Mechanical Hub presents this multi-part series on pressing technology. Mechanical Hub features a Q&A with the leaders in pressing technology. Press technology is gaining momentum as the preferred choice in pipe joining. Introduced into the North American market in 1999 by Viega, pressing is gaining acceptance as the most efficient and cost effective method of joining piping materials. Press currently makes up nearly 12% of the copper fitting market, and that number is expected to rise with contractor education and training.
Mechanical Hub recently talked with some of the major players in the press technology market to learn more about what they are doing in this growing market.
The series continues with an exclusive interview with Thomas Farrell, president of Teal Corporation, the North American importer for REMS. (The Mini Press ACC tool with 360-degree head rotation featured on home page.)
Name some of the applications in which pressing is ideal?
Farrell: Press is ideal for residential and commercial plumbing, heating, gas, and fire sprinkler installations. It is especially suited for repair work where it is not possible to completely prevent drips from existing piping. It is very difficult to sweat a dripping pipe but easy to press. Additionally, it is great for cases where one cannot use a flame without evacuating or going thru additional measures to ensure safety-hospitals, schools, nursing homes, etc.
Standard Akku-Press ACC tool with 360-degree head rotation
What is the scope of press piping? Copper, PEX, Stainless, Iron, etc.?
Farrell: Copper, stainless, PEX, multilayer composite(PEX-AL-PEX), and carbon steel all have press systems available in a variety of systems offerings. At this time, I don’t think radial press joining can be used in refrigeration. I think there are some limitations in solar.
Are your pressing tools proprietary? Or can they be interchangeable with other manufacturer's pressing clamps and fittings?
Farrell: Many standard sized tools carry the same pressure ratings. The REMS standard sized tongs can be driven by REMS radial presses as well as suitable tools from others. Likewise, REMS standard sized tools accept tongs made by others. Basically, standard sized tongs up thru 2” seem to be interchangeable. Nibco is the only manufacturer I am aware of whose 2½”, 3”, and 4” fittings require a special tool provided by Nibco. They approve REMS and others for 2” and below. Many mini or compact tools also carry the same pressure ratings. However, in general, it seems mini or compact tongs are not interchangeable. As I understand it, each manufacturer makes theirs unique to their tools. Pressing contours of REMS pressing tongs are often system specific and in many cases are therefore made exclusively to crimp one manufacturer’s system only. This is more common in Europe. In North America, all copper systems below 2” that I am aware of that are currently offered utilize the same pressing tong profile.
I have heard the pressing is used predominantly in Europe. Why has it taken the North American market so long to catch on?
Farrell: Any major change seems to take time. The cost of launching a new product line is expensive and each manufacturer has to make a sizable investment in inventory, tooling, and marketing costs to release product in domestic sizes. Right now, I think there are only about five or six companies offering copper press fittings. They then need to get approved by codes and standards. There is also initial reluctance from the users. Then they often run into the “we’ve always done it this way “ syndrome. “My grandfather sweat pipes, my father sweat pipes, we sweat pipes.” Some may view it as taking work away. Union contracts could play a role also. I think the initial investment in tools and the higher cost of fittings were also a barrier. If you consider when copper press was launched in the U.S. and just as it was about to catch on the economy tanked and construction halted, press has actually made significant inroads. Even today, some plumbers still need to learn that the benefits of press can outweigh what seems to be a more expensive system. It is very quick and if installed according to the manufacturer’s specifications, there are essentially no callbacks. Lack of fitting availability may have played a role, particularly in outlying areas. Smaller wholesalers were less likely to stock two systems that accomplished the same thing. In general, as the economy slowed, inventories were reduced. Trying to convince someone to stock a new slow moving inventory was probably not easy. Chicken, egg…
Standard sized Akku-Press ACC in action
Is pressing technology continually evolving? (effectiveness, ergonomics, weight, cordless & battery efficiency, larger pipe diameters, etc.)
Farrell: Yes, it’s a natural evolution. As press gains market share more systems will be released or be imported so the choices should be broader. Today, I think all the tool development still is taking place in Europe and driven by that market. Tool manufacturers continue to make improvements. Tools have more features and batteries have become lighter, with faster recharge cycle times, and more pressing per charge. Larger pipe diameters are probably in the future but that is a really a question for fitting and valve manufacturers. Right now, in the U.S. anyway 4” is the largest sized I have heard of. If they go bigger I think more powerful tools will need to be developed and likely be larger and more expensive.
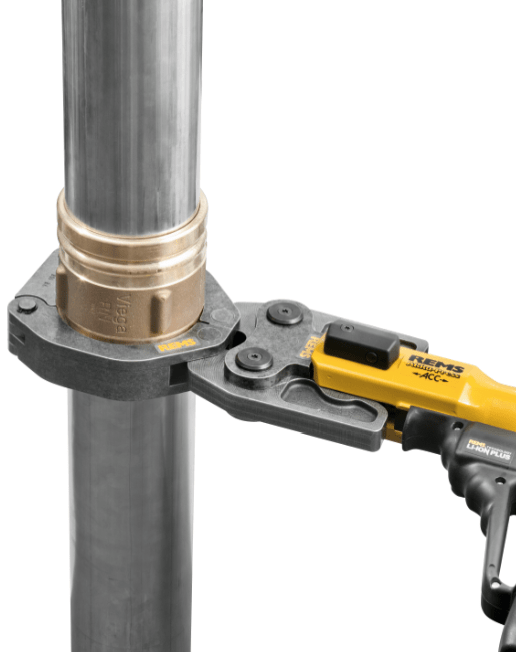
Large diameter Pressing Ring
I have used the pressing tools so the obvious question would be, why wouldn't contractors use pressing technology?
Farrell: See #4. Some don’t readily recognize the labor savings and think it is taking away from the trade. They have the attitude that if it’s not broke, don’t fix it. In my humble opinion it was broke and it is being fixed. Systems are becoming more widely available and are quick to install.
For more information on REMS, www.remstoolsusa.com.
Join the conversation: