In the endless quest for efficiency and innovation, an engineering marvel emerges from the shadows, capturing the attention of industries worldwide: air bearings. But what is this cutting-edge solution, and why is it revolutionizing motion control? Let’s embark on a journey to uncover the secrets of air bearings, a technology that promises to reshape the landscape of mechanical systems.
What are Air Bearings
Air bearings, often referred to as fluid film bearings or aerostatic bearings, operate on a principle that’s both simple and profound. They utilize a thin film of compressed air to create a virtually frictionless surface between two objects. Unlike traditional bearings that rely on physical contact and often suffer from wear and tear, air bearings provide a contact-free motion, delivering unparalleled precision and smoothness.
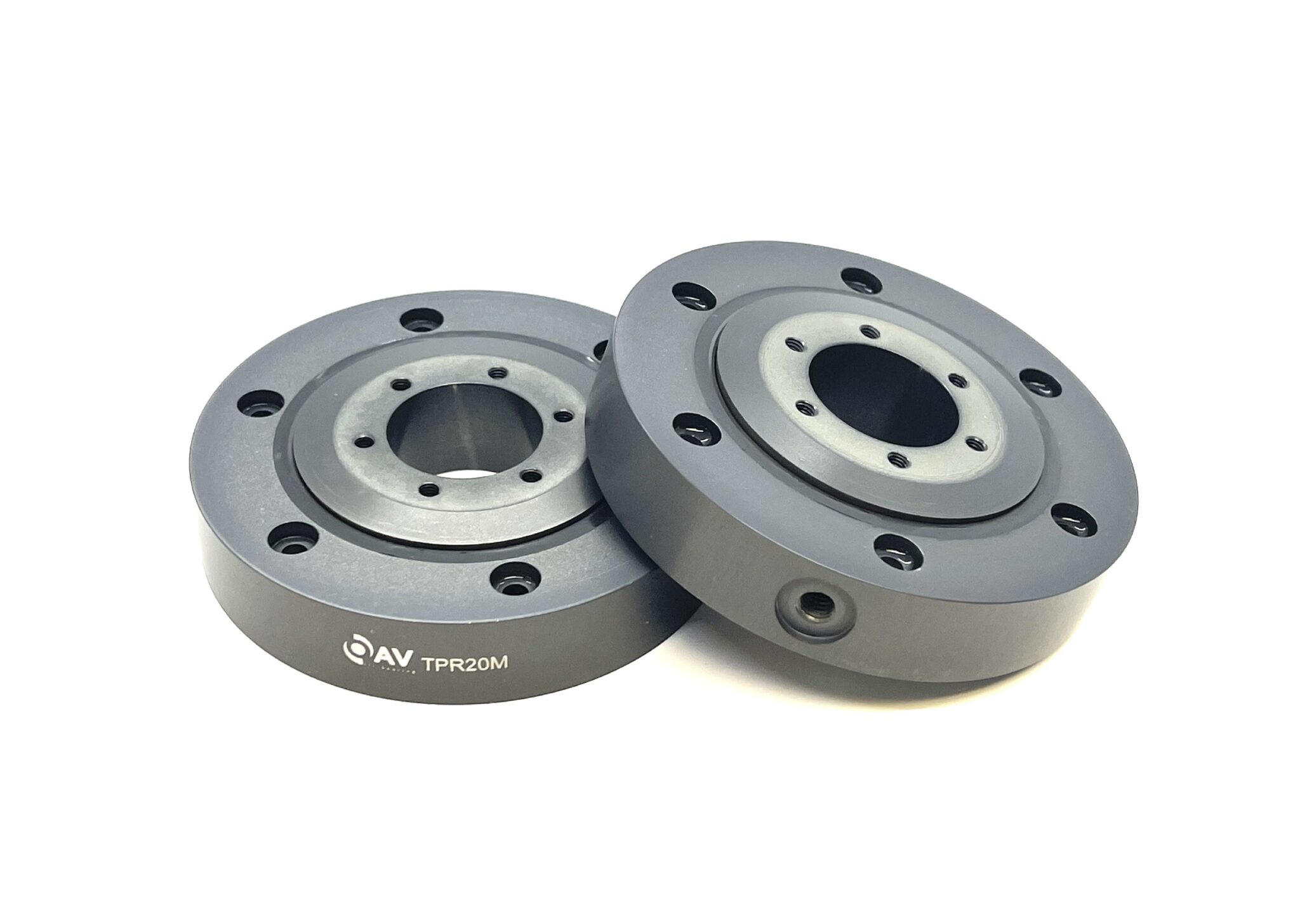
How Air Bearings Work
Air bearings function by creating a thin cushion of air between the bearing surface and the object it supports. Let’s delve into the mechanics of this unique technology.
The Components of Air Bearings
Air bearings are typically comprised of the following components:
The bearing itself, often made of specialized materials like ceramics or stainless steel.
An air supply, usually a compressor, that provides the necessary pressurized air.
A set of orifices or porous media through which the air is delivered to the bearing surface.
Before listing the specific attributes of these components, let’s understand how they interact with each other in an air bearing system.
Interaction and Coordination
The air compressor forces the air through the orifices or porous media, creating a stable film of air that separates the bearing from the object. This cushion of air is maintained at a consistent thickness, allowing for precise control and minimal friction.
The Operational Principles
Understanding how air bearings work involves recognizing the key principles that govern their operation. Here’s a glimpse into the core mechanics:
Pressure Distribution: The air film’s pressure must be carefully balanced to support the load without allowing contact between surfaces.
Stability and Damping: Proper design ensures that the air film remains stable, and additional damping mechanisms may be used to control vibrations.
Efficiency and Environmental Impact: Air bearings offer increased efficiency and minimal environmental impact due to the absence of lubricants and reduced wear and tear.
These principles collectively contribute to the wide range of applications and benefits that air bearings offer.
Applications and Benefits
From aerospace to manufacturing, air bearings have diverse applications.
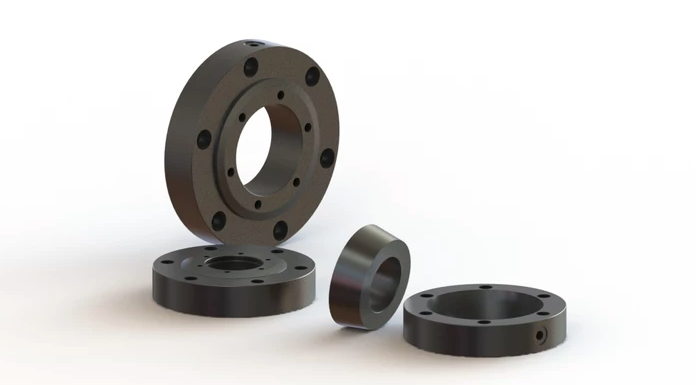
Industrial Applications
Whether it’s in the high-tech world of silicon wafer handling or the demanding environment of heavy machinery, air bearings prove to be invaluable. Here’s how:
Semiconductor Manufacturing: Achieving microscopic precision in the handling and processing of semiconductor wafers.
Heavy Machinery: Providing smooth, controlled movement in large equipment where traditional bearings might fail.
To fully grasp the depth of their influence, we must explore their benefits in detail.
Key Advantages
Air bearings offer several key advantages over traditional bearing solutions, setting them apart as a technology of the future:
Frictionless Operation: Elimination of physical contact reduces wear and tear.
Increased Precision: The controlled air film allows for more accurate positioning.
Environmental Friendliness: Lack of lubricants and reduced waste contributes to sustainability.
Cost-Effectiveness: Longer lifespan and reduced maintenance result in overall cost savings.
These compelling features make air bearings an attractive option for numerous applications.
Different Types of Air Bearings
Air bearings are not confined to a single design or operation mode; rather, they encompass a variety of types, each catering to specific needs and applications. Let’s explore the distinct kinds of air bearings and what sets them apart.
Aerostatic Bearings
Aerostatic bearings rely on an external pressure supply to maintain the air film between the bearing surfaces. Their key characteristics include:
Precision: Exceptional control over positioning, particularly beneficial in applications requiring micrometer-level accuracy.
Adaptability: Suitable for various tasks, from machine tools to precision measuring devices.
Common Applications of Aerostatic Bearings
Aerostatic bearings are prevalent in industries where precision and control are paramount:
In semiconductor manufacturing, they enable intricate alignment.
In optical devices, they facilitate high-resolution imaging.
Aerodynamic Bearings
In contrast to aerostatic bearings, aerodynamic bearings generate pressure through the relative motion between the surfaces. This self-acting mechanism has its unique advantages:
Self-Sustaining: They do not rely on external pressure sources, making them more autonomous.
Energy Efficient: By utilizing the motion to generate pressure, they often consume less energy.
Where Aerodynamic Bearings Shine
Aerodynamic bearings are commonly found in applications where the energy efficiency and self-sustaining properties are essential:
In turbo machinery, where high-speed rotation is standard.
In energy-efficient transportation systems, such as magnetic levitation trains.
Hybrid Air Bearings
Hybrid air bearings combine the features of both aerostatic and aerodynamic bearings, offering a versatile solution:
Flexibility: They can function with both external pressure sources and self-generated pressure.
Broad Application Range: Suitable for scenarios demanding both precision and energy efficiency.
The Best of Both Worlds
Hybrid air bearings are employed in contexts that require a balance between precision and energy conservation:
In aerospace applications, where weight and efficiency are equally vital.
In medical devices, offering accurate and smooth operation without compromising on energy consumption.
These diverse types make air bearings a flexible technology capable of catering to a wide array of industrial needs.
Challenges and Considerations in Implementing Air Bearings
While air bearings present a plethora of advantages, they also pose certain challenges and considerations that must be addressed.
Design Complexity
Implementing air bearings can be a complex process that requires intricate design and understanding:
Precise Calibration: The air film’s thickness must be carefully controlled, demanding sophisticated engineering.
Material Selection: The right materials must be chosen to withstand the pressure and environmental conditions.
Cost Considerations
While offering long-term savings, the initial investment in air bearings may be substantial:
High Initial Cost: Sophisticated design and specialized materials can drive up initial expenses.
Maintenance Requirements: Though generally low-maintenance, specialized care may be required in some cases.
Environmental Factors
Environmental factors must be considered to ensure optimal operation:
Air Quality: The quality and purity of the air used can significantly impact performance.
Temperature Control: Temperature variations can affect the air film’s stability and efficiency.
Conclusion: The Future of Motion
Air bearings are more than just an engineering novelty; they represent a profound shift in how motion is controlled and achieved. With their diverse types, wide application range, and unmatched benefits, they hold the key to a new era of precision, efficiency, and sustainability. Yet, like all pioneering technologies, they come with challenges that must be skillfully navigated. In embracing air bearings, industries are not merely adopting a new tool but aligning with a vision of progress that transcends traditional limitations. The journey of air bearings is only just beginning, and the horizons they will explore are boundless.
Join the conversation: