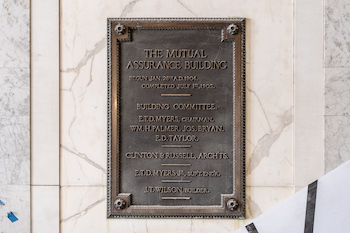
While working in the 120-year-old building, maintaining the historical integrity of the structure was one of the largest challenges all the contractors involved were faced with.
Renovating historical, urban buildings offers a great number of benefits over demolition and replacement, including lower embodied carbon and the alure of a bygone era blended with the comfort and convenience of the 21st century.
As cities evolve, repurposing old buildings becomes integral to creating more resilient, resource-efficient, and culturally rich urban environments.
But with miles of red tape to navigate, turn-of-the-century construction methods and materials to contend with, and special regulations to adhere to, revitalizing old urban structures requires a specialized team.
An outstanding example of the collaboration needed on such a project can be witnessed at The Mutual Building. It’s the oldest high-rise structure in Richmond, Va., originally housing a stock brokerage firm and later a law office. Built as a 9-floor building in the early 1900s, three additional stories were constructed later.
Key players
In November 2020, Shamin Hotels sold the 12-story building for $12.8 million to Landmark Property Services, Inc., a Richmond-based property management firm and The Wilton Companies, a Richmond-based commercial real estate firm. Their intent was to convert the high-rise into 168 upscale apartments. The 22-month project would present a wide array of challenges to overcome.
Landmark Property Services, Inc. sought the expertise of Walter Parks Architects (WPA) to help bring The Mutual Building to new grandeur.
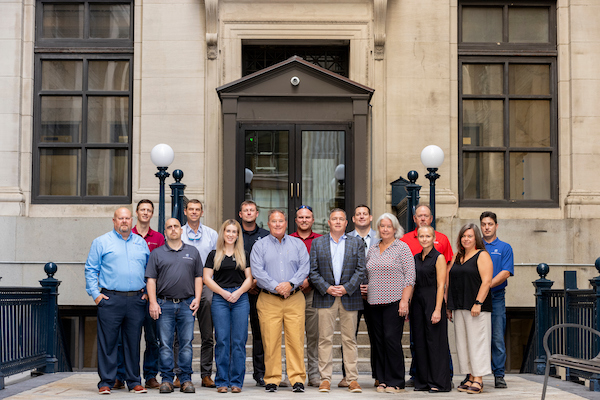
Representatives from Landmark Properties, Snyder Solutions, L.F. Jennings, Ferguson Enterprises and Harry Eklof & Associates gather in front of the main entrance.
“Our company specializes in historic tax credit work,” said Sarah McInerney, senior project manager at WPA, who completed the early project pro-forma. “Multi-family work is my preferred project type, though we handle other residential and medical facility projects as well.
WPA’s involvement included designing the apartments and working closely with the various engineers and contractors involved with the renovation. The firm has conducted similar work for 30 years, and McInerney herself for 20 years.
James Willis, design engineer at O’Neil Engineering, was one of McInerney’s first calls. WPA has worked with O’Neil Engineering on many similar projects. The involvement of a mechanical engineer familiar with challenges common to old buildings in Richmond would prove critical to success.
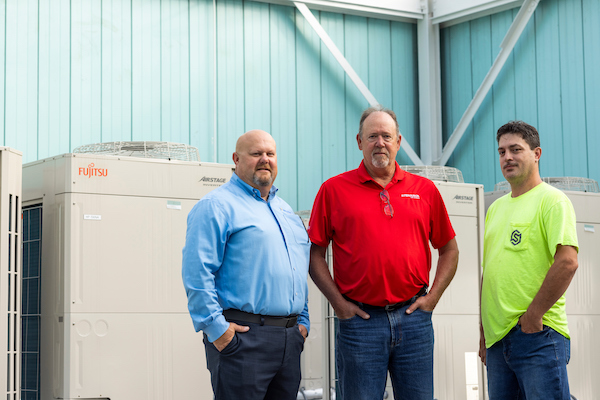
(left to right) Brian Adkins, with Harry Eklof & Associates, Alan Dukes, of Ferguson Enterprises, and John Jenkins, with Snyder Solutions.
Snyder Solutions, a full-service mechanical company founded by Ryan Snyder in 2009, was hired to install an extensive Fujitsu Airstage heat recovery VRF system to replace the boiler/chiller VAV system.
L.F. Jennings, a 350-person firm, was selected as the general contractor. They specialize in a broad array of project types but have relative experience with adaptive reuse, having just converted a similar office tower into apartments just two blocks away.
Unique challenges
“Qualifying for historic tax credits is a three-part process,” said McInerney. “The building must be nationally recognized in a historic district. Designers must comply with the Secretary of the Interior’s Standards for the Treatment of Historic Properties, and finally, the project must pass inspection by the Virginia Department of Historic Resources and the National Parks Service.”
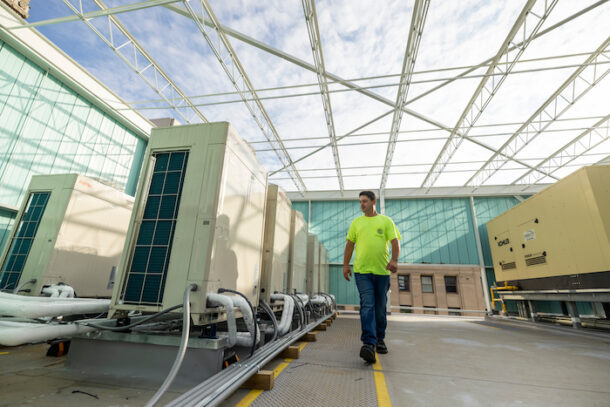
John Jenkins, assistant supervisor at Snyder Solutions, walks the rooftop of the Mutual Building.
All parties involved understood that installing new electrical, plumbing, heating and cooling systems must be completed in such a way that visual disturbance to the property, inside and out, be minimal. This meant preserving flooring, trim work, signage, and eliminating outdoor mechanical components from view.
To further complicate things, the building was originally constructed using a “Metropolitan Floor System.” Unlike conventional concrete or steel construction, the Metropolitan Floor System is an architectural relic from the 1890s utilizing pairs of twisted wires, as catenaries, draped over the steel floor beams and embedded in a plaster-of-Paris matrix. The load-bearing capability of the floor relies entirely on the tension in the wires.
Meticulous design
When working on the design, James Willis, Ryan Snyder and Andy Anderson, director of mechanical division at Snyder solutions, collaborated to confront their largest hurdle, the need to maintain the historical integrity of the building.
“If it weren’t for the need to conceal outdoor units, this project could have been conducted with mini-split heat pumps,” said Snyder. “But Willis determined that VRF systems would better serve the purpose. The outdoor units needed to be mounted so that all stories could be served by the new HVAC system, from the 12th floor down to the sub-basement. Landmark Properties has experience with VRF systems on other projects, so they understood the flexibility and efficiency it provides.”
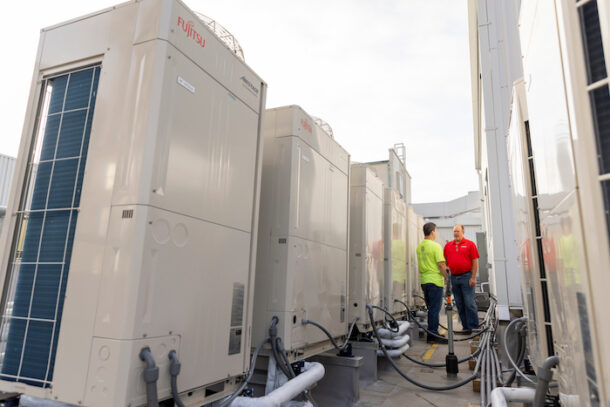
John Jenkins (left), assistant supervisor at Snyder Solutions, discusses the Fujitsu Airstage heat recovery installation with Alan Dukes, of Ferguson Enterprises.
Willis and the team at Snyder Solutions tapped Brian Adkins, HVAC sales manager at Harry Eklof & Associates, and Matt Coley, commercial HVAC manager at Ferguson Enterprises, for specifications on the Airstage heat recovery system.
“To overcome the vertical height challenges, we settled on a plan to mount the majority of the outdoor equipment on the roof,” said Willis. “This project had a zero lot line, with almost no room at ground level for equipment. To serve the lower levels of the building, we planned to install several systems in the light wells just below street grade, maintaining the original look of the building.”
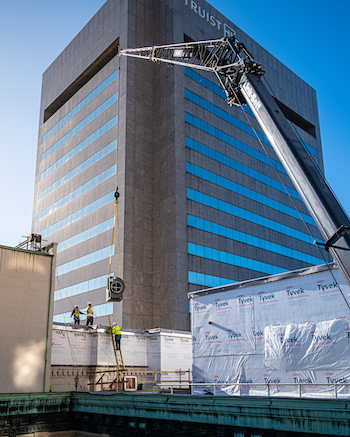
A fan used to pressurize stairwells and elevator shafts is craned to the roof of the building.
The five systems installed in the light wells serve the lower three levels of the building, which include the main floor lobby, mail room an indoor dog park, golf simulator, gym, and storage space.
In all, 200 tons of Fujitsu Airstage V-Series heat recovery equipment was installed, consisting of six, eight and 10-ton outdoor units. Inside, slim-duct air handlers were installed in living spaces, with ceiling cassettes in common areas. A total of 217 terminal units were installed.
This approach lent itself well to the building layout. Apartments range in size from 500 to 1,050 square feet, meaning that flexibility was needed in the HVAC design.
Training and support
Heat recovery VRF systems were selected over heat pump systems for the ability to provide simultaneous heating and cooling from the same system. Heat recovery has the added benefit of salvaging BTUs from a zone calling for cooling and rejecting the energy into a zone calling for heat.
One heat recovery system serves two floors. These systems are 16 tons in capacity, save those serving the lower three floors.
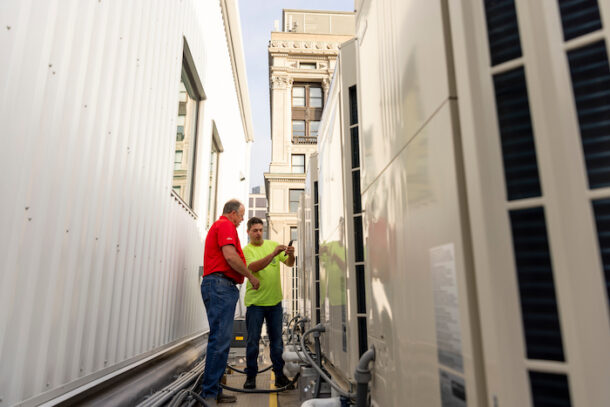
Alan Dukes (left), of Ferguson Enterprises, and John Jenkins, assistant supervisor at Snyder Solutions, discuss the Fujitsu Airstage heat recovery installation on the roof of the Mutual Building.
“When it came time to install the equipment, Alan Dukes, VRF Technical Advisor at Ferguson, was very involved,” said Willis. “We’ve worked extensively with him on other projects like this. He’s extremely detail oriented, and visited the site frequently to answer questions and ensure that the equipment was being installed to spec.”
Dukes has a relationship with Snyder Solutions, too. He has provided Fujitsu training to Snyder technicians in the past.
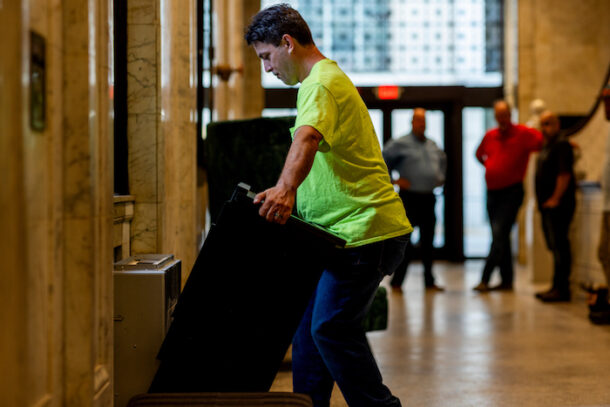
John Jenkins removes wooden casing from around a vertically-mounted Airstage ARUL slim duct fan coil.
“An application like this requires precision in the design and installation,” said Snyder. “We’ve worked with Ferguson since I founded Snyder Solutions, and Alan is the grandmaster of VRF. They don’t make guys like him anymore. He’s forgotten more about VRF than I’ll ever know.”
Snyder Solutions has one or two VRF projects going on at any given time, but this is the largest Fujitsu installation they’ve undertaken. The company’s initial training session with Dukes included 12 technicians at Ferguson’s Chesapeake location, and subsequent training sessions are ongoing.

Snyder Solutions is a 100-person mechanical firm serving the Richmond metro, focused on commercial and industrial work.
“The help that Alan provides is a great example of why we install Fujitsu more often than other VRF brands,” said Snyder. “They give us the most support and the product quality is fantastic. From the factory team to the reps and wholesalers, they have a knowledgeable team that’s aways quick to help.”
Old building, new solutions
“Like most historical projects, there were no building blueprints to reference,” said Anderson. “You don’t know what you’ll run into until you open up walls and floors, at which point you need to come up with solutions on the fly. Pippa Brown, L.F. Jennings’ assistant project manager and lead coordinator, was a great asset whenever we ran into an issue. She kept everything on track with the retrofit’s objectives.”
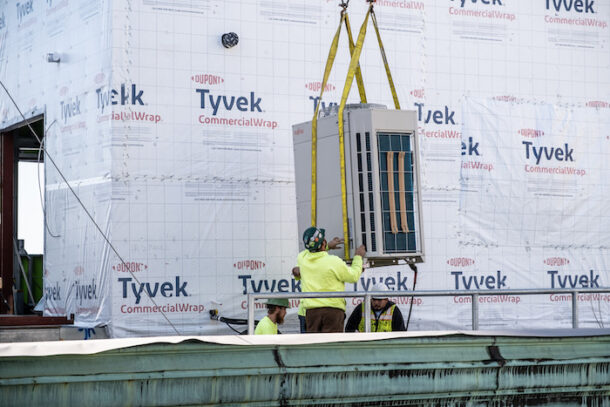
One of many Fujitsu Airstage heat recovery condensing units is craned to the 12th story roof.
Snyder Solutions technicians—led by Adam Mitchell, superintendent, Tony David, lead service technician, and John Jenkins, assistant superintendent— worked with the L.F. Jennings crew to open walls. Refrigerant lines were run down through stud bays. Terminal units and ductwork had to be hidden, and louvers could only be installed in specific places.
“We take great pride in creating solutions for difficult projects, and this one brought out the best of our team,” said Anderson. “There was no straight path from A to B, and we had to be careful not to disturb historical artifacts, like trim and molding.”
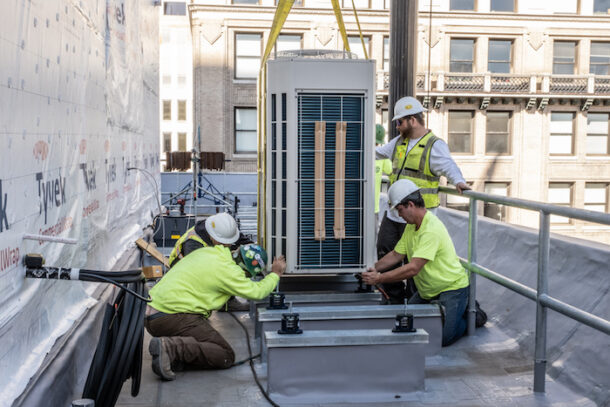
Airstage condensing units were mounted on seismic isolators.
The biggest hurdle, however, came each time the installation crew penetrated a floor. Thanks to the Metropolitan Floor System, this proved to be every bit the arduous task that Snyder Solutions and Willis knew it would be. O’Neil Engineering, Snyder Solutions and L.F. Jennings had previous experience with the unique system.
The catenary wire system within the plaster can’t simply be cut without compromising the integrity of the floor. To create a floor penetration, the plaster slab must be dug away, wires cut, and a custom fabricated steel sleeve inserted, designed in-house by L.F. Jennings and Balzer Associates. Once the sleeve is set, the wires are then secured to the sleeve and the penetration is poured back. There are various different penetration types and sleeve sizes that required coordination. These penetrations may be no less than nine inches apart, making plumbing penetrations especially difficult.
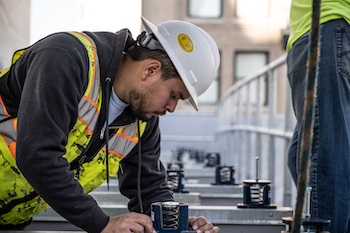
A Snyder Solutions crew prepares to mount heat recovery condensing units on seismic isolators.
To minimize the number of penetrations needed, combination sleeves were designed to house multiple penetrations in a line; only refrigerant lines, the plumbing system, and outdoor air risers run vertically through the building. All ductwork connected to the Fujitsu air handlers runs horizontally. Ventless dryers were used, so no drier stacks were needed.
A textbook success
Instead of commissioning all the VRF systems at once, Dukes worked with Snyder Solutions to start up each floor individually as they were completed from the top down.
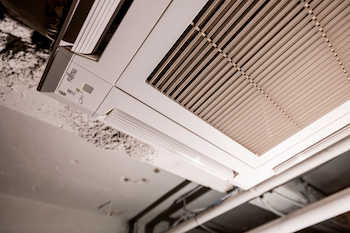
While most of the building is served by slim duct air handlers, a variety of ceiling cassettes were used on common areas storage space.
“The installation and commissioning went very smoothly,” said Dukes. “That’s a testament to a solid, adaptable design, fantastic communication between all parties, and an installation team that really committed to doing their best work.”
“The building has been occupied for almost a year and we’ve had no issues,” said Snyder. “With the number of systems installed here and the severity of last summer, it’s quite impressive. I can proudly say that we delivered what we promised.”
This project exemplifies the delicate dance between preserving the past and embracing the future in architectural endeavors.