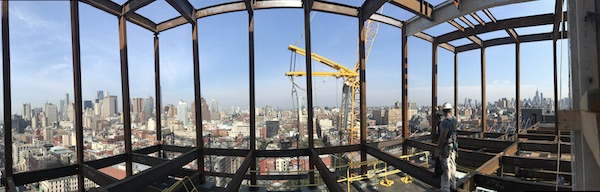
Photo credits: citizenM, Chris Cooper, SBJ Group
Although citizenM markets itself as offering affordable luxury, modular construction doesn’t necessarily contribute to affordability. “From what I hear,” says Isaac-Daniel Astrachan, a principal with Stephen B. Jacobs Group, “the cost of construction is not that much different between conventional and modular.” What chiefly makes citizenM affordable is its small unit size. The Bowery property fits in about a third more guest rooms than what a typical hotel with the same square footage would achieve.
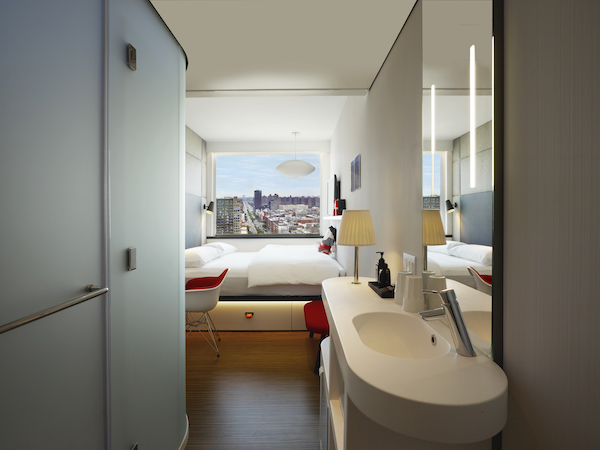
One of the finished box modules at the hotel. Photo credits: citizenM, Chris Cooper, SBJ Group
With construction costs coming in about even, schedule is often one of the main reasons to go modular. Units are under construction simultaneously with site work, which typically shaves weeks or months off construction. But for this project, a number of complicating factors meant that advantage did not pan out. For example, the decision to use a manufacturing facility in Poland—which had built the modules for the client’s hotels in Europe—added shipping and customs to the schedule.
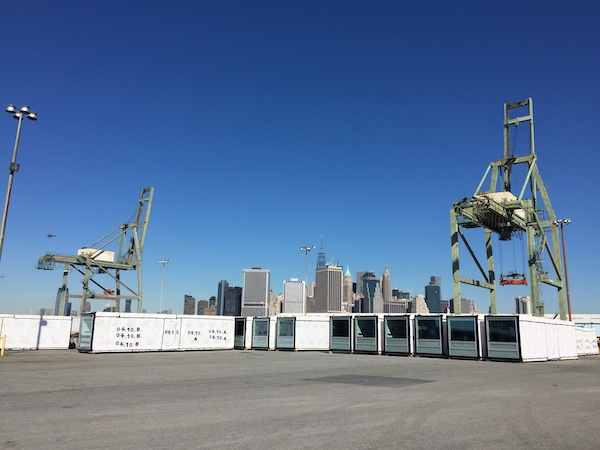
The steel boxes are ready to be fit into place at the hotel. Photo credits: citizenM, Chris Cooper, SBJ Group
Quality control may be the primary advantage of modular construction that this project was able to realize. With work being conducted out of the weather, at workbench height, and with assembly-line production methods, “modular construction takes the pressure off the back end of the construction schedule,” says Michael Schwartz, a senior associate at DeSimone Consulting Engineers, structural engineers for the project. “There was none of the usual check-listing—cracked tile, loose wallpaper—when the hotel was trying to open.”
“Modular construction is ideal in buildings where a high degree of repetition is implemented, such as hospitals and hotels,” says Stephen B. Jacobs, president and founder, Stephens B Jacobs Group, designer of New York’s citizenM Bowery Hotel, the tallest modular hotel in the world. The architect has five such projects in development, two in construction and three in the design phase. Jacobs sees a future in modular construction but “until we have enough critical mass and more reliable firms that can tackle challenges such as fire-proof boxes.”
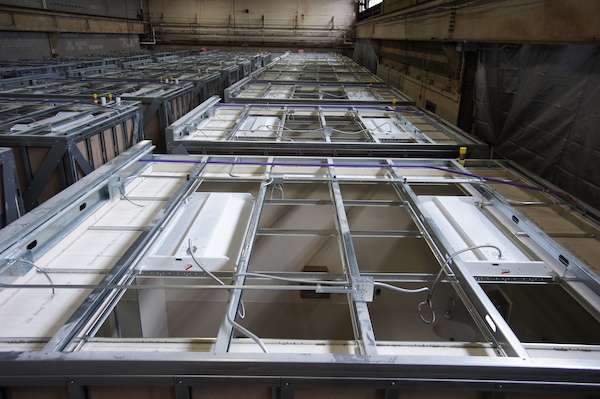
A look at the prefabbed healthcare modules from Hill Mechanical.
Hill Mechanical, located just outside Chicago has dabbled in modular construction for nearly a decade. “We have seen an increase growth in the modular industry over the last eight years. Healthcare has been one of the largest contributors to this increase along with the data centers. As more owners understand the benefits, more of the industry is looking for modular opportunities on each project,” says Kari Holtz, project manager, Hill Mechanical.
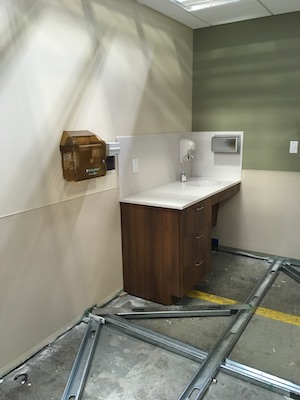
One of the 53 prefabricated medical waiting rooms undergoes a transformation from Hill Mechanical.
When evaluating a modular project, Hill Mechanical is looking at what items have the potential to benefit the schedule. Typically, the prefabricated units are being built while site work and MEP overhead is being installed. “When creating a schedule this means a portion of the finishes will be done significantly earlier that what a traditional build method would see. The time savings that comes from being able to move up the finishes results in the owners being able to open their building earlier which results in the overall costs savings,” says Holtz. Relying on its prefabrication shop in Franklin Park, Ill., one such prefab project is Hill Mechanical’s work on Chicago’s Advocate-Aurora Health facility, which included 53 prefabricated exam rooms.
Other benefits Hill Mechanical has found in utilizing modular construction for a jobsite include;
- Higher Quality Materials are used in some cases to withstand the shipment.
- Increase in safety
- Early involvement with AHJ (Authority having Jurisdiction)
- Dust Mitigation
- On-site congestion reduction (Primarily for existing buildings)
- Productivity from crews and smaller crews required
- Reduction of waste
- Early design and acceptance in the manufacturing plant reduces the on-site punchlist and change orders.
With this “new normal” as a result of the coronavirus, perhaps modular building will become more popular in theory and application. Workers are able to work in controlled environments instead of busy, more populated jobsites, bringing the jobsite in-house. With time savings and potential cost savings, it’s worth a look.
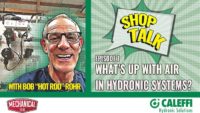
The first episode features Caleffi’s training and education manager, Bob Hot Rod Rohr, as he discusses how to effectively remove air from a boiler system. https://youtu.be/u3ZLZXltGMc Read more
The first episode features Caleffi’s training and education manager, Bob Hot Rod Rohr, as he discusses how to effectively remove air from a boiler system.
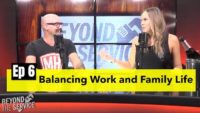
John & Devynn discuss the tight rope act of balancing your work and family like, which can be difficult at times. https://youtu.be/BX0GSPm70rs Read more
John & Devynn discuss the tight rope act of balancing your work and family like, which can be difficult at times.
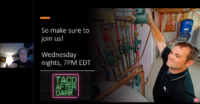
Online learning brings us together. Join Taco’s John Barba on Wednesday nights at 7:00pm EDT for fun, fast-paced training sessions. He’s broken down Taco’s full-day residential hydronics training class and will be delivering it to you one hour at a time, every Wednesday night. Topics include basic heat loss, boiler selection/pipe sizing, sizing & selecting Read more
Online learning brings us together.
Join Taco’s John Barba on Wednesday nights at 7:00pm EDT for fun, fast-paced training sessions. He’s broken down Taco’s full-day residential hydronics training class and will be delivering it to you one hour at a time, every Wednesday night. Topics include basic heat loss, boiler selection/pipe sizing, sizing & selecting circulators, DHW recirculation, and much more.
Join us on Wednesday, April 1 @ 7:00pm to learn about Basic Heat Loss. Click to register https://bit.ly/39o611c
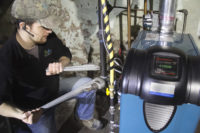
I will always preach that a successful cast iron water boiler installation begins with proper planning. I worked for an oil company for 20 long years, and nine years of that I was a service manager. During this time, I came across many problematic jobsites. I would evaluate the installation issues and try to figure Read more
I will always preach that a successful cast iron water boiler installation begins with proper planning. I worked for an oil company for 20 long years, and nine years of that I was a service manager. During this time, I came across many problematic jobsites. I would evaluate the installation issues and try to figure out where the problems had started. This knowledge has greatly helped me as a Training Manager for U.S. Boiler Company. Now, after 40 years in the heating business, I know how important proper boiler installation planning really is for reducing the number of problem jobs and expensive callbacks. In fact, planning is much easier than you may think …
- Proper boiler sizing. Complete a thorough heat loss calculation. Do not fall into the trap of oversizing the boiler because you sized it based on the old boiler size or you measured the connected radiation load, and never allow the customer to talk you into a larger boiler than needed. Today, with physically smaller boilers and less water volume, oversized boilers will short cycle more than ever. Increased short cycling means higher maintenance, higher fuel costs, and higher installation costs.
- Follow the boiler Installation & Operation (I&O) Manual. Be sure to follow one of the suggested near boiler piping options listed in the manual. The boiler tapping may not have to be the same size as the manifold piping. Use the flow charts for pipe size. You can pipe the boiler the same size as the tapping, or in some cases, use smaller piping dependent on the heat loss requirement. When the heat loss is known and the proper boiler size is chosen, you may be able to use smaller air separators, expansion tanks, and piping. You can use the following as a guide to size the boiler and system piping:
- 3/4” pipe = 40,000 BTU’s @ 4 – 5 GPM (gallons per minute)
- 1” pipe = 70,000 BTU’s @ 7 – 8 GPM
- 1-1/4” pipe = 160,000 BTU’s @ 16 – 18 GPM
- Bypass piping. Bypass piping is discussed briefly in the I&O manual. We cannot continue to install modern cast iron boilers the same way we used to install boilers with larger water volumes. When needed, a bypass system should be installed to protect the boiler. There are primary/secondary piping and circulated bypass options, both of which we will discuss later in this article.
The bypass system discussed in the manual is called a “boiler bypass” and is always installed the same size as the supply and return headers. When adjusted, the water flow through the boiler is slowed so the water spends more time in the boiler. This allows the boiler temperature to increase faster and decreases the possibility of boiler condensation. This means that some of the system return water is bypassed around the boiler and enters the supply beyond the boiler. I know what you are about to say. “Well, that will cool off the supply water going to the homes heating system!” That is correct, but it is not a problem. This is what I call a “poor man’s outdoor reset.”
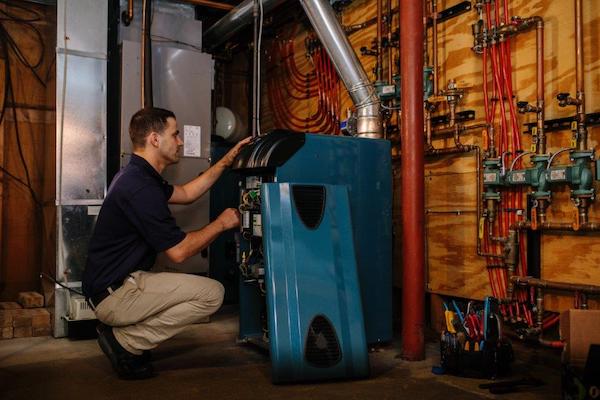
The system will run quieter and the system water temperature will increase slowly until the radiation outputs enough heat to satisfy the thermostat. The colder it gets outside, the hotter the system supply water temperature will be. When the valve placement is installed as shown in the manual, we can easily adjust the ΔT through the boiler. Simply put, leave the bypass valve open and adjust the flow through the boiler with either valve located on supply or return pipes below the bypass pipe to slow the flow and force more water through the bypass. Partially close one of these valves and check the ΔT through the boiler. You will need a minimum of a 20°F rise. If this is a large water volume system, like cast iron radiation, increase the ΔT through the boiler to 35 – 40°F ΔT.
Quick Tip: If the bypass is hotter than the return pipe, the flow is backwards and you have piped a system bypass as opposed to a boiler bypass. Follow the piping in the manual to verify correct installation.
- Primary/secondary piping option. Primary/secondary piping utilizes hydraulic separation so that the water flow from system pumps do not affect boiler pump flow. This allows us to reduce the flow through the boiler to heat the water faster and heat the water to a higher temperature without affecting the flow in the system. In other words, we can have a higher flow in the system and a lower flow in the boiler. We still want a minimum of 20°F rise through the boiler, and for higher water volume systems we want a higher ΔT near 35°F – 40°F.
- Variable speed bypass pump option. To have the best boiler protection, install a variable speed bypass pump with a temperature sensor. This will change the speed of the pump to obtain the proper return water temperature. We offer a variable speed bypass kit with instructions for gas water boilers. This will protect the boiler in a high-water volume system or radiant in-floor radiation application.
Quick Note: My concern, and the reason for the above discussion of boiler protection from condensation, is excessive water flow through the boiler and slower temperature increase. I have experienced multiple boiler installations where the ΔT through the boiler is less than 20°F. In fact, I have witnessed some as low as 8°F. Lower ΔT’s are a result of excessive flow, possibly caused by the number or circulator sizes installed on the system. So, what is the minimum flow rate on cast iron water boilers? Look in the I&O manual under specifications and find the DOE heating capacity (MBH) of the boiler. For instance, the Series 3 model 304B has an input of 105k MBH and a DOE heating capacity of 88k MBH. Divide the DOE output by 10,000 to discover the maximum flow required by the boiler. If your flow exceeds that number, the ΔT will be less than 20°F. You can use this hydraulic formula to determine flow rate through the boiler.
- Avoid short cycling. Short cycling is caused by lower water flow, or higher ΔT. Higher ΔT may mean that the circulator is to small, the boiler is oversized, or the valves not adjusted properly. Generally, the minimum boiler flow should be half (but not limited to) of the maximum boiler flow.
Boiler Flow Formula:
Q/(500*ΔT) = Flow
Q = DOE Heating Capacity
Let’s put some numbers to that formula. Let’s assume that a boiler has a ΔT of 15°F. The Series 3 model 304 (referenced above) has a DOE heating capacity of 88,000.
88,000/10,000 = 8 GPM. This is the maximum flow required by the boiler. Divide this in half to get the minimum boiler flow. In this case, it would be 4 GPM.
Now, back to the formula.
Q=88,000
ΔT = 15°F
88,000/(500 * 15) = Flow
88,000/7500 = 11.7 GPM
The flow is almost 4 GPM higher than the maximum flow the boiler should have. This tells us we need to achieve a 20°F ΔT, which means less flow through the boiler. Why do we have to much flow? There are oversized pumps or to many pumps. Using a bypass or primary/secondary strategy above, we can easily correct the flow through the boiler.
- Vent the boiler properly. If the boiler is chimney vented, the local and federal codes apply. A chimney liner may be required. If the unit is direct or power vented, the manufacturer dictates the venting according to the certifications obtained during testing. Since this article applies to cast iron water boilers, a sidewall vented boiler requires AL29-4C vent pipe. No plastic!
- Outdoor air. I like to use outdoor air as much as possible to verify enough combustion air. Plus, there is less chance of contaminated air.
- Gas pressure. Check the incoming gas pressure and the manifold (outlet) pressure with other gas appliances running. Check all safeties. Finally, always complete a combustion check.
Ron Beck is Outside Technical Advisor and Manager of Training for U.S. Boiler Company, where he’s been since 1998. Ron’s 34 years of experience in the heating industry include climbing the ranks of a HVAC company, from apprentice to service manager. Currently, he’s the go-to solution guy for contractors in the field.
Ron can be reached at RBeck@usboiler.net