For the past several years, the Youndts, a family of five, kept their eyes open for a rural property—a new place to call home.
Turns out the 10-acre property the Youndt family bought (not far from the company they own) had the ideal fixer-upper of a home on it, with a big barn and bungalow, too.
While the pond and swimming pool caught the attention of Vince Youndt’s wife Amy and their kids Brynn, Drew, Riley and Brady, Vince was smitten by the old stone home and its 70-year-old, oil-fired boiler. He just knew he’d have a fine time dialing-in the hydronic heat.
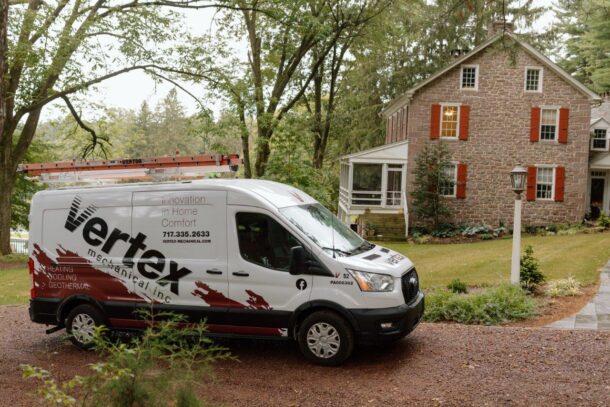
Vince Youndt (pronounced “Yunt”) is president of Vertex Mechanical, one of the best-rated HVAC contracting firms in Central Pa. Twenty-some years ago, Vince followed his father Ray into the business; Vince has been president of the company since 2002.
“When the stone home and property hit the market, we knew we had to see it,” said Youndt. It wasn’t long before the Youndts were signing settlement papers.
There were a few surprises along the way. They soon discovered the home’s 1847 date stone, its three working fireplaces, a hefty 36-inch rock foundation and the property’s 15-gallon-a-minute freshwater spring.
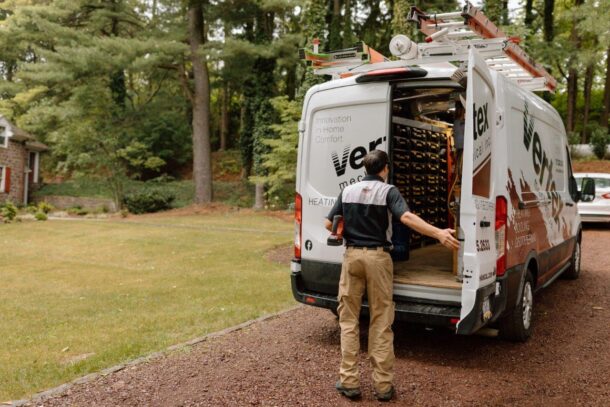
Youndt also learned that the home had only fireplace heating from 1847 to 1951. “Imagine carting hardwood to all those fireplaces several times a day and night,” he said. In ’51, the home’s first heating system was installed: the boiler that still occupied most of the lower-level mechanical room.
$2,000/month for fuel oil
The old 500 MBH behemoth steel block boiler served just one zone: the house. All 4,300 square feet of it, with three floors and no insulation, five bedrooms and 3½ baths, were all on a single zone. On, or off. In the shoulder seasons, the previous owner just opened windows to adjust the heat.
Youndt was also surprised to learn that the previous owner spent $2,000 a month to heat the place. “And that was long before fuel oil cost four dollars a gallon!” he exclaimed. “They also shelled out $600 a month through each summer season just to heat domestic water.”
A few months after buying the place and just after the 70-year-old heating system took its last gulp of fuel oil—Youndt decided to tackle the hydronic system retrofit.
Wedding venue
Just as Vince was muscling through the demolition of the 1,500-lb. boiler, another need appeared on the horizon. The Youndt’s eldest son, Andrew (“Drew”) expressed interest in having his wedding at the new homestead.
While Amy, Drew and his fiancé were scouring bridal websites and landscaping with flowers, Vince ran the business. His lunch hours were spent specifying the boiler of choice, circulators and other components, or with calls to wedding vendors.
Dreamy hydronics
Amidst the onset of preparations for the wedding, Youndt sketched and re-sketched his circulation and piping strategy for the hydronic retrofit, then finalized his wish list for the boiler replacement. Taco ECM circs and several Zone Sentry zone valves were planned, followed by an NTI boiler and indirect, and a heat pump water heater for use in the summer.
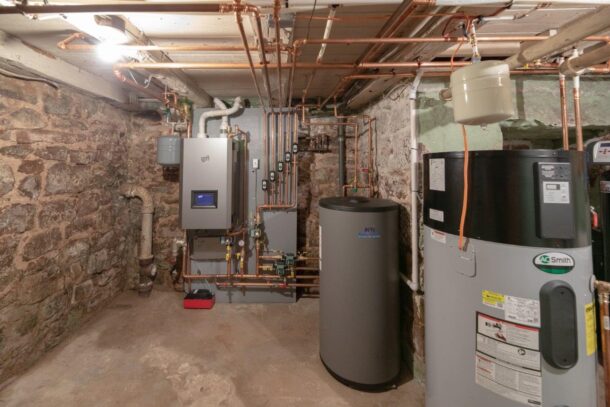
“At the time, I was having vivid dreams,” recalled Youndt. “I’d wake up at night with thoughts about the wedding—intermixed with dreams about a heavenly hydronic system! What a combination. It was all doable, and I knew that we’d have a really comfortable home. We now wake up to birds chirping, feeling that the home and property were left behind by one of those dreams.”
Good nights of rest led to moments of tough labor—including the rigors of demo work in the home’s daylight basement level. “The space downstairs seemed to triple in size when we finally got that monster boiler out’a there,” said Youndt. Vertex technicians Jared Fox, Steve Zook and John Harris will never forget the day they muscled it—all in one piece—to an awaiting truck.
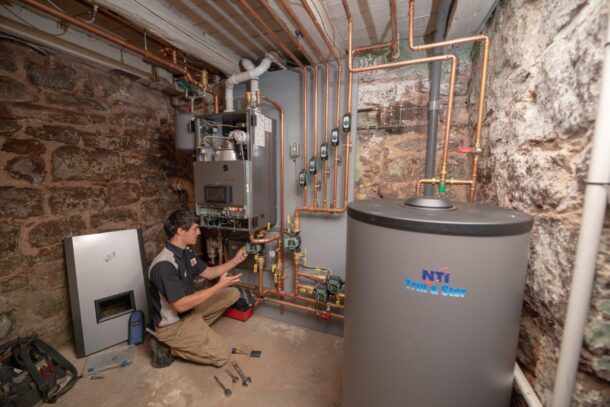
It then took Youndt most of a weekend to drill an eight-inch hole through the foundation. He quickly learned—to make way for a planned passageway for insulated supply and return lines to a wood-fired boiler (yet to be installed)—that the home’s masons, long ago, sandwiched giant granite boulders between Berks County sandstone.
“That granite was a bear!” he exclaimed.
In the fall of ’22, Eric Grant, regional business manager for Fernox USA, visited the Youndt’s home. Grant arrived with the company’s PowerFlush flushing machine, a mobile system with pump and filtration, mounted on a dolly. He also brought several gallons of Fernox hydronic fluids.
After Youndt cut into the old boiler’s iron pipes, the two soon found what sort of mess the pipes contained.
“The crud went from semi-solid gobs of oily sludge, to thick metallic pudding, then a dirt slurry, and finally semi-transparent soup,” explained Grant. That’s when Grant connected the cut pipes to the new PowerFlush. Together, he and Youndt then poured F3 cleaner into a reservoir that quickly mixed with water they ran through the flushing unit.
An hour later, the result of the chemical cleaning was made evident with crystal clear fluids returning to the PowerFlush unit. It pushes up to 30 gallons a minute to scour-out and capture all the scale and rust that can collect in a piped, hydronic system including—and especially—the heat emitters attached to it. The result: a fully-cleansed, restored system.
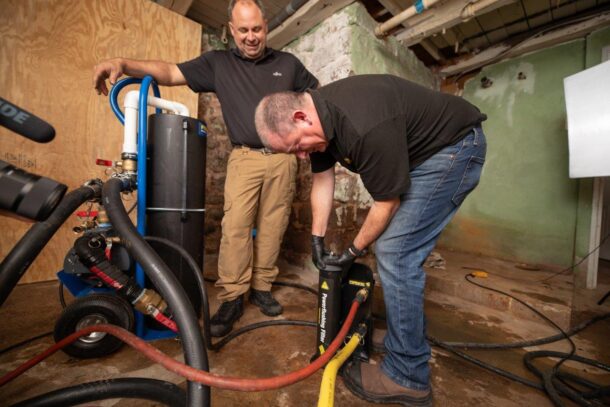
Before leaving the Youndt’s home, Grant left behind a couple of gallons of Fernox F1 Protector, a solution for later maintenance of the system—all prearranged with Youndt.
Grant then presented Youndt with the last of his purchases, a nickel-plated brass TF1 Omega+ filter to be installed when Youndt finalized installation of the new equipment.
Hydronic minimalism
Youndt recalls the days, years ago, when he wanted to fill a wall with hydronic components. “It was the ‘Mad scientist’ laboratory’ look that appealed to me back then,” he said. Lately, though, he favors what he refers to as “hydronic minimalism.”
His plan called for five heating zones in the home, and one for domestic water. Then, ultimately, the wood-fired boiler within a year or two.
One evening, he put two coats of gray paint on a single sheet of ¾-inch, pressure-treated plywood. “I wanted to hang everything on one sheet, to get the NTI boiler and Taco components as tightly together as possible, yet with plenty of room for later service work,” he said.

The plan materialized nicely. Youndt, Zook and Harris, armed with a stack of copper pipe and Viega press-fit couplings, began the process of reengineering the near-boiler piping. Now, the primary-secondary arrangement provides full-flow in the boiler loop, high- and low-temp distribution, and variable flow for secondary piping to all sources of heat distribution.
Throughout the house, there’s a mix of standing radiators, and baseboard for high-temp heat, with gentler provision of warmth for floor and ceiling radiant heat.
The NTI boiler was first in place. The 150 MBH, TFTN150 wall-hung boiler, representing a huge reduction in boiler output and physical size, and with outdoor reset, offers remarkable capability. “The boiler has the ability to control up to four zones of heat, each with its own temperature assignment,” stated Youndt. “Because of the five zones and a desire to use a sixth for domestic heating, we included NTI’s expansion board to add them; each zone now is independently managed.”
Youndt installed four Taco 0015e3 circulators. One serves as the boiler pump. Another manages the secondary heating zones. The remaining 0015e3’s serve the 50-gallon NTI indirect water heater, and future wood boiler. A Taco Zone Sentry zone valve manages circulation for each of the home’s five space-heating zones.
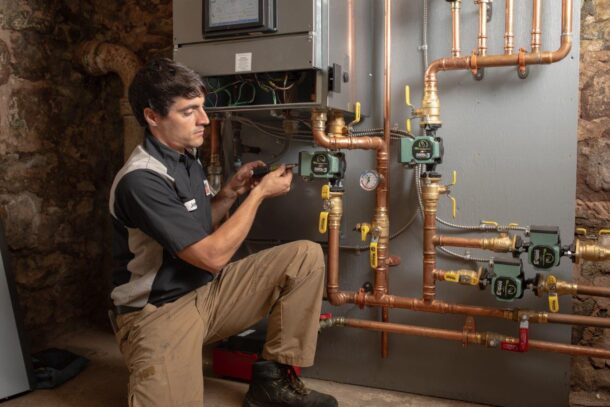
“We’re using only six circulators for the entire system, two of which are for the wood side of the system,” explained Youndt. “The NTI fires on a call from a thermostat, then looks first to see if there’s heat in the heat exchanger coming from the wood burner. If there is, it’ll be used as the first stage of heat.
“Because of the multiple low temp radiant zones in the system, the circulator for the heat exchanger offers variable speed with an outdoor reset control that governs the mixed temp coming from the heat exchanger—never to exceed the requirement,” added Youndt. “If the fire on the wood burner is out—maybe because I didn’t want to feed it, or we’re in the shoulder season—the NTI will kick in the burner utilizing the outdoor reset to determine the heat needed.”
In the summer, and with the old stone wall basement, the Youndts have a significant humidity problem. “But we don’t use a dehumidifier,” concluded Youndt. “We shut down all the other equipment while operating the heat pump water heater. It’s pretty remarkable—the water heater then uses the energy from the humidity to heat all of our hot water—all summer long. This allows us to keep the humidity in the basement at about 50 percent, and we never lack hot water, all at a cost of about $30 a month.”
A historic, and energy-efficient dream home. What could be better?