It was an unseasonably warm day for Attendorn, Germany, in mid-March, standing in the exact spot where we had stood two years prior looking over undeveloped land and listening to the vision of what was to be. Fast forward two years last week and we were looking at Aquatherm’s new 160,000-sq.-ft. production facility, which features its extrusion processes for piping.
Earlier in the day, Dirk Rosenberg, one of the three co-directors for Aquatherm, said “We want to create our future independent of outside influences.” I think it’s safe to say that the facility affords them the opportunity to do just this. With revenues nearly tripling over the past decade and a half, “You can feel the energy in the company,” said Dirk.
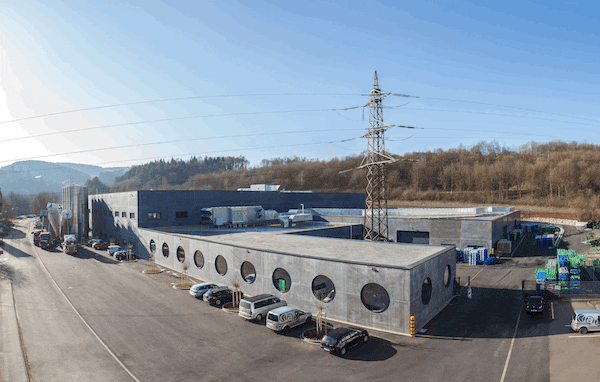
The new 160,000-sq.ft. manufacturing facility in Attendorn, Germany will accommodate for potentially 60% more company growth.
Aquatherm, a leading manufacturer of polypropylene (PP-R) piping, is headed by co-directors, the brothers Rosenberg: Dirk, Maik and Christoph. It was their hard work and execution that made the new plant a reality in a relatively short period of time. Our tour guide, Maik Rosenberg, boasted that the ideas implemented in the design of the building were “95% me and 5% the architect.”
There are some pretty innovative things happening inside the facility to practicing what they preach in using their own piping, to heat recovery, to metal panels that extend from the ceiling to reduce temperatures in different zones, to smart LED lighting, which can actually mimic outdoor daylight activity so employees can get acclimated to the surroundings better.
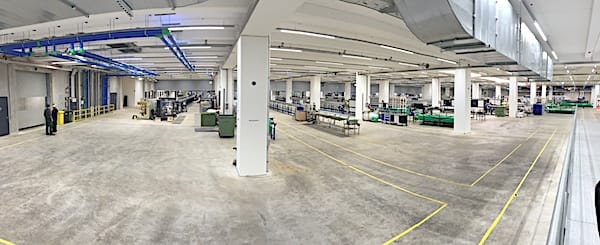
This panoramic, sneak-peek view of the extrusion facility is the extent of how close we could get to take pics.
There was room to expand in its current manufacturing configuration, and to potentially increase production by 20%, but the new facility gives Aquatherm the ability to increase production by 60% by 2022, and the ability to create 620 kinds of pipe on 19 lines—with the possibility of 28-29 lines by 2025.
With a goal of delivering product within 10 days, the production process needs to be continuous. The act of stopping and starting lines is a long, wasteful process. With three shifts running seven days a week, the only time the lines stop are for holidays and scheduled maintenance. (They were running 346 days last year, for example.) Because of this, it took 10 months to move from the old fabrication facility to the new one.
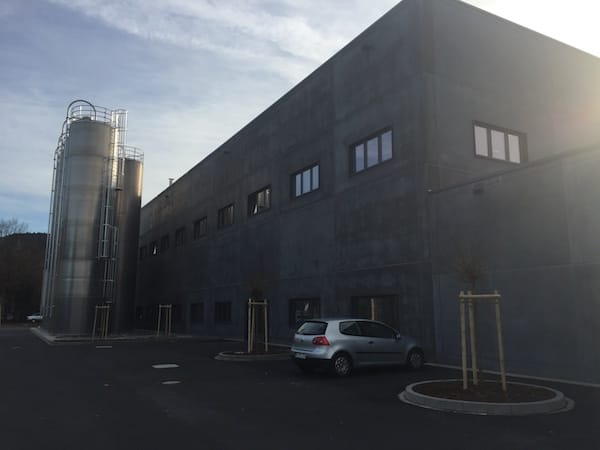
The raw materials—polypropylene resin pellets—are stored in these silos located to the left, back. Approximately 40,330 tons of raw materials came through the plants last year with approximately 900 trucks making the drop-off.
The first floor houses all of the extrusion processes and piping production. The basement features all of the process cooling, the heart of the fire protection system—featuring 2,080 sprinkler heads throughout the building—compressed air, a recycling station where material not approved through testing is sent back. There is also a room that houses a boiler back-up system, which is served by three Vaillant boilers for space heating and DHW. This is only really used during maintenance periods. The third floor features vacuum systems to extract the raw resin pellets and organize them accordingly.
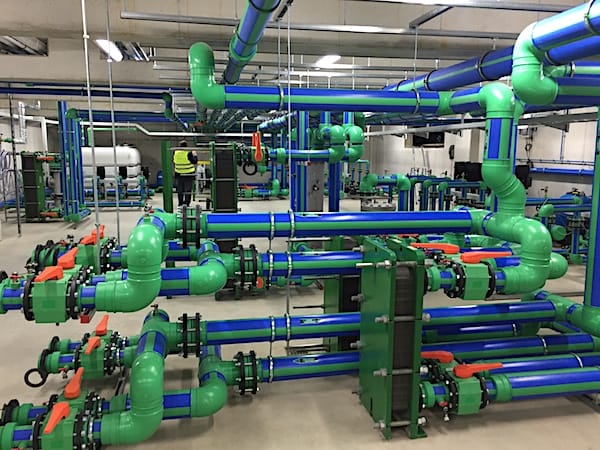
As artistic and aesthetic as functional, the Aquatherm Blue piping carried water to cool the production facility and return through heat exchangers to heat DHW and space. heating.
Part of the process cooling involves water and stable temps underground and from the nearby Bigge River. Water is then returned to the river—121,519,144 gallons per year, to be exact—at a temperature no more than 23 C or 73.4 F. Water is run through three loops, which run through heat exchangers for process cooling and heating and DHW heat recovery.
Aquatherm designed a way to get the water to the plant and the original design called for a L-shape off of the process cooling mechanical room. An additional room would have cost the company upwards of an additional $1M. The ingenuity of Maik Rosenberg and his team created a 90-meter/295-ft. tunnel to accommodate additional piping.
** In 2016, Aquatherm Worldwide assumed control of Aquatherm North America and is moving to a new, larger North American headquarters, located in Lindon, Utah.
Join the conversation: