Mike Travers Sr. got started as a machinist on a U.S. Navy destroyer, and worked nearly 30 years as a technician and district manager for York International Corp. His son, Mike Jr., also had more than 15 years with York. This gave the pair all the parts n’ pieces they needed when they teamed up to build a service-oriented company.
Mike Youngman, Mike Travers Jr. and Sr. look over plans for a hospital project.
In April, 2006, they did just that. The doors to Travers Mechanical Services swung open in Albuquerque, New Mexico. Today, their firm serves commercial and industrial customers – statewide – with 24/7 service. With over 20 technicians – and still hiring – the company stays more than busy, despite a lackluster market and reductions in new construction work.
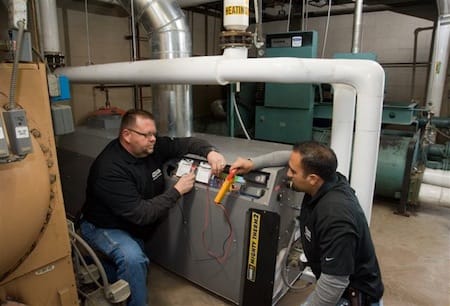
“Dependability and client satisfaction have been the keys to our success,” said Mike Jr., who left York with his father to become co-owner of the company. “Most of our new business comes through referral.” Their primary goal as a service provider is to offer customers the highest degree of integrity while continuing to build on their proven capabilities.
Gary Holbrook and Eric Tafoya service a Laars boiler at Summit Apartments.
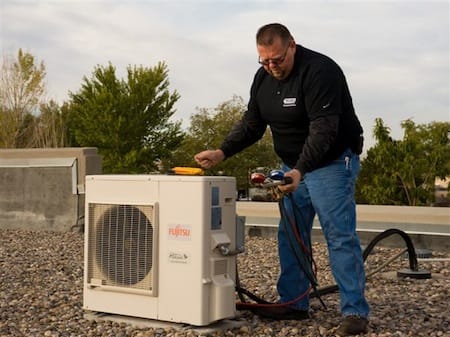
“The majority of our new customers come from existing ones,” said Mike Jr. “We get calls weekly from people saying, ‘We heard you’re the guys to call when it comes to chillers and boilers.’” Travers only advertises through sponsorships, golf tournaments, and banquets. Their lofty customer service standards – expectations they’ve placed upon themselves – help maintain and grow the customer base.
Gary Holbrook puts the finishing touches on a Fujitsu condensing unit installation at the NM Gas Masthead building.
New hydronics: 270 water-sourced heat pumps in one facility
The pros at Travers were recently tapped to help renovate and re-commission an HVAC installation for a 75,000 s.f., three-story US Forestry office facility in Albuquerque to help win LEED points – a job in progress now. “There are 270 Trane water-source heat pumps there, with substantial cooling tower work as well, making it a hydronic system overhaul of giant proportions,” said Mike Youngman, Travers’ health care division manager. And there’s substantial reward in it for the building owner, with state and federal tax incentives on the line (about $250,000) for the LEED-qualifying make-over.
Nearly the whole Travers crew ready to roll out for a day full of service calls, retrofit work, and new installations.
According to Youngman, the many two- to eight-ton heat pumps were designed for use with R22 refrigerant. “We’re now overhauling them to operate with CFC-free 407C refrigerant; fortunately, the new refrigerant’s almost a drop-in replacement for the R22.
“The focus of our effort is to remove the old R22 and – with several other facets of mechanical system work – to reduce cooling tower water temperatures,” added Youngman. “By reducing the evaporation, we can lower chemical treatment use and water consumption. As head pressures are reduced, the heat pump compressors don’t work as hard, and this reduces equipment amp draw . . . so electrical consumption is decreased. In total, we’re anticipating a 35 to 40 percent reduction in the building’s electrical energy consumption.”
Travers Mechanical: the hydronics solution in Albuquerque.
New Mexico Gas taps Travers
In a part of the world known for relentless sun and high temperatures, and where ducted systems were once a rarity, it’s no surprise that Travers pros have become well acquainted with ductless system technology – an ideal was to cool or provide supplemental heat for hydronically-heated structures. New Mexico’s arid climate and widely-varying ambient temperatures makes mini-splits an attractive option for commercial and industrial customers.
In the summer of 2011, a loyal client called Travers about adding additional cooling to an existing facility. New Mexico Gas Company needed to cool a new server room at their headquarters facility. In addition, a large conference room quickly overheated during well-attended meetings. The key problem was that an under-floor plenum system wasn’t sized correctly when the building was constructed several years before.
Within a week, two condensing units were installed on the building’s roof, and two 42,000 BTU ceiling cassette units were installed in the conference room. The room’s drop ceiling made installation a breeze.
“This kind of installation is pretty popular,” said Mike Jr. “Most office buildings here aren’t set up for servers. For the small offices that need to keep server equipment cool, this is less expensive, when compared to a full server room ac unit. On this job, they also wanted the option of quickly changing the temperature in the conference room.
“We’ve installed several different split-system brands, but we’ve stuck with Fujitsu since 2006 because of their dependability and warranty response,” said Michael Jr. “If we run into any problems, our supplier, Johnston Supply, takes good care of us.”
Installing the Fujitsu systems were only a small part of the work Travers does for New Mexico Gas. According to Mike, they take care of each of their six facilities within the state. The relationship entails Travers’ care of chillers, boilers, hydronic systems, roof top units and split systems.
Solar Villa Housing Community
Several technicians spent the majority of their summer months last year at the Solar Villa Housing Community in Albuquerque. Between April and August of 2011, Travers overhauled the 120-unit complex’s entire mechanical system.
“We replaced 110-ton scroll chiller,” said Mike Youngman, project manager. “It had an evaporator coil leak that contaminated an entire circuit. Given the age of the unit, it was better just to replace it. The new one’s an air-cooled McQuay scroll chiller, located on the East side of the building.”
The facility had three boilers, two of which were ancient, one that was relatively new. Each old gas-fired boiler was replaced with a new 750 MBH Laars Mighty Therm II, while the newer, existing boiler remained.
The Mighty Therm II is especially attractive for replacement projects with straightforward controls and flexible installation piping options. The multi-stage, low NOx boiler can be installed indoors and outdoors.
“When we installed the new boilers, the newest of the three original units got tied into the two new systems from Laars,” said Youngman. “All three are now part of a big primary-secondary system.”
“We use Laars boilers whenever one of their models fits the application,” said Mike Jr. “The wide product line makes it a pretty regular occurrence. Their boilers are compact and easy to install. I’ve never had a problem with a Laars boiler that we installed.”
According to Mike Neely, service technician and lead installer, the biggest challenge at solar villa was working around the tenants in each apartment. Working with insulation subcontractors, electricians and government project managers added the typical challenges, as well.
According to Neely, each apartment had a fan coil unit, and 11 more were used in common areas. Three things were plaguing the old fan coils; motors were going bad, there was water restriction inside the coils, and airflow restriction through the grilles. All 131 units were replaced with new 37,000-BTU Lanco H 800 units.
Many hydronic products used on Travers projects come from Boyd Engineering Supply, in Albuquerque. “We get great support from Boyd. For help with boilers, they have a Laars certified guy on staff that is wealth of information,” said Mike Jr.
Summit Apartments
“The challenge our climate poses is most notable in apartment buildings,” said Michael Jr. “Most have a two-pipe system: cooling during the summer and heat during the winter. It can be 75° one day and 40° the next, so during the changeover season it can be tricky to choose the right time to switch from heating to cooling, or vice versa.”
At Summit Apartments in Albuquerque, the swing season issue was compounded by a 40 year-old boiler with ruptured tubes. Travers would have fixed and retuned the unit, but suggested a replacement. The 193-unit complex has two boilers, one of which Travers recently replaced. With three technicians on the job, they were in and out within 24 hours.
According to Travers, the boiler room is small. The boiler that got replaced was closest to the door, so the project went quickly. When comes time to replace the other boiler, the new, two million BTU Laars Mighty Therm II will need to be temporarily disconnected and set aside to allow the next boiler passage into the room.
Mike Jr. and Sr. already know they’ll be the ones called to install the next boiler. They know the systems inside out, and they’ve built a solid relationship with facility managers. They’re available around the clock and, after all, they’ve been pursuing this American dream for decades.
Pictured on the homepage: Mike Travers Jr looks over a Fujitsu split system just installed in a small server room.
A version of this story ran in the February issue of Contracting Business magazine. For more on Contracting Business www.contractingbusiness.com.
Join the conversation: